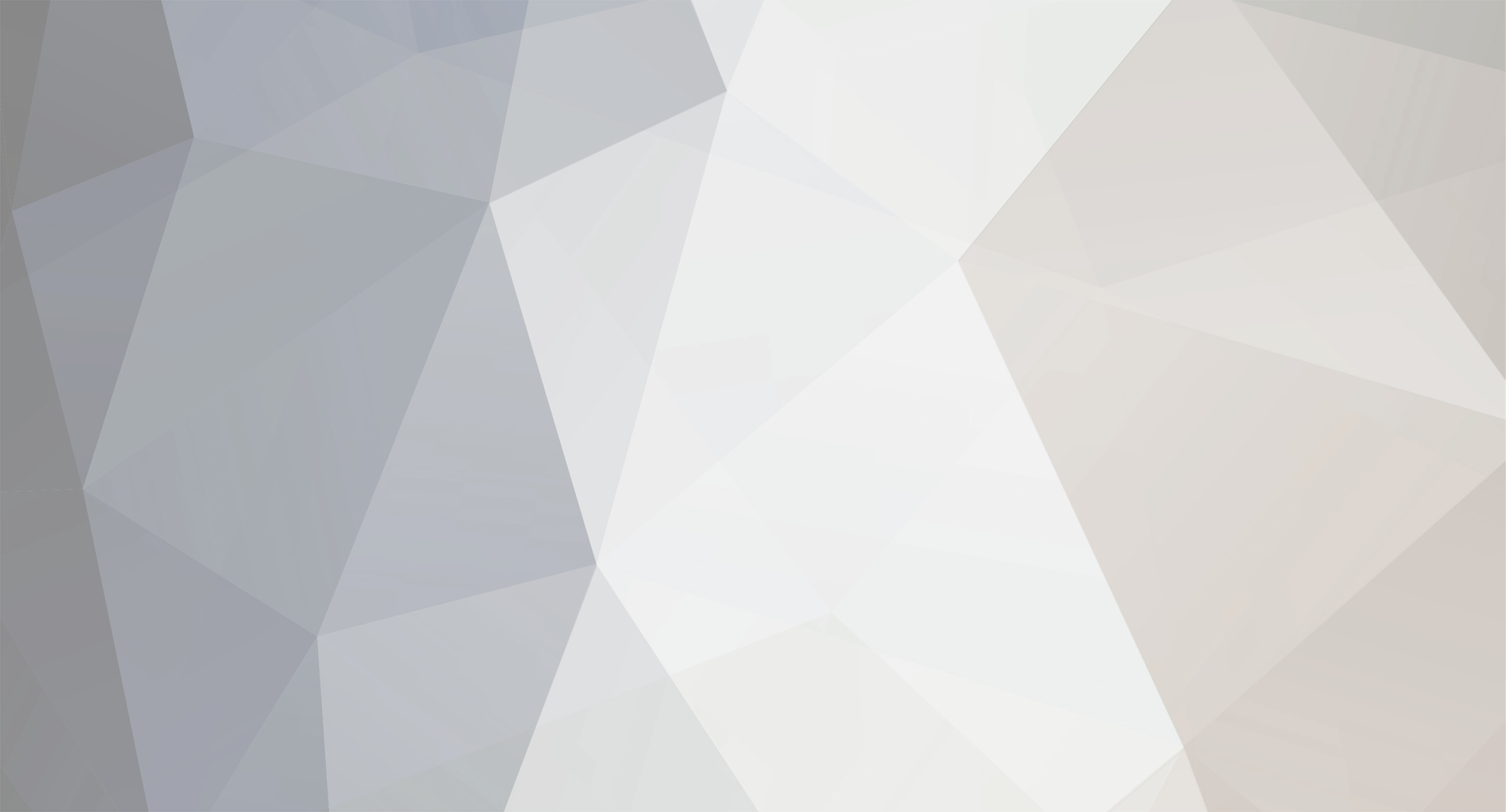
Martin_H
Members-
Posts
185 -
Joined
-
Last visited
Never
Content Type
Profiles
Forums
Blogs
Gallery
Calendar
Downloads
Everything posted by Martin_H
-
Reminds me of Chuck Yeagers Suitable Piece of Wood - a cut down broomstick so he could operate the overcentre lock on the cockpit door of the X-1 after breaking his ribs falling off a horse!
-
I rebuilt a Grumman Widgeon amphib in 1988 that had been sliced in two through the rear fuselage when lifted by a wire rope by an unsupervised crane operator. No drawings so I took a guess that the rear fuselage skin would have been manufactured from a standard 4' wide sheet of alclad. I eyeballed everything into position and filled the gap between centre fuselage and tail as best as I could and when we finally did get drawings from Grumman we were dead centre of their factory drawing, which gave a tolerance of plus or minus 1 inch for the fuselage length... I would LOVE to model this plane!
-
I haven't had any issues with the Deans connectors, though I am build rather solidly and wish I had a computer keyboard at least 1/2 size bigger to accommodate my fingers...I am a bit suspicious of some of the Deans STYLE connectors getting around though - these have only about half the depth of plastic on the male connector and don't give much room to grip. I only do this mod when I really have to - in most cases I can solder direct to the spade without any hassle, the method I have outlined has only been to overcome my inherent messiness when using noodle wire. For me Deans connectors are good BECAUSE they grip so well, other types of connectors that do not use friction to lock together use some other mechanical lock - Tamiya plugs for instance. All my batteries are fitted with Deans female plugs, that standardises the fit in all my applications and means I don't have to carry around different types and sizes of adapters for my charger. If Deans ever comes out with a three pin plug in a ' - l - ' configuration then I would be fitting them to the esc and motor wires! Edited By Martin_H on 31/03/2010 10:21:16
-
Nice! I find, though, that tinning the wire results in capillary action drawing most of my solder up into the wire... I tin the bullet connector and with the iron still in contact plunge the wire into the end, feeding extra solder as required through the little hole in the side of the connector. That seems to keep the solder close to the end where I need it.
-
Way back in my aircraft maintenance days one of the checks we had to carry out on the GAF Nomad undercarriage was a torque check of the clutch on the undercarriage electric actuator. This entailed disconnecting the chain drive from the actuator, fitting an arm with a spring scale attached then loading up the clutch by driving the actuator, reading the clutch torque on the spring scale... Part of the maintenance instruction was to 'place a suitable piece of wood' under the arm to prevent accidental damage to the skin of the aircraft. Being Military and having strict tool control in the workshop meant we manufactured 'A Suitable Piece Of Wood', catalogued it, painted it GSE Yellow and found a place for it on the workshop toolboard. For modelling I have found 'a suitable piece of wood' very handy. Mine is a piece of finnish ply, 25 mm thick, about 300 X 600 mm in size and covered on one side with a piece of 'caneite' (a soft pin up board material made from sugar cane waste). It gives me a soft side for pinning out and assembling small parts, a hard size for cutting and working on and is light enough to carry around and work from a lounge chair or the kitchen table. Edited By Martin_H on 31/03/2010 05:09:14
-
Hi Doug, Noodle wire is that very fine multi multi strand wire - it is very flexible, like a wet noodle, hence the nickname...
-
I recently bought a Turnigiy LiPo and was having trouble achieving a neat joint between the Deans connector and the batteries 12G noodle wire. No problems fitting bullet connectors to noodle wire so perhaps maybe combining the two would solve my dilemma. Soldering the bullet connector to the Deans spade then soldering the noodle wire to the bullet wire fixed the problem. This is how I did it: I drilled a 1/16 hole through the bullet close to the end as possible I tinned the deans connector with a good glob of solder Pushed the bullet onto the deans connector then soldered the two together using the 1/16 holes I drilled earlier to bridge between the bullet and the deans connector Repeat for other spade and bullet Solder noodle wire to the end of the bullets (remember to slide heatshrink over the noodle wire first!). Make sure the battery polarity is correct and heatshrink as you go to prevent shorts Heatshrink finishes off the job! I got so excited I made a second set! Edited By Martin_H on 31/03/2010 04:14:59
-
For building from/on plans - the non-stick Glad Bake and Cooking Paper - translucent, no glue known to man sticks to it, you can draw on it and its free! (As long as the missus doesn't find out you are taking it...) Whilst you scout the kitchen Nylon cutting boards (not plastic) are simply brilliant and come in assorted sizes and one universal colour (white).
-
David Boddington has had a great and magnificent influence on so many of us over the years so I thought I would start a thread on favorite Boddo designs. My all time favorite must be the Barnstormer series - not having built one myself but watching one magnificent and well crafted example of the big biplane version floating around the local flying club field converted me to big models. The DB Autogyro was a lot of fun - experimenting with different rotating directions on the two rotors, both clockwise, both anticlockwise, contra rotating ; forward over the fuselage and backwards over the fuselage, proved nothing but having a great time doing it! When I can clear enough space amongst the current projects I have the 1/8 scale Boddington Vickers Vimy to build. I remember well the story of the model and its debut in the Masters in Florida. Electric for me! Edited By Arte et Marty on 12/03/2010 15:41:58
-
BTW, We ended up building the EasyStar using fibreglass tape and hot glue. I was very happy with the hot glue, holds servos in place very well and worked a treat on the tailplane. Trick was to position the parts then apply a hot glue fillet. I found the DIY hot glue guns a bit cumbersome so invested in a quality one - you can get different nozzles and variable temperature with the one I bought. The fuselage was quick and easy - hot glue the motor in place on one side then place both sides together. Use 1" tape around the fuselage forward of the canopy, forward and aft of the tailboom then add the antenna and control outers with blobs of hot glue and tape their length with 1/2" fibergass tape. From the forward antenna hole around the nose, up to and back inside the cockpit area we used 1' tape, as well as along the top of the fuselage above the wing and the top of the tailboom. Hot glue around the rear of the motor, hot glue the servos and control horns and the structure is complete. We managed to build a banana shaped fuselage that was easily remedied, would have perhaps been a nightmare had the usual superglue and kicker been used. In use the tape and the hot glue seems to flex with the elapor during not so gracious attempted launches and untidy landings but stays together in flight and so far the only maintenance has been to give the tape a rub down between flights. Compared with my 'traditionally' built (cyano/kicker) EasyStar the performance is similar despite the impression of the extra weight of the tape however I have not used any decoration on either model, apart from painting some red and blue stripes on the tail and black on the canopy. Both models would benefit from a brushless setup! I know of one modeller who is using this method on his Cularis, he is allergic to cyano fumes and was at a dead end when faced with the construction of the model. My next father/son project will be the EasyGlider and if that s successful then maybe the Twister! I do think though the Twister may be the time to introduce cyano and kicker to my son's building repetoire.
-
Thanks Steve! I checked out the PU glues at our local Bunnings (Trade/DIY store) as well as looking at a couple of other forums. Certainly looks a winner as far as stickability goes and I wonder if it could be used on ABS parts too. One of the recommendations I found was to spray or wipe one side of the foam with water and apply PU SPARINGLY to the other, bring together and clamp or tape together. I guess practice would make perfect. Another is to add PU to water, mix well, pour off the excess water then apply with a brush and clamp up. Both the brands I could find - Selleys and Vice, carry warnings about handling and fumes so I dont think it would be suited to those with a superglue allergy (PU contains a cyanoacrylate ester as a reagent) or for young children. I use an Aliphatic PVA for furniture and plywood construction projects including my teardrop camper trailer and am considering using PU to finish off the teardrop. Thats my excuse, anyway. If a little ends up glueing model aircraft, well, thats life!