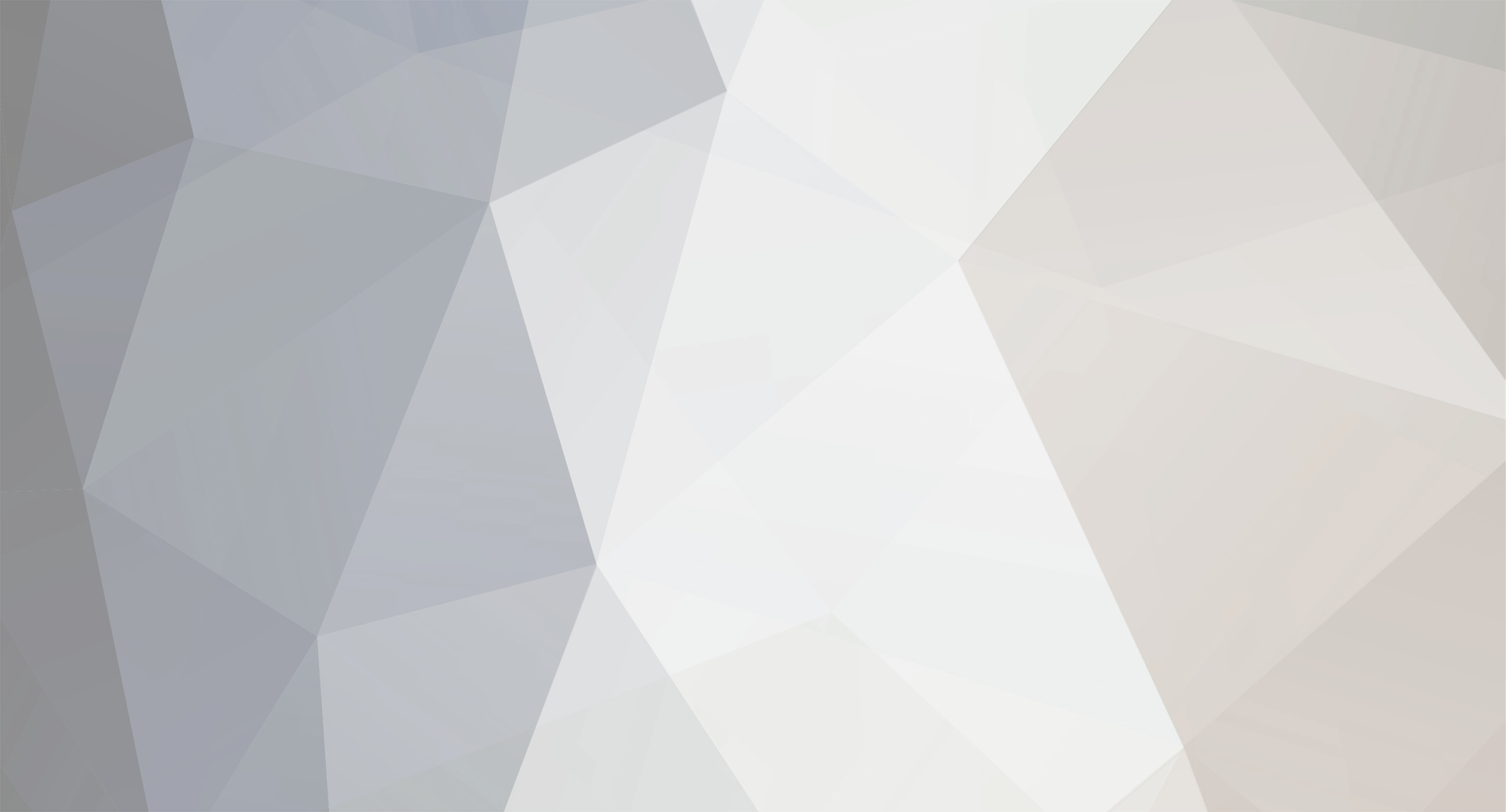
Tony K
Members-
Posts
294 -
Joined
-
Last visited
Never
Content Type
Profiles
Forums
Blogs
Gallery
Calendar
Downloads
Everything posted by Tony K
-
Not a lot of progress recently, other things getting in the way. I made a start on the upper structure but I've run out of wood for the sheeting. Also cut a set of ribs for the wing.
-
Thank's Ton. Here the hatch sidees are glued to the front and rear formers. I had to rough out some clamping blocks at the front to hold the sides to the front former. This is the almost finished hatch. I havn't decided what to do about the air inlet yet.
-
I spent a lot of time thinking about the undercarriage mounting and eventually decided to (roughly)follow the plan. I think the hatch is the next job.
-
A bit more progress. As the hatch will be larger than shown on the plan, I have added 1mm ply doublers to spread the loads and stiffen the sides a bit. As a secondary function, I have cut the ply 2mm long on the lower edge to provide a locating rebate for the hatch. The lower fuselage sides are glued to the centre section formers ready to be pulled in at the front and rear. The rearmost former in this picture looks as if it is set at an angle. That is a camera trick, all the formers are vertical.
-
Made a start on the fuselage. A further deviation from the plan is to make the access hatch bigger. At 75% of the designed size, it is a bit too small. I think I will extend it back to the undercarriage mounting. Also, I think the fuselage formers behind the wing (F6 & F7) are not necessary. The tapering box section should be stiff enough. I will put in a couple of 3mm square cross braces instead. The motor mount, F1, will be two pieces of 2mm ply laminated together. One piece is split (can be seen in the picture above) so that it can be aligned and glued to the base plate while it is flat on the bench. Then, when the assembly is turned over for the upper structure assembly, the other piece can be glued onto the front and the second part of the first piece glued in place.
-
Posted by Tony Smith 7 on 21/02/2013 12:39:52: 35mm diameter, 20mm length in that example. Edit, I should say that's the normal convention. Edited By Tony Smith 7 on 21/02/2013 12:41:47 That's a 30-45 amp motor with a 5mm shaft, it will be longer than 20mm.
-
Ton, I've sent you a PM. I do not have the experience to comment too much on your design. For quick and easy assembly of a kit of ready cut parts, it seems ideal. The "basic plate" (F0 on your plan) makes it almost impossible to build a fuselage that is not straight. So for that reason it is a good feature. No model building at the moment, we have visitors staying for a few days.
-
Graupner in Financial Trouble
Tony K replied to Simon Chambers's topic in R/C Retailers / Distributors / Manufacturers
Posted by Erfolg on 21/02/2013 10:33:57: I personally look forward to the day, when UK designed and built engines power formula one cars again. The Mercedes F1 engines are designed, developed, and manufactured in Brixworth, Northants. -
I consider myself a novice at this building game so I am following the overall design very closely but changing some of the details. Tailplane and elevators. Started thinking about the power unit. If I can keep the weght to about 1,5 Kilograms, 300 Watts should do. So with a 3 cell lipo, the motor should draw about 27 amps. I have a 1200 KV motor rated at 32 amps continuous which should do the job.