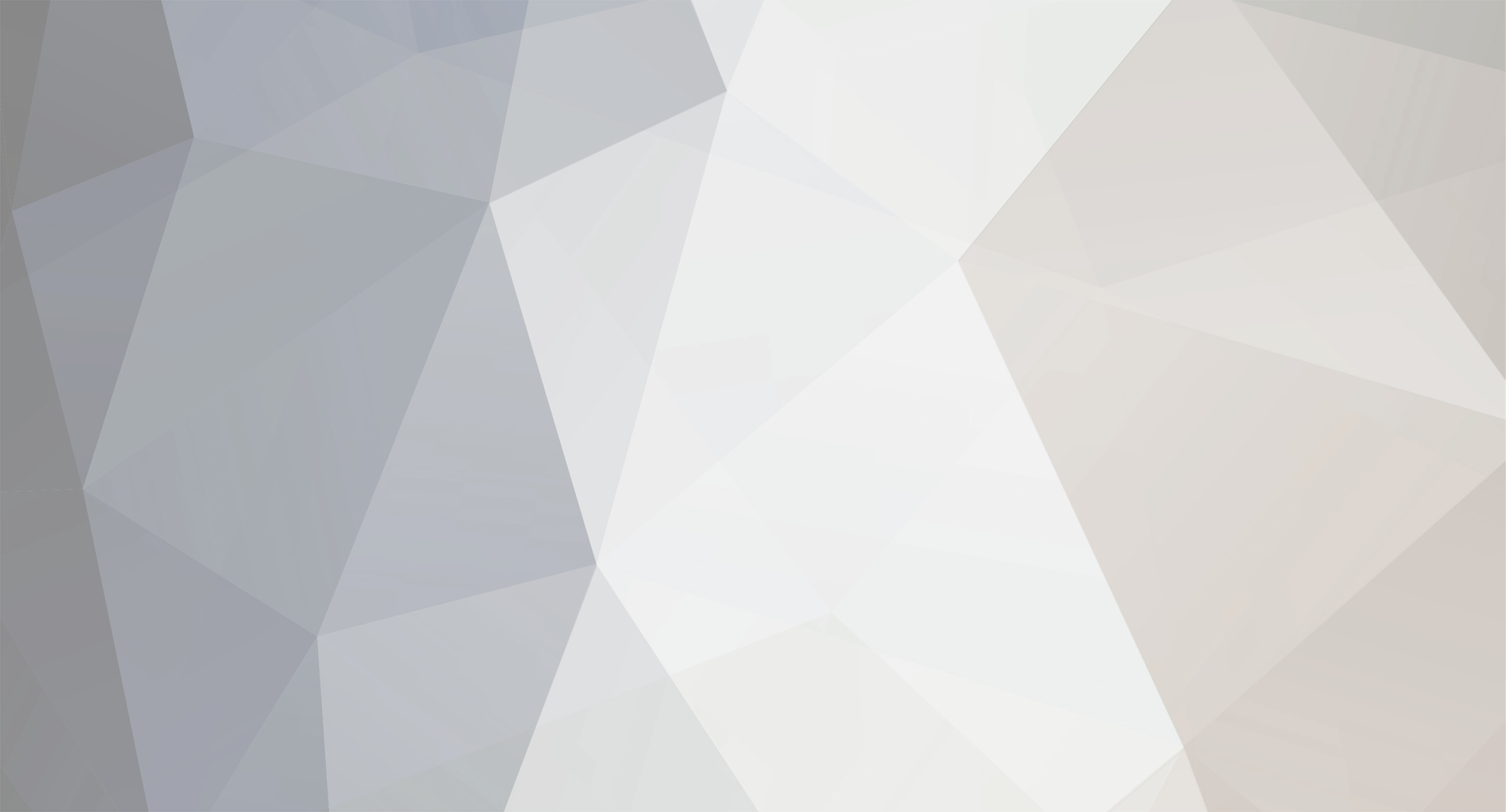
David Tayler
-
Posts
106 -
Joined
-
Last visited
Never
Content Type
Profiles
Forums
Blogs
Gallery
Calendar
Downloads
Posts posted by David Tayler
-
-
Having implanted hundreds of pacemakers over 20 years and studied the effects of arc welding upon pacemaker function I would say the risks of flying using EU compliant gear are very small indeed. Going near a domestic router on 2,4 G is probably more dangerous. Nevertheless most pacemaler manufacturers would advise keeping a distance of 30 cm between the transmitter ariel and the pacemaker. The implanting hospital or the pacemaker manufacturer should be able to provide more information ,although these understandably tend to err on the side of caution.
-
I may never need differential thrust but dividing the channels between the wings simplified the wiring. I have soldered most of it and used as little wire as possible to try and save weight.I have those green multiplex connectors for the signal wires ,one pair for each wing.The power connectors are xt60 .I have two 22003s batteries in parallel.AUW at present 6and a half pounds.span 72 inches.
-
Well I have solved it! When trying to calibrate the throttle I must have inadvertently gone into programming mode for the ESCs. With the aid of an Emax programmer I have now set up the ESCs to be appropriate for my motors.Low advance timing and a higher start torque.All 4 motors run up nicely.each wing has a separate channel so I could use diferential thrust if I feel brave! Thank you all and especially Kieth. David
-
Thank you for your thoughts and help. All the negatives are connected together. I have two batteries but they are in parallel.There is one esc per motor,but the signal wires are joined at the multiplug where the wings join the fuselage.I will try unsoldering these and test each motor individually.I am hoping not to have to do a major rewire as that will involve cutting through the glass covering the wing and a major rebuild!!
-
Chris, One esc supplies the receiver .No supply to the others-my error in the post above.David
-
II have tried calibrating the throttles- indeed when I did this ws the time the problems started.The ESC can also be put into programming mode by powering up with the throttle at maximum. I wonder if this is where I went wrong. As to wiring I have one signal wire to each ESC , connected together in pairs at each wing root.I have two channels for throttles ,one for each wing.,The negative wires are common as are the positive ones. Only one esc provides the positive supply.
-
I have built a four engine Lancaster out of Depron foam with some balsa reinforcements . The wings are sheeted in 3 mm Depron and contain the wiring for the motors .I tested the motors and theESCs prior to installation. One ESC provides the 5 V supply to the receiver and servos. All the motors run without the propellers but with the propellers fitted, three of them just rotate slowly, unless flicked round when they burst into life- ouch blood to prove it! The ESCs are EMAX 20 amp Simon K-series and are producing lots of bleeps. I wonder if I have inadvertently got them into programming mode, or that the problem is caused by having an inappropriate program for my motors. The behaviour is the same whether I use a receiver or a servo tester. There is one wire to each motor to transmit the servo pulses. I am looking for a reprogramming card to try and solve the problem but they seem to be unobtainable now. Does anyone have a surplus one I could buy? Or has anyone any other clever suggestions which will save me doing major surgery to the wings and the nacelles?. David
-
I have the yellow pins.I also got fed up with stabbing myself.But a bit of blue foam or depron keeps them point down nicely.It releives those nasty pin pricks. My pins still rust when I leave them covered in aliphatic .
-
I wonder if one of the clever 3D printer experts could print something similar and then make the files available on Thingiverse or similar? It looks a useful tool.
-
I check my 1S cells under load. To make a simmple battery checker all you need is a digital volt meter module( less than £2 from China, a push to make switch and a 4.7 ohm resistor. I described this in a letter to RCM&E a few years ago. Failling cells will show 4.2 volts when fully charged, but the voltage collapses under load.
-
Dear Ray, If I sent you a box of 360 x 800 x30 mm could you put the depron in it and post it back to me? I would of course pay postage, and for the depron. Thanks David
-
Thanks to all who have ofered advice. I have ordered some aero depron and will try cutting 6mm white down with a hot wire. It largely seems that I have missed the boat for 2mm white depron ,which is a shame as I have built 3 Fockers and 5 Chipmunks out of it,and they fly well. Plans for the Focker will be published in our club magazine shortly! The vector board seems heavier and more floppy, but also more resillient.;However for indoor flying lightness is everything. David
-
I have been making models for indoor flying out of 2mm Depron. Recent internet searches for more supplies have been fruitless. Does anyone know of a good source of 2mm depron. Preferably in the UK. Thanks ,David
Edited By David Tayler on 27/10/2019 21:07:03
-
I straightened the wings of my Lidle glider that I converted into a twin motor plane by cutting part way through them then filling the v with PU adhesive( Gorilla glue type of thing). Held it all down flat ,clamped to a board while the glue dried and it has worked a treat. I suggest some masking tape under the glue line to make sure it does not get stuck to the board! David
-
Daire, Do you know the brown out voltage for your receiver? 3.7 volts seems rather low for a receiver supply .However you say 2s. if that is a lipo that gives 7.4 volts which is high for many servos. I hope your new esc will give 5 volts which is fine for most receivers and servos.
-
If you PM me your address I am happy to send you hard copy of the plans and article. David
-
Thank you all for the help ,especially Andy in this instance. I can now see all the cells and the total. My current sensor arrived yesterday so I will add it. I think for the air speed sensor it may be as cheap to buy the Frsky modulle,even if that seems like cheating!
-
Chris and Mike, Thank you for your help. Sorry to be confused by the Frsky/arduino nomenclature. I now have a module almost working for lipo voltage. I have the following display on my Taranis X9D;-
1: A2 11.1V( presumably from the receiver)
2: Cels 11.49V
3: RSSI 84dB
4: RxBT 5.0v
5:Vfas 11.50V
I only have 3S lipos and have not yet built the current sid eof the modue.The arduino pin connections are as per Chris's diagram/ PCB. VFas_SOURCE VOLT_3 to use the balance lead. Why do I not have individual cells displayed ? Also I have a series of flashing stars on the transmitter display.Why?
Thanks for the project I am gradually getting my head round it. One last question is there a cheap airspeed sensor available?
David
-
Chris, isn't A4 used for SDA in the I2C bus. David
-
Thank you Steve, My store will be the 23rd too.I will be there! David
-
Steve, How soon is soon? Last time when there were gliders Lidl had sold out by the time I got there.Thanks
-
Chris,I am watching this tread with interest.I have read the"H" files but not yet tried programming my Arduino . I would be interested in two pcb's.
-
I have poured cough mixture into my Taranis and Amber has lost her Dakek speach. Seriously though I had the odd speach with my Fun Cub selected,I moved to my Acrowat and the speach improved .I went back to the Fun cub and all is now fine. I am at a loss to know what was wrong but it seems to have righted itself! Thanks to all who offered suggestions as to the cause of the problem. David
-
Chris, The sound files sound fine when played on a PC. They also sound OK when played in my friend's Taranis which is running 2.2.2. Should I try to go back to that?
Mains charger / converter 13.8v anybody?
in Batteries and Chargers
Posted
If you are happy with simple electronics or can find someone to do some simple soldering for you ,you can't beat a computer server power supply.As many watts as you could wish for; long term reliability and cost abou t£20.240 volts ac to 13 volts DC.