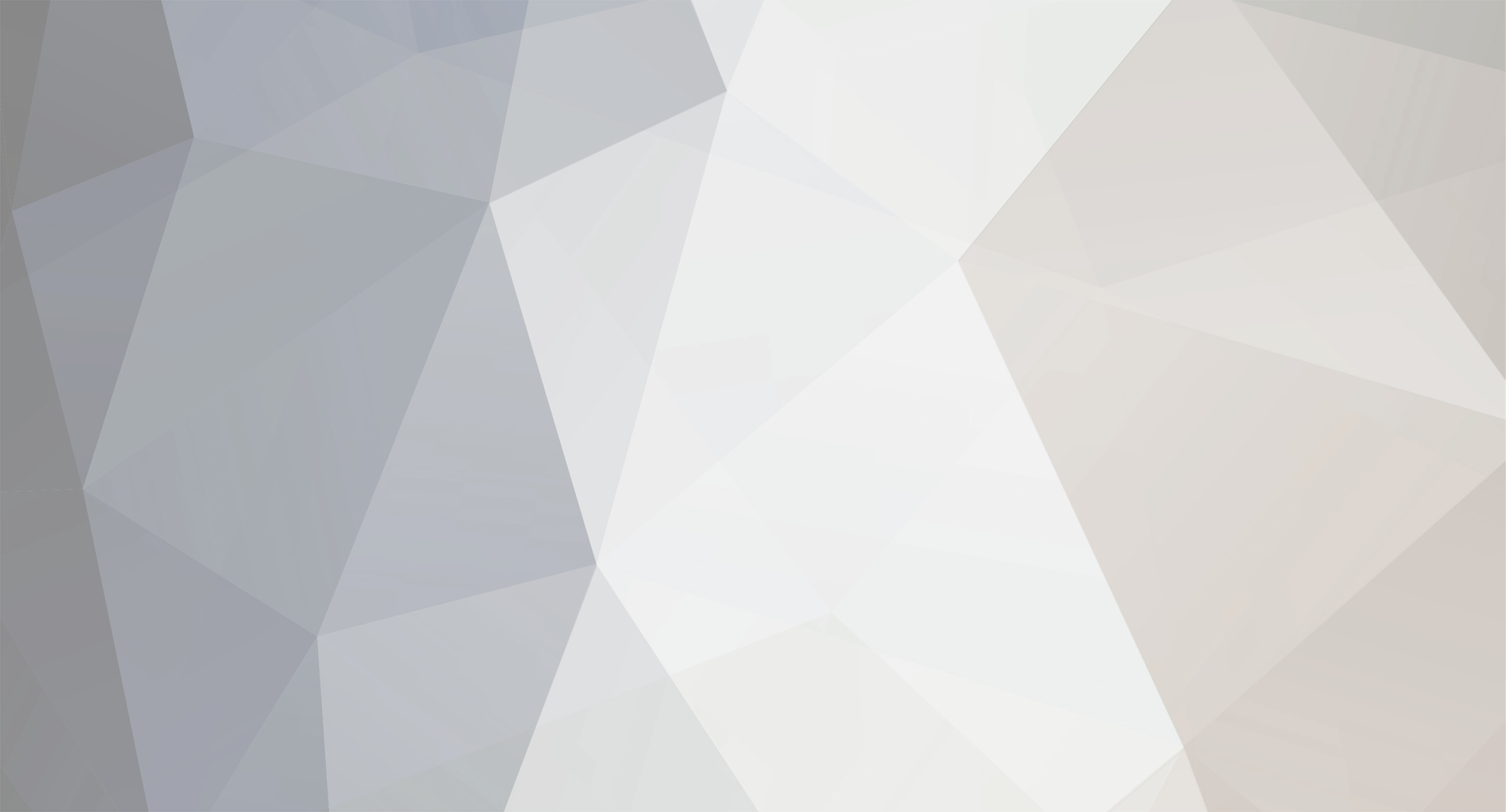
kenking-King Design
Members-
Posts
1,169 -
Joined
-
Last visited
Never
Content Type
Profiles
Forums
Blogs
Gallery
Calendar
Downloads
Everything posted by kenking-King Design
-
1/9th Halifax U/C
kenking-King Design replied to kenking-King Design's topic in Model Engineering and Accessories
cont'd. I know I said I'd not mention them again until finished, but couldn't resist a picture of the head sculpted to show the shallow ribs over the top pivots. The radiused edges help make it more casting-like and add a little more realism ... Just one more hot process to go through before filling in the arches, and that is making and attaching the leg clevis brackets for connecting the retraction arms. I scaled bracket dimensions from the Messier service manual cutaway, and have started machining them .... I'll get two out of this block, then repeat for the second casting ....... Once they're on, the arches filled in, and the brass liners with stud plates are bonded in, I plan to give a spray coat of silver/grey which I hope will complete the casting illusion. Can't wait for that. Then when Ben paints them black he can simulate wear and chipping in strategic places to reveal the casting colour beneath - a standard 'weathering' practice I've admired in the work of you real scale artists. In the meantime I've also started planning the dampers construction. I have four spring-loaded ball type non-return valves, salvaged from some hand soap dispensers, and hopefully they will play a part in changing resistance with direction. Silicon oil struck me as being a promising fluid to use, and I will initially run some simple tests, pushing and pulling a plunger in a tubeful, to get a feel for how resistance alters with different plunger clearances, using knowledge gained to fix the design. More on that later, Ken -
1/9th Halifax U/C
kenking-King Design replied to kenking-King Design's topic in Model Engineering and Accessories
cont'd. As a little light relief from soldering I took offcuts of the two steel tubing sizes to be used for the legs, set one into the other, then polished the smaller diameter, being the oleo leg which will protrude from the Messier casting ..... then positioned it in the sliding tube to see how it looked with the retainers and nuts ...... I thought that looked good, but decided I'd bored out the retainer plates too big, and there wasn't as much land left as I'd like to act as the downstop for the leg, catching the larger diameter tube. A second set of retainer plates was therefore made, corrected accordingly. If any of you are thinking I was just mucking about, looking for ways to avoid the final soldering job, all I can say is 'How very perceptive of you'. Having thought about it a bit more in the interim though, I realised I was needlessly making life very difficult by trying to solder on the INSIDE of the assembly, hence putting all previously made joints at risk. The idea had been to avoid much external cleanup, but soldering round the OUTSIDE avoided the dangers, so that's what I did. Trying to leave a proud bead resulted in some less than pretty seams .... and I can't pretend it was all plain sailing, but eventually the job was done. The trusty belt sander was used to VERY carefully reduce the beads back to the desired surface, bearing in mind the sheet components are only 1.5mm. The first one is sanded as far as I'm willing to go ...... and there remain small surface defects and sunken areas which I intend to fill screed over using Lilliput epoxy putty, before a final sand. Huge sigh of relief from me, and perhaps I detect some from readers who have been flogging their way through this saga, and are now look forward to more interesting aspects? To finish the 'castings' the arches and shrouds will have balsa infills and be skinned with lining paper to give a smooth continuous surface through the tunnel, and rear clevises added for attachment of actuating arms. I'll show them when finished; I reckon we've all seen enough of these for a while. you can all have a gold star for endurance, Cheers, Ken -
1/9th Halifax U/C
kenking-King Design replied to kenking-King Design's topic in Model Engineering and Accessories
cont'd. The final bend in each shroud was made in the vice, rigid laminate cut to fit neatly inside, and a bigger piece outside, much juggling to get things square and on the line, then tighten using a knee as is common practice. Another laminate block and a lump hammer persuaded the lid to close, the internal joint areas were cleaned up prior to soldering, then external sanding finished off the shaping. I'm showing the best of two, naturally ... With smooth surfaces it was easy to flip them over on the bandsaw table, and follow the premarked line for removal of the arch, rocking over onto the other plane as the cut progressed .... Then came careful filing and finger adjustment of bends to make a good fit on the mother assembly, which now begins to look much more like a Messier casting, in my eyes anyway .... Repeating with the second lot has presented me with two assemblies, representing considerable investment in time and minor burns, which now require final soldering along that crucial joint line ... and frankly, I'm dreading it. The eagle-eyed among you may have spotted the solder bead already in place but, sadly, unwanted movement caused that attempt to be abandoned, parted, and surface prep repeated. Tomorrow will be a better day for it, perhaps .... Ken -
1/9th Halifax U/C
kenking-King Design replied to kenking-King Design's topic in Model Engineering and Accessories
Hi Ben (Ben is the chap I'm making this for), some time ago I invested in a bench mounting bender, I think it cost £30 -£40, and was produced in limited quantities by a blacksmith or small engineering company when they had nothing else to do. It's very simple, so one has to juggle things to get the needed setup, but works pretty well. I'll include a photo of it soon. Scoring is normally to be avoided as it will act as a 'stress raiser' liable to initiate fracture. Speaking of which, on the first side fold I felt the aluminium crack as it reached 90 degrees, and soldering that crack has been a nuisance. For all the other folds I ran the small gas torch up and down the bend line (in the flat) a few times, and that slight degree of annealing was sufficient to avoid cracking. Another lesson learned. Glad you're pleased with progress, more later. Ken -
1/9th Halifax U/C
kenking-King Design replied to kenking-King Design's topic in Model Engineering and Accessories
Thanks Cymaz and Ace, I was beginning to worry that It was becoming quite boring - well, perhaps it really is for some folk, but not the more discerning ones eh ? I'll just carry on then. Ken -
1/9th Halifax U/C
kenking-King Design replied to kenking-King Design's topic in Model Engineering and Accessories
cont'd. Managed to grab a bit more shed time today, and finished soldering in the last arch piece, still using oxy-acetylene. At this point I should make it clear that, despite my earlier outburst, there is absolutely nothing wrong with my small gas torches; in fact they are very convenient to use. The trouble comes from the way I've made up these U/C assemblies with so many conjoined seams that any stray heat spells trouble. For a simpler assembly such a gas torch is fine, so don't be put off the process. Moving on to the front shrouds; these really define the unique shape of the Messier casting, so I'm keen to see them attached. They also form the crucial brace between the head/deck and the legs. I spent some time marking out the developed shape on 1.5mm sheet, and after the usual short period of confusion between what was waste and what needed to be retained, I transferred to the bandsaw, complete with new fine-tooth blade. Here's one of the cut blanks .... I plan to saw out the arch shape later after folding, as the sheet is more stable that way and the bends will benefit. The sides were folded up, leaving one more fold to give the extra angle on the front lower portion, with two short front seams to complete the shaping ....... At this point I couldn't resist sitting a part-finished shroud into position, as one does with such things. Of course, one then has to half close eyes, defocus, and imagine the rest, but we all do it, don't we ? Once soldered up there will be some fettling and filing to ensure a good fit to the main assembly, then some heart-in-the-mouth moments with the torch, around the head/deck shroud junction. Joining to the legs doesn't worry me too much, but if anything should happen to the machined head pieces !!! It doesn't bear thinking about.