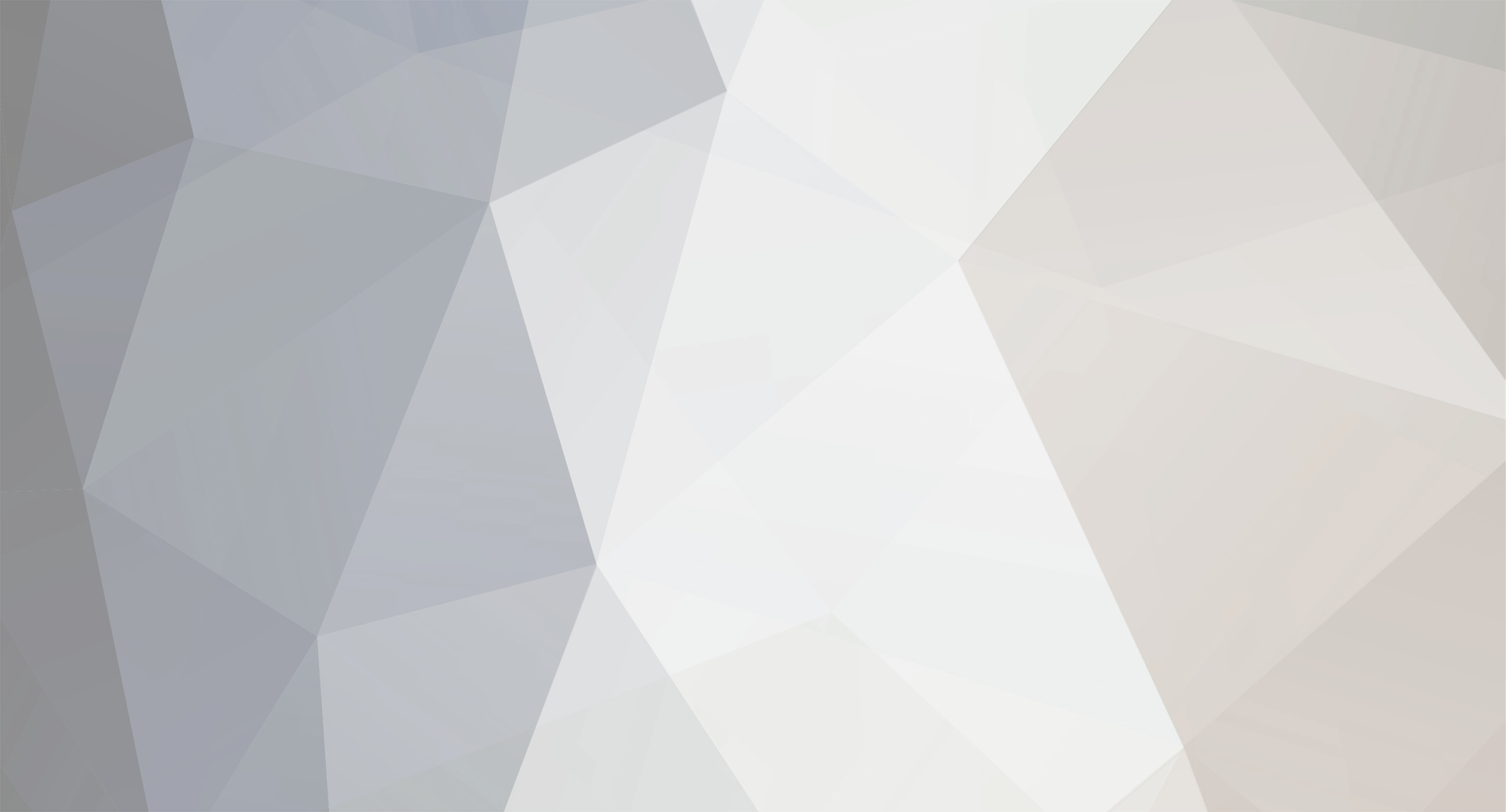
Tim Campling
Members-
Posts
277 -
Joined
-
Last visited
Never
Content Type
Profiles
Forums
Blogs
Gallery
Calendar
Downloads
Everything posted by Tim Campling
-
YT International 120 Spitfire build.
Tim Campling replied to Tim Campling's topic in Build Blogs and Kit Reviews
Ok, today I fitted the new pull pull cables from those nice guys at Slough Model Centre. The Sullivan 2-56 kit has 40lb steel trace and all the fittings, (but £15 seems a bit steep)! Anyway can't fault the service. I've used the Sullivan Gold n rod snakes before and the hardware is excellent. I opted to solder the trace into the clevises at the torque rod, remember to pass the wire through the clevis twice to provide security. Unfortunately, the holes in the torque rod were too small and needed to be enlarged. My only option was to drill through the fuse but the 2mm holes can hardly be seen and can be easily fixed. At the servo end I have made a simple bell crank to prevent loading the servo bearings on one side. By using two pushrods I have elliminated any twisting action on the crank mount. The pull pull kit has threaded loop arms for the metal clevises that allow for precise tension adjustment. It is important to make sure all the trace lengths and push rod arms are the same length and tension to prevent binding. A bit of time spent here meant that the trims were all at neutral with no servo buzz. Once set, thread lock! I fitted a piece of ply across the open space to take the receiver. This also stiffened up the crank mounting. The tank is held in with a cable tie and sits on foam as does the receiver. For your information there is a great foam product called Dynaliner. It's available from good car audio retailers and is more commonly used as a sound proofing product. It comes in 1/8th, 1/4 and 1/2 inch thick, is sticky back and light. A full sheet is £60 (enough to line two car doors) but your retailer is bound to have some small off cuts. I'm going to install a glow driver next. By the way, I'm wondering if it's a good idea to mount the flight batteries on the engine mount. I'm concerned about vibration but it would help to get the weight forward. Any thoughts? -
YT International 120 Spitfire build.
Tim Campling replied to Tim Campling's topic in Build Blogs and Kit Reviews
Most excellent mate! -
YT International 120 Spitfire build.
Tim Campling replied to Tim Campling's topic in Build Blogs and Kit Reviews
Hi Alan The wing is one piece and feels and sits better for it. I did radius the torque rod holes but I fancy a heavier guage trace and I will grommet the holes as well. It's good to be back on the build. I saw that vid of yours with the sound effects again and got all keen again! -
YT International 120 Spitfire build.
Tim Campling replied to Tim Campling's topic in Build Blogs and Kit Reviews
The rudder hinges are the barbed pin type and holes need to be drilled into the fin and rudder. Easy enough and there is a wood strip inside the fin but I found the strip to be quite soft. for security I ran epoxy inside the fin where the pins protruded, I don't want them pulling out! I've been very careful to minimise weight at the back end but felt that this extra glue was justified. Next I fitted plastic tube at the pull pull cable exits and assembled the rudder/tailwheel linkage onto the rudder. The pull pull cables are threaded through and the tailwheel steering linkage assembled. The manual recommends quite a big movement on the rudder so that packer on the tailwheel bulkhead plate is essential. Finally assembled and looking good with full movement and a nice even gap. Now at last she sits on her own wheels! Next for the radio and engine. Allthough I couldn't resist a quick mock up now I've got the spinner! -
YT International 120 Spitfire build.
Tim Campling replied to Tim Campling's topic in Build Blogs and Kit Reviews
Next job is the tailwheel. This has a steering arm driven from the rudder linkage and just needs to be assembled onto the bulkhead plate before being screwed to the former at the front of the wheel well. I spaced it off the former by 6mm as the steering arm fouled the fuse otherwise. I wanted to set the wheel as close as possible to the fuse which should help ground handling and give the Spit a nice nose up attitude when sat still. To facilitate screwing the bulkhead plate to the former cut a screwdriver size hole in the back of the fin. I also had to relieve a bit of the fuse to allow the steering horn a clear path. The supplied elevator pull pull traces are in at this point but I think I am going to change them for a heavier guage. There is a wheel well cover and I'm not going to install a retracting tail wheel. You can't tell from the picture but there is decent gap for the spring to operate. The cover will be screwed to the fuse to finish. Next the rudder. -
YT International 120 Spitfire build.
Tim Campling replied to Tim Campling's topic in Build Blogs and Kit Reviews
Hi all. It's been a while but I'm back on the case so to speak. The long gap caused by work, family and a Black Horse Stuka! Well as advised I have produced a new wing joiner that has no slop from marine ply. A tip I picked up ages ago was to use the plastic wing bags to protect against epoxy finger marks. Next up was the elevator. This has a torque rod that passes through the fuse and is intended for a pull pull system. Neat as there are no external horns. The rod supplied is substantial enough but was twisted and I took care to make sure it was dead straight first. This passes throgh the fuse slots before the plastic hinges are glued into the stab. Take great care to cut the slots EXACTLY in the centre or the elevator will be offset. Once glued in place I smeared Vasaline over the hinge before glueing the torque rod into the elevator halves one at a time making sure the cyano wick hinges engage into the slots. Small strips of card ensure no glue from the torque rod holes squeeze onto the stab. Don't forget to rough up the metal rod for a good key. Finally wick cyano into the hinges to finish.