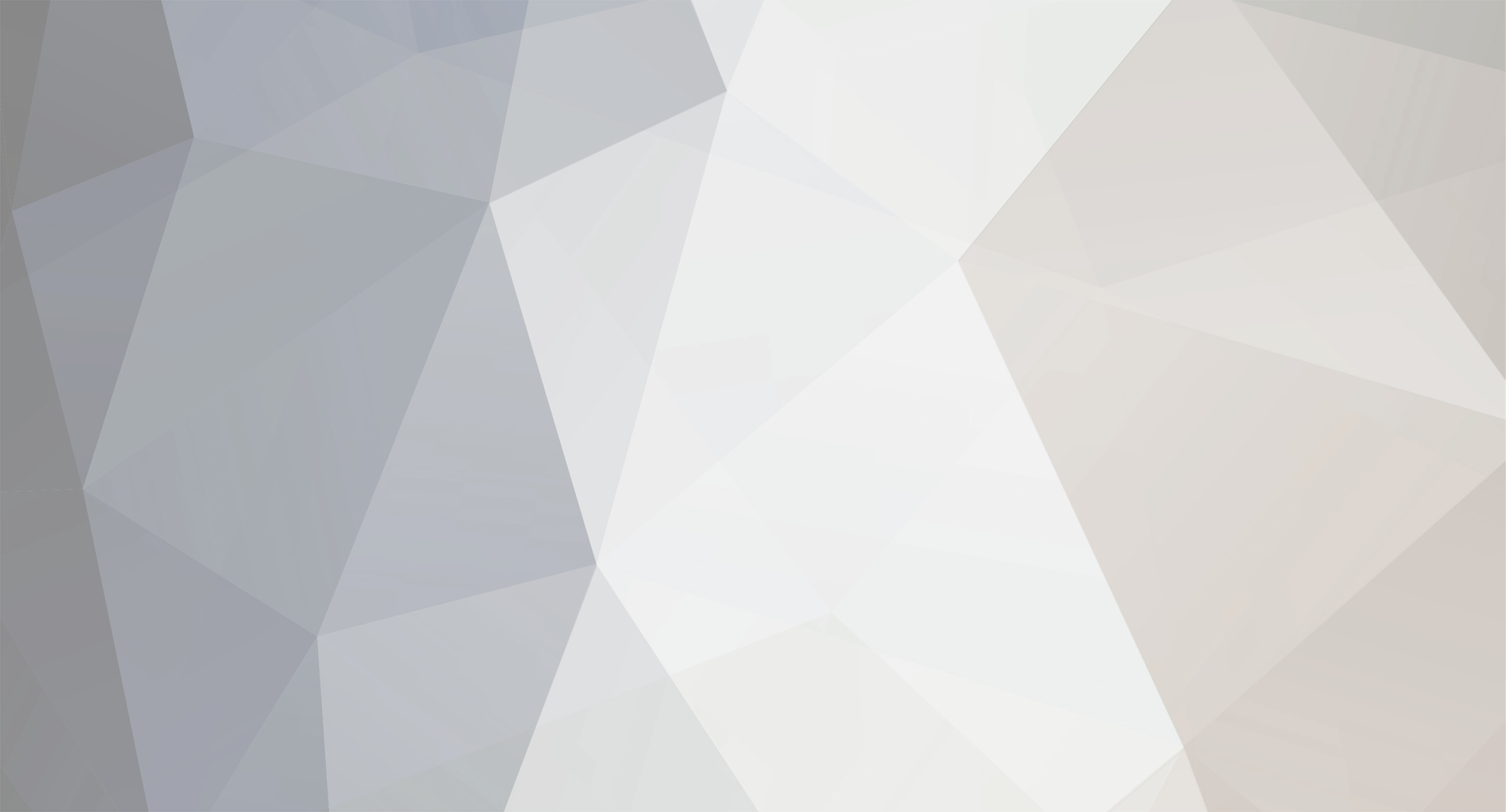
Craig Spence
Members-
Posts
1,911 -
Joined
-
Last visited
-
Days Won
1
Content Type
Profiles
Forums
Blogs
Gallery
Calendar
Downloads
Everything posted by Craig Spence
-
Fitted both stabiliser half’s and screwed in place. They’ve taken really well and the alignment with the fin looks bang on so happy with that. Over the weekend I should be able to fit both elevators and give it dry run to see if movements are ok. Then I’ve gotta figure out control horn fixing, I’ll probably use G10 and epoxy in place.
-
Thanks Ron, it does help a great deal and much appreciated ?? The hinge points are bang on as plan and the leading edge does go above the trailing edge of the stab. I have a trailing edge to add yet which will help (although only 1/8th”). I won’t have a great deal of movement on the elevators so they won’t be much above like on the video. I may however put more of a chamfer on the leading edge of the elevators but only once I have the trailing edge complete on the stab and it’s in situ on the plane. I don’t suppose you have anymore photos? The only one that was in the UK got shipped off a couple of years ago.
-
Mate, it’s not a question what 3D pilots do or any otter pilot does. It’s scale and designed for a purpose as stated in the article I posted. It’s not for yaw like a fris’ ailerons (not sure that’s the right spelling though ?). It was designed like that on the full scale planes to reduce the amount of force a pilot had to put into the stick for the manoeuvres. The exposed edge got caught by air which made pulling the full surface easier in a nut shell. Since most planes are hydraulic, electric or pneumatic now or all 3 (A10) there’s no requirement for that design any more. Hence why you only see it on some warbirds. It is as the real one was built for the reasons detailed in the article ?
-
The extending leading edge is designed to get drag to help the pilot pull manoeuvres with manual controls. The leading edge will catch air and help deflect the surface more so pilot doesn’t have to rely on brute strength. How did you read it? A lot of warbirds have this on the rudder & some civils. As well as ailerons as well.
-
Hi Danny, I agree it is unusual but it is scale to the plan and scale to the aircraft to have offset hinges for rudder, elevator and ailerons. I believe the reason is as you say but to actually cause a high point of drag, meaning my landings will be hot ?? The only conventional hinge is on the flaps which are bottom hinged. It is an unusual aircraft and was ahead of it’s time but also with many faults ? I’ll post a reference later ? Cheers.
-
Small update tonight. Added tips to one elevator and sanded the leading edge and tip. Functioned to see if all is ok and it’s looking good. Hopefully I’ll get the stabs and elevators finished this week and then move back into the fuselage. Still waiting on retracts (end of June!) but I’ve decided I’m going to go ahead and sheet it after drilling holes for the nose retract and adding t-nuts. I’ve asked the manufacturer to not drill holes in the mount so I can sheet the model without fear of issues. I have found a right pig of a curve to sheet on the main wing fairing which is really going to test me. I’ll add updates when that happens ?
-
Decided to crack on with one stab half. Sheeted it and decided to cut the servo hatch (the hatch will be made after glassing and I will cut it from G10). To extend the bolt out of the skin I decided to use carbon so I can sand it down easily enough (with a bit more prior thought I could have done this a lot neater but it will look fine and won’t add much weight). Filled in the gap around the tube by layering balsa from the inside and then cut the tube with a dremel and slowly sanded it down. Fillers been added and I will do the final sand tomorrow if this area and move to the other stab.
-
Cheers Danny, cheers and great to see it done like that ? The plan calls for a dowel and a T Nut but I swayed for this, the way that is done is better as well as the tube goes through the sheeting, I’ll be cutting around mine and sanding flush. it’s not great but will look good once sanded and glassed ?
-
It’s been a while! I’ve been away for celebrations past few weeks. There is a method to fix the stab to the fuz but I preferred a different method for maintenance purposes. I screwed in a threaded insert at near 45% angle, then drilled out a dowel which will be the fixing point later. The dowel will be reinforced locally as well. I will later add a carbon tube to guide the bolt down to the dowel and sand flush. The plan method is to insert a 10mm dowel into the fuz stab rib and on the end of this would be a T-nut. I’m not keen on this for alignment and also if the tail plane ever takes a knock it would mean serious surgery. Whereas if the tail plane takes a knock with a threaded insert it’s an easy fix. Retracts arnt due until end of May now so more delays!
-
Fitted 20kg Savox servos today and continued with hinging. The hatches for the servos will be all in one, I’ve done similar with my bolt and it will become apparent later. Elevator horns will be made from G10 and slots will be cut later to accommodate these, the elevator leading edge is mainly balsa but the hold will be strong with these epoxied in. Gonna be a while for the stab and just as well really, just told yesterday that retracts won’t be turning up till end of May now! I just they don’t turn up ?, the fellas a nice bloke so I’m sure they will. But so far I’ve had 3 months delay to the project due to the kit and retracts. Hopefully I can get it finished this year as that is the plan. Hope everyone had a good Easter break
-
Little bit of work done the other night. Added foam tip and base to rudder, I will have to put finishing resin on this to toughen it up at a later date. Started the elevator halves and hinging, I used lite ply for these which is proving to be a good choice as the rudder weight is quite high with the birch (supplied in kit). Decided to cut the elevator half’s myself. Have a good weekend all
-
Well, turns out waiting for parts has really done me a favour because I’ve noticed a load of things I need to do before sheeting. Tonight I’ve been working on the stab & it’s been great, as previously said I’ve noticed a few alignment issues and it’s really helped. I e also glued foam & started shaping it to the rudder, if it’s over or under the profile I can sort it out so all good. Tomorrow I think I’ll start the elevators but I’ll be using light ply and not birch, this should help keep the weight down and still maintain the strength. Also had a good drink, why not Anyway, happy Easter to all ???????
-
Framed out the other side of the stab tonight. The fit between the two is great although was tedious trimming the holes. Stops are in for the tubes now and I’ve decided to go against plan screw into the wing tube to fasten the stab. I’ve also found that the hinge holes in the tail are out by about 1.5mm! Doesn’t sound much but it will mess up the geometry. So In a way, I’m glad I’m still waiting on bits because once the stab and elevator are complete I’ll have to do surgery on the tail of the fuz to change the hinge point!? Not a major though and I will replace the brass for a carbon tube now with a 3mm internal diameter. This way I can fit the elevator, align the hinge in the fuz and glue in place. I know better but never mind. I’ve also found out that I’m going to need some smaller high torque servos for the stab. A standard one will fit but much better to have smaller ones and room to adjust. Waiting on parts for the stab now.
-
Small update but a lot happening. Haven’t done much this weekend as I decided to take one of the warbirds out flying (a bit rusty as well but all good). Moved the fuz so I could start on the stabiliser, again this will be another half finished job ?? I have to wait till the fuz is done before finishing the stab! Anyway. Had to open up the ribs where the tube passes through and a bit of fiddling about getting the angles right for the tube but it’s all good. Just need to get some spruce and I can start the other side. Putting out an order tonight I think.