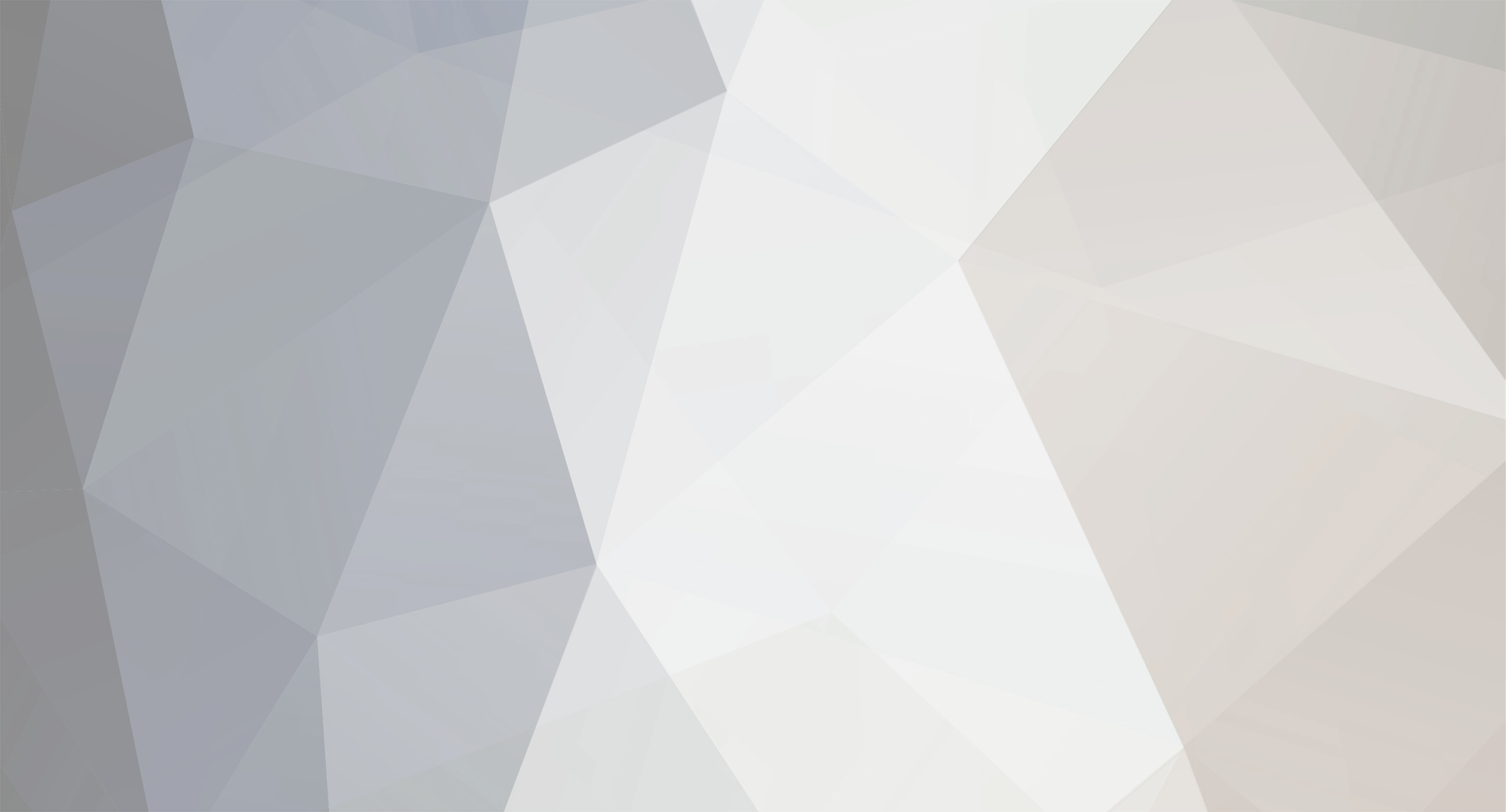
Ajohnw
Members-
Posts
36 -
Joined
-
Last visited
Never
Content Type
Profiles
Forums
Blogs
Gallery
Calendar
Downloads
Everything posted by Ajohnw
-
Have to disagree about lead free solder and long term joints. The automotive electronics industry would be in terrible trouble if it didn't. Component failures are measured in so many per million hours of operation (fits) on some of the more critical bits. Rather impressive when you consider how many there are about. There shouldn't be any problem at all re soldering with lead solder but when using lead free a flux pen is needed or hand soldering can be very difficult. Flux pens are tolerated in the work place as a result. The only possible problem is the flux in multi core. It is usually corrosive so should be cleaned off. On the page some one linked to a no clean multicore is mentioned but if it's the same as the one I use it needs a relatively cool iron (weller 6 from memory) as the flux turns corrosive if over heated/burnt. The data sheet might tell you. Modern components also benefit from very thin solder wire. As with all fluxes it's best to not breath the fumes. Flux should be cleaned off. When the boards are made this is usually done with a product such as safewash 2000. A brass pencil brush is as good. Those are the pens with a brass or fibre glass insert that emerges as the end of the pen is turned. Resoldering a 2.4ghz rf board may prove problematic. Even the track width and spacing on the circuit board in the actual rf area of the board can have an effect. If I did that because I had too I would take some care and apply a minimum amount of solder. If it's a dry joint a flux pen and the soldering iron will probably cure it. I would have to wonder how one gets a dry joint on a surface mount board though. Solder paste is applied through a screen, parts are often stuck down and then the lot is passed through a reflow oven. Heating components for too long can damage them so the job has to be done fairly quickly how ever it's done. John
-
Having spent many years working in an electronics automotive factory I can assure you all that there is nothing wrong with lead free solder. All down to process control or lack of it if things go wrong. There may be a bit of a problem with hand soldering due to the absence of flux. At home that can easily be fixed with a flux pen. If any one does their own repairs it's well worth having one of those anyway even if there is still some multi core lying about. People who hand solder with it all day usually use a rather hot iron say weller 8 or 9. I've used this thread to comment because it relates to several comments about having it fixed by the distributors and the wonderful turn around. These days they may have done anything to it and may well have just updated the software. If they are sensible manufacturers it should be possible to do that at home. One aspect of software has changed dramatically over recent years. Microprocessors that are cheap and can be programmed easily usually after the circuit boards have been built. This tends to make companies more relaxed in the testing and proving areas as they know that the software can easily be changed by simply re programming the unit what ever it is. John
-
Having had some fun flying micro heli's mostly over a double bed and having motor problems with 2 of them I thought I would try something different. The double bed makes flying heli's cheaper by the way especially for the 1st few flights while trimming is sorted out. While browsing through Hobby King I found the ep100. Looks to be mostly made of plastic and has cp and is fitted with all separates rather than a 4in1 or something similar with a couple of esc's. It also comes with a brushless motor and a belt driven tail all in a heli with a 340mms rotor diameter. Has anyone else tried one and have any comments?. The reviews are rather mixed but for what they cost I thought it was worth a try. I've seen several of them in video's on the web but generally with a different rotor head. Does any one know where these come from? I have also read that the ep200 is the same and just uses longer blades and a more powerful motor. ??? John
-
If I wanted 2.4ghz it would definitely be the one I would buy. It seems to be the only one on the market that offers rx's with sensible aerials on the end of leads rather than 2 bits of wire. This leaves a lot of freedom for mounting and can easily cope with carbon fibre fuselages and other possible problems. John
-
This helicopter gets worse. It was supplied with the tail motor reversed. Fixed that, balanced the blades and checked tracking and it's the most unstable one I have tried to date. Me thinks there is a fault some where. Looking at cost plus spares it would have been better to buy a new one. John
-
Not sure if I would support 2.4 aerials as it may well cause problems. Microwaves can be curious things. Watching the news tonight a problem with Apples latest i phone was mentioned. It seems that some people held these in a way that Apple didn't think they would and the result was no reception. The cure seems to be a thin clip on frame that quote " allows the phone to adapt to the user". Another odd one. Use your cars keyfob and see how far away from the car it will work. When out of range, point it at and touch it to the middle side of your head, look at the car and press the button. You may well find it will work like that at even at 3 or 4 times the normal range which is subject to general conditions any way. Seems a head can capture the signal concentrate it and maybe beam it out of our eyeballs. No doubt there is some other explanation. Who knows but it works on all of the cars I have owned even the newer ones that use short range fobs. John Edited By Ajohnw on 07/08/2010 21:47:45
-
From memory going way back getting theoretic radiation patterns out of a simple monopole vertical aerial involves radiating metal ground rods or mesh a long way out in all directions from the aerial to give an effective ground plane. The wavelength is rather long at 35mhz so classical theory doesn't really apply especially to an aerial sticking out of a transmitter. A simple T type dipole helps get round this sort of thing. One half of the top of the T forms a sort of reference for the other with a low resistance feed point in the middle - just what's usually wanted for efficient radiation. My understanding is that theoretical performance is more likely in the microwave regions as the wave length is so much shorter. Be interesting to measure the field strength around a transmitter. The "Spektrum effect" may have another aspect. Are these incidents more prevalent than they were on 2.4gigs earlier days when there was presumably only really those about. Implying that things have got worse as more futabas have appeared. I'm basically a design engineer who finished up working on automotive software for rather a long time often sorting things out. Brown outs to me usually mean software bugs or inadequate processing of incoming information. More often bugs. Bugs sometimes turn out as features - wow I didn't know it did that - isn't that great or at least the bug can now be added to the user instructions or features list. This area is basically why I feel there aught to be some standardisation of the basic mechanisms used by the different manufacturers. This doesn't have any bearing on what information is sent by the transmitter only on just how it should go about doing it. There are many such standards about in other areas and we could all be a bit more confident if this area had one too. John
-
Does anyone know which if any of Futaba's synthesiser modules will work with this transmitter. I have seen an asian site that offers the 72mhz version of the TK-FSS for the 9Z but also states that it will work on the FF8 as well. They also sell the 35mhz TK-FSS but don't state that it will also work with an FF8. It would be a little odd if they had restricted synthesisers to 9 channel transmitters. John
-
I suppose I am a little reactionary on this subject as I have been in and out of models of one sort or another for many years. 2.4ghz came as a bit of a surprise especially after I looked at the equipment that is available. Receivers with 1 wire bent or not, others with 1 or 2 V's. Then there is the aerial on the transmitter itself. In theory point the stick at the model and it will receive no signal at all or if it's vertical none if the model flies directly over head. That aspect would lead me to expect maybe a horizontal T shaped aerial on the transmitter, more self contained and less dependent on the surroundings. Might even make a decent carrying handle. All this and the other points I've mentioned make me wonder about the whole thing. Basically cheapness and excess distributor profits gone to far. anyway just bought an ff8 and that will meet my more recent helicopter needs and my old digi fleet suited me for my occasional use of a glider while I await further developments. I do believe there will be some changes eventually. I've toyed with the ideal of a small self designed powered glider for some time and would have thought rather basic screening and filtering techniques would rule out any interference, Even that 2,4ghz micro heli has the usual small capacitor on the motor terminals just as they always have had. Motor brushes can create a lot of very high rf interference. Maybe the receiver power also needs some added capacitance. John
-
I think my comments on the ratio of those 2 systems out there stands for some time. No doubt more people will buy other brands as time goes on and then we will see. Yes TV aerials are directional and just illustrate an affect that many may have experienced. This does make them more sensitive to near by things but this affect gets worse as the frequency goes up. All aerials are affected by nearby objects due to capacitive effects. These appear as shorts to the aerial that drop in resistance as the frequency goes up. The wavelength of 2.4ghz is only 125mms if a quick web source is correct so all of the 2.4ghz model aerials I have seen are moderately tuned to this frequency. I believe they are bent/use 2 to try and get round directional affects. The space around them in a model is likely affect their performance. Compare them to things that have stuck out of mobile phones. These aren't direction, don't cost much and are likely to offer better performance in a number of respects. They would need designing for 2.4ghz though. These days nothing sticks out at all. Hence my comments about cheap and nasty. Many models for instance could have lighter versions of the transmitter aerials fitted externally - even these look like 1/2 wave wire in plastic - more cheap etc. Ofcom's comments about 2.4ghz are that equipment must be able to cope with interference from IMS (Industrial, Medical and Scientific use). It's a relatively open band that can have some relatively powerful signals on it that need not be point to point as some one mentioned earlier. I've seen 2w video/audio transmitters on offer for instance, stick aerial which will tend to radiates equally in all directions unless some one stands in the way or is rather near it. I posted a link that mentioned 500w amateur transmissions. Have one of those nearby and it's likely to totally overload a model's receiver just as hospital etc transmitter some times break through on car radio's tuned to an entirely different frequency. All interesting in a way but personally apart from a micro helicopter complete with a 4channel 2.4ghz transmitter gyro etc for £50 I intend staying away from it for a while. The same things could have been done for 27mhz there is nothing magical about 2.4ghz other than the parts needed are very much in use all over the place and as a consequence rather cheap. Personally I hope that 2.4ghz goes the same way as 27mhz. It was moved because other sources caused problems. All it will take is a few of the right kind of accidents and I don't mean smashed up planes either. John
-
I'm away for a week so can't get at a pc so often. Interesting reading the more recent posts but a few points. If you look at the ofcom web site you will see certain comments about the 2.4ghz band and their attitude to it. You will also find an number of other bands allocated to model control. Could be that one day one of these may be offered with the same degree of protection that the 35mhz band enjoys but who knows this may involve buying a licence these days. Aerials. Think back about the evolution of mobile phones. Model control in this respect has always been ultra cheap and nasty. All bands just use wire at the receiver end. Some may have spent time pointing their TV aerial in the correct direction and noticed how different it performs when they are near it. Stick bits of bent wire in a model and proximity effects are beyond the control of any manufacturer. Pick Spektrum or Futaba etc? If one brand is more prevalent in the field than the other which I believe it is - very much so in this case - comparisons are pointless. Spektrum caught the others napping and there are far more of them about so if problems do exist they are more likely to experience them. Cost is another interesting aspect as is the opportunity to have all people world wide using the same band. In my view 2.4ghz gear should be cheaper than 35mhz. John Edited By Ajohnw on 04/08/2010 11:32:48
-
I just looked at the manual for a walkera helicopter that comes with a 2.4ghz transmitter. It notes that the transmitter and receiver take 10 secs to lock and asks multiple users not to lock their set ups at the same time. It would be interesting to know what recommendation the other makes state. John
-
2 msec is 500 times a second and it's not possible to guess how long a transmission lasts without hard information. They might update all channels in one go but as typical servo's move through 60 degrees in 90msec there wouldn't be a lot of point. No doubt some servo's may be quicker but human aspects come into it as well. As to detection using simple numbers to pick up a signal that occurs every 2msec a channel needs monitoring for 2mses as all transmitters will not transmit at exactly the same time. That's an ideal situation in the real world where environmental effects might prevent detection one might look for a signal for say 10msec or even a lot longer. So if scanning 80 channels that would take 800msec. Big problem though. By the time all channels have been scanned some one might have started using one that was clear or some one else might have also marked it as clear and be about to use it.. Say the data transmissions are 100usec long to detect those the microcontroller that's probably doing the job would have to look and see at interval sligtly shorter than 1/2 of that or more than 20,000 times a second. There are several other approaches to this that can do the same sort of thing but all have cost aspects and then there are things called asic's/ Application Specific Integrated Circuits. Also microcontrollers that are tailored to do a specific job much used in the automotive industry. No point working out what this means as above because we have no idea how long the data takes to send or if it differs between manufacturers. Again it will take longer than some might think. Detection is really easy flytilbroke isn't it. Ok so the transmitter and receiver have found maybe found their channels what's next? Can't spend ages looking for activity on the channel as transmissions have to be sent every 2msec and little can be done anyway as the model might be in the air. Might be nice if the receiver light a beacon if it thought that it was getting too much garbage but this might not be good for sales. Hopping is interesting but it's rather difficult to generate true random numbers. Most methods generate the same sequence of numbers over and over again but there are ways of improving them a little by using methods that increase the chances of the numbers used by each transmitter being different. The length of the sequence is a measure of it's quality. Mixing hopping with fixed has some interesting implications as to which one stomps on the other most often.. Lastly the 2msec interval. This is likely to be rather precise as it's in radio equipment but this introduces another problem. No 2 transmitters are likely to be exactly the same so the signals slowly drift across each other. The lower the difference the slower the drift and once they collide the longer they will take to drift clear. All sounds like futaba and jr might win out but it could also be dependant on how many of one particular transmitters are in use. There's lots of scope for problems and it all comes down to probability in the end and just how many times and how often the aircraft has to be updated to work in an acceptable manner. Then there are the increasing numbers of other makes - who knows what they do. John PS Maybe amateur radio people us 2.4gig for moon bounce communication. Best not fly when there is a full moon.
-
Hi John. That just goes to show the dangers of believing every thing on the web. From one site I had gathered that spectrum use 2 channels and do not hop. Futaba hop but I suspect they still have to look for a clear channel, see the pdf link below. Time can be used to get round the point you mention about bi directional transmission. The receiver can expect a signal at some particular time and if it doesn't get it or gets something that looks like it's not for it or even corrupt move on to the next frequency. There are all sorts of variations on this. Few links that might be of interest http://www.bmfamid.co.uk/forum/index.php?topic=20.45;wap2 The IMS use of the band is entirely correct. eg but there are many uses http://en.wikipedia.org/wiki/IEEE_802.11 And finaly on the seek unused channel and locking etchttp://www.google.co.uk/url?sa=t&source=web&cd=3&ved=0CBwQFjAC&url=http%3A%2F%2Fwww.mpba.org.uk%2FPDF%2520Files%2FUKRCC.pdf&ei=KSBTTPjOFYKQjAfHjuDCBA&usg=AFQjCNGxtwHPo-lfredYRnxDgyv0cUgPxA I took that as a ce requirement. On only transmitting 10% of the time could be that they are always transmitting a carrier and only sending actual data 10% of the time. Locking on 2 empty channels permanently would be a bit of an issue if not.. The spread spectrum system I worked on effectively worked like that. The carrier was always there and the data was sent periodically in the form of so called chirps. The data can contain various things to allow it's integrity to be checked or even reconstructed if some is missing or corrupt. If anyone knows of any hard information on the technical machinations of these systems on the web that isn't advertising etc I would be very interested. John
-
The 2 channels are established and there after shouldn't be interfered with by other legitimate transmitters even the hopping ones as they should detect the channel is in use. Hop and it has the flaw I mentioned more so with increasing numbers of transmitters in use. Throw in noise and what ever and it's rather hard to make a judgement as to which is better but I would still be inclined to favour all using fixed channels. On down linking from memory the official frequency for that is something around 500mhz at 10mw. I wouldn't have thought that would be a problem given sensible 2.4ghz receivers. 4.8ghz transmissions may be but microwave does have the advantage that such signals are well away from the wanted signal so can easily be filtered out. I think the US made a sensible decision on adopting 70 odd mhz on that basis and also propagation but have no definite information on that. I suppose 2.4ghz and the current apparent free house and complete lack of compatibility between systems worries me especially the 2.4 part. Having had some limited involvement with spread spectrum communications I am also rather curious as to what form it takes in the model area. It can be a rather nebulous term. Off topic but some (long) time ago I had a vision of model fliers towing a flight simulator hooked up to there model behind their cars when they went flying. Video linked drones are already in use. A simulator is only a step away but a lot more expensive. I wonder where it all will go next? John
-
I'm not knocking the merits of any system but it should be appreciated that the frequency hopping technique does have one flaw. Each time it hops the system must detect an unused channel. Fine but another transmitter is very likely to be doing the same thing at the same time. There is always a time lag between systems that detect and then act so it's possible for 2 transmitters to start using the same channel at the same time. The rational for not being too concerned about this aspect is that it will not happen too frequently and the loss of 2msec worth of data doesn't matter. Arguing that this approach avoids interference is a bit bizarre and seems more appropriately related to other 2.4g rc transmitter generated interference while they are controlling other nearby models. One thing is for certain these clashes will occur and will be more frequent as the number of transmitters go up. By trade I am an automotive design engineer and have spent rather a lot of time working on comms some of which have exactly the same problem. On this basis the 2 channel approach is more reliable leaving nothing to chance other than local conditions causing an apparently clear channel and of course signal drop out. which is why they have presumably opted for 2 channels. My view really is that the whole comms link for model aircraft control should be the subject of an international standard. There are several used in other fields already. In this case the physical layer is a 2.4ghz signal. Some use wire, others use light some use rf at various frequencies. In many cases the problems are very similar and standards set out the steps needed to negate their effect to an acceptable level. The alternative is relying on some software engineer some where figuring it out for themselves. That's not a good idea when safety is of concern. John
-
Nosing about on the web 2.4ghz offers 80 channels. Some set ups use 2 channels so that can result in 40 really being available. When powering up the transmitter must scan the channels and detect one or in some cases 2 that are not in use. This is part of what the ce sticker is about.. It would also seem that some set ups switch channels every few milliseconds. This is or will probably be eventually an attempt to gain more effective channels as a 2msec loss of control is regarded as un important - Futaba who use 2 aerials. It seems Spektrum use 2 receivers and 2 channels. 2.4gig is also used for data links in local area networks. It seems these may be from one building to another. There are other uses of the band too. As there is no information I could find on rc channels spacing etc it's difficult to know if these could interfere and even then much would depend on the quality of the receivers. That goes back to an earlier point some one made where a strong near by signal prevents the reception of the wanted signal. Some car radio's suffer from this on FM when they go past certain transmitters eg maybe an ambulance services etc. I would hope that the CE sticker takes reasonable care of these sorts of problems but it will probably be with a commercial bent. No good laying down specifications that price equipment off the market. I use the word seems often as it's not wise to accept info on the web as gospel but the same sort of information is available in a number of places. 2.4gig is really in the microwave realm, That's an odd sort of place. I would be inclined to keep the transmitter aerial vertical and hope. All of the above and more is why I have asked if anyone has a sanwa 8 channel 35mhz set up for sale. I need more channels and don't feel inclined to go 2.4gig yet. John
-
Has anyone who has had or seen problems with craft fitted with the receivers that use 2 units and 2 V shaped aerials installed as per the instructions? A subject I'm deeply interested in. John
-
Doh I had already checked the gyro that way so motors must be connected correctly. Forgot that thanks for pointing it out.. On the mixer gain I tried adjusting it to see if it would help get the tail rotor up and running correctly before the main rotor starts spinning, It doesn't seem to have any effect on that only the speed of the tail rotor when the main is running. To be expected I suppose as some fraction of zero is still zero but there might have been some interaction in the circuitry. I'm using the supplied transmitter. The blades are off at the moment to tidy up an small epoxy repair to the end of one of the main blades and then rebalance them correctly. I'm also berating the ebay seller on the fact that one of the blades was reversed plus the other oddities. I'm left in an unhappy situation. With 3d on etc there is negative pitch, this suggests the pitch needs increasing. At full throttle the motor can't cope suggesting too much pitch - that could be down to lack of airflow generated by lift as I am holding the heli in my hand. (Blades above my head or at least not at eye level) Being a glutton for punishment I'm picking up an esky cp belt tomorrow with pitch guage and one or too other bits and pieces which should help check the the cp2 out further. The cp2 turns out to be a cp2.1 by the way. Following that check I'm going to give it a go again and see what happens. If it's stupid it's going back to the seller. The esky is very reasonably priced but lacks a battery. I consider it a decent purchase as the major components would cost far more than I am paying for it and I intend going in the larger direction at some point anyway. Probably more sensible than trying to electrify the MFA even though I'm sorely tempted. All part of a long term curiosity about model helicopters. 2 things I've noticed that might be worth passing on. The main engine shaft is one piece with the gear that drives it on my cp2. Not good, fair bit of dismantling to replace also more expensive. Could be that gold parts fit. These seem to have a separate shaft and gear. When balancing the blades I used a wicks spirit level packed up to be level as a reference. Easy to check if the level is ok. Place on some surface, note bubble position which may not be central, swinging the level round through 180 degrees should give an equal and opposite displacement of the bubble if the surface it's on isn't level. I always try that in the shop before I buy. On the micro twister I'm inclined to think that it would make a very good sensible 1st time step into helicopters even though a controlled yaw left or right of a few degrees is rather challenging to say the least. It also uses infa read for control but that isn't too much of a problem really especially in doors. I fly mine round the bedroom for a few mins before I get up each morning. Excellent practice. It sometimes takes rather a long time for the throttle to start working so watch out for that. John
-
Being fair to your 1st link David I think he assumes that the heli is already trimmed out at least on the ground. The pages do provide some useful clues though eg balancing the blades out to individually before balancing the usual way or at least checking them. The suggestion of turning the gyro gain down while setting up the mixer on the wiki is interesting too. The gyro setting of a little before the tail wags is the same as the instructions that come with other esky heli's I have seen. There's none of this sort of information with the twister cp. I've seen many comments that the on the box statement "has been test flown" is entirely incorrect. Not so sure. I think the problems in that direction may be that if a person sits on the end of a production line all day testing heli's they will soon manage to fly anything. A statement like trimmed out to hover with all trims central would be much better - in our dreams. On swash plate settings in the two modes I'm really trying to find a method of checking that pitch is where it aught to be. The fact that the swash mechanism is central with the trimmer also set central with 3d on concerns me. The heli wont always power up like that as it detects main rotor power. Set the trim right down it powers up ok but pitch goes negative when the 3d switch is used. I just checked if the pitch can be set to zero with the throttle trimmer but it's still slightly negative with the trim right up. I did have the throttle stick central when I tried this. Slight mod needed to this paragraph - since I stoned out the rough edges on the hole in the engine shaft the swash remains central in both modes providing the throttle trimmer's central as well. It must have been sticking due to being forced on. I'm beginning to wonder if the tail and main rotor motors are plugged the wrong way round. Trouble is though that swapping them may overload the tail drive and let the smoke out. (All electronics work due to smoke as they stop working when it comes out.) This and a miss set static pitch might explain the trim settings needed to get it to work as per the book. The mixer gain doesn't seem to affect this aspect. John
-
My 1st reaction to the link is to laugh but I need to start at page 1 and go on from there before I really laugh or maybe change my mind. I certainly haven't noticed the effect you mention - once my heli was correctly set up On spinning up the tail rotor 1st that is as per the instructions that come with a twister cp2. It makes a lot of sense too as the tail is driven by a separate motor which will take time to spin up. The MFA uses a geared drive off the main rotor and variable pitch on the tail rotor for control. On friction with the ground again as per instructions on the cp2 twister and others I will set up for stability with a sufficient amount of lift to very very nearly lift the helicopter off the ground. This is a gradual process. As soon as the heli starts to turn trim it out and allow the setting to settle. Then apply a little more lift trim out again and so on watching to see that it's lifting evenly all the time and trimming that out with the cyclic trimmers. A training stand is a great help with that aspect. This helicopter flipped instantaneously some way before this stage. I didn't have a stand at the time and had no intention of getting anywhere near lift off. It looked ok and a tiny bit more lift and bang. Next comes the actual lift off and here there is a definite problem of varying degree with all helicopters. As soon as the helicopter starts to lift the air flow increase through the blades and this generates more lift which in turn generates even more air flow and so on. You could say that the blades are stalled/working inefficiently until the helicopter starts to lift. Much the same as the static thrust on a normal aeroplane propeller. It is likely to be entirely different to the thrust generated when it's actually flying. Once the heli is stable with hardly any load left on the ground the next thing is what happens when it lifts. This is where the mixer should come in. Obviously changing this will alter the earlier trim settings as well. The 2 setting inter react but it doesn't take all that long to sort out.. Once set up it wont always behave entirely perfectly but should be close. As to gyro's it's very easy to see just how effective they are. Disconnect the main motor, fire it all up, put some throttle on if there is a tail rotor motor and then swing the helicopter about it's vertical axis at various speed. Varying jerks would be a better description in some ways. You will see the effects with a variable pitch tail rotor and hear/see the effects if it uses a separate tail motor. You should also see something happening with a twin rotor craft. The Cp2 settings out of the box are interesting. The part that moves for cp is central with the throttle trim set central as well but it's a good way of centre with the throttle trim where it needs to be. Personally I don't think it pays to take information on the web as gospel. It often isn't. Those links I posted need some thought. The comment on the motor managing to reach full speed is a very interesting one though, My cp2 wont. Full throttle actually causes the low volts warning to come on and the speed to drop. This could well be down to too much pitch. To much of that and the blades will act like paddles. The effect is so sudden I am fairly sure they are behaving just like that but this could be down to the fact that the heli isn't lifting. Likewise on the links should the pitch be zero with throttle in the middle and the 3d switch on? Makes sense in some ways but clearly negative pitch wouldn't be a good idea. A sudden drop in pitch might not be such a good idea either. I'm inclined to think the pitch shouldn't change at all if throttle in the middle and the switch is used. Only way to find out is to try it. John
-
Few points on some of the comments. The cp2 twister does have the mixing control on the 4 in 1 as per usual. With the trim central on mine the main rotor motor can be heard ticking - just on the point of turning and the mixing control doesn't seem to have any affect. I have found that the trim needs to be moved up towards the central position to get the tail rotor spinning as it should before the main rotor starts up. Using right cyclic on lift of due to gyroscopic effects of tail rotor? I've not experienced anything of concern due to that. This tip occurred short of the point where the heli would lift off anyway. My MFA was more likely to be in need of minuscule amounts of left or right tail rotor not cyclic. That one was made when companies did try and make sure that the things they sold worked. On the twister cp I'm getting the impression that it's a case of getting the mechanics right first and then adjusting the mixer on the basis of what happens at lift off. As per normal really. Problem though the throttle trim may interfere too from what I have seen so far offering a sort of mixer come trim on the fly so as too speak. John
-
Yes it's the main blade and of course the end took a small chip and I suspect the engine shaft which in this case includes the gear has a very slight bend in it, Fortunately it really is very very slight. Going from the videos the pitch is too high but that's assuming there should be near zero pitch when the 3d switch is used. I would say there is about 5 degrees at the moment. Any one any thoughts? I've had the head off and the blades were 1 loop of tape light on the undamaged end. It spins up more smoothly now but does shake about at one rev setting. On the pitch the it struggles a at full throttle again suggesting there is too much pitch according to the video's. Any thoughts the suggestion that it should reach max revs at full throttle and not struggle seems sensible to me. One blade lifts slightly more than the other too but as the revs increase lower one more or less matches it but bends more. There's a difference at the lift of speed. The tips match at a throttle level for the brave. Maybe we need to match them against bending loads too. The head was difficult to get off and rather hard to get back on too. Reason the hole in the engine shaft for the retaining pin. Rough edge. I fired up the engine and smoothed it very lightly with a very fine slip stone. Much easier now and it hasn't altered the fit.. John
-
Well a gallon of welsh cawl is in the slow cooker and I've started checking it over. 30 sec and I notice one of the blades is the wrong way round ! Now why didn't I notice that when I skidded it along the floor. John
-
I'm still living in hope of some one coming up with a copy of the instructions. On the other point I've ticked remember me and so far I log in automatically. John