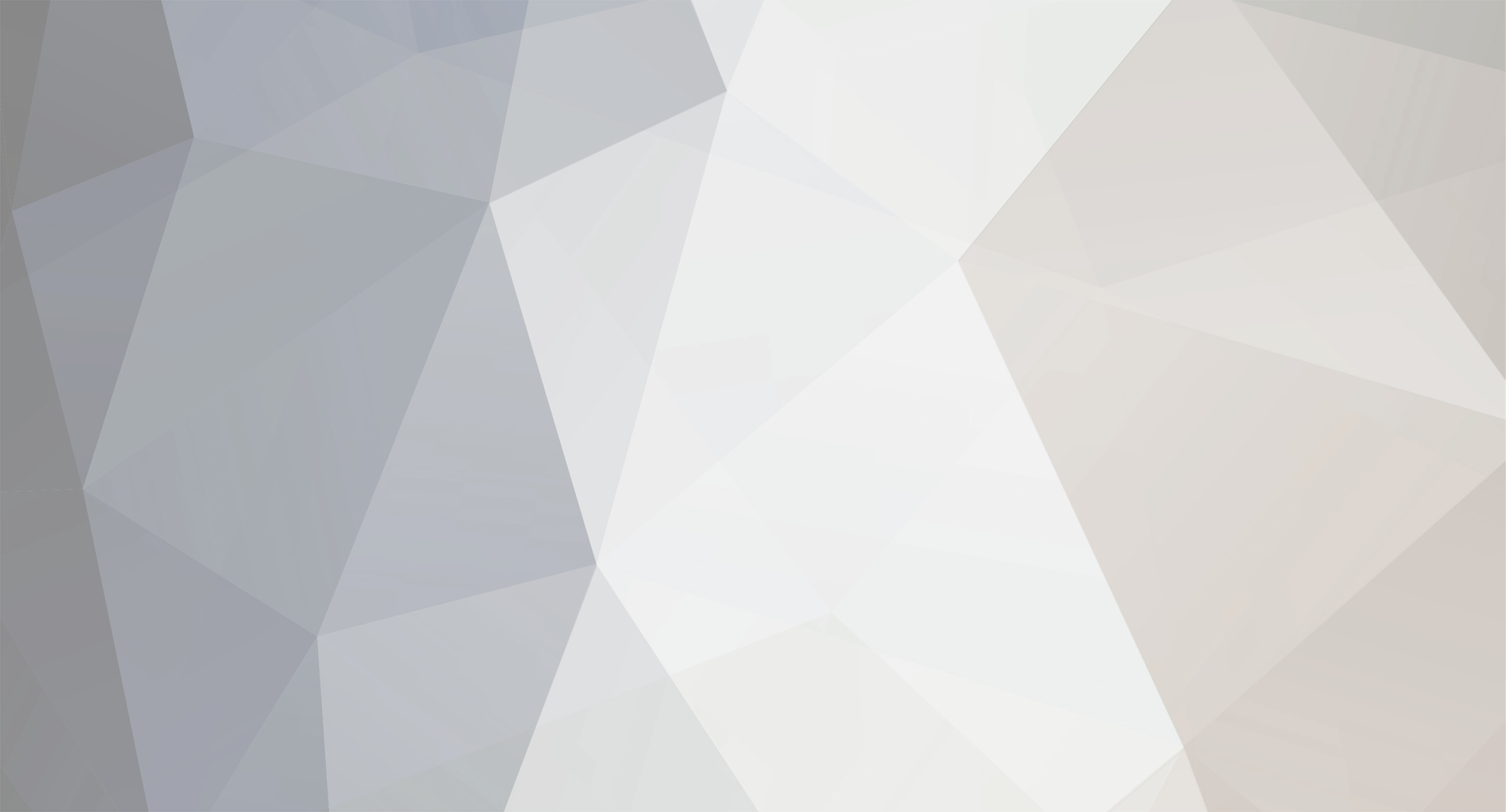
Garry Hallam
Members-
Posts
62 -
Joined
-
Last visited
Never
Content Type
Profiles
Forums
Blogs
Gallery
Calendar
Downloads
Everything posted by Garry Hallam
-
Take the Balsa covers and drill the holes longitudinally straight through the sections, I made mine oversize and dimensioned them around the holes accordingly after drilling. Glue them in place with epoxy but remembering to make a left and right hand version in relation to the profiles which are them sanded to shape. Note that on the top section, the Balsa cover will be covering the slot and drill hole for now. Now wrap the tin plate around the upper section of the leg and Solder along the overlapped seam. Ensure that the bottom leg section fits into the free space with room around it, and then glue in place. Apply the Paper wraps and then remove this and the Balsa from the top section where the Slot is. Note that this only needs to be on the inside where the upper hinge fits, again making them left and right handed. Take the 2mm drill bit and extend the holes through the Paper and Balsa for the pin. Make the Hinges as per Drawing by simply sawing out and filing, followed by drilling the Holes. Fit the lower hinge by tapping in the 2mm pin and mushrooming it either side to secure. Temporarily fit the top hinge and where the attachment screw fits, ensure that it can be accessed with a screwdriver, you may have to file away the top outside of the leg with a round file to enable this. Also note that at this stage you may wish to make the Oleo cover and drill a hole in the end to allow access to the appropriate length fixing screw to allow removal for servicing. Take the springs and make a dry run of assembly ensuring that everything moves freely. Finally stripping back down and Painting. On the final assembly apply some Vaseline to the spring and shaft for lubrication. The top hinge can be secured with a suitably sized straight pin to allow free movement as it will be kept in place by the Oleo cover. I have posted Photos. For one reason or another the Photo’s have to have their own thread, sorry for this. Any questions please feel free to contact me here or at [email protected] Garry
-
I have developed a sprung Oleo leg for the Pioneer that others may wish to use. The only drawback to this is that the leg at the top attachment Point protrudes from the Fuselage more than a fixed one would do, and consequently the Oleo covers will need to be made deeper. Also it will be worth stiffening the attachment point from behind. Below is a list of Materials and Tools required. The Alluminium Tubing & 6mm Solid Alluminiun Round Bar are available at B&Q in 1 metre lengths, as is the 10mm Square Bar and cost around 2.50 each. Materials 1. 10mm Outside Diameter x 1mm wall Alluminium Tubing 2. 8mm Outside Diameter x 1mm wall Alluminium Tubing 3. 6mm Outside Diameter Solid Alluminium Bar 4. 10mm x 10mm Solid Square Alluminium Bar 5. 2mm soft wire ( Pushrod off cut) 6. 50mm Long springs to Fit. (I found these in my Junk Box, but should be available fairly easily online) NB. Ensure they will take the Initial Weight of the Pioneer without too much compression. Each of my springs topped out at 5kg on the weighing scales when fully compressed. Tools Hacksaw Files, inc Needle files for finishing the slots 2mm Drill bit 2.5mm Drill Bit 2.9mm Drill Bit (Tapping Drill) M3.5mm Tap 8mm Drill Bit 10mm Drill Bit Pillar Drill for Sanding / Polishing the Tubes to the correct diameter Various grades of Emery Cloth / Alluminium Oxide for Polishing Tubes down I originally made my drawings to Scale in Microsoft Word but the Photo images here are not. Anybody wanting the originals can email for a copy. Also be aware that the lower leg Balsa cover has a dimension error; the 9mm Dimension should be 8mm. Also the stated 2.5mm hole in the Top hinge should be 2mm. After cutting the tubes to length the first step is to insert the 6mm long x 8mm Diameter tube spring stop inside the top section (This should require minimum sanding to allow a tight tap fit) then Pin it by carefully drilling through the outer tube just enough to enter the stop. Then Tap the 2mm wire in to hold the stop in place, it should be a tight fit, and then file flush on the outside. Now is the time to sand the 6mm OD bar down to 5.5mm, making a good loose fit in the 8mm Tube. Remember to leave the 10mm long section unsanded. Finally sanding this down as well but to a good tap fit in the lower leg section. We will now secure it into the 8mm tube bottom section with another 2mm pin, although the 2mm Drill hole can go straight through followed by a slight countersink either side to make a rivet type affair. Again file flush to the Outside. Drill the 2.9mm Hole in the end of the now 5.5mm bar & Tap m3.5, taking care to get it centralized. We can now cut and file out the slots in the top & bottom of the upper and lower sections, finally drill the 2mm hinge pin holes again taking care that they are centralized through the cross section. Due to size restrictions this is continued in the next Thread
-
Thanks David, and for having the Plan in the Mag. I would hope that Chris Read gets a heap of well deserved recognition for his Design. As Jim states he has certainly made a terrific contribution to RC in designing this model. I owe a great deal to Peter, the owner of this thread he has helped me in many ways on and off this forum. Thanks especially for the Decals, you made a fantastic Job. Hope to see your finished Pioneer on here soon Peter. Regarding the Slat screw up. think that I will try them in the Position that they are for now and see how it goes. Regards Garry
-
Guys I screwed up when fitting the wing slats, but have only attached one so far. The Slat, as I understand it, is tapered downward to allow a lesser angle of attack than the wing leading edge at takeoff. however when mine was fitted, it is at a more or less similar angle to the LE. Please see the clickable photo link. This seems to have given a slotted type wing instead, and I am now wondering wether or not to attempt repositioning it. Problem is that it may cause damage in doing so. Now I am wondering if I should just install the other the same way and see what happens! Anybody have any Ideas on how the flying characteristics will be affected.
-
I kinda see what you mean, although I sometimes pay for the convenience of the Model shop, I also prefer to buy screws and the like by the box. I generally go to the Local Engineers supply shop. Great for drill bits also as they have a large range and the quality is much better than most you will find. Look in the directory under Engineering supplies, i'm sure they would be happy to supply you with what you need. They also have some of the more elusive items such as Grub Screws. In fact I went just the other day for a dozen 3mm grub screws which he gave to me for free. In fact for small quantitys they often do this, I sometimes hand him a pound or two to put in the Tea kitty, that way you know they look after you and not seen to be taking advantage of their good nature. regards Garry
-
Thanks Steve I will get them Sorted out garry
-
Hello Fellow Pioneer Builders. My Aircraft is almost ready now and I am now looking for a Pilot for the Cockpit. The one chris Read used looks perfect but I am unable to find anything like it. All the ones I have seen are the Typical Bust types. I did see Captain Jack Harkness an action Figure From Doctor Who thats looks perfect for size and may be suitable with some modification? Any body have any other Idea's. garry
-
Roof attached
-
Having been Influenced by Jims Modification to the wing mounting I decided to adopt a similar method. The wings are attached with 5mm Cap head screws which are accessable through the removeable roof that is held with small magnets. A picture says a thousand words, so here's the detail with one wing attached and the renaining one shows the Bolt screwed in. I may change the screws to alluminium ones later.
-
Can anybody shed light on which way around the Taper of the Flap goes? The Drawing shows it at the Slot side, but does it go towards the Tail end as one would think?
-
Chris Please could you send the Glazing photo's on to myself also. Garry [email protected] thank you
-
-
-
Having got to the stage of installing the tail end I decided to make a modification of the Rudder/Steering Horn. It seemed a little tricky to install the Pushrod Z bend so consequently the Cam shaped horn now can be attached after fitting it all together. I am guessing that chris glued it to the 5mm dowel but I wasn't keen on this permanent installation just in case any adjustments needed to be made. The bottom end of the dowel having been sized in my spinning drill is glued into a externally threaded sleeve and the horn fits onto this and secured with a nut. This I think, makes installation somewhat eaisier. The Bush and nut were modified from a Panel Mounted Electronic Potentiometer. I have included photo's to show the detail
-
Quote Hi Jim, I think I get your point! Remember that song: Like sister and Brother? - BARRY TAYLOR Whats this Barry? Care to Explain!
-
Peter Hows your Pioneer going now. Did you sort out the Hatch? I planked my lower rear fuz fully and then cut out the hatch from that and added end plates and sheeted the top after dimensioning to allow for the added thickness. Looks like the assembly for steering and rudder should be fairly straightforward, but I havent done that part yet. I am now just finishing covering the tail end set now. The Slots may be a bit tricky as I also found with the three 0.3mm strips on the stabiliser. The covering I have used on everything except the nose top has been Solarfilm as I did'nt realise it was different from Solarspan! It went on OK, except that I found the iron leaves the Colour looking patchy. Was thinking that I might wire wool it all over, then fit the Decals followed by sparaying with Laquer all over. Garry
-
Peter It just occured to me that the Acrylic Paint I was refering to was from a bottle of Tamiya Paint from the Model Shop. I have Covered the Fusalage now, except for the Cabin. The Front upper Black Section was covered in Black Litespan and then Sprayed with the Automotive spray can I used on the Cowl. It seems OK so far but time will tell. I also opted to cover the back upper Fusalage in Silver, as I wasn't keen on it being white. I originally thought it was silver when looking at the Magazine article. I then realised it was white after seeing the photo of your Fuz, but I had my heart set on it being silver so I went ahead. Not sure now whether or not to just Paint the Cabin Detail in white, as there is not Much to really cover. garry
-
Peter What Paint will you use on the Litespan? I Intend using it. I once tried it on a Electric model and found that it crinkled up when in the Sum. The Paint I used was acrylic! garry
-
Pionner People I Have been thinking about building a smaller Pioneer, one that I could chance flying, and utilizing a .15 Engine I have. Any thoughts on how much to reduce the scale of the original plan? Any help appreciated garry
-
Hi Peter Thanks for the reply! I bet your fuzz will look great once you have finished sanding & filling, plus you will have a very tough finish. Bet you'll be glad in the long run! As a beginner at this, Glassing was definately not for me! I Think the Solarspan will definately be better for weight saving as you say, but... in my case, as I am unable to fly very well anyway, I am Really not planning on flying this Model, The thought of picking the peices up afterwards would probably have me in tears. Also I have been advised that Solarspan can look very toy-like compared to Tex. Good luck with your sanding....Phew regards Garry
-
-
Just an update of where I'm at with my Pioneer. Except for adding the Rib detail on the Rudder & Elevator, owing to the Mistake I made, I am now ready to start covering. I really wanted to glass the Fusalage & Wings but I don't have the confidence to do it. Instead, I'm thinking about using Natural Solartex followed by Spray Paint. Any Pro's & Con's of doing it this way? apart from having to fill the weave. Should I use Balsaloc? despite the covering being self adhesive with the heat applied. Here a couple of Photo's with Most of the Parts assembled.
-
We must always be carefull where we put the Decimal point. As an ex Engineer I have seen it done many times! Incidentally, Converting Imperial sizes to metric is as follows: For Example lets take a 1/16" Drill Bit: 1 divided by Sixteen =0.0625". Then to convert it to Metric size we Multiply it by 25.4 (This is how many Millimeters there are in 1 Inch) 0.0625 Multiplied by 25.4 = 1.5875 Rounded down we find it is 1.58mm. Just thought this may help. Garry
-
Hope the Photo of My Rudder did not throw you JJ. I used the Sandwich method reversed with 3/32" inside and 1/16" balsa each side for a thickness of 7/32". I will be putting the pattern in with 1/64" sheet each side and cut out accordingly. I cannot see there being too much of a weight Penalty. (Sorry Chris, but I don't always follow the Rules) good luck with your build JJ. regards garry
-
I think you are talking of 0.1 Increments & not 0.01? Even at 0.1 thats a lot of drills! I generally go for 0.5mm increments metric and then have Imperial sizes for in-between sizes which generally do for most jobs. 1/16 = 1.59mm 1/8 = 3.17mm etc