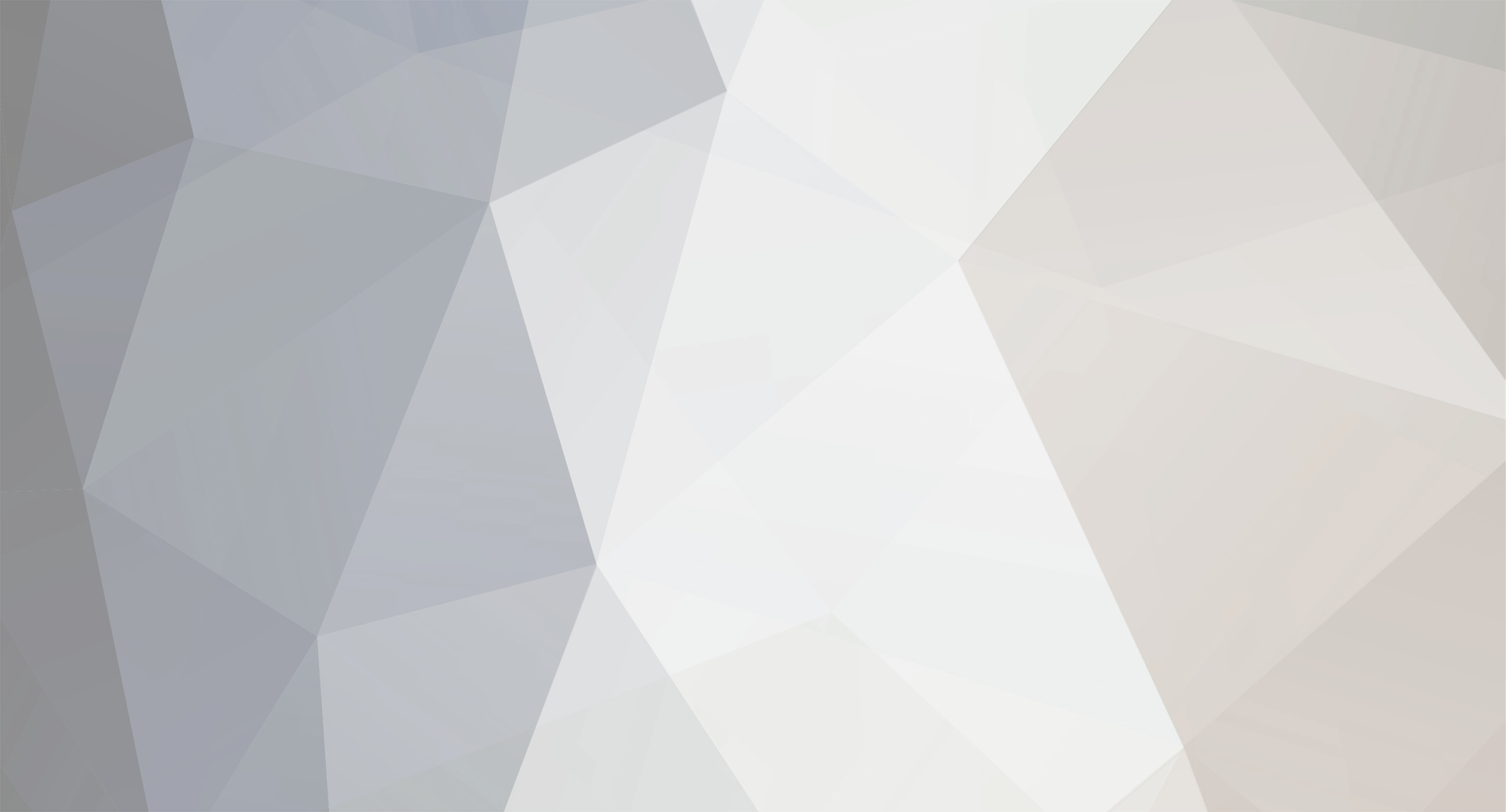
Monz
Members-
Posts
581 -
Joined
-
Last visited
Never
Content Type
Profiles
Forums
Blogs
Gallery
Calendar
Downloads
Everything posted by Monz
-
Posted by Erfolg on 13/12/2019 18:39:11: I am getting the impression that Monz is creating his Decals from scratch. That is coating onto a surface such as a gummed paper with WBV. Then printing or hand painting onto this substrate. Finally over spraying the art work. Such work is beyond both my abilities and patience. I just buy in Decal paper onto which I print. My over spraying the art work is to both protect it and to increase the total thickness. My methods are about deskilling the process. Which I have to do. Not sure how you come to that conclusion? All I do is buy in laser decal paper onto which I print....
-
Decals need a good gloss coat to adhere properly so on foam models a coat or two of gloss WBV will give a nice surface to work on. Once the decals are on then another coat of gloss varnish will seal them in and also get rid of the 'silvering' (edges of the decal). Then a coat of semi or matt varnish for whatever finish you're going for. A couple coats of thinned varnish on large models adds hardly any noticeable weight. Here are the decals I made for my two Impalas, one 1/4 and the other 1/10 - Both sealed after with a gloss and the edges of the decal disappear completely. Again, the white is hand painted over a grey text decal.
-
Posted by Harrier Mate on 12/12/2019 21:40:46: Monz, amazing scheme. And so much cheaper than Arizona Models fabric (about £150 for just the wings). Could you tell me more about that technique. You have clearly covered the model in a base layer first.... plain tissue or fabric? And then applied the printed lozenge to tissue??? The model is covered in jap tissue with a coat of dope to seal it. I built a test frame to see how the decal would react to it. On the test frame I had different sections with different treatments - non shrinking dope, banana oil, shrinking dope, matt, semi gloss and gloss varnish. In the end it was three coats of very thinned Tamiya gloss varnish over one coat of shrinking dope that worked the best. I drew up the lozenge pattern in Photoshop to match the lozenge on the reference aircraft, along with the other decals like stencils, markings etc and scaled it to match the three view I built from. Where there were white stencils I did a light grey decal and then hand painted over that with white enamel. The white rib tapes are all 2mm wide strips of white decal paper applied individually. That and the hand painted stencils were an exercise in patience! The domestic laser MFP's are a much better investment over any domestic inkjet.
-
Posted by Don Fry on 12/12/2019 20:27:41: How big is that bit of flying art? 1/10th scale, rubber powered.
-
I've used Laser water transfer decal paper run through my HP home laser printer. Everything on my DVII except the pink paint was laser printed decals over the tissue. I drew everything up in Photoshop. I used a combination of clear and white paper. The clear gives some transparency while the white is opaque, though does take some planning as domestic printers don't print white! The advantage of laser printed decals is you don't have to seal them with anything - Print, dunk, apply.
-
Another one almost ready for the Orme. Will get the last of the details done and radio in tomorrow. The thread heading is incorrect, it's actually a 1/10 scale kit, not 1/8.
-
The wings have been joined and glassed, tip tanks glued on and I made some air intakes from 6mm depron laminated together and sanded to shape. Also spent some time sanding the seams on the fus joint down and sanding the stab balsa to shape. There is a pre cut slot in the fus for the stab which once in is square to the fin, but once the fus is on the wing its out of square. Turns out the one wing seat is 2mm less than the other, so a quick bit of balsa filled in and now everything is square. Well, almost, now the canopy base and front fus is out, but I can live with that as they're not really visual. I'd rather have square wings! The stab has been glued in, the elevators next, and then the wing. A shot of it together shows a nice little Imp in the making. Hope to get primer and silver on it during the week.
-
Hi Chris, I remember seeing that on SABC news as a kid. Very sad, especially as he was a friend. I know Dave's son, Andrew, editor of Aeromodeler, also a gentleman that shares his dad's passion. The pics were before I had numbered the Imp, it now wears 517. Being that I'm originally from SA, if I build a model and the SAAF used it then it must have some bokkies on it! The small one I'm busy with will be 460 in 4 Hangar at Ysterplaat.
-
Martyn's F-86 Sabre Build Blog
Monz replied to Martyn K's topic in PSSA Mass Build 2020 - North American F-86 Sabre
Very nice Martyn! -
Next up as a quickie will be this 1/8th scale kit from AB Models. Kit comes with a glass and CF fus, tip tanks, belly pan, canopy and cockpit base. The wings are foam core with Obechi skins, spruce LE and live hinged flaps and ailerons with built in gap seals. How cool are these! I'll be doing the all silver trainer scheme as below.
-
Forgot about this thread on here, so time for an 'update' and almost wrap. This project did languish for a good few years due to work, other modelling interests and just a lack of space in my flat. But with some mojo I found under a pile of balsa I got cracking with it again a few months ago. It was a case of 90% done, 90% to go. I started by glassing the front fus, getting that filled, rubbed down and primed. I used Soudall lightweight filler in a tube which worked really well. Then it was on to painting. I used lots and lots and lots of masking tape for this scheme. I used the yellow Frog tape which worked really well. The only bleed I had was where I hadn't rubbed the edge down properly and this was very minimal. This is good stuff to use if you're spraying. I used B&Q rattle cans for all the painting, the stock colours matched what I wanted pretty spot on and after many hours of masking, spraying, masking, spraying, masking..... this was the end result. Then it was time for decals. I make my own laser printed water transfers. The black, orange and white lettering was hand painted. Between decals I bought some 1mm PETG sheet, built a vac box and made a canopy plug. The canopy is 80cm long by 20cm wide by 15cm high. I initially tried pulling it in one piece but couldn't get enough heat to the edges of the plastic so had to split the plug at the canopy joint and do it in two pieces. This actually worked out better in the end as I now have easier access to the fus for the radio and lighting bits. The canopy frame is made from the same 1mm petg cut to shape and glued to the molding. And after some silver paint I was quite chuffed with the result! The canopy had been bugging me for some time. I couldn't find anyone that was able to do one that size and after some prodding from certain fellow modellers.... A bit of a cockpit mock up tub type thing... ... ready for a pilot and seat to go in. I ordered a print of a pilot and seat from Andy Meade to go in, but with that only being an after thought I couldn't fit him in without some serious surgery. I couldn't bare to cut the prints up so have ordered a a bust and top half of the seat from Andy instead. The original full figures will go into something else These are the full figures. Friggin awesome! The servos have gone in and a few small details added and next will be to get the radio set up. The weight is about 10kg so far as a guesstimate. Soon as the weather improves I'll get it outside for an assembled shot.