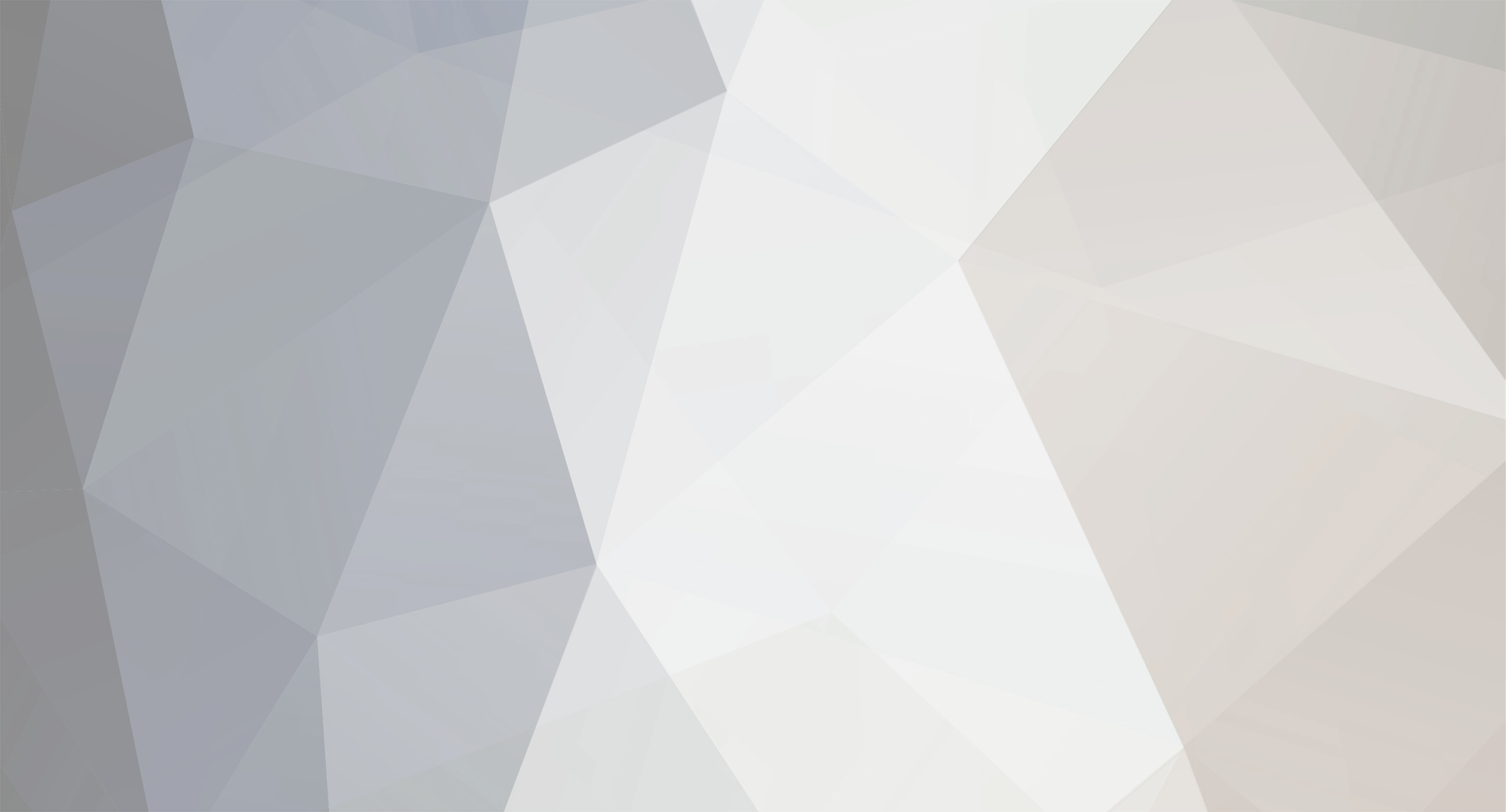
"L"Plate
Members-
Posts
122 -
Joined
-
Last visited
Never
Content Type
Profiles
Forums
Blogs
Gallery
Calendar
Downloads
Everything posted by "L"Plate
-
Ever wanted to get into or improve your aerobatics?
"L"Plate replied to Peter Jenkins's topic in In The Air
Good on you Geoff, we have all had our ups and downs; I smashed my first Monolog after hitting a bird (I was part way through a roll at the time), it was a horrid sight and I thought about the expense of a new airframe and the time lost sorting things out, but Peter got me going again. Thanks Peter. -
Ever wanted to get into or improve your aerobatics?
"L"Plate replied to Peter Jenkins's topic in In The Air
Hi SR71, I can recommend a look at Bondaero http://www.bondaero.co.uk/ I have had very good service from him, 2 Monolog 110 (crashed the first one after hitting a bird at low level half way through a roll), and I am now building the BiSIde 70. He has a secition for Sport and Practice Airframes and currently has the Axiome 70 (CPLR) model on special offer. You will find alternative motor on 4Max and ESC at Hobby King, fit good quality servos and any of those models will be a winner, capable of taking you up to and including Masters. Peter has a Monolog 70 and it sounds like it performs as well as the 110. You will find that the 70 size model's fuselage are not small and these models do perform very well. -
Ever wanted to get into or improve your aerobatics?
"L"Plate replied to Peter Jenkins's topic in In The Air
On my Monolog 110, which can run any conventional power train: electric, nitro or petrol; I have the wire UC and can say it is a bit soft (and my landings are not that hard normally) but no structural problems. As Peter said, according to the manufacture there are some aerodynamic issues with the G/F legs, especially in knife-edge flight. I didn’t know John had a Monolog -
Ever wanted to get into or improve your aerobatics?
"L"Plate replied to Peter Jenkins's topic in In The Air
Hi Geoff, For a model of you size a 2mm threaded rod cut to length should be fine, if you wanted to go the extra bit to stiffen them up, you can sleeve it with a piece of carbon tube with an internal diameter of 2mm. I have a few model set up like that and it works well. Good suggestion to wick thin cyno around the mounting plates and into locating holes post one of the link explains and it works for UC's as well http://www.rcmodelforum.com/showthread.php/226-Servo-fitting As you may gather I post my builds on that forum, with tips and explanations of what I am doing and why. A tip for your hinges may be worth a look at http://www.rcmodelforum.com/showthread.php/227-Fitting-Cyno-Hinges With F/G UC's that are bolted to the bottom of the fuselage, some pilots fit them with nylon bolt that can shear in the event of a heavy landing saving the fuselage and legs. On your model I would probably start off without the spats and some bigger wheels, if you fly off grass (spats and small wheels on grass at this time of year can be a big problem, even on bigger models). Edited By "L"Plate on 19/01/2015 15:25:21 -
Ever wanted to get into or improve your aerobatics?
"L"Plate replied to Peter Jenkins's topic in In The Air
Geoff, The problem with “Z” bends apart from the fact it has a radius in the bends that can bind or wear the hole, it the fact that to allow the “Z” to be fitted the section that goes through the horn or arm is wider than then needed, this allows the control rod to move up and down causing play; further as the wire is thin and the force is applied to one side, it will flex (unlike a clevis or ball link that transmits the force straight along the rod, a good reason not to put any bends into the rods to get around things), loosing the positive control movement needed (allowing the surface to be blown back and in extreme cases even flutter). To get a “Z” bend through a fibreglass horn the hole has to be enlarged to larger than the wire diameter and this also leads to slop, you can get away with it with nylon horns as they stretch / flex a bit. I think Peter thought I was talking in general about the grommets and made the same mistake I did reference the size of you model, as I said on a model of your size and with ring grommets I would direct fit but larger models with full width or double grommets I would always use them to isolate the servos from vibration. John, That is a hard question to answer, it is down to the quality if the wire, the weight of the model and the standard of the field (and the pilots landings). Some of the wire UC’s I have had in recent times, supplied with kits, are just too soft and bend; in the past I have had some wire so hard that it has broken. The alternative is of cause F/G but again some of these can be brittle or delaminate, I prefer F/G for heavy models off grass. There is an argument (which is valid), that if the UC is too stiff the shock of a less than perfect landing / rough field, will be directly transmitted to the airframe and could cause damage that is unseen or ripping out the lower fuselage (unlike the soft legs absorbing the shock by bending). Sorry for the none answer. -
Ever wanted to get into or improve your aerobatics?
"L"Plate replied to Peter Jenkins's topic in In The Air
Sorry I thought your was the 70. The small spinner system looks like it would work very well. I avoid “Z” bend on all but indoor models, never had a problem with ball links on either helicopter or my fixed wing models (and I do throw them around a fair bit), most of the big boy F3A chaps used ball links as well (as they give less slop than clevises, which are better than “Z” bends after a few hours flying). As your model is a 400 size, there is no problem direct fitting the servos and definitely as your servos have ring grommets. -
Ever wanted to get into or improve your aerobatics?
"L"Plate replied to Peter Jenkins's topic in In The Air
I have the motor mounted in the Monolog 110 on a rear crucifix mount (I think it is the same with the 70), there is a large opening just behind the cowl under the fuselage (I mounted the ESC there), I cut two holes in the front of the cowl. As the majority of flight is at low throttle only using full power for vertical climbs and about ¾ for a large loop, the motor and batteries hardly get warm and the ESC remains cool (my flight times are around 10 so less than 6C average as I normally have 3.8V per cell left). On the 70 it might be worth cutting a hole in the covering at the bottom rear fuselage (last open bay), this will help air flow over the battery, if you still think you need more cooling air then a vented spinner like these **LINK** or cutting the front off a spinner (make sure you balance it afterwards),will let air through (as long as the back plat has hole in it). On the servo front, it depends on a couple of thing: A – Is the servo supported from rocking from side to side? B – Are the grommets full width? If not, then I straight the servo that has single screws at each end, if using grommets make sure you put the ferrules in the right way (post two on the link) **LINK** I would also add this piece of advice, If you want to fly the model a lot and keep precision in your controls, don’t use “Z” bends, use good ball links at both ends of your control rods (Align 600 class helicopter ones are a reasonable price). -
Ever wanted to get into or improve your aerobatics?
"L"Plate replied to Peter Jenkins's topic in In The Air
You can’t use a single servo as the wings slide off, however if a model uses just one both points are to a point true, not so much with the slop part but you are then operating an aileron through a toque rod normally to the inboard end, so can mean the ailerons lose some movement towards the tip. I have landed a petrol model without a problem when one aileron servo died in the air, but that should be unlikely with an electric model, just as a thought not a lot of models (in our size range) use two servos for the elevators (if they fail a single point landing will result). That is a good reason for using servos with a proven reputation (that said it was a Futaba servo that died on my model but then petrols do produce more vibration and it had done a fair number of hours). -
Ever wanted to get into or improve your aerobatics?
"L"Plate replied to Peter Jenkins's topic in In The Air
I have a Monolog 110 and I use separate channels for the ailerons (as I do for most models with a servo for each servo) for a few reasons: You can use subtrim to get the servo centre, if you can’t get the arms fitted at 90deg to control rod. You can programme in aileron differential if needed. If the model has a tendency to tip stall up can set up spoilerons (both ailerons go up by a small amount), or if it doesn’t have a tip stall tendency then flaperons (both aileron going down again a small amount), to allow slower landings if needed. By the way, for the money the Monolog is a very capable model and is more than capable of taking you through a lot of competition flying. Edited By "L"Plate on 16/01/2015 17:55:12 Edited By "L"Plate on 16/01/2015 17:55:47 -
Ever wanted to get into or improve your aerobatics?
"L"Plate replied to Peter Jenkins's topic in In The Air
Played with the square loop and half roll, it started to looked fairly good as long as I used full power on the up line, with just a slight tightening on the normal loop radius to help maintain the speed up, then with part brake set on the ESC the down line was not too far off the same speed as the up. After about five attempts it started to look squares and the speed almost constant, most importantly the rolls seemed the same length and in the middle. With a bit more work it might even get to good. -
Hi Peter, There are a few companys that produce electric retracts, they are easy to retro fit in the main using simular mounting methods but rather than air just need to be conected to the RX by a "Y" lead, they are slower than spring air retracts in operation (but you don't have the problems with air seals like you can get with air systems, either having the retracts come down in flight or not working leaving you to do a belly landing). All the electric retracts I have tried have worked well, even the cheap ones from Hobby K.
-
Ever wanted to get into or improve your aerobatics?
"L"Plate replied to Peter Jenkins's topic in In The Air
I don't know how the spelling mistock got in but I wanted to say how short should the straight lines be? Thanks though for the reminder that they have to be vertical or horizontal or you loose points, not that I will as this is just for me as I am not at that level yet! I will try with a slightly tighter loop radius and see how well I can keep it in the box, while keeping the radius fairly large, I think that would look good and will save scrubbing too much speed off (which would need more power in the up and harder to keep straight especially in the wind). -
Ever wanted to get into or improve your aerobatics?
"L"Plate replied to Peter Jenkins's topic in In The Air
As my loops a fairly big to start with, will that not take them above the top of the box by a fair bit? I have been flying them with a slightly tighter radius to keep it in the box (I get away with it due to the power of the model), and sort of fly it as a hesitation loop. How sort are the sort straight lines? -
Ever wanted to get into or improve your aerobatics?
"L"Plate replied to Peter Jenkins's topic in In The Air
How do you fly the square loop with half rolls up and down? I am not sure how tight the radius is meant to be. -
Ever wanted to get into or improve your aerobatics?
"L"Plate replied to Peter Jenkins's topic in In The Air
Martyn, About seven post above -
Ever wanted to get into or improve your aerobatics?
"L"Plate replied to Peter Jenkins's topic in In The Air
I have nor seen it written but I feel it is good practice, that if you are reversing the direction of a circuit that you call it so others know. Whether this is expected during the test I am not sure but if other pilots are flying at the same time as you this should help avoid the head on crunch, also carry out a visual before changing direction. Edited By "L"Plate on 19/11/2014 14:47:10 -
Not as bad to fly as it sound! Don’t forget that the wing loading and speed of the classic aerobatic models is higher than a modern model and the power to weight ratio was less as well, the models also had less side area. The extra bit helped to keep things in shape and with a modern radio are easy to control, just think of what it was like back then, with sliders and knobs needing twiddling, rather than a computer mix set up we can do now.
-
Ever wanted to get into or improve your aerobatics?
"L"Plate replied to Peter Jenkins's topic in In The Air
Well said Willyuk, too much challenging the good advice Peter is giving. -
Ever wanted to get into or improve your aerobatics?
"L"Plate replied to Peter Jenkins's topic in In The Air
In my day (a long time ago), for the full size you had to fly the line vertical as best you could compensating for the wing, the tip frames gave you a reference but you still tilted slightly into wing until you were close to the turn itself then you made it true vertical. Still the judges saw it the same way as an RC pilot, judge / examiner now. I was told that for extreme verticals it appeared the aircraft was curving away from the viewer, but to my eye it always looked right. I think most of the time that I flop forward or backward with a model on a stall turn is when either I allow it to slow too much without enough throttle to give prop wash or it is not enough and has a CofG too far forward. I think an examiner would have to be very picky to fail a candidate for the vertical for the amount of effect that the perspective would have, this is not precision aerobatics, it is about being in safe and correct control. So the aircraft going up at close to vertical (say between 87 and 93 deg possibly more on a windy day) a proper stall (not a wing over) and then returning down the same line / very close to the same line; to me would show good control, although not perfect (but then I am not an examiner so will bow down to you and Peter). -
Ever wanted to get into or improve your aerobatics?
"L"Plate replied to Peter Jenkins's topic in In The Air
I am interested in this. I have seen in full size an effect in long verticals that make it look as if the aircraft is curving away from the viewers point but not been told or noticed this at model scale. Please explain further Terence. -
Ever wanted to get into or improve your aerobatics?
"L"Plate replied to Peter Jenkins's topic in In The Air
Funny thing, today flew my monolog and timed the roll rate using the tx timer. Doing three in each direction, so get an average roll rate, timer read 16sec so that works out about 2.5sec a roll (I thought it would be about 2sec per roll). Then just for fun I repeated the test twice more with the same result. I don't think I would want to slow it up much more as the model uses a lot of sky going down wind at that rate (but I was doing three rolls), but a slower model that I flew was timed and it was very easy to achieve a 3.25sec per roll, roll rate. I also find that timing the elevator easier with the slower rate and still not need rudder. For the slow roll I do need ruder on both models (timed at between 5&6sec each and needing more throttle on the slow model as the rudder struggles to maintain hight in knif edge without speed but the Monolog can be flown at the same airspeed as the double roll) So I think Peter must be on the money with this one. -
Ever wanted to get into or improve your aerobatics?
"L"Plate replied to Peter Jenkins's topic in In The Air
Hi Peter, I used the same make of prop for the tests. You are right that different makes, do change performance, probably due to changes in aerofoil and flex. I did do a bit of testing using a wind tunnel on a speed model as the prop was over square (more pitch then diameter) and static testing proved nothing, but in a wind tunnel at 200mph proved to have significant thrust. The model needed a bungee launch and took a few seconds for the prop to unload, before the model would accelerate. The model got to a speed of over 220mph before the prop throw a blade at an estimated 47,000rpm and the motor was ripped loose. We think, using data from the telemetry that the model might have got to 250mph, in level flight. I must admit I have been an exponent of diameter over pitch for vertical performance (the added advantage is more prop drag in the down line) and pitch over diameter for speed. With IC I have always stuck to the recommended prop for the engine. -
Ever wanted to get into or improve your aerobatics?
"L"Plate replied to Peter Jenkins's topic in In The Air
Hi Peter, I may be doing things wrong, but I feel that a Watt meter on its own is a good tool but I also use a tacho, as a motor may draw more power but that may not translate to effective air movment. I also know of other who use a spring balance to check trust. I have had motors draw large amounts of power but with a small reduction in pitch have produced a large increase in RPM and duration, giving much better vertical performance. I know of some speed models and EDFs that unload in the air and become far more effective, but I don't think this is the case with F3A as constant speed (so traction) seems more the order of the day. Have I got it all wrong? -
Ever wanted to get into or improve your aerobatics?
"L"Plate replied to Peter Jenkins's topic in In The Air
Depending what you speed is like in level flight and provided you have clearance, I normally go for a bigger diameter, to get the vertical (some times with a little less pitch. Is this wrong thing to do? -
Ever wanted to get into or improve your aerobatics?
"L"Plate replied to Peter Jenkins's topic in In The Air
It might be to do with the fact the model was trimmed upright reducing the effect, as it is supporting the weight but when you go Neg G it adds to the weight. Just a thought.