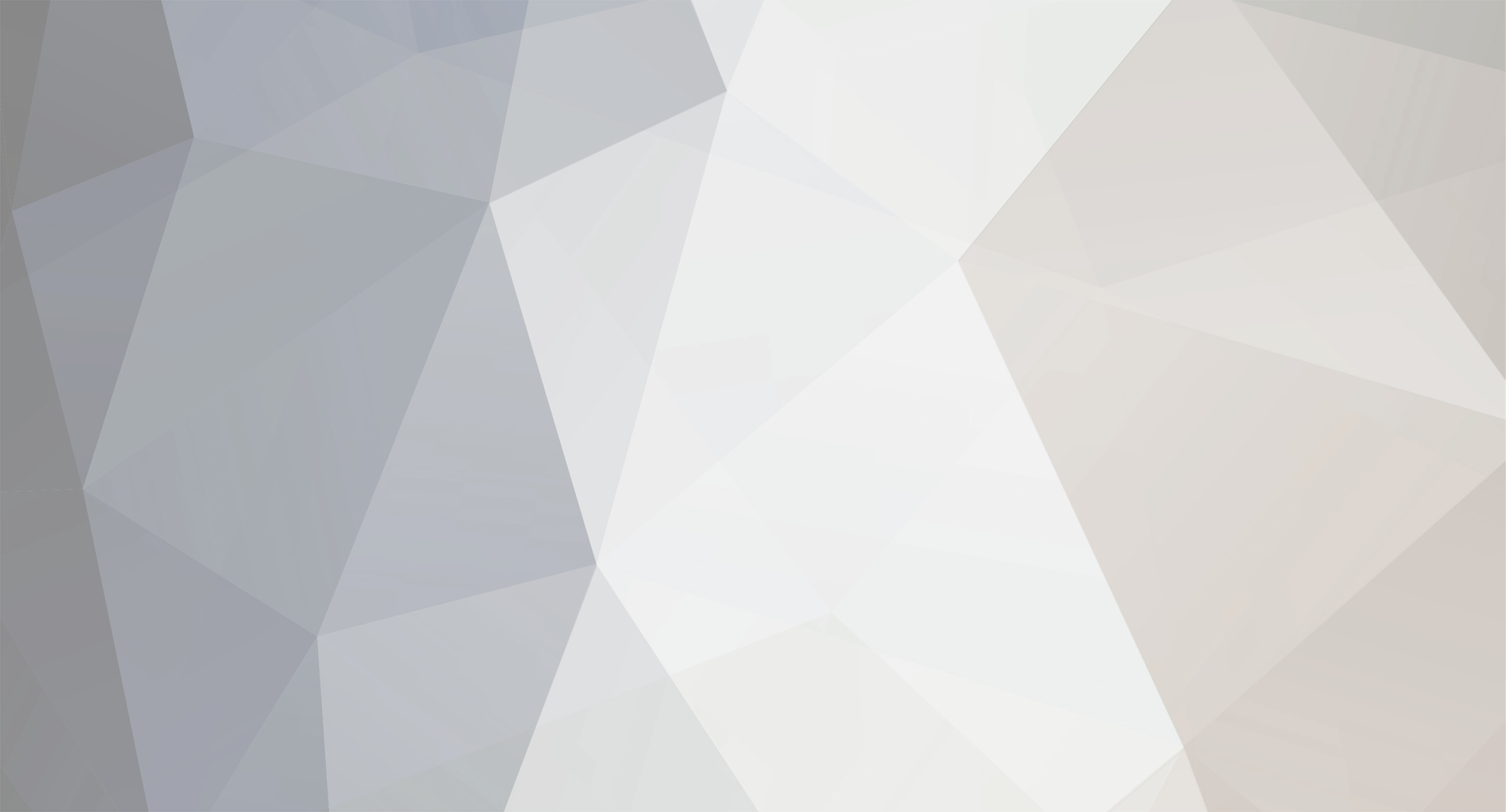
mike skingle
Members-
Posts
51 -
Joined
-
Last visited
Content Type
Profiles
Forums
Blogs
Gallery
Calendar
Downloads
Everything posted by mike skingle
-
The exhuast holes in the cowl were and still are blocked by gaffa tape. I'm not sure if you would get enough draw through the exhausts but its worth a try. If i get the chance I'll try running the engine with the gaffa tape removed and block the duct. What could possibly go wrong ?
-
Hi Ron On my mustang the air enters through the chin intake gets forced to the lower left side (as you look at the model from the front). The air is then forced across to the right side through the engine cylinder heads by the firewall and a baffle stopping the air going over the top over the crank case. The air then exits through a hole in the firewall on the right side. And is ducted out the back of the fuselage. At an ambient temperature of 16°C the temperature in the duct is about 40°C. Currently I am working on modifications to a YT spitfire. The air will go in the oil cooler intake and be for to the left lower side of the engine bay and across the cylinders and out through the firewall. The only difference is there will be no ducting and the air will be drawn out of the fuselage through the back of the radiators underneath the wings. The theory is that the radiators will draw the air through the fuselage and the fuselage acting as a duct will slow the airflow so less turbulence near the carburettors but we'll see. Ron my old yt mustang balanced with no lead and a laser 150. The added weight of the inline twin means to save adding weight to the tail, mounting the servos in the tail maybe a solution. My test mustang the servos and dual batteries are towards the rear of the wing and I have added weight to the tail to get a better CG balance. It's not been test flown yet though.
-
Hi Ron I've checked the CG and its slightly forward of 137mm at around 130mm when measured from the leading edge at the centre of the wing. It needs a little back pressure on the stick, so 137mm is probably right not 157mm. If you're building it from the kit then I would suggest that you consider putting either or both the rudder and elevator servos in the tail as I have 2 large lipos and the fuselage servos towards the back of the wing and it's still needs more weight towards the tail.
-
I have an Aerodrive 17x8 wooden prop otherwise it would be a G sonic 18x8 or 16x10. Or a beila 16x8 4 blade ? I found that the support for the rudder snake had come unglued from the fuselage andwas now wedged further down the fuselage hence the change in rudder trim.
-
Jon full right rudder trim had been applied to try and straighten the rudder, not sure how it came about, it was straight when setup in the workshop but when it was taken out at the field the rudder was slightly off to the left so I will investigate and get back to you but looking inside the fuselage it looks like the guide for the snake has bowed not sure why. I have a 17x8 so I'll try it next time, it might not be an APC though. The pilot in question was very restrained on the first flights apart from a short burst of full throttle most of the rest of the flights were at no more than 2/3 throttle. There didn't seem to be any problems overheating and ground runs have shown no overheating. The engine also has had a reasonable running in period so it was time to see if the cooling was sufficient at higher throttle settings (which it was) and see what it can do, but most of all it was about having lots of fun as we probably won't have weather like that again any time soon, with a plane that looks and sounds great.? still grinning ? If you have any specific requests then we'll see what we can do. ?
-
YouCut_20211117_222015568.mp4
-
YouCut_20211117_215733831.mp4
-
YouCut_20211117_214951848.mp4
-
YouCut_20211117_201318288.mp4
-
Paul you may not like this but here's some more videos. An intermittent fault with one of the remote glow plugs and a reciever have caused a few false starts, but it has caused me to ground run the engine a few times and the good news is no overheating problems even after a 10 minute 30seconds run that's with an abiet 16°C. We'll have to wait until the summer to see if the warmer weather is a problem. Ron I will measure the CG but I wanted to see how it flies with the change in battery position before measuring it. It flies great but see is believing. YouCut_20211117_200339522.mp4 YouCut_20211117_200339522.mp4
-
A challenge for you Jon an eight cylinder radial 2 banks of 4 cylinders
-
I think on this occasion ESM misprinted the CG. I'm sure coming up to the field will be fine. I'll give you a call next time I'm going. I haven't actually touched the tuning it started easily and seemed to run with great throttle response. I didn't particularly want it screaming away on its first flights, and half throttle was more than enough. The undercarriage is all fixed now we just need some good weather to fly it.
-
Using the finger method it was around the 135-140mm from the front of the wing.
-
Jon advised a 16x8 so I put a grey graupner 16x8 on it. I think once it's run a bit I'll try something slightly bigger but most of the flight was around half throttle. Ron is your YT Mustang the P51B or P51D as I found that the manual has the CG at 137mm and 157mm respectively and I seam to recall that the instructions were wrong i think on the P51D. I hope to accurately measure the CG but I think it's closer to 137mm. To get it at 157mm I would have had to put 300grams of lead in the tail? just something to consider if your planning your build.
-
The last flight with the cowl on. Sorry for the poor quality it's the only way to get the file small enough. YouCut_20211022_231652089.mp4
-
YouCut_20211022_214911441.mp4
-
YouCut_20211022_214443941.mp4
-
Wheel wells came out when I put the retracts in the ones that came with it had been well used and twisted. I used the old oleos with some new electric retract units. I managed to get some of those traxx onboard glow leads and wired the plugs on 2 separate curcuits. The engine was test run and would start only on the front cylinder when both glow plugs were attached to the battery. Both glow plugs when tested worked fine they were New OS type F . Applying the battery to one plug at a time got both running and the engine ran very smoothly. The model was flown twice with the cowl off to balance and trim it. The last flight was with the cowl on and the engine performed faultlessly throught the flight and it sounded great ?. Unfortunately on the landing rollout just before it stopped the axle on one wheel came off and the retract pin bent so we had to stop. The rain follwed about 30minutes after. If I can work out how to upload the videos then you can see for yourself. All in all a good start. Hopefully the ground test run will upload. 20211018_111854.mp4
-
Jon Please put me down for a 540 radial and a 200 or 310 flat twin. Cheers Mike
-
Ron the tank can be 60mm wide as the ribs inboard of the wheel wells are about 30mm from the centre ribs
-
Some progress today lowering the fuel tank cutting a section from the leading edge and boxing it in again. Unfortunately due to the ducting the tank is off the centre line with the result being one of the wheel wells is in the way restricting how much the tank can be lowered without taking all the ducting out. (Sorry Jon ) I'm not going to be able to get the tank any lower Without alot of work. currently it's 50mm x 65mm cross section at the narrowest point. Anyway this is proof of concept and I just need a starting point ideally soon. Ron when you do your yt P51 i suggest a tank no wider that 30mm either side of centre line and it will fit nicely between the wheel wells ? Ron I'm afraid I haven't done any 3D printing it might have made things a bit quicker. The duct is balsa and fibreglass. I think Ted on page 11 on the 200 inline thread printed. My ducting only goes up as far as the servo tray if it needs biger ducting then I'll take it out and start again.
-
Jon I've managed to lower the tank and am in the process of smoothing out the bulkhead to ducting connection. My initial thoughts on cooling were chin intake down the left side and across and out the lower right side of the bulkhead. When Ron had the problems with the carburettors and had to add the tubes i tried to work out how to make the flow of air smooth as I assume that there is some turbulence in the cowl which varies depending on the speed of the airflow. Any how after many hours of thought several watches of Jons video and with no other examples I'd start at best guess. And here it is. The extra holes in the bulkhead will be blocked up. Any other suggestion or pictures of what you guys with your 200 inlines have done would be helpful.
-
Sorry my photos are abit out of sync. These one show the top section of the front fuselage cut away as you can see it will be covered by the cowl when it goes on. The next one is the exit of the cooling air duct. The last one shows the ducting through the fuselage. At the moment this is abit of a frankinstein but it's move of an attempt to find out how much cooling air is needed.
-
Hi guys I have just started a new thread ( I think it'sthe first time I'vetried to start a thread) for the laser 160 inline twin that I've been fitting in a YT international P51D. I hope it makes sense
-
There's the engine mounted it was on a 5mm ply which made planning and modification easier. Removong the top section of the front fuselage made getting the 18mm thick bulkhead alot easier. The ducting was made in sections out of a mixture of balsa and fibreglass.