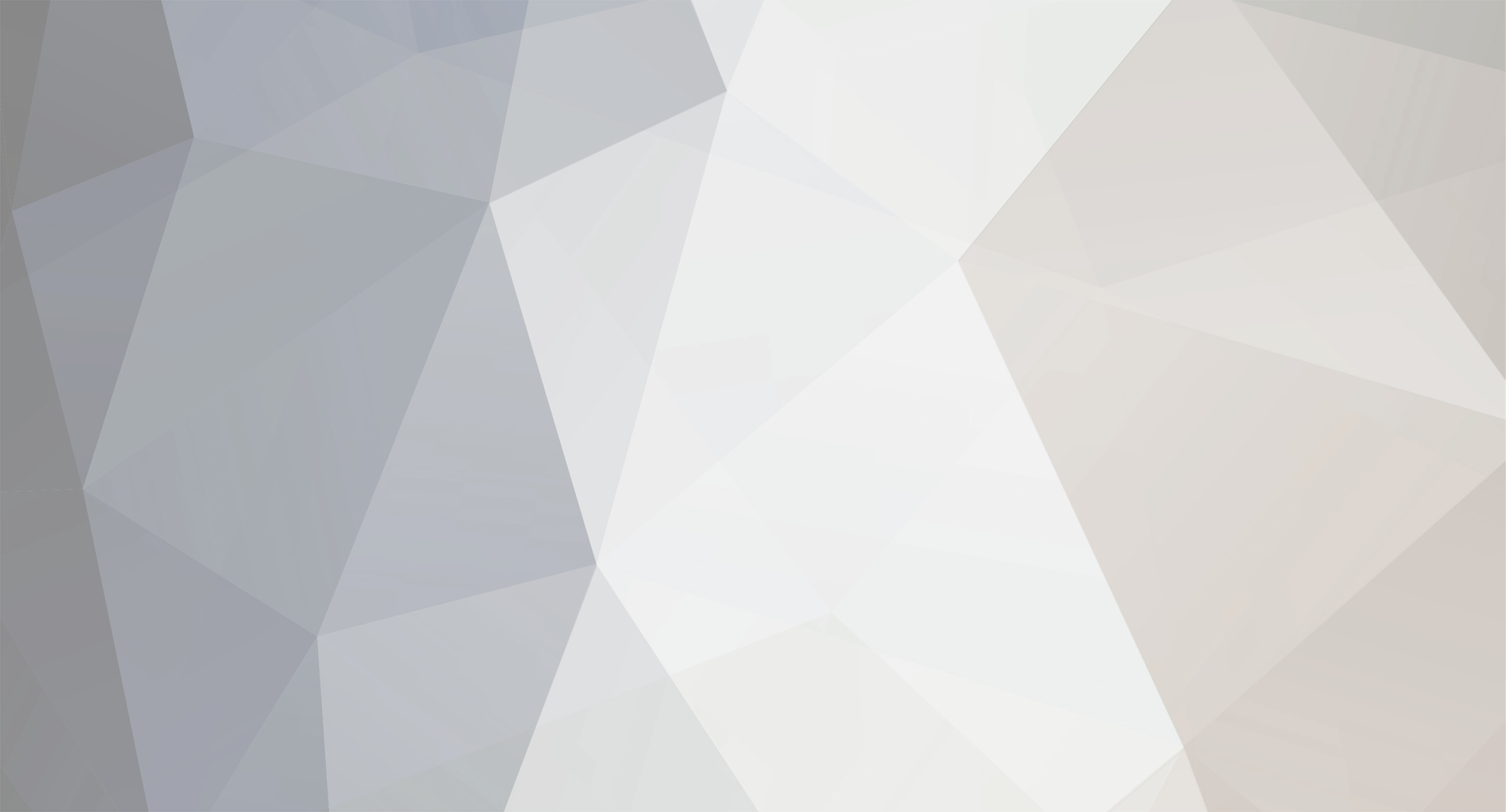
Ben M
Members-
Posts
43 -
Joined
-
Last visited
Never
Ben M's Achievements
0
Reputation
-
Ben M joined the community
-
Hi WolstonFlyer, That formula is interesting. I have seen other versions. However the parameters are defined in a non-numerical way. For instance CL is related to the pitch however we do not know if we need to use an angle in grades, radians or an trigonometry expression such as sin, cos, tang. The speed is related to the RPM however it doesn't say if it is angular or linear speed (the last one may need an integral because the linear speed is different for each point along the blade depending on the distance to the rotor's center). To be able to calculate Lift in a numerical way we need to properly define each input parameters including their units.
-
Very interesting. Thanks for the information. I think I understand it better now. Does anybody know how can we calculate the lift done by the blades while the rotor disk is horizontally and there is no cyclic control applied to it. I now that calculating it when the rotor disk is tilted or it has cyclic control is much more complicated. I would like to be able to calculate it in a simple scenario where the heli is hovering without moving and without wind. The formula should take into account (as per your comments): Wind speed: should be 0. Blades' size. Blades' pitch Rotor head's RPM Density of air The formula could be very interesting to play with. I wouldn't mind if the formula is complicated as long as the input parameters are well defined with the right measurement units to be used.
-
Hi Steve, Thanks for your help. I am not sure if I understand the concept of "Overproping". On the one hand, as per your explanation "Overproping" is an issue with the motor not having enough power to keep the requested RPM. On the other hand, as per the explanation on this site, "Overproping" is a problem caused by the propeller not being able to handle its load at the correct RPM. I understood that "Cavitation" was related to "Overproping" and it has to do with the propeller characteristics (including pitch) not with the motor’s power. The helicopter’s rotor is a propeller which pitch can be changed on the go. However at the end of the day it is a propeller and we can study it as a fixed pitched for a given angle of attack. Regardless of the meaning of “Overproping” my interest is about how to know if the size of the blades are right for the heli's weight. Is there a way to calculate the ability of a given blades to generate lift (assuming the motor has enough power)?. I am assuming that not all blades are good for all helicopters due to their ability to push air down and generate lift. I guess that the bigger the blades are the more air can push down and thus more lift. Does it make sense? Thanks again, Ben Edited By Ben M on 08/02/2015 23:48:13
-
Hi, I have some doubts about overproping on helicopters and I would appreciate if you could help me. To be honest I do not know if we can talk about overproping on helicopters. I have seen that this term is used for fix pitch propellers. For this reason I will explain what I understand as overproping on helicopters: When the pull provided by the rotor disk at a significant RPM doesn´t provide lift enough to hold or lift the helicopter. In other words, the rotor head´s load (helicopter weight) doesn’t allow the helicopter climb (or hover) as it should with a given rotor speed and angle of attack. Is my previous definition of “overproping on helicopters” correct? Can we talk about "overproping" on helicopters or is there another term for helicopters? Can we fix an overproping issue by using longer blades (assuming the motor supports it)? Is there an easy way to measure or calculate if there is overproping? Could we calculate the lift a given rotor disk should generate at hovering? On the following link we can see how to calculate if there is overproping in a fixed wing aircraft: **LINK** I wondered if there is a similar method to calculate the same concept swapping translational speed by vertical lift. On the following link there is a formula to calculate rotor blade lift. However it depends on a parameter called “lift coefficient at specific angle of attack” which is unknown so I cannot use it. **LINK** Thanks in advance for your comments. Ben
-
Thanks Dave for your corrections and for your comments. They are very interesting. I didn't know anything about "Overproping" or "ESC timing". I saw the ESC setting called "Electronic Timing" but I didn't know what it was so I followed the manual's instructions which were: 1. "6 or more poles should use Mid timing" (the 450L Dominator's motor has 6 poles) 2. "High timing gives more power at the expense of efficiency. Always check the current draw after changing the timing in order to prevent overloading of battery" 3. "When setting to the Quick throttle response speed, the accelerative peak current will increase." The problem of the motor stopping while screeching is clearly related to an excessive current consumption. I would have never tried any setting that may potentially increase the current draw. So I did not pay attention to this setting and I used the default value "Mid timing". This suggests the ESC was losing timing (it pulses the three windings to gain rotation). For this to happen at all there was something clearly wrong, and to continue to use the model without finding the reason and curing it was sadly always likely to end in tears. ESCs have user settable timing settings to adjust for differing motor winds. I doubt the Align ESC is any different. If an ESC cannot keep pace with the pulse rate you get a high pitch whine/scream. Do you think that using a "High timing" value may help to avoid the motor stopping and screeching? How can it be if this increases the motor and ESC current and temperature? Your figures above do not include head speed counts, but your text suggests that you (and from your comments others) have exceeded the safe load, possibly by over pitching the head. 20 amps though is not that high for a 3S Heli installation! What do you mean with "exceeded the safe load"? What make you think so? In my case I was just hovering very slowly and within a small area. I have double checked the Telemetry data I got from the day the motor got burned. During the first 20 seconds of flight (take off) the motor RPM went from 0 to 30K. Taking in account its gear ratio of 10.08 (with the stock 12 teeth pinion and 121 teeth main gear) the main rotor head should be 2,975 RPM. After that the helicopter flew about 30 seconds (gentle hover) around 32K motor's RPM which should be around 3,174 head's RPM. I would say that these values are very high for a gentle flight. The radio settings I had that day were: Throttle curve: 0% 75% 85% 85% 85% Pitch curve: 50% 62% 75% 85% 95% Pitch angle: 0º 2º 5º 7.1º 9º (Based on measures taken on the bench with each Pitch %) In the moment of the motor failure the throttle stick should be just over the centre: throttle 85% and Pitch angle between 5º and 7º. I would say 6º. The diameter of the main rotor head is 710 mm. Is this overloading? Can I know if there is "Overproping" with this data? 5. Its not a good idea to run any ESC at well below its rated max current. (or of course over!) I don't think I'd like to try to calculate and install a single ESC that would deal fully with those two very differing mech's, though obviously I don't know the correctness of the mech setup affecting their actual current draws at all flight stages. The ALIGN stock ESC for the 450L Dominator is rated to work with a max continuous current of 45A and a max voltage of 22.2V. Does this mean that flying between 8 and 14 amps may damage the ESC? 6. A high kV rated motor has comparatively little torque. It takes less extra mechanical loading to push it over the edge out of its "comfort zone". That is why it should have a smaller pinion to allow it to turn at its design speed while getting the right head speed. And why its a little more critical on any mechanical stiffness. This is why I think that making the 3,200 KV motor pinion bigger (more teeth) than the one in the 6S version makes the 3S version weak and prone to electrical problems. Edited By Ben M on 10/01/2015 21:02:48 Edited By Ben M on 10/01/2015 22:27:43
-
I have read several publications talking about the two different versions of the ALIGN 450L Dominator where the S3 version seems to be very good and the S6 is extra powerful. Guided by this information I made the mistake of buying the S3 version. I want to share it hoping I save some frustrations and money to somebody else. After few flights with the S3 version where I only tried to keep the helicopter hovering 1 metre high I started to have problems. The motor stopped in the air at the same time that it made a strange noise (pitched whine). It happened intermittently in several flights until the day that the motor got burned. My conclusion after a thorough study is that the problem was that the S3 version’s motor draws too much current and the components that provide that current (ESC and battery) cannot support it. If you want to know more about this issue then you will have to read the long version of this post.
-
I have read several publications talking about the two different versions of the ALIGN 450L Dominator where the S3 version seems to be very good and the S6 is extra powerful. Guided by this information I bought the S3 version because I was not interested in extreme 3D flight so I thought I didn’t need “super power”. I want to share my experience with the aim of helping somebody else to avoid my error. I bought my S3 version and after few flights where I only tried to keep the helicopter hovering 1 metre high I started to have problems. The motor stopped in the air at the same time that it made a strange noise (pitched whine). It happened intermittently in several flights until the day the motor got burned. After a thorough study in technical forums I found other people with the same problem and all of them had the S3 version. None of them had the S6 version. This was strange because the S6 version is more popular. Most of the people buy the S6 version so I was expecting that someone with the same problem had the S6 version. Especially because I was pointing the ESC as the responsible of the problem. My conclusion after quite some time (and money) spent is that the problem was not due to any faulty component. It is just a matter of wrong design. The S3 version’s motor draws too much current and the components that provide that current (ESC and battery) cannot support it. The S3 version has a 32,000 KV motor which is different from the S6 version’s motor which has 18,000 KV. The S3 version’s motor gets its power by drawing a lot of current with low (11.1V) voltage and the S6 version’s motor gets its power from the higher (22.2V) voltage (with less current). The ESC is the same for both and it has a feature (security system) called “Battery Protection” that detects if the battery voltage is under a certain threshold in which case it stops the motor. Telemetry information shows that even for a very gentle hover the S3 motor can draw quite some current (around 20 amps constantly). As the helicopter flies the voltage of the batteries goes down very fast passing from 12.6V to less than 11.1 in 1 or 2 minutes (in some flights). This voltage change makes the motor increases its need of current to keep the power constant and here is when the whole electric system collapses because the battery voltage drops even faster until the moment when the ESC stops the motor. This problem occurs intermittently and there are several factors than can affect such as: ESC settings. Radio settings. Gyro settings. Flying style. Batteries Environmental temperature. By finding the right settings in the ESC and the radio some people with this problem could get rid of it at least for some time. I did it and I thought it was solved until the day the motor got burned after stopping. This day the telemetry information indicated during more than one second the motor drew more than 730 watts which is its maximum instantaneous power limit. There was a moment when it drew 117.29 amps and the battery had 8.18 volts which made 959.43 watts (31% over the instantaneous limit). Talking about limits I remembered something interesting in my study. The S3 motor can draw more power than the S6’s one however its specifications has lower power limits which is something I cannot understand. The maximum continuous power limit in the S3 version is 500W while the same limit in the S6 version is 650W. And the maximum instantaneous limit in the S3 version is 730W vs the 970W the S6 version has. Moreover, the S3 version has a motor pinion with 12 teeth and the S6 version has a motor pinion with 11 teeth. This means that the S3 motor has to push harder to make the main rotor head turn once. This extra stress makes the motor draw more current. If the S3 version had the same pinion as the S6 version theoretically it should need less current. The only reason I can think of why ALIGN may have chosen that pinion for the S3 version is to get similar rotor speed in both versions. In my opinion, it is an error because they are raising the risk of electrical problems when the people who buy the S3 version are expecting to have less flying power than the S6 version. Finally I upgraded my S3 version to the S6 version and now the helicopter flies with current flows between 8 and 14 amps (with more active flights) with the exact same ESC (I didn’t change it). The only component I changed was the motor, the motor pinion and the batteries. In summary, the S3 version brings its electrical components to their limit which has a high risk of problems. And the only way to be get rid of them (with peace of mind) is by choosing the S6 version or upgrading your S3 version to the S6 (if you already bought the wrong one). My experience in the RC world is short (only 1 year) so I do not have sense of what is normal voltage for a battery and what is an extra powerful battery. If I read in several sites that S6 is extremely powerful and 3S is normal then I believe it. However, as in many other sides in life things are relative. In the case of the 450L dominator the S6 battery is not that much, it just what it needs to fly. I may be wrong in any of my thoughts. If somebody has different experiences please share them so that all learn from them.
-
The end of the year is a good moment to summarize our achievements. I thought it would be nice to share it with all of you who helped me with your comments. Finally I got first the Blade Nano CPX to practice at home and later the ALIGN 450L Dominator 3S to practice at the flying field. The first one was nice because I could "fly" it at home. However it was so unstable that was extremely difficult to keep in the air. It helped me to play with the radio settings and see how important are. The radio settings made the difference between being and not being able to fly it. After playing with the Nano heli for some time it started to have problems. The main motor started to stop during flight. The shop where I bought it didn´t provide the support I was expecting from them. I read it was a problem with the motor and I saw several people with the same problem. I decided not to spend more money in that heli. The ALIGN 450L Dominator was much more stable. I would say it was easier to fly than the one on the simulator. I was using Microbeast Flybarless system (from BeastX) with a beginner setting that made the heli very docile. The main problem I had with the 450L Dominator was the motor. In several occasions the motor stopped while flying and started to do a strange noise. After a lot of research I found out that the 3S version motor (with a 3,200 KV motor) has a problem that makes the motor stop in some circumstances which are difficult to control. I decided to get rid of the problem by upgrading the heli to the 6S version. After changing the motor, the motor gear and the batteries the helicopter changed completely and now flies without any problem. My flying skills have improve a lot during this year. The tool that have helped me the most has been Phoenix simulator. The real helicopter is amazing but I could not go to the flying field every week. The simulator was available every day for a quick flight at night. Every time I had a chance (which was not as often as I would have liked) I practiced for few minutes. I realized that the more regularly I practice the more I improved. I felt a big improvement when I started to manage the orientation. I would say that orientation is the big thing to learn. More than everything else. And the simulator is perfect for that. I agree with the people that say that the real world is different to the simulator however the orientation is the same. If you master the orientation on the simulator you have a huge improvement in the real world as well. Other tool that helps to practice orientation are the micro quadcopters. The link below points to the model I have used to practice orientation. It is cheap and helps a lot: http://www.nexusmodels.co.uk/radio-controlled-models-bnf-airplane-jet/quadcopter-micro-quadrocoptor-blade-qx-hubsan.html After one year of learning I am very happy to say that I am able to fly a Collective Pitch RC Helicopter. Even though I do very basic maneuvers such as hovering, circles and the 8, I am very happy and proud of it. I hope next year will be as good as this one and I keep learning and making friends in the flying field. I wish a very happy new year to everybody. Ben
-
A beginners journey to successfully flying a Blade 450 3D.
Ben M replied to Andrew Cummings 2's topic in Helicopters
(CONTINUING PREVIOUS POST) That Sunday was very windy. Certainly not the best day for a first fly (for both the heli and the pilot). A reasonable person would have delayed the test but I was too excited and I wanted to take the risk. I found the heli more stable than those on the simulator. It was amazing! Although not all was good. It was having quite a lot of wagging. Also the ESC was getting too hot and the settings I had chosen for the radio needed some changes. And even with all that the heli has flying (hovering) so nicely! Amazing!! I had to pay somehow the rashness and the wind was in charge of it. Not only it was windy but also the wind was not constant. In addition I was trying to keep the helicopter as near to the ground as possible and the wind was making the heli move up and down so much. The heli was also too tamed down so that I was not able to counteract those fast movements up and down easily. Finally, one of those movements was strong enough to make the helicopter touch the ground (a bit strong) for a second and since then it started to make a noise. I landed it and checked very carefully but I didn’t find anything so I kept flying (hover) “normally”. When I arrived home I disassembled it to see where the noise came from and I found the Torque Tube drive gear with some teeth broken. The issue was around £10, fair enough. It could be worse. The good news was that all my effort had given me the ability of repairing the heli. The following flying days were much better. After the appropriate study regarding wagging I set the tail gain properly and the wagging disappeared (even with wind). I have also reduced the taming so that I have more control over the heli movements. I have increased the main rotor speed to try to low down the ESC temperature and it seems it is working (now it seems it gets less hot) although I am not completely happy about it. I have read that flybarless system doesn’t like low main rotor speed and the motors draw more current when rotating slower which in turn make the ESC get hotter. I am working with this. And this is my journey until now. I feel quite happy about my progress. Now my main challenge is learning to fly. -
A beginners journey to successfully flying a Blade 450 3D.
Ben M replied to Andrew Cummings 2's topic in Helicopters
My journey is similar to Andrew's. Since I was a child I liked anything that could fly. When teenager I wanted to buy a helicopter but my budget didn't allow me so I forgot about it. Last Christmas I saw a toy grade coaxial 3 channel helicopter in a shopping centre and I decided to give it a try. After flying my toy every day for several weeks I started to get interested in understanding how it worked. My research brought me to the RC helicopters world. And here I am a few months later flying my ALIGN 450L Dominator. How was it? Internet is wonderful source of information. Now a days saying “I don’t know how to do it” is just an excuse. Internet has the answer. If you do not find it directly you can find books and other resources where to get it. After studying videos about the basics I decided to assemble and fly my own CCPM (Cyclic/Collective Pitch Mixing) helicopter. Before buying any helicopter I had to see which one should be best for me so I keep digging on Internet and reading all I could. Before making any decision I considered all possibilities: Size Electric vs IC (Internal combustion) Brand Flybar vs Flybarless Belt driven vs shaft ('torque tube' driven (for tail rotor) Kind of flights I am interested in Budget I also got information regarding how to learn to fly and where to do it. This was how I found this forum. I was researching about places nearby where I could fly the heli. I didn’t want to spend money to find out later that I could not fly it nearby. With my research quite developed and an initial budget ready I started my shopping. What an exciting moment. My first shopping was the radio (Spektrum DM8) and the simulator (Phoenix V4) followed later on by a small Blade Nano mCPx helicopter for real world training (this was a very good advice I got from this forum). By then I didn’t know yet what helicopter I was going to buy although I knew that these three items were going to be useful to learn regardless the heli I chose later. Playing with the little Blade Nano was very interesting. I realized how difficult was flying it but also how painful was charging the batteries one by one. I also saw the importance of understanding the radio settings. With the right radio settings the helicopter is much easier to fly! During this period I decided to get enough batteries to be able to fly for a while and to get the right equipment to charge them in a reasonable time. I didn’t want to spend hours to charge the batteries after each flying day. The project budget was increasing accordingly too. After some time the moment of buying the heli arrived. Other exciting moment. Few days later I had the heli (kit), the power supply and many of the items I needed. The party was starting. What a nice sensation. My first CCPM heli!! Amazing It took me several weeks to assemble the whole heli (the time I could spend was limited). Many things to consider: how to connect the electronics, where to locate the receiver with its satellite, how to setup the main rotor head and the flybarless system. Y found the wiring the most difficult thing because the helis’ manual explained how to connect the ALIGN 3D flybarless system but I had got the MicroBeastX one, which is different. This was the only thing I didn’t get much information from Internet so I decided to study carefully each component and do my best guess. I was lucky and I connected everything right. Once assembled and “set it up” I tried to spool it up to track the blades. I had so much vibrations!! And I didn’t know what was wrong. It was time to research. I found a lot of information about the subject. I didn’t understand everything so I started for what it seemed to be “easier”: the blade balance. I got a precision scale and after several tries and days I got the blades balanced. New tests confirmed the balance was the reason of the vibrations. The big day arrived. I was going to fly my heli for the first time! I already had got my BMFA membership card so I had all what I needed. I also had visit several flying fields to see where I could go to learn and practice. Everything was ready but me (I was so excited and nervous). (MORE IN NEXT POST) -
Glad to read it, Mark. Let me know how it goes. Good luck!
-
As the title states it is a book to help you understand how to setup a CP RC helicopter. It is sold in PDF format through a Web site (http://www.rchelicopterfun.com/) where there are more useful help for beginners. It helped me a lot.
-
Hi Mark, Yes I did. It is amazing. I found it easier than the helis on the simulator and easier than a little Blade Nano I also own. The first day I flew it I had some waging (it was very windy). After I found the right trail servo gain setting, by the second flying day, it was flying stable as a rock even with wind. Well, I must say that my flying style is very basic as I am learning and also I am working on finding the right settings for the heli and me. I hope this helps. Ben
-
Hi, After having tested this schema I can confirm it works. I hope this helps somebody else. Ben
-
Hi all, I am assembling my first helicopter (Align TRex 450L Dominator 3S) and my knowledge about electronics is very limited. After studying how to wire the components there are some connections where I am not completely sure. I have read that a wrong wiring may cause damage to the equipment so I would like to make sure before providing the power. The components I am talking about are: Receiver (Spektrum AR8000) Flybarless system (BeasX Microbeast V3) ESC (ALIGN RCE-BL45X, DC Input 2S-6S 45A, BEC Output 5-6V 3A) Servos (3 x ALIGN DS416M and 1 x ALIGN DS525M) The wiring schema I have come across with my research is: I would appreciate if somebody has connected these components before and can confirm that my schema is correct. Thanks in advance. Ben