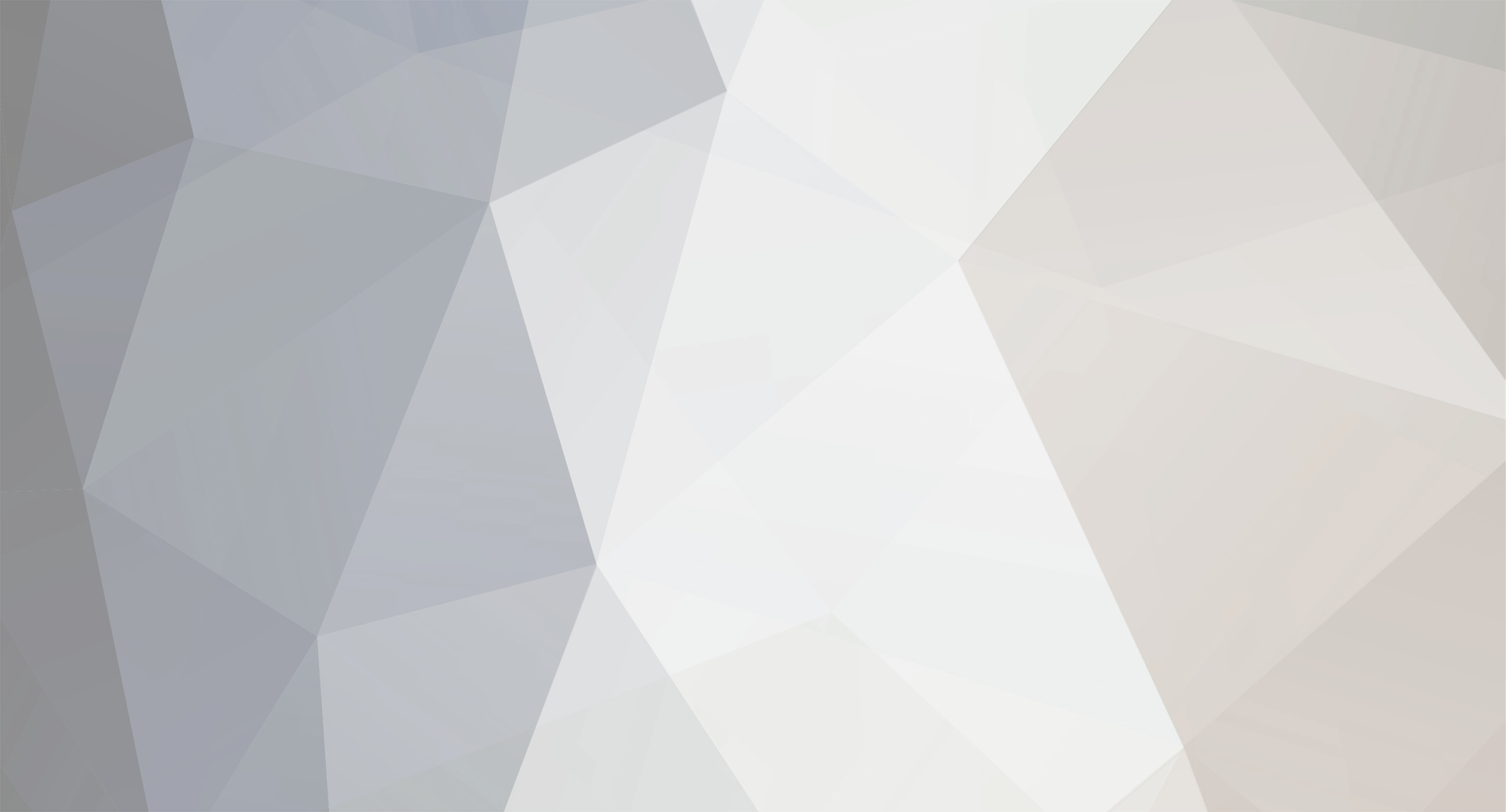
911hillclimber
Members-
Posts
566 -
Joined
-
Last visited
-
Days Won
2
Content Type
Profiles
Forums
Blogs
Gallery
Calendar
Downloads
Everything posted by 911hillclimber
-
This is very useful real-life experience, thank you all. Just been to Hemmingways for a fresh steel billet, but now home it is too short! Thus, a short ish return tomorrow i hope to swap for the right length. This is an insurance incase the pinning idea fails... I will try the force fit. I have borrowed a 1/4" reamer from my oldest friend (who has now joined this forum to keep abreast of my adventure) so that should fix it. I'll order a ground pin as suggested before from Simply Bearings. That should negate the need to machine the pin I hope. These things are sent to try me!! Mind you, I doubt a Myford Super 7 would help.lol
-
That approach had gone through my mind too, but I'm not sure I can get the pin in square to the crank or indeed to get the right interference fit to get the pin in tight and for it to tolerate the engine running. This is why I had the thought of En8 pin oversize and brazed in (after press fit). Machining the pin as before will get it square as the dia is machined down to a 1/4". If I allow the parts to air cool slowly the En8 should stay reasonably soft.
-
A bit more of a tease doing the crank shaft this afternoon. The crank is not co-operating at all. Slowly machined the shaft down to 5/16" ish using the tipped side n face cutter, new for the hacking down stage, then a fresh tip to get to a size that gave a nice running fit in the reamed bushes. That sounds easy, but was a sod to do, but now have a crank that fits into the case. However.... The pin that I just about managed to save and now 6 mm dia is in the wrong place. The throw is too large. I have obviously set the 7/16" throw to far or have crank case diameters too small or both. The clearance from the pin to the rear cover thread to far too small. Will measure tomorrow, but on the face of it would demand a big end con rod wall thickness of a mere 1/13", it should be 1/16". So, what to do to fix this? My thoughts are to remover the machined pin, and drill for an oversized pin, braze it in and machine the pin to a stroke less than 7/16", more 3/8". At this stage i have nothing to loose but to try it all and see if I can get it work. IRRITATING.
-
Thank you Dave, just the kind of post I expect on this great forum which I've used a LOT to get me over my model flying pains! There is a spark ignition engine on Hemmingways which I really fancy next.... Hemmingways are only 20 mins from me so can get another bar of En8 from them and do the crank again to drawing, but would braze an 8mm fresh pin in first and machine the over sized pin to 1/4" dia first. But this one first. Back from a nice sunny drive/visit to Ludlow today and some safety glasses i can actually see through. Seems I need them. (LOL)
-
Every day is a school day! The tool dug in as I was cleaning out the radius of the pin to the crank web trying to get the rad to = the tool tip rad. It is not too bad, a big end 6 mm v 0.25". I wonder about removing the machined pin and drilling/ream a 5/16 hole and make an En8 pin to fit and braze it all then set=up and machine the inserted pin to 1/4", but a lot of messing about. I'll need a 6 mm reamer now if I stick with it. In hindsight, I should have machined the blank down to around 5/8" and put that in the Vee block which would have tucked the two jaws in tighter, but we are where we are! I plan to machine the crank to 5/16 to suit the bushed reamed to that size, An hour should have that done. The lathe on it's lowest speed and the tipped tool machines badly. An old lathe but all I have! Feeling a bit dispondant at the moment, but tomorrow is another day.
-
Had a hard few hours in the garage on the crankshaft where I sort of managed to dodge a bullet. First, surface finish and tools. Tried a new tip, cuts well for 4 passes on En8 and feels dull after but still cutting. Tried HSS on the same material, no difference just so hard to shape the tip on a small grinder. With a good tool form results may have been better (?) Raised the lathe spindle speed to roughly 2 x the normal speed. Cutting much better using a fresh tip, but the belts are too tight and the head stock bearings were getting hot! Back to normal speed and light touch. As to the bloody crankshaft pin... All was going well right down to about 10 thou over the 1/4" pin diameter and suddenly the tool dug in, stalled the lathe and put a deep gouge in the pin AND rotated the bar in the chuck so loosing the pin position, just about the worst thing that could happen at this stage. Got the pin roughly back into place, but the pin still eccentric no matter what I did, so with it around and about right decided to carry on turning the pin until it cleaned up. This was, of course, below 1/4" dia BUT smack-on 6 mm so the con rod will have a big end dia of 6 mm and not 1/4" and we shall see what happens. Crank now back in the 3 jaw and busy machining down to 5/15" dia, lots of swarf. Day off tomorrow which may be just as well! 73T 911
-
Found the Hemmingway design on the web page, nice approach. The cuts I use are by instinct, 1/4 turn to 1/2 turn seems to be about 10 thou and I can cut 2 to 3 " in about 10 to 15 seconds all by hand turning the center screw on the round bed. I have a dodgy digital caliper to use to see how i'm progressing and down to the final pass. All a bit by touch and sound! Oddly, there is a graduated dial under the cross slide to set the angle od a taper cut, but you need a torch to read it. That is the only graduated control.
-
Well said. My daughter, who is approaching 38 now did Resistant Materials, an amalgam of metal and wood work. She took to it well but when things broke at her local school they stayed broken, never fixed, so the practical side disappeared quickly. She now works in property and is restoring a house with her husband who has trained her in nail gun use to polyfiller... Hope it warms up today so I can get back on the crank this afternoon in the garage, flippin' cold out there!
-
Interesting! Know the belt type you describe Jeff, thank you. Going to try machining with HSS tip tomorrow, see if that is better. If I speed the lathe up i loose torque and then the cut has to be even lighter. All this 'compromise' comes to play when cutting large diameters, around 1" or above the old lathe gets marginal. Come down to 3/4 or 1/2" max dia and all is far better. Still love this old lathe and these little challenges .
-
No idea at all. It is limited to a few pulley sizes and the V belt can't be adjusted to all of those, so the speed I'm using is 'one speed fits all'. I think is is part of the issue of surface finish and depth of cut. The motor on the lathe is not the strongest...
-
Thank you Brian, kind of you to say. This project has been interesting for me beyond what i expected. I think the Vees and clamp were indeed EITB as I made a marking out stand too, and a machinists vice, a Vee screw jack, a hacksaw, an adjustable pipe wrench and a tool box to put the lot in. Also made a small vertical drill press (!) but the thing got stolen at the end of the year. The Apprentice School closed after my year moved out.... No idea how i made all that lot. The plan is to machine the 'centre' off on the pin area and then centre drill off the tailstock and have a dead centre engaged. Pulled the tail stock back for ease of use and to calm my nerves! (and to take the pics) Tricky to get the tool bit right up to the rod pin as the tool holder is a bit balky.
-
Started my crank/crank pin turning this afternoon. Your Vee block gave me the inspiration, and it has worked well, albeit nowhere near the elegance, but I'm working with limited facilities (my best excuse). Can I ask Jeff how you get such good surface finishes? Seems you use HSS tools, not replaceable carbide tips, is that the secret/ I'm struggling to keep the tips good machining the En8.
-
Thank for the advice Jeff and it was something i worried about too. The jaws are all on the edge a bit. I check their tightness every 4th (fine) cut. I think I'm taking 10 though cuts at a time (no graduation on the cross slide so a guess) I'll try the wood shock absorber technique too! Will take some time.....
-
Started my crank/crank pin turning this afternoon. Your Vee block gave me the inspiration, and it has worked well, albeit nowhere near the elegance, but I'm working with limited facilities (my best excuse).
-
Another great few hours this afternoon on the engine. Felt in the mood to start the crankshaft. Big lump of En8, 3 1/8" long, bit of a tease to machine. Has some inspiration to how to set the bar up to machine the crank pin 7/16" off centre to set the throw of the crank/rod. Found my Vee blocks and clamp i made when 16 in my first year as an apprentice, and put faith in those parts being accurate (!)First time I have ever used them in 54 years. The Vee block mounted well on the 4 jaw, the hold being really sound and stable and the final jaw clamped the crank bar 'blank' tight and the stirrup clamp I made back then secured the top. The pics say it all. First few cuts were super light to test all is well. The mass turns as a blurr with almost no reference to the lathe to assure yourself you know where you are. This is the mother of all intermittent cuts, and a bit nervy to say the least. I have kept a check on the chuck jaw tightness! Leaving the pin well oversize (it is 1/4" dia when done) and only 3/16" long. This has perplexed me a bit since I bought the design, but seems to be working out so far. A lot more swarf to generate yet. 73T 911 Coupe, road/h
-
About to start the crank on my Sparey also. Will be very interested to see your method to machine the crank pin, but I think that is what the above set-up is for?
-
I'm a bit worried they are daily updates, but this project is keeping my tinkering spirit alive every day almost and getting obsessive much as my Lola build was. Made some significant progress this afternoon in as much as actually finishing the parts so i can move on to the Big Challenges ahead. Silver brazed the inlet stub to the cylinder that certainly blackened it! That was followed by soft soldering the transfer porting cover to the cylinder as well, and that added to the scruffy look.... I last silver brazed/soldered back at school for my GCSE in metalwork which I got a distinction in (and Art). Those were the days. The school was a bit off-the-wall in those days (60's) and there was an after school Club for all subjects, so I did metalwork where the game was to do anything outside of the curriculum, so we cast metal (!), brazed, and cut and made nice things. I really wanted to be a jeweler as a career, but my father was not so sure (he was an architect) so i did a heavy engineering apprenticeship instead. The crank case is all done, cylinder studs in and loctited and it all screws together! Amazing for me and my skill base. A few pics as ever, but I'm getting excited. 73T 91
-
Thanks Dave. Much of this project is getting a 100 year old lathe to do this when it has no scales on the slides or controls let alone being a 'compact' design. Some more for amusement: Determined and productive day in the garage on this engine. Wanted to finish the difficult machining on the crank case, the cylinder bore, the rod clearance slots and the transfer port plus the 4 tapped holes to retain the cylinder in place. Nearly did it all. Just have to tap M4 the 4 cylinder holes and the 4 mounting holes for the lugs if this engine ever makes it into an aeroplane. Had to make my own boring bar for the cylinder as i don't have the right size milling cutters or an adjustable internal boring bar, so spent 30 mins making one instead of spending and waiting for a 'real' one. Few pics below. The surface finish leaves a bit to be desired, but a dremmel will sort that out. Big step out of the way, crank next when I've finished off the case and the cylinder details. 73T 911 Coupe, road/hillclimber 3.2L
-
A few more hours today and a major (to me) step forward on this little project. With my new drill sized for 'pre-reaming' the crankshaft bushes here drilled and reamed those rock 'ard bushes. This bearing material is a serious challenge to the machine tools I have, but got there. This allowed at last the removal of the crank case from the 4 jaw chuck and onto the compound slide to machine the tricky bits on the case. This all went to plan after a few hours of preparation a few days ago. I made a close fitting mandrel and a stainless through bolt to screw everything tight to the vertical slide. Managed to arrange the lot on the lathe's cross-slide to allow rotation of the casting and to mill the right surfaces starting with the engine mounting lugs before a very long thinking time before attacking the cylinder bore and more. Made a pass or two on the one lug face (4 to machine) and it all cut well with very little chatter from the cross slide that (now) has near zero backlash (fixed 100 years of wear yesterday). A few pics: 73T 911
-
Phew! The dimensions on my drgs are the same as the original drg. Hemmingways have changed them at some recent time I presume.
-
Thank you. My drgs show the exhaust and the transfer @ 21/32 to their centres and the inlet 13/32 to it's centre from the same base surface/datum. I therefore think this is as per the original design?
-
Thanks for the kind words Jason, but don't look toooo closely!
-
What were the differences in the Sparey port dimensions please? Made mine to the supplied 2010 drg (+/- half a house brick) and getting ready to solder the port covers. Would like to know the difference incase I need to 'adjust' the position(s). Graham.
-
I now have the reamers and awaiting the drills all under size by 1/64" which might be here tomorrow. Had a few hours today making the crank bushes. The material supplied had a remarkably reluctant skin on the surface, but eventually the parts were made with about 2 thou interference fit (I guess) and were knocked in place with red loctite helping along the way. The bushes can now be drilled and reamed to 5/16" dia and removed from the 4 jaw ready for machining the case mounting lugs , deck face and cylinder bore followed by the transfer port. All tricky on the compound slide and the cutters in the lathe chuck. It is doing this that you realise how flexible even these old cast steel machines are even with light cuts. I have no idea how to machine the crank yet, but that is for another day. There are hours to be put into the crank case yet. The crank bush is much smaller, the part you see is the crank thust bearing face that is part of the main bush: 73T 911
-
Thanks for the advice. I have both but will prefer the soft solder route too. Borrowing the reamers tomorrow but awaiting the right dia drills for the reaming (all 1/64th under size). Spent ages sorting out how to hold the case for the milling and boring of the deck height etc, but all sorted now i think. No idea how I'm going to turn the crank pin on the crank, that will need some inspiration!