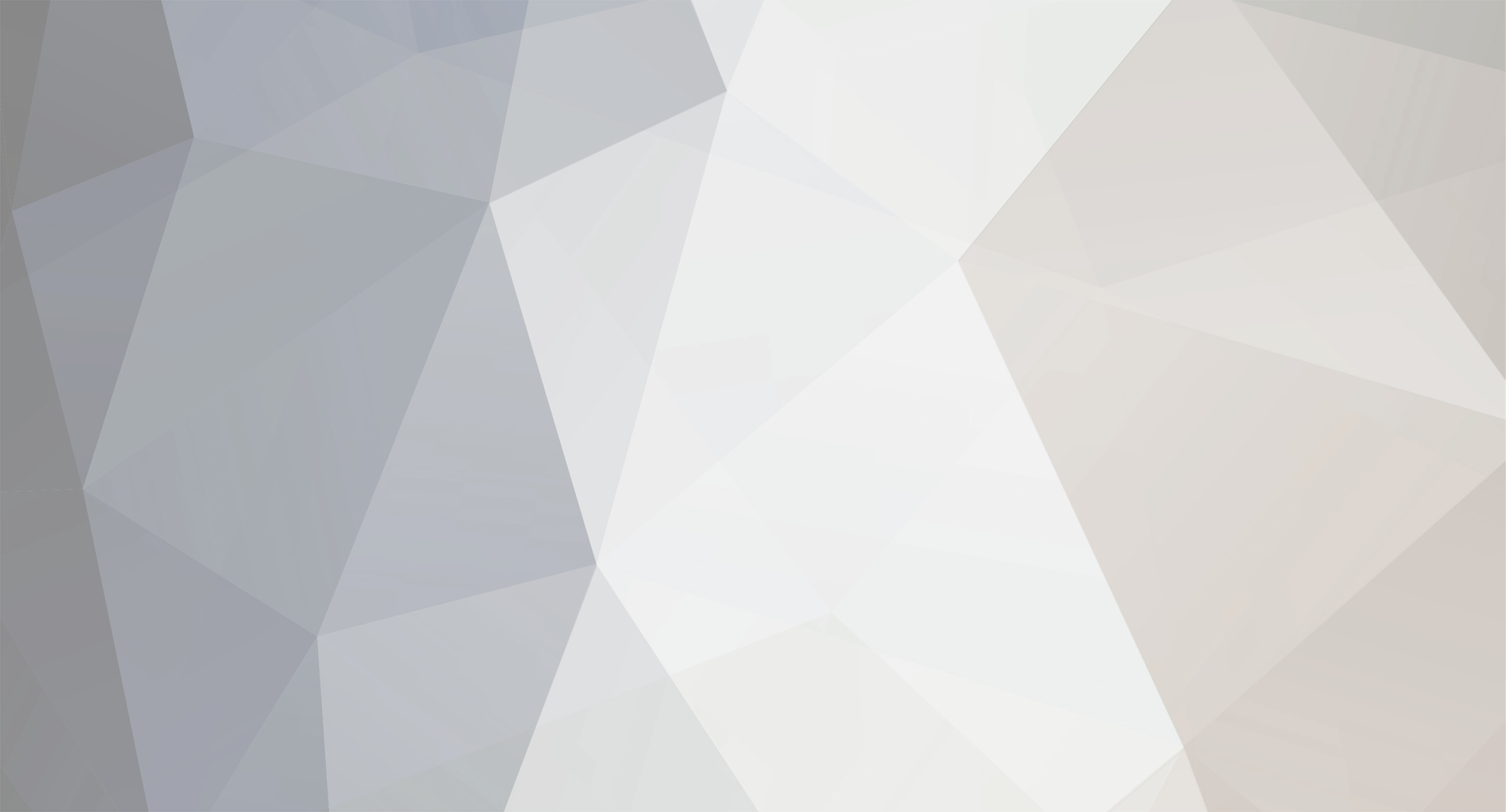
Matt Watts
Members-
Posts
161 -
Joined
-
Last visited
Never
Matt Watts's Achievements
0
Reputation
-
Matt Watts joined the community
-
I was meaning to reply as soon as I had the thing flying again, but that took WAY longer than I expected. Humble thanks for the help, after some rearrangement and plenty of glue, it's airborne!
-
Hello chaps! It's been a while. So after nearly a year's break, I'm starting flying again with my Flyingwings Raven. Thing is, it's got a CG much further ahead than it should be. I moved the battery back last year, but that necessitated cutting extra EPP out of the airframe. I'll need to cut more out to move it back even further, but I want to do so without compromising structural integrity. What materials would you reccomend for filling and reinforcing the gaps where the battery used to be sitting? Humble thanks in advance for your assistance.
-
I should probably have mentioned that this is my first attempt at working with an IC engine. You don't happen to have any guides on modifying said containers? Also, what's a balloon tank?
-
I've been looking around for a 8-9oz fuel tank that we can stick in our aircraft's wing. However, The wing currently stands as having a maximum thickness of 25mm. All of the fuel tanks I've seen are square in design, and none appear thinner than 52mm high. There's plenty of space in the other dimensions, but I really, really need something thin. So, are there any thin 8-9oz fuel tanks out there? I appreciate that the wing might still have to be made thicker to accomodate it, but what I'm looking at is clearly not ideal. The reason the fuel tank has to sit in the wing it that the engine is mounted into the leading edge. My thanks in advance for your help.
-
Oh yes, that's a point. I should have made it clear that we settled on a monoplane design. Sorry for not mentioning that earlier.
-
So some of you may remember me asking about the potential of a biplane design for our university's entry for the BMFA Heavy Lift Challenge. Well, after craptonnes of coursework causing all sorts of wailing and gnashing of teeth and causing the project to slide to a stop... a design has finally been chosen! Huzzah. One important feature is the integration of the engine into the wing (obviously with the cylinder head poking out in the breeze). This necessitates mounting the wing on a pylon above the fuselage to keep the propellor clear of the fuselage. Now, the maximum payload we can carry is 4kg, and I'm assuming that the added weight of the airframe, engine, etc would bring the effective weight being carried by the pylon to about 6kg. Thing is, I have no idea to what tolerance this pylon should be built - the aircraft won't exaclty be doing much bunting, but I don't want any nasty surprises tearing our beautiful (subjective) aircraft in two. So... yeah. 50%? 100%? Somewhere in between? Higher? Lower?
-
For us, the Heavy Lift Challenge is a voluntary thing we do outside of our course. It gives us first years something to do in between deadlines, not to mention a serious edge in the 'UAV' building we do next year. Don't get me wrong though, I'm in this because I love the hobby, and wish to learn more about designing and building models. And believe me, I'm not the group mentor. Perhaps someone who took a little initiative by seeking help from this forum, but little more.
-
Now there's an idea - a design/build blog. We have a meeting tomorrow, so I'll see if I can sort that out. People are still throwing basic design ideas around like hot potatoes, so it will be some time before we'll have anything particularly interesting to say. Oh, and by the way - the telemetry idea. Thank you, thank you, THANK YOU! I had completely forgotten such things even existed! I guess this is what happens when I don't keep up with things. Hell, I haven't even flown since last summer, after I accidentally fried the Raven's receiver... Much catching up to be done. Learning is fun! @import url(http://www.modelflying.co.uk/CuteEditor_Files/Style/SyntaxHighlighter.css);@import url(data:text/css,);@import url(/CuteEditor_Files/public_forums.css);
-
@import url(http://www.modelflying.co.uk/CuteEditor_Files/Style/SyntaxHighlighter.css);@import url(data:text/css,);@import url(/CuteEditor_Files/public_forums.css); Ugh... I swear I can hear the gears grinding along this ethernet cable... We're limited to an Irvine 40 engine, and non-flying scoring is done on empty weight. The cargo box is 80*80*200mm. So I'm aware that a biplane design will almost inevitably end up getting us worse scores in weight - I'd just rather not see our final work spread over the flying area through lack of available lift. The only (major) obstacle for a the lifting body design is the fact that we have to stick a forward-facing tennis ball on the plane, which must be sat at 45 degrees to the ground, and must have a 180 degree arc of 'vision' (it's supposed to be an imaginary camera), which can be neither covered, nor obscured by the prop arc. Of course, this will likely interfere with a fuselage-shaped aerofoil. The biplane idea was actually suggested as a way of getting the 'camera' as far out of the way of the tractor prop as possible. Still, I really, really, REALLY want the lifting body idea to be part of the final design. During the flying part of the competition, we aren't allowed to replace anything but the glow plug, undercarriage components and prop. The wording of the rules is a little vague, but I believe repairs are allowed between rounds - can anyone who did this before verify whether this was allowed in past competitions? @import url(http://www.modelflying.co.uk/CuteEditor_Files/Style/SyntaxHighlighter.css);@import url(data:text/css,);@import url(/CuteEditor_Files/public_forums.css);Edited By Matt Watts on 12/02/2012 15:55:32
-
Our head of aerospace suggested that a pusher configuration loses about 20% efficiency in comparison with a puller. I assume a puller with canards isn't the best idea? I can't imagine the wing being too happy if a deep canard deflection suddenly robbed it of fast-moving air from the forward-facing engine.
-
I always did love Rutan's designs... I mentioned the lifting body idea to the group a few days ago, which was met with a positive reaction. To be honest, anything that adds lift with minimal weight (and effort) increase is a godsend. I suggested leading edge slats on the leading edge, but the group don't want the added complexity - for the same reason, I have thus far refrained from suggesting canards. Say, what exactly are the aerodynamic advantages of something like the Long-EZ or Quickie? I mean, apart from being exceptionally slippery beasts. Oh, and for the record: if the biplane idea gets shot down in flames, I'm fine with that. At present, I can't really make an informed decision about what design style to take. Thanks for the replies by the way, I wasn't expecting nearly as much help as this! @import url(http://www.modelflying.co.uk/CuteEditor_Files/Style/SyntaxHighlighter.css);@import url(data:text/css,);@import url(/CuteEditor_Files/public_forums.css);
-
Hello again forum! It's been a while... So. I'm a member of a team undertaking the BMFA Heavy Lift Challenge. At present, we still have to decide on a basic design for the project. Given that the wingspan cannot exceed 2m, but the airframe must carry a payload of 4kg, a variety of solutions have been proposed. My personal choice would be to go with a biplane design - however, I understand that biplanes can be... complicated. Doubling the number of wings doesn't simply double available lift, and the weight penalty is not to be taken lightly (I'm sorry, that pun was to intended more to amuse myself more than anyone else). Currently, I'm looking into ways to reduce the level to which the airflow going past one wing interferes with the airflow going past the other. Apart from staggering the wings and trying to keep the vertical space between them as large as reasonably possible, what can we do to minimise drag and maximise lift? And are there any particular things we should be aware of with biplanes? Oh, and while I'm at it, is designing a biplane a terrible idea? And if so, why? @import url(http://www.modelflying.co.uk/CuteEditor_Files/Style/SyntaxHighlighter.css);@import url(data:text/css,);@import url(/CuteEditor_Files/public_forums.css);
-
Ah, I wondered if depriving the electronics of moving airflow might be part of the issue. I've spent the last two or three years having only an Easyglider to fly with (fortunately I have an RC flight sim), and only just got back into the hobby in the last week. It's an outrunner by the way.Oh, and you're going to have to fill me in here - what's PWM?My thanks for your help here.
-
I've just finished the Flyingwings Raven, but I'm having some troubles with the drive train that came bundled with it. Holding the aircraft stationary at full throttle with the (bundled) propellor attached causes the motor to suddenly stop after about 30-40 seconds or so. After lowering the throttle to minimum and attempting to restart the motor, it simply spits and sputters into life, and becomes almost too hot to touch over this period (the ESC also becomes quite hot, though not nearly as much). Since this issue never occurs with the propellor off and the motor appears healthy other than for this issue, it seemed reasonable to conclude that the ESC was at fault. Given that the motor is designed to operate at a high RPM, I believe (but I'm not sure) that the ESC timing needs to be changed from medium to high. Would I be right in doing this, and what exactly is timing anyway?
-
Best place to route a receiever aerial on a flying wing?
Matt Watts replied to Matt Watts's topic in General Radio Discussion
Great, thanks for the advice. I guess I have a bit of a range advantage in that the Raven doesn't need covering, though the icreased risk of getting the aerial caught in the prop is a little discomforting.Just out of curiosity, how well to 2.4GHz receivers behave in small flying wings? I don't have any 2.4GHz equipment, but my interest in the hobby has just flared into life again in the last week or so. Is it still generally superior to 35MHz?