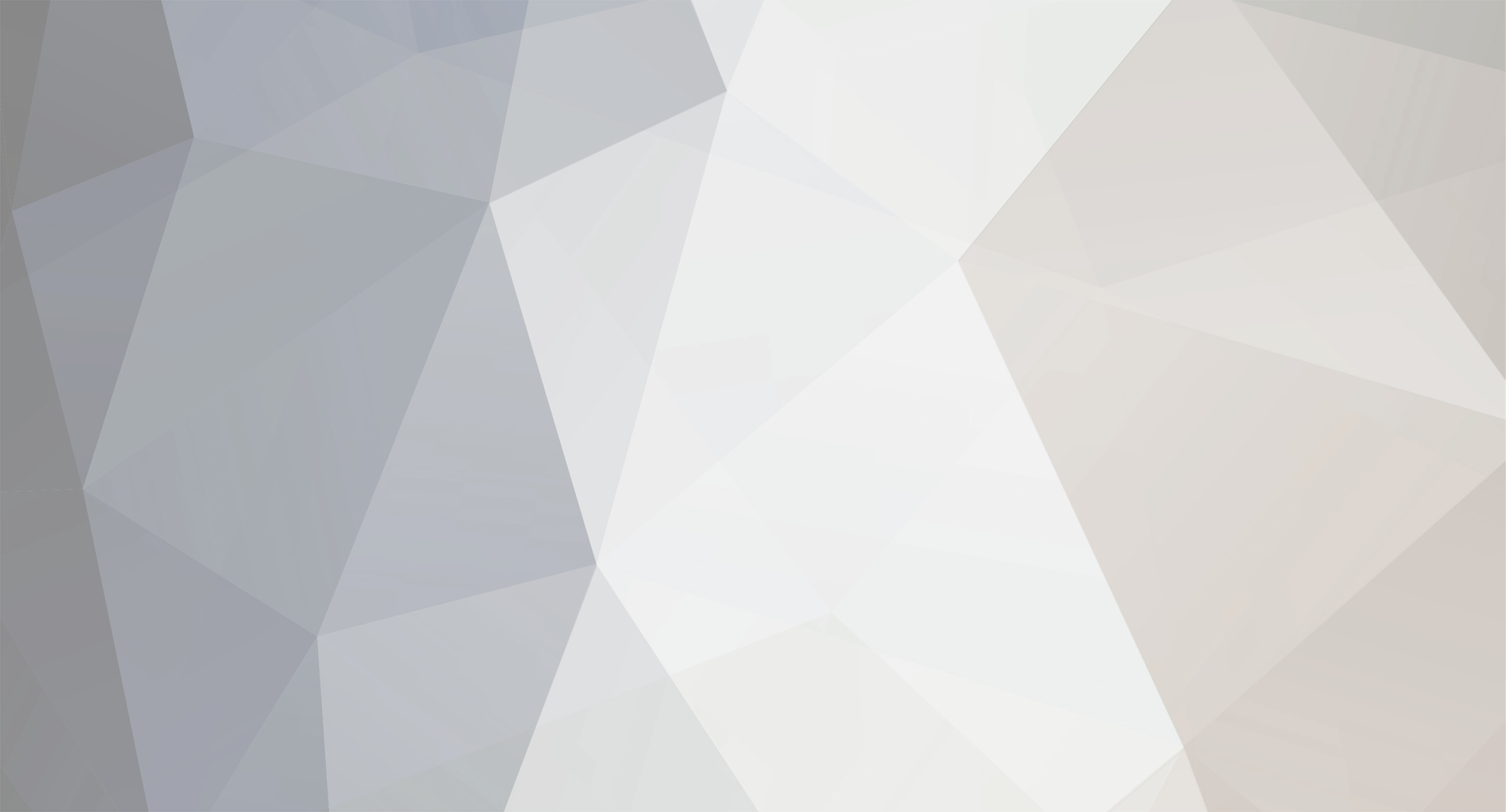
Ben H
Members-
Posts
180 -
Joined
-
Last visited
Never
Content Type
Profiles
Forums
Blogs
Gallery
Calendar
Downloads
Everything posted by Ben H
-
Pilot-RC Extra 330SC 88" 50cc
Ben H replied to Adrian Smith 1's topic in Build Blogs and Kit Reviews
Thanks guys, it's getting there. There was a break in the rain long enough to run the engine up today. The DLE 55RA was primed by performing the Walbro needle valve blow off pressure test, which was fine and filled the line with fuel nicely. A few flips by hand on choke and it fired, 3 more flips choke off and it ran. Apart from checking and sanding flat the reed valve seats, the engine is stock and fitted with a Falcon 23x8 beech prop. Oil is 40:1 stihl hp ultra. After a few minutes warming up at low to mid throttle, the idle was steady at 1800 rpm and 6750 rpm max. This is one sweet running engine, I haven't even touched the needles yet and there's no hesitation on acceleration and doesn't burble into 4 stroking until under 1/4 throttle. The midrange is really smooth, better than any DLE I've had previously...I wonder if the Walbro carb has been designed specifically for the engine?? I'd expect the max rpm to increase to around 7100ish and idle about 1700. Even as is is now, not broken it, the prop thrust calculator gives it 13kg thrust, making power to weight 1.625:1... Needless to say, I'm very happy with this engine! Prop thrust calculator - http://adamone.rchomepage.com/calc_thrust.htm Adrian, the DLE pipe is fairly quiet, certainly much quieter than a muffler and a nice low tone, but hard to quantify the actual volume level.. Tbh I wasn't really concentrating on the loudness!! I've got a db meter that I'll check it with next time and post the findings. I'm happy with it though, and pretty sure it's contributing to the engine performance. Bryan / Adrian, I hope you both enjoy your time away and that the weather is better on your return. Edited By Ben Holt 1 on 02/01/2016 15:28:51 Edited By Ben Holt 1 on 02/01/2016 15:52:13 -
Pilot-RC Extra 330SC 88" 50cc
Ben H replied to Adrian Smith 1's topic in Build Blogs and Kit Reviews
Congratulations on your maiden flights! Sorry to hear about the nose over.. Was it partly to do with the long grass? Interesting about the cg needing to move back a bit, I guess they give a nice safe starting point..I'm pleased to hear it though as I think I'll only just make the mark with my batts as far forward as they'll go. I'll make them a temporary fix for now... Do you know your all up dry weight? Mine is coming in at 17.5lbs ish, there might be another few oz of wiring yet... I would have thought it was a rocket with the os60 gt.. I'm sure it'll pick up with some gas through it! She looks great in the sun by the way! I'm jealous of your break in the weather, I hadn't flown for weeks.. Edited By Ben Holt 1 on 01/01/2016 22:50:36 -
Pilot-RC Extra 330SC 88" 50cc
Ben H replied to Adrian Smith 1's topic in Build Blogs and Kit Reviews
The wings saw the light of day today. Installed the aileron horns and servos. Not much to say here at hasn't already been said...the slots that the horns fit into needed some relief to allow the horns pivot holes to be positioned in line with the hinge and epoxy into place, making sure the horn has been sanded to give it a key and the covering removed as appropriate. I made up some 7" servo extensions with 22awg twisted wire and pulled through with the installed pull line (as others have mentioned, it was also a little on the short side making it fiddly). I put a cable joiner lock on the connector and attached it to the 2nd rib with some 3m foam adhesive pad, to stop it flapping about. I particularly like the cable tidy "swirl" in the 1st rib that the servo wire goes through. Very nice touch that keeps things neat and tidy. The mechanical setup was done first, ensuring equal servo arm movement to aileron movement in both directions, then used the Hitec Servo Programmer to programme centre and end points. This allows a balanced radio setup with minimum or no sub trim, and full servo travel up and down, giving the best possible resolution and no unwanted aileron differential to dial out. Adrian, did you manage to get a maiden flight in today? The weather was awful here -
Pilot-RC Extra 330SC 88" 50cc
Ben H replied to Adrian Smith 1's topic in Build Blogs and Kit Reviews
Another few jobs from the list... After a dry fit, I fitted the canister brackets with tri stock and 30min epoxy. The pair marked "rear" are too wide for the tunnel and required cutting down before fitting, but other than this it was straightforward enough. When it was dry, I removed the canister and header, masked off the area and sprayed some clear coat to fuel / moisture proof the area. The canister was refitted again and fastened to the header with high temperature rtv sealant. To ensure no leaks around the flexible section, I removed the Teflon tape, applied high temp rtv and re-wrapped in Teflon tape. The eagle eyed amongst you might notice some thin ply added to the lower front of the engine box, between the carb and the header areas. This is to prevent excessive heat causing vapor lock problems in the carb due to the rear exhaust header being directly underneath. Next was fitting the landing gear to fuselage spats, not sure if spats is the right term here but I'll call them that for now!! Maybe fairings is better? The fairings need cutting to allow them to slide onto the undercarriage and the black rubber trim fitting. The cutting was easily achieved with a dremel and cutting disc, while thin ca did a good job of fastening the trim, the latter was done by pulling the trim on and cutting to suit, then running thin ca around the inner lip of the trim which wicked in nicely and seems to have gotten hold of it very well. The fairings are fitted on the legs, which have been given a key with some 80grit in the area under the fairing, which were then attached with epoxy. Axles were next. I borrowed the idea of fixing the inner locknuts with Loctite 290 (green) overnight so they don't spin when tightening the nyloc nut. Wheels were fitted with collars and a dab of Loctite 242 (blue) on the grub screws. The threaded portion is ridiculously long so was cut down in the vice before fitting to the legs. I'll leave the wheel spats until after the maiden and when the ground is a little drier. Finally for today was to fit the top deck to the engine box, I decided to epoxy it on as I can access my throttle servo through the slots. Then finished off by opening an additional cooling slot in the cowl, to expose the remaining cylinder cooling fins.