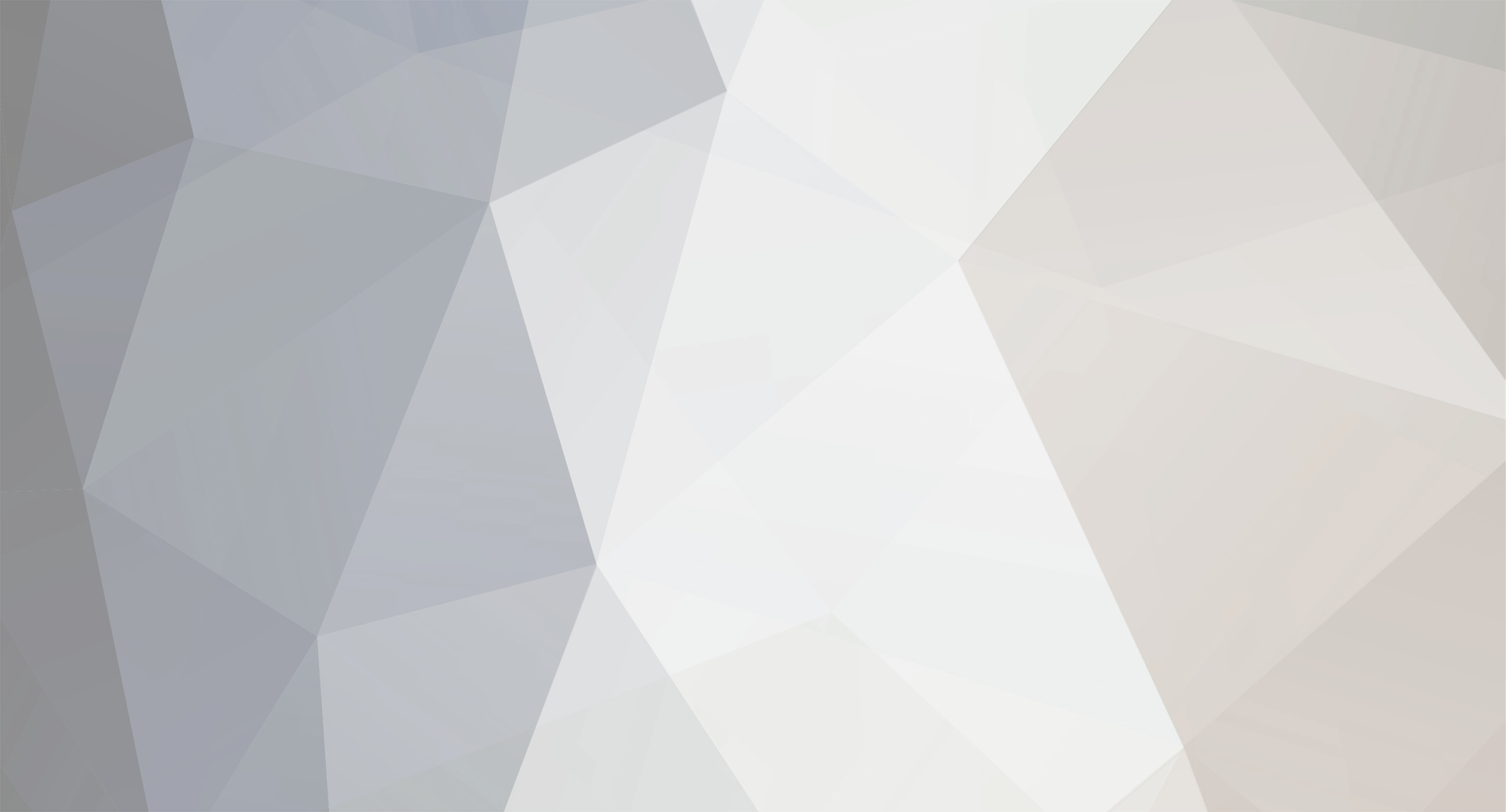
Phil Beard
Members-
Posts
223 -
Joined
-
Last visited
-
Days Won
1
Content Type
Profiles
Forums
Blogs
Gallery
Calendar
Downloads
Everything posted by Phil Beard
-
Andy Conway PSS BAe Hawk T1 the ideal starter PSS model
Phil Beard replied to Phil Beard's topic in PSS Build Blogs
Aft Fuselage top initial sizing fit prior to shaping and cutting hole for rudder to fit into. -
Andy Conway PSS BAe Hawk T1 the ideal starter PSS model
Phil Beard replied to Phil Beard's topic in PSS Build Blogs
Fuselage issue of skins not joining in the middle after some careful planking and add weights to the original skins to make all align seems to have worked as can be seen in the photo. Back to normal progress on the model hopefully tomorrow. -
Andy Conway PSS BAe Hawk T1 the ideal starter PSS model
Phil Beard replied to Phil Beard's topic in PSS Build Blogs
Well I decided to go with option wetting the balsa in the area of the curve with hot water and using masking tape and c;lamps to hold in place till dry. I used the technique I was told to wet the balsa with hot water and leave for 15 minutes and then try the bending and holding. This technique worked well but the plan that gave a developed shape of balsa required was wrong and you can see a 10mm space on both sides which I'll need to now plank. -
Andy Conway PSS BAe Hawk T1 the ideal starter PSS model
Phil Beard replied to Phil Beard's topic in PSS Build Blogs
Aft Fuselage pieces including the mounts for the elevator mechanism was put together and then installed on the respective fuselage side. Once the elevator mounts were glued in place Frame F8 can be installed. Note at the top and along the back edge in the middle small areas need to be filled with a balsa insert due to errors in the drawing pack, nothing serious. Final photo shows the 2 skins that need to be curved over the frames. On communicating with a number of PSS members the following methods could be used:- 1. Wetting the balsa in the area of the curve with hot water and using masking tape to hold in place till dry. 2. Wetting the balsa in the area of the curve with Ammonia and using masking tape to hold in place till dry. 3. Steaming the balsa in the area of the curve with hot water and using masking tape to hold in place till dry. 4. Cutting off the 2 skins and blanking the area instead. I'm going to try the hot water technique today and if it doesn't work I'll cut them off and plank the area. -
Andy Conway PSS BAe Hawk T1 the ideal starter PSS model
Phil Beard replied to Phil Beard's topic in PSS Build Blogs
Piers I do remove the majority of the material using a razor plane, but I still find the final sanding laborious and boring, especially with this area as I couldn't run the razor plane along the whole length. -
Andy Conway PSS BAe Hawk T1 the ideal starter PSS model
Phil Beard replied to Phil Beard's topic in PSS Build Blogs
It's a month on now from when I first started this blog and have made little progress today due to other priorities. From the photo you can see that the port forward fuselage side has been sanded to shape and now to do the starboard side. I find doing this sanding very boring. -
Andy Conway PSS BAe Hawk T1 the ideal starter PSS model
Phil Beard replied to Phil Beard's topic in PSS Build Blogs
Fuselage build continues and it's starting to look more like a BAe Hawk. Fuselage base was added and noting to chamfer the edges to 45 degrees before fitting makes it so much easier. Fuselage sides from 6.4mm balsa have been added between F1 and F3 and applying chamfer to these before fitting will speed up the process of the build. -
Andy Conway PSS BAe Hawk T1 the ideal starter PSS model
Phil Beard replied to Phil Beard's topic in PSS Build Blogs
Elevator control rod cut to length from 10 swg rod as can be seen in the photos. Work on the fuselage started again with putting in F7B. Note to mark as shown the area that needs to be glued as not the whole back. Cutouts for elevator rod to sit in put together noting you need a port and starboard. These will be glued onto the fuselage side later. Front fuselage sides need to chamfered to a 45 degree angle as shown in the photos, this will allow the other balsa sides to be added flush later. Final photo shows front fuselage being joined onto the aft after the chamfering has been finished. -
Andy Conway PSS BAe Hawk T1 the ideal starter PSS model
Phil Beard replied to Phil Beard's topic in PSS Build Blogs
Inserted elevator mechanism into elevator and bonded in place using epoxy. Filled bigger hole with balsa wood piece and the smaller hole with model lite filler then sanded flush. Remember to have the access to the grub screw on the lower surface and make sure you make a port and starboard elevator. Will finish the elevators in glass cloth later once these have been checked for fitment with the aft fuselage side. -
Andy Conway PSS BAe Hawk T1 the ideal starter PSS model
Phil Beard replied to Phil Beard's topic in PSS Build Blogs
Had also mean't to mention using this techniques you gets the 10swg rod going down exactly the middle of the square brass tube as their is very little if any play if you look at the tolerances. -
Andy Conway PSS BAe Hawk T1 the ideal starter PSS model
Phil Beard replied to Phil Beard's topic in PSS Build Blogs
I thought I'd make the square brass tube and collets which need to be soldered together prior to inserting into the elevator as shown in the 1st photograph. The main thing to remember here is to make sure the wife is out as you're going to need the gas hob to heat up the parts. The process is shown in the following photographs. Firstly cut the square brass tube to length and put over the 10swg rod and then fasten a collet on the bottom and tighten up with the grub screw. Put some tape over the other end of the square brass tube to stop it moving relative to the collet. Put the collet and square brass tube over the gas ring putting the end over the blue tip of the flame and bring to temperature and then solder. Results can be seen in the last photograph. -
Andy Conway PSS BAe Hawk T1 the ideal starter PSS model
Phil Beard replied to Phil Beard's topic in PSS Build Blogs
Wingtips have been sanded level flush with the top and bottom skins, only the rounding of the edges still to be done. Front fuselage has been fully sanded to shape or as near as, so much easier with it not being attached to the rest of the fuselage. The square metal brass rod has arrived in the post today and can be inserted into the elevator later on today. -
Andy Conway PSS BAe Hawk T1 the ideal starter PSS model
Phil Beard replied to Phil Beard's topic in PSS Build Blogs
Wing leading edges have been razor planed and sanded to shape as can be seen in the photo. Mylar hinges have been inserted into the ailerons and 2mm holes drilled through and half a cocktail stick pushed through and glued in place and onece glue is dry the cocktail stick is trimmed and sanded flush. The same process will be repeated once the ailerons are fitted into the wing. Wing tips have been sanded near enough to final shape and glued into place. Once glue is dry these will sanded to final shape. Forward fuselage to be razor planed and sanded to near final shape. This sanding part is the bit that I really hate. -
Andy Conway PSS BAe Hawk T1 the ideal starter PSS model
Phil Beard replied to Phil Beard's topic in PSS Build Blogs
Wing build continues with marking and cutting the holes for the mylar hinges both in the wing and aileron. Mylar hinges are 12.5mm width by 30mm long has been found to work. Note these will also be pinned into place later as described previously. Wingtips have been put against the end of the wings and marked so that these can be sanded to shape. Leading edges have been attached to both wings and initial razor planing and sanding to meet bottom and top wing surfaces undertaken prior to completing the final shape. Spruce strips have been added and glued in place so as to attach the servos into the wing. -
Andy Conway PSS BAe Hawk T1 the ideal starter PSS model
Phil Beard replied to Phil Beard's topic in PSS Build Blogs
Not much progress made unfortunately today. What you can see is that I've marked the positions for where the Mylar hinges are to be put into both the wing and the ailerons and the tolls used to make sure these are centralised. Note the hinges need to be pinned in place after being glued in place using 2mm holes drilled through and a cocktail stick then pushed through the hole and glued in place. Also photo showing the required rebate in the aileron and hole for the control mechanism to be inserted and bonded in place to stop any relative movement. Mylar hinges are made to the required shape from sheet bought from Hobby King. -
Andy Conway PSS BAe Hawk T1 the ideal starter PSS model
Phil Beard replied to Phil Beard's topic in PSS Build Blogs
Continuing with the wing build it's time to make the Aileron/Spoileron control fittings. Main points to remember is to make port and starboard side controls and make sure the out metallic brass tube is fitted prior to making the last bend. These are bonded in place using epoxy. -
Andy Conway PSS BAe Hawk T1 the ideal starter PSS model
Phil Beard replied to Phil Beard's topic in PSS Build Blogs
Top skins now fitted to both port and starboard wings. Note the pins don't go all the way through into the board only at the lead and trailing edge wing tips and the trailing edge root so that the correct washout is included using the wedge underneath as shown in the plan. Added to the root fairings to both port and starboard engine intake, note that these are handed so make sure you know which way up these are. As previously mentioned these will be tacked onto the side of the fuselage for sanding to shape prior to covering as this wont be able once glued in place. -
Andy Conway PSS BAe Hawk T1 the ideal starter PSS model
Phil Beard replied to Phil Beard's topic in PSS Build Blogs
Port wing completed to the same level as the starboard wing. Don't forget to include the reinforcing inside the wing at the hinge positions, note I moved the outermost hinge position to the final wing bay. Upper skins have been cut-out and glued together prior to fitting. Have also started to pull together the required external decals for the BAe Hawk once it's completed. Phil Cooke, Looks like it will be XX285. -
Andy Conway PSS BAe Hawk T1 the ideal starter PSS model
Phil Beard replied to Phil Beard's topic in PSS Build Blogs
Starboard wing build started and is undertaken in the same manner as the port wing. -
Andy Conway PSS BAe Hawk T1 the ideal starter PSS model
Phil Beard replied to Phil Beard's topic in PSS Build Blogs
Port wing build continues wing the addition of the lower wing 3.2mm spruce spar followed by the addition of the wing ribs which were only glues from the spar to the rear spar and don't forget to put the wedge in place so that the wing has the correct washout. Once the ribs are glues form the sprue spar to the rear spar it's time to glue the ribs to the lower skin by placing wedges under the skin at each rib position so that it forms the correct wing section. once all ribs are fully glues add the top spruce spar and this is where I decided to add 2.4mm balsa shear webs between the top and bottom spruce spars and adjacent ribs. This won't add much weight but will substantially stiffen up the wing. Also don't forget to add the 6mm doubler as shown on the plan at the dowel position. Placed a servo in the wing trying to decide best position and made up a little box for it to sit into and will include a spruce former onto the top wing skin so as to screw the servo in securely. Hope this blog helps anyone that decides to build the Andy Conway PSS BAe Hawk T1. -
Andy Conway PSS BAe Hawk T1 the ideal starter PSS model
Phil Beard replied to Phil Beard's topic in PSS Build Blogs
Now to start building the wing also. You'll need to cut out the angle template for W1 this should give the right angle for W1 so that you've 12.5mm dihedral under each wing, plus also make the wedge for washout under each wingtip which needs to be in place during wing build.. See photo's of the template for W1, dihedral requirement and the Wedge for washout. A spruce spar 3.2mm x 3.2mm is required top and bottom of the wing and I ripped mine from 3.2mm spruce sheet using a circular, this saves lots of money and time being able to cut to size any required strip from sheet balsa or spruce. W1 to W7 we're sanded within the top and bottom notches to allow the top and bottom spar to sit within at the correct angle. Drawing was annotated so that the ribs and spars could be positioned correctly once the 1.5mm skin was placed upon the drawing. Lines on the drawing were extended so that the skin could be cut to the required shape. -
Andy Conway PSS BAe Hawk T1 the ideal starter PSS model
Phil Beard replied to Phil Beard's topic in PSS Build Blogs
F3 top half needs to be glued into place using the angle guide to give the correct angle onto the bottom piece of F3. Once glue is dried insert the 3.2mm x 6.4mm balsa strip into cutouts in F3, F5 & F7 and glue into place as show in the photographs. Individual engine intakes need to be grouped into 2 sets of 3 and glued together as shown in the photos. -
Andy Conway PSS BAe Hawk T1 the ideal starter PSS model
Phil Beard replied to Phil Beard's topic in PSS Build Blogs
F4 added to the fuselage and the engine side fairings cut out of 12.5mm balsa and sanded to shape. -
Andy Conway PSS BAe Hawk T1 the ideal starter PSS model
Phil Beard replied to Phil Beard's topic in PSS Build Blogs
Aft fuselage exhaust pieces cut our of of 12.5mm balsa. As you can see form the attached drawing 9.5mm + 12.5mm doesn't equal 27.5mm. Therefore used 2-off 12.5mm balsa and will add a 3,2mm extra at the end and sand down to length. F3B added to the fuselage and used some 6mm dowel in the hole to make sure they align before fully clamping up. Remember to remove dowel as any glue seepage will end up with this being glued firmly in place. F4B as a spacer is then added once F3B is firmly set and then F5. Don't glue the bottom of F5 to the side at this stage as 12.5mm balsa inserts need to be fitted later. -
Andy Conway PSS BAe Hawk T1 the ideal starter PSS model
Phil Beard replied to Phil Beard's topic in PSS Build Blogs
Phil thanks for that. Have to say that it's a nice one.