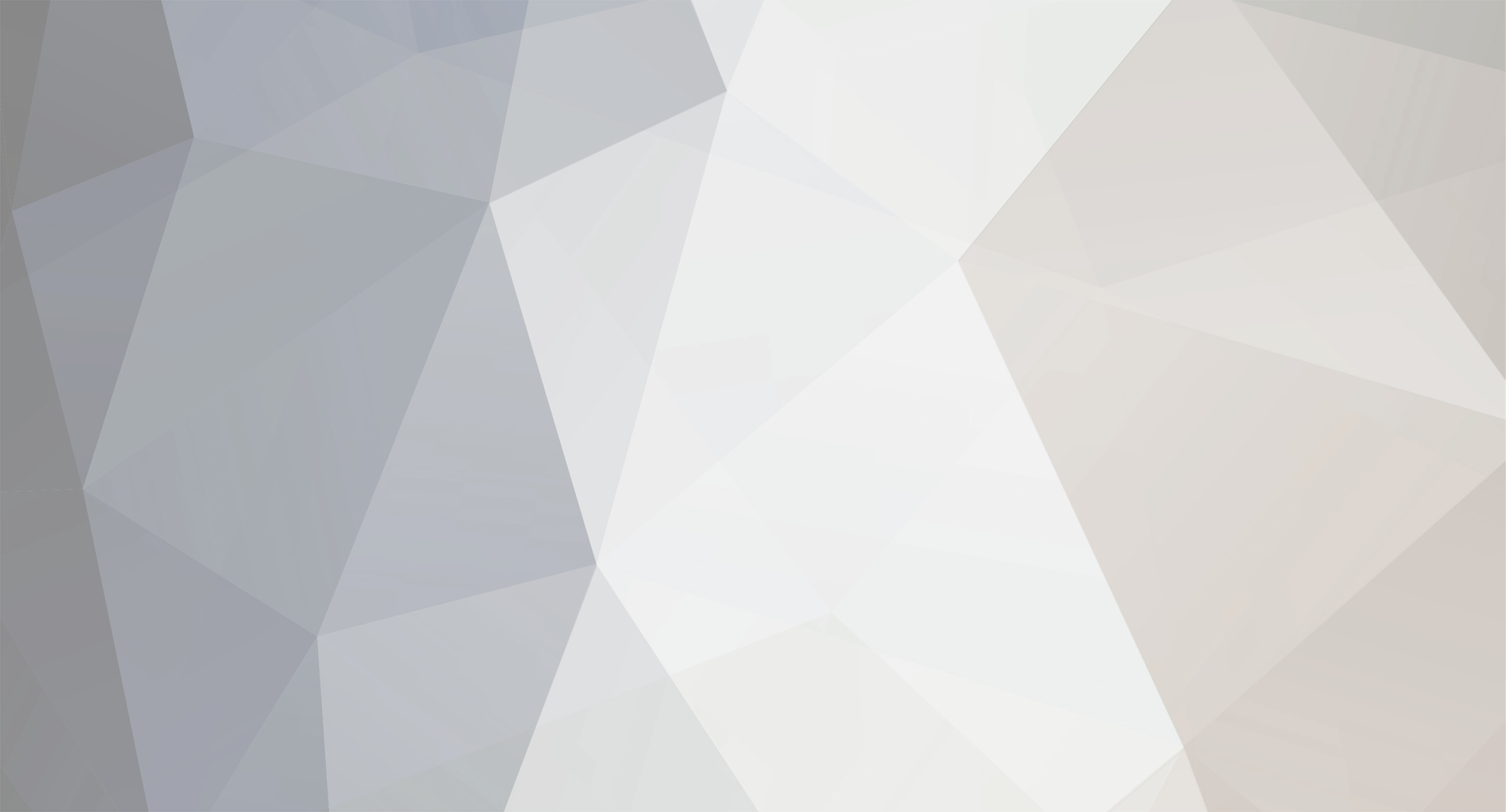
Mikenotts
Members-
Posts
12 -
Joined
-
Last visited
Recent Profile Visitors
The recent visitors block is disabled and is not being shown to other users.
Mikenotts's Achievements
12
Reputation
-
Westland whirlwind (Cloud models kit) build blog
Mikenotts replied to Mikenotts's topic in Build Blogs and Kit Reviews
Hi Andrew, Not flown yet. Our field is still too wet and the mower man says he will sink in and leave ruts! I will let you know when and if it survives maiden flight. The Westland Whirlwind I have built is quite modified , this kit after all is sold as a PSS unit i.e slope soarer. Mine has rudder, stearable tail wheel, and retracts. Also because there is quite a lot of weight forward it allowed me to put a servo directly in tail assy for elevator, instead of the S snake arrangement. Rgards Mike -
Westland whirlwind (Cloud models kit) build blog
Mikenotts replied to Mikenotts's topic in Build Blogs and Kit Reviews
Fitted ubec power supply, cut both red wires to ESC's so there is no voltage conflict. Its very tight in front end, but it all fits in. Final assembly. Total weight and that includes a 4000mah 3s lipo for motors and a 500mah 2s lipo for ubec, power to servos and receiver, 1.760kgrams. (1760grams). Center of Gravity 58mm from leading edge, which should be ok with the mods to tailplane. Took some photos, but these were indoors as its still raining. Will have to wait for grass at our runway to be cut, oh for it to stop raining before I can maiden it. But retracrs work and does rudder and tailwheel steering......roll on spring. -
Westland whirlwind (Cloud models kit) build blog
Mikenotts replied to Mikenotts's topic in Build Blogs and Kit Reviews
Whilst waiting for UBEC to arrive ran numbers through a CofG calculater , wanted to know what effect my increasing tailplane area would give. To give a more scale view of tailplane glued a 4mm strip to tailplane and 9mm to elevators to give a shape as shown in attatched scale drawing. Figures for original tailplane give CogG 55 mm from leading edge. With the increase to overall width by 13 mm gives a CofG from leading edge of 58.5mm. This is good news, it gives me a lot more flexibility on where to put UBEC. -
Westland whirlwind (Cloud models kit) build blog
Mikenotts replied to Mikenotts's topic in Build Blogs and Kit Reviews
Slight setback, whilst setting up rudder and elevator noticed light on receiver flickering when operating servos, traced to onboard receiver BEC , it's linear and not up to job. Was going to fit a seperate UBEC as I did on Lancaster, but didn't have one handy so went with esc bec, mistake, one on order but where to put it , going to add extra weight in wrong place, just when I had CofG just right with minimum extra lead. Well cannot be helped, will see how it affects balance when it arrives. -
Westland whirlwind (Cloud models kit) build blog
Mikenotts replied to Mikenotts's topic in Build Blogs and Kit Reviews
Okay other U/C leg arrived, fitted complete wing to fuselage. There appears to be enough weight in wing assemby to allow a certain amount of freedom with tail. So as room is very tight arround front of fuse decided to make load bearing part of tail support out of 1.5 mm balsa and fit a 9 gram mg elevator servo directly in tail, this makes things very simple and positive. Fitted another servo in fuse for combined rudder and tail wheel. To cut down on weight all non load bearing parts ie rudder, vertical tailplane front edge and tail top fabricated from foam. Checked balance and very little lead will be required, in fact we are just nose heavy, but lets see where we are after a base coat of paint.! -
Westland whirlwind (Cloud models kit) build blog
Mikenotts replied to Mikenotts's topic in Build Blogs and Kit Reviews
Started to assemble wing parts motors fitted, ESC's and clockwise and counter clockwise 3 blade 9x4.5 inch props. Glued plastic naceele covers together, decided to make them removeable, so back portion is glued to wing, front portion held with single screw. Only 1 spring undercarriage leg arrived so on hold till other arrives. -
Westland whirlwind (Cloud models kit) build blog
Mikenotts replied to Mikenotts's topic in Build Blogs and Kit Reviews
Next job glue wing tips to central section, as this epoxy takes so long to go off it will need mechanical support to align and locate wing tips and an elastic bungee cord to hold everything together whilst it sets. Fitted a couple of pieces of carbon fibre tube into wings, made a template to give a 3 degree angle, drilled central section at 3 degrees to top of wing and wing tip parallel to top, this will, if my calcs are right give 35mm af dihedral at wing tip. Glued 1 CA tube in 1 half and 1 in other . When dry test assembled to check dimensions, all okay so glued together. -
Westland whirlwind (Cloud models kit) build blog
Mikenotts replied to Mikenotts's topic in Build Blogs and Kit Reviews
Got a couple of 2836/07 1100kv motors that are slightly larger than the 4 I fitted to the TN lancaster, they should be okay. Got both 30 amp and 40 amp ESC 's in my bit box will go with 40 for time being. The retracts are from foamy spit/P40. The nacelle crutch to support this hardware will be based on lancaster pattern, still got drawing of those to copy from. Main decision is where to put ESC's, best place is in nacelle which has decent airflow, but that means lengthening power cables. Whilst on Lancaster I fitted 470mf 25v capacitors next to each ESC, to cancel out spikes which can cause premature failure, these were quite long extensions. If can keep power extension to under 150mm on 3s (12v) it will be okay but if need to go to 4s will need these capacitors. Built wing generally as described marked out where nacelles will go, but only glued 3mm infill to slot between outer edge and nacelle and in center section. This will leave a open bit between nacelle and center to allow all these extra cables to be managed. Contructed nacelle crutches and glued directly onto wing, trial fitted motors, and retracts and fitted ESC power cables in cut slot as described in instructions. Used XT30 power connectors they will be okay with calcullated load, and there is not enough room for XT60's without lengtening cables. -
Westland whirlwind (Cloud models kit) build blog
Mikenotts replied to Mikenotts's topic in Build Blogs and Kit Reviews
Hi Geoff, Not tried that particular epoxy, having built mainly from wood have tried to avoid epoxy in past, due to it being heavy and other cheaper options work better with balsa/ply. When I did use it on some foamy planes it was the stuff from HobbyKing typically 5 min, but cannot get that now and with all other sources drying up its left to by on internet. The stuff I bought from ebay was 5 min and worked on a foamy I had, but not this foam. I think the issue may be time some 5 min epoxy generates heat as part of curing, and that can melt some types of foam. The glue I got for £1.50 takes forever to go off but no heat. As I had not worked with this particular foam before tried to find cheapest option that works, other epoxies will no doubt do job but cost more, oh and this stuff does not smell. Regards Mike -
Westland whirlwind (Cloud models kit) build blog
Mikenotts replied to Mikenotts's topic in Build Blogs and Kit Reviews
Been a good day today 10 degrees,warm enough to work in unheated garage. Built the fuselage as described in instructions. Scaled instruction picture of fuse to give position for spacers, added fin assy and promptly broke it bring clumsy so rebuilt it and added balsa sheet to give it mechanical support while I work on fuse. Cut away last part of top deck moulding making it easier to fit. Offered up top deck moulding. But very difficult to work out where to cut it as it keeps moving. Cut some foam supports from scrap foam and glued these to top of spacers and former, rubbed them to shape to support moulding, now have contact at front, rear and above spacers and former, moulding nolonger moving, so drew line with straight edge and cut to just fit. Top deck held in place at moment with rubber bands. Next will be wing, I am working towards being able to rough assemble everthing to see if balance is going to be an issue. -
Westland whirlwind (Cloud models kit) build blog
Mikenotts replied to Mikenotts's topic in Build Blogs and Kit Reviews
Cliff, Thanks for update, I am hoping that the combined weight of motor, ESC and retracts in front of 55mm balance point will allow me to get CogG without extra weigh in nose. There is one question though, in the absence of a drawing, and going by specs for full size plane, wing appears to be at 1 degree incidence so I will be making tailplane 0 degree to maintain said decalage (longitudinal incidence). Going to use a straight edge to get tailplane parallel to top of fuse sides. How did you set yours up?. All my previous builds have been traditional ply and balsa, TN hurricane, spitfire,lancaster to name a few, never used veneered foam before, so the is a big learning curve for me. The first thing I did before starting was to experiment with different glues, zap a gap for balsa, ok . For balsa and foam PVA but not on highly stressed parts, now comes the tricky bit glueing foam to join wings etc, tried most things, hot glue, the 5 minute epoxy, super glue ALL melted foam. Was about to shell out on foam safe epoxy,.....but... Its very expensive. In desperation tried some epoxy from a £1 store (okay it cost £1.50 ) and this stuff works great, it takes 30 mins to start to go off, needs to be left in warm place to cure but sets rock solid and very strong, picture to follow. Thanks Mike -
Mikenotts started following Westland whirlwind (Cloud models kit) build blog
-
This will be my 1st build blog. As I could find no other builds for this model it will have to follow the line of flexibility. Also having no natural slopes and had enough of catapult launches, it will have retractable landing gear and rudder with stearable tail wheel. These mods are going to add weight in wrong place so I will start by assembly of basic fuse then wing to find out how many liberties I can take with said undercarriage and tail assy. In addition I have boxes of parts from previous planes, retracts for example, I have 3 working sets of retracts for planes up to 2kg that will be used. Looking to finish with AUW of 1.6 kg. First decision which battery, well I have 3 cell, 2200mah, 4000mah and 4 cell 2200, 300, 3300,4000.....need to make model able to accept any of these, as which to use will be governed by trying to achieve CofG without adding weight to nose. First job mod battery box to accept any of above batteries. Glued in 3 mm and 4 mm strips to give battery box internal dimension 52mm wide 28mm high. The 2 battery box support formers will need careful modification to accept these mods