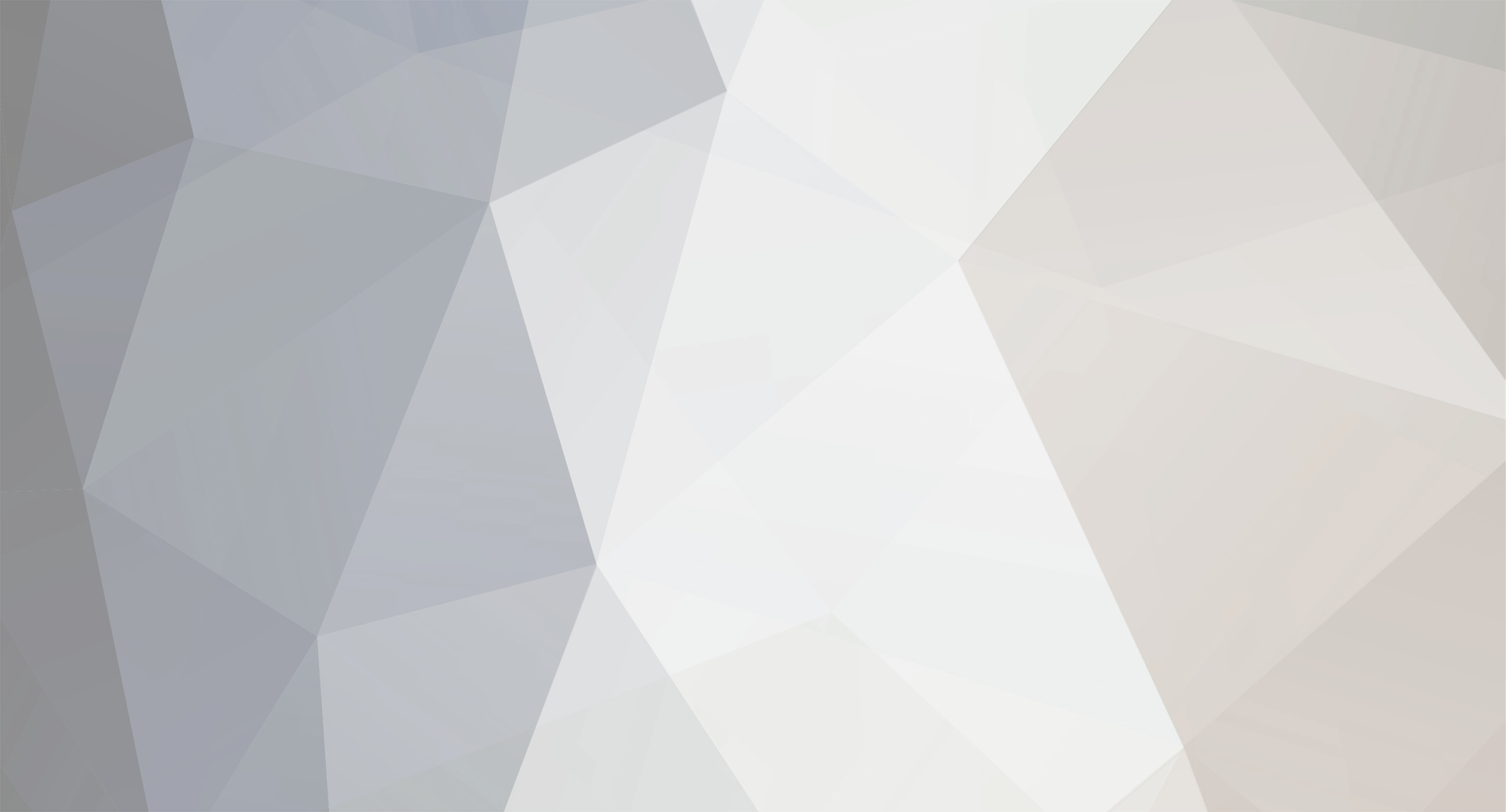
ROY DAVIES
Members-
Posts
12 -
Joined
-
Last visited
Never
ROY DAVIES's Achievements
0
Reputation
-
ROY DAVIES joined the community
-
It's got to be mine this month - Who mentioned birthdays I've got to win this time as I'm fast running out of birthdays !!
-
The July Grand Prize Draw
ROY DAVIES replied to David Ashby - Moderator's topic in All Things Model Flying
As Elvis said, "Please let it be me" -
The July Grand Prize Draw
ROY DAVIES replied to David Ashby - Moderator's topic in All Things Model Flying
I had the correct engine combo for the last one and I have for this one too. So in we go !!! -
The June Grand Prize Draw
ROY DAVIES replied to David Ashby - Moderator's topic in All Things Model Flying
Here I go again. In for nowt with a chance of something - DID I SAY SOMETHING - What a cracker of a prize. Best of luck everybody especialy me -
The June Grand Prize Draw
ROY DAVIES replied to David Ashby - Moderator's topic in All Things Model Flying
I didn't win the last one but my spare gear is ready to fit the Fury. Thank you David for choosing one of my favourite aircraft to have a go at winning. I wish me all the luck in the world. -
It has to be me as YELLOW is my favourite colour and I have a desperate need to win something as I missed out on the lottery this week!! So There.
-
The April Grand Prize Draw
ROY DAVIES replied to David Ashby - Moderator's topic in All Things Model Flying
When I win this Cub I hope it won't be such a lump as the last one I had. I wish you, and me of course - The best of luck. Engine and servos are waiting The sky in Wales is Cub friendly ! -
Silver Soldering
ROY DAVIES replied to Allan Jordan's topic in Building from Traditional Kits and Plans
Thank you for that reply, I can follow a lot of what you mean in my own simplistic way.You mention the crystaline structure in fractures etc. When I was a boy I worked at the local steelworks in the slab yard. The slabs were anything from 6" to 12" thick up to 13' long and sometimes were 4 or so feet wide of differing grades fit for their purpose. The yard was where the stocks were sorted and repairs to blemishes made before re- rolling. The case in point. We rolled a grade called COR - TEN this was for the sheet 'iron' core of transformers, immediately it was rolled and in the yard, they would roll about !00 tons of 'Trostre' grade { for the car indusrtry } as it was called this was to muffle the Cor -ten to keep it better than 'black hot' all the time it was in the yard. The 'Trostre' was changed at regular intervals as its temp' went down. All had to be perfect, if there was a hiccup in the rolling and storage there was a serious problem. When there was a slowdown in the system the cranes would up lift Cor - Ten that was by then down to black hot and often it would snap in half all 30 tons of it and fall to the floor. Now that was crystalization. As an aside as most of this post is. It was always easy to warm one's tin of beans or Fray Bentos pie on a black hot slab, 3 min's I remember, the crane drivers would as a prank lower a full load of glowing slabs within an inch of your tin and carbonise your food. It was after this job I went to fix planes for HMQ's airline . -
Silver Soldering
ROY DAVIES replied to Allan Jordan's topic in Building from Traditional Kits and Plans
Erflog re piano wire,Can you explain this. Long ago our wire was tinned in some kits and consequently was easy to solder, I also remember wire breaking when it was bent, the breaks were often like dowel snapping leaving sharp striations. You could see the grain as you mentioned in your post. I know I had a few nasty cuts this way. the wire did not have to be bent to a sharp radius for this to occur. Was this due to some chemical reaction with the tin coating ? I know we have had a problem at work with high tensile screws with the heads coming off due to Hydrogen embritlement after the passivation process - electro zinc plating. -
Silver Soldering
ROY DAVIES replied to Allan Jordan's topic in Building from Traditional Kits and Plans
Nice one Eric I fell for that. Actually I need to correct the name. It is Fry's Powerflow, obtainable in three sizes. starts at around £4 for the smallest.Now if that was chocolate I could do with some right now as its benefits are sorely needed. A lot of you are reminiscing about your youth so here's is my three P's worth. In the '50s I was given the EAGLE BOOK of BALSA MODELS I plowed through a few and needed a moddel to use my Jetex 50 on, I decided to make the ROCKET. It would slide along a wire on paper hooks for many hundred yards (It did) so the blurb said. So- I had a coil of pin making wire hundreds of yards of it, I stretched it across the valley where I live ( Wales) so we have few, 250 yards or so. I crossed via a bridge. A friend and I tied it off on railings and we were in business. It worked perfectly ran out of fuel so time to wrap up.--- Unfortunately--- The wire snapped! and fell across power cables and put out half the village! And believe it or not nobody knew who did it, they were completely in the dark!!! I used to make 'cannons' from pram tubing and the powder from Mighty Atom bangers. Flatten the tube one end stuff a ball bearing in a rag and use a resistance wire fuse and fire at telegraph poles, they used to boom and the wires would sing. It was quite good. All down to Errol Flynn and too many pirate films I think. Then I nearly grew up and went to fix 'planes for the Queen just like Peter Miller. Talking of flattening tube. If you can't get your head around silver soldering use tube sleeves and soft solder, there are various sizes of Microbore copper tube ask a plumber for some off cuts. Anneal it, = heat it up and quench it and there you are, brass tube will do the same but they both work harden so if it's a tricky job you may have to do it again -
Silver Soldering
ROY DAVIES replied to Allan Jordan's topic in Building from Traditional Kits and Plans
Yes Eric you are correct. The new legislation means that no equipment made from the implementation date is allowed to use lead based solder, and as you say it is still readily available even from the big boys, e,g, Farnell, R,S. and others. Peter has mentioned Bakers fuid, if any of you buy some to use don't get it under your nails or in even a small cut, or it will make you dance some! I have not used it myself for years. A more user friendly flux is LA-CO' Comes in a back plastic pot in a small and large size. The other even better product is, Fry's Easyflow ? in a yellow pot. Both are available, in plumbers supply centres. The Fry's flux is that good you do not have to clean copper or brass tube first , dip it in and apply heat and it cleans before your eyes, But I do clean piano wire. The fumes produced by these products are all nasty so use in a well ventilated space. -
Silver Soldering
ROY DAVIES replied to Allan Jordan's topic in Building from Traditional Kits and Plans
Hello Peter A few more tips on silver soldering. Don't use more than is necessary. I cut a piece that is quite small but hopefully enough for the job, a matchhead size piece is more than big enough to join two U/C wires together. Use a decent side cutter and watch the bit doesn't fly as it's quite hard.How to get it on to the job? I use powder flux, put a few spots of water on a tin lid ( preffered ) and mix to a stiff cream/paste. If you're only making a minute amount spittle works equally well. Warm/Heat the joint and apply a little of the paste and it should coat it. Using a piece of thin wire with a tiny amount of flux paste on it pick up your piece of solder. Heat the joint untill the flux melts and apply the solder and wait untill it flows then take the flame away.This method prevents too much heat at the joint, and you are not heating up the solder stick as most of the time it can be bigger than the job which means you overheat the wire getting it up to temp' together with too much solder and an ugly joint. When the joint has cooled pour boiling water over it to clean off the flux, if the flux is left it goes hard and it will be as hard as glass and just as sharp when you chip it off. BE AWARE MOST SIVER SOLDER FLUXES ARE POISONESS so no biting your fingernails. Re, soft solder. Lead solder is now banned and tin alloys will replace them an exception where I work is that Defence equipment is exempt and it can be used for repair work on in service equipment. Keep your eyes open for cheap solder stations as the new ones required for the new regs' operate at a much higher temparature range and aresuper exspensive - 100s of £