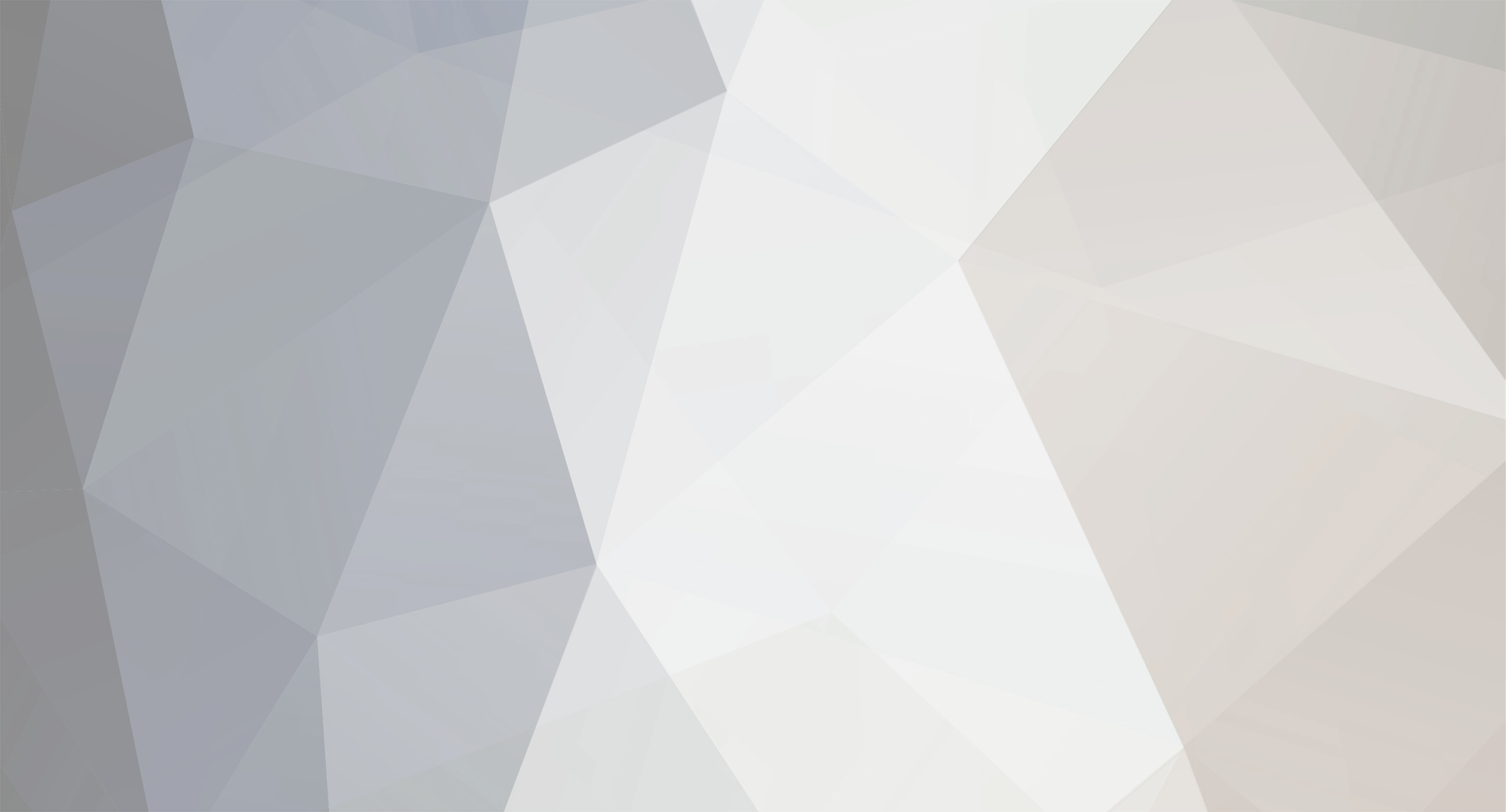
Wasaforumite
Members-
Posts
165 -
Joined
-
Last visited
Content Type
Profiles
Forums
Blogs
Gallery
Calendar
Downloads
Everything posted by Wasaforumite
-
Tweedy Bird (Small Dirty Bird)
Wasaforumite replied to Wasaforumite's topic in Classic Aerobat Build Blogs
After a few days some more progress. I seem to get to stages in construction when the 'chicken and egg' problem arises. Here it's the case that the wing can't be finished until it's been fitted to the fuselage and fitting to the fuselage is difficult because the wing isn't finished, if you follow me. Also there are steps that are critical to the performance of the plane like the alignment of the wings that are best done slowly. Anyway these are my excuses for apparently not getting on! The procedure for mounting the wing is outlined in the original kit instructions for the full size Dirty Birdy. With the fuselage upside down, the wing was first roughly fitted by sanding the saddle. The wing bolt is then fitted and the alignment checked many times with more adjustments to the saddle. The measurement from the wing tip to the tail was equalised using a steel rule. More adjustments were made to the saddle. The position of the wing dowels was then marked through the holes in the former in front of the wing and the wing leading edge was drilled to accept the dowels.The inner ends of dowels are anchored by holes in lite ply spar webbing . I predrilled the webs and made them slightly undersize so I could adjust the position of the dowels. I wanted the dowels to position the wing without any unnecessary stress, so after positioning the wing the webs were just glued with epoxy where they ended up. I haven't at this stage glued the dowels in place as I want to put a fibreglass band around the wing joining area and it will be much easier without them being in the way. (chicken and egg again). I hope this explanation is clearer from the picture. Having mounted the wing, I can now get on with installing the servos and remaining sheeting. -
Tweedy Bird (Small Dirty Bird)
Wasaforumite replied to Wasaforumite's topic in Classic Aerobat Build Blogs
I've loaded another photo. The fuselage is nearly finished and the wings have now been joined, althought the join still needs glassing. I have been trying to source a canopy but neither Sarik or Vortex have one suitable. I've started work on making one using blue foam which I will cover with fibreglass cloth. This will be new to me so I'm keeping my fingers crossed. I was really scratching my head about how to get a template for the teardrop shape, particularly the overhead view. It finally dawned on me that the wing aerofoil shape was as good as any - staring at me from the plan! I just scaled it up by 12% in my printer and then widened it by about 1mm on each side. The side view is shown on the plan and that's enough to get me going. I have been quite taken by the logic of this design and how it evolved through Kaos, Super Kaos, Dirty Birdy and UFO. As I mentioned earlier I was toying with idea of the Kosmo 3 for my next project but I have come to the conclusion that it will be too fast for me. I've now got a pdf plan for the Super Kaos which might be a bit more suitable. It will mean that I'll have to get my hands dirty with glow fuel and I'll be the butt of a million remarks at my Club, where I'm known as a staunch leccy flyer. I'll have to go in disguise. The image is upside down. It isn't on my computer! -
Tweedy Bird (Small Dirty Bird)
Wasaforumite replied to Wasaforumite's topic in Classic Aerobat Build Blogs
I went into Al's at Wolverton today to pick up the trailing edge stock. I was amazed to see that there was old kit for sale for the Birdie Ten! This is picture above see leccy flyer's post. There was no price on it but it's worth a call if you are interested. It's at the back of the shop on the left at knee level in case you want to help the assistant find it. -
Tweedy Bird (Small Dirty Bird)
Wasaforumite replied to Wasaforumite's topic in Classic Aerobat Build Blogs
Jim - I notice you are going to use an Enya 10 SS BB in yours. Should be a terrific performer - the ballbearing Enyas are superb engines. -
Tweedy Bird (Small Dirty Bird)
Wasaforumite replied to Wasaforumite's topic in Classic Aerobat Build Blogs
Thanks to you all for suggestions re the trailing edge stock. Before pressing the 'buy' button at balsa cabin i thought I'd give Al's hobbies a ring and it turns out they have this stock after all. I won't be able to get there until later this week. I've made more progress with the wings. I'm fretting the tips out of 1/2 inch balsa sheet and there's still a lot of capstrips to do. As with the Birdie Ten trailing edge pictured above, I've sheeted the it with a half inch strip. I think the trivial weight penalty is worth it for the extra strength. I'll post some pictures tomorrow. As soon as the wings are finished they will have to be joined together. Slightly off topic, I was reminded by the picture of the ic Birdie Ten that once I got used to flying this machine, it might be interesting to compare it with one powered by a 25. However, it's pretty boring to build two planes the same in succession. I looked at the Mantua kit for the Mini Kosmo, which is much the same size but I was rather put off by comments on Italian forums that said it was heavy and flew like a missile. The full size Kosmo 3 looks a beauty and I am surprised there hasn't been any mention of it in the group. Edited By Wasaforumite on 01/03/2016 23:15:53 -
Tweedy Bird (Small Dirty Bird)
Wasaforumite replied to Wasaforumite's topic in Classic Aerobat Build Blogs
Here's a view of the rear of the fuselage. I'm using DuBro snakes. The rudder and front wheel are operated by a Hitech HS225-MG and the elevator by an HS81MG. The rear of the fuselage will be covered by 1/8 balsa sheeting with the grain running lengthways. The plan calls for 1/16 sideways. I'm hoping that the cross pieces and formers will overcome any weakness in the grain orientation. I really don't get on trying to get a good finish when sanding acroos the grain. There's a lot of sanding and shaping to be done yet. Now onto the wing. I cut out all the ribs only to waste 4 of the 20 by deciding to up the thickness of the two ribs in each wing that carry the undercarriage. Mr Bridi obviously never saw our strip or my landings when he designed the wing! I also cut out some heftier reinforcements that carry the load right into the wing spars. There isn't much else to report at the moment. One problem looms - the plan calls for 3/8 by 1 inch ailerons and they are solid wood. There's no way I can cut or plane such sections accurately and this size doesn't exist in any of the shops I can get to. I couldn't find smaller t/e stock that I could laminate either. Looks as if I'm going to have fabricate them which will be time consuming. -
Tweedy Bird (Small Dirty Bird)
Wasaforumite replied to Wasaforumite's topic in Classic Aerobat Build Blogs
I'll just catch up this evening on responding to those forum members who have taken the trouble to contribute to this thread. Robin: As you say the longer u/c will be useful for the bigger prop required by the electric motor. I'm going to use 4s to keep the prop size as small as possible. The hatch will be on the underside in front of the wing. Not the most convenient place but I would like to keep the top 'plank' in one piece for strength. Jim; Your comment came too late, sorry - I'd started the build a couple of weeks before deciding to run this blog. You are quite right - build the fuz on the underside of the top 'plank' and get a straight fuselage. Later, I found an article on building the full size DB and it explains it. Set up the formers on the plank and glue them into position. I'm not experienced in building foam wings (only repairing them!). They are a time save and are pretty strong. I'm trying to build light, helped by modern servos etc. so I don't end up with a missile. My reactions are going to be tested by this plane for sure. Max; I hope you can revive your DB. Good Irvine 40's might be expensive to find though, if you haven't kept yours. I'm well on the way to finishing the right wing and i've discovered how to print out mirror images on my Epson Workforce printer so the left wing should be started this weekend. I'll post a few more pictures tomorrow. Edited By Wasaforumite on 24/02/2016 20:44:25 -
Tweedy Bird (Small Dirty Bird)
Wasaforumite replied to Wasaforumite's topic in Classic Aerobat Build Blogs
The fuselage consists of four box sides but they are all joined at the 'seam' by tri stock. Ttri stock is really quite expensive but I haven't found an easy way of making it. The commercial stuff is quite hard which is good for this purpose. The fuselage corners are planed/sanded to make a rounded section. One problem I found was that the front undercarriage mount screws more or less have to coincide with the motor mount. As the motor has to stand off the front bulkhead I made a sandwich of ply. The motor is attached to the first layer, the second layer is a filler and the final layer is the bulkhead itself with the u/c mounted on the back not the front as shown on the plan. -
Tweedy Bird (Small Dirty Bird)
Wasaforumite replied to Wasaforumite's topic in Classic Aerobat Build Blogs
Many thanks for the constructive replies received so far. I've got a few photos of the construction which I'll post below. Jim your point about how the fuz is built is very relevant. I initially thought I would use my SLEC jig in the usual way but found on the net that the Dirty Bird fuselage is built over its own top 'plank'. So I unpicked what I had already done and started again. I dislike liteply, especially for formers, as it always seem to warp as soon as it is cut so the front two formers are 1/8 birch ply and the next two are laminated 1/8 balsa with the corner joints overlapped. I did end up using the Slec jig to help hold the curves. The position of the slot for the tail plane was marked but not cut as at this stage the fuz still has a flat top and it’s easy to mark out. Apart from substituting 1/8 for 1/4 ply and not using lite ply these are the only changes so far. The first picture shows the fuselage that was scrapped. The second shows it reassembled in the correct way. -
Tweedy Bird (Small Dirty Bird)
Wasaforumite replied to Wasaforumite's topic in Classic Aerobat Build Blogs
**LINK** (hope I'm allowed to show links to pictures on web) There aren't many images of the Tweedy bird on the net. Here's one I found. The Dirty Bird heritage is pretty obvious. Looking over the plans I was pleased to find that the undercarriage is almost the same as that of my E Flite Advance 25 and to save a lot of work I found a 'spares' kit in my local model shop. This had the three legs, mounting hardware and some collets. The legs are about 2 cm longer but with our bumpy strip it will help save a prop. I'll post pictures tomorrow of work on the fuselage. -
I enjoy flying planes that I can fit in the boot of my car, the E Flite Advance 25 being a favourite. About half my planes are self build and I was looking for something possibly with a bit more speed and came accross the plans for the Great Planes Tweedy Bird. This is a 49 inch span version of the Joe Bridi Dirty Bird for .19 size ic. It seems ideal for conversion to electric (sorry!). I have a JP Enrgy C3520/10 1100kv motor and on 4s it should be a good match for plane that will hopefully weigh around 3-3.5lbs. The Great Planes plan shows enough detail for the build except that only the root rib is shown. I am indebted to David (posts as Doxilia on various web forae) for sending me a couple of pdf's of the ribs. He has produced laser kits of various F3A planes. Unfortunately, as he is located in Montreal, the cost of bringing these over to UK would be prohibitive. I will be using a Mk26 Swann Morton laser aided by an Epson printer that does produce good plans at 100%. Hopefully, some members of the this forum will be interested although of course I realise the size and the fact that its electric will put quite a few off! Over the next few days I'll put up some pictures of progress. Edited By Wasaforumite on 22/02/2016 20:47:28 Edited By Wasaforumite on 22/02/2016 20:48:42
-
Martyn, many thanks for posting this article. The explanation of the method of building the wing is is the best I've seen. I suppose that rather than using 1 inch deep pieces of thick (and these days expensive) balsa one could, at least with the leading edge, have a false leading edge of hard 1/8 balsa and then attach a strip of 3/8 balsa leading edge much narrower than 1 inch to complete once the wing is all glued up. I'm about to start building a Tweedy Bird, a smaller version of the Dirty Bird and the plans look very similar. The construction notes for the Diamond will certainly be a help. The TB is for 400 watt electric power. I've had a lot of help from David Oxilia in Montreal in sorting out plans and ribs etc.
-
Hi Everyone I would like to thank those who have given advice following my earlier post. The plane I am about to cover is a Mercury Aeronca. In the article by the late Dave Deadman, he mentioned good results can be obtained using a sable brush and thin coats, although over Modelspan and mylar covering. I'm afraid I just wouldn't have the patience to do cover a plane twice! I am going to see how this works with Solarlac over Solartex. The original planes seem to be gloss finished over either fabric or alloy.My plane will be covered firstly in 'linen' colour 'tex as that will easy to hide using paint (hopefully). Ian
-
Ben I think you are being too kind to BM and Ripmax here. I purchased the product by going to the product from the left hand side list and this is what you see: Flexible Snake, 36 inch (SN503) £7.10 This Package Contains Two of Flexible 36" Nylon Gold-N-Rod Push Rod Systems from Sullivan. FEATURES: Used to connect servo arms in the model to the model's control surfaces. Made to tight tolerances to ensure smooth operation with minimum friction. Comes complete with Gold-N-Clevises and other installation hardware. Nylon push rods made from a special compound to reduce thermal expansion and prevent radio interference. Light, strong, and flexible. The yellow inner rod spline construction reduces friction and binding. Each brass plated Gold-N-Clevis is constructed of tempered steel with an interlocking collar, welded pin, and an exclusive steel retaining clip to prevent accidental opening. This has a red sheath and a minimum bending radius of 2-1/2" making it good on small to medium aircraft or lightweight, medium strength applications. PACK INCLUDES: 2 Push Rod Systems SPECIFICATION: Length: 36" Minimium Radius: 2-1/2" (64mm) Colour: Red & Yellow Thread Size: 2-56 Note that this is called a 'system'. Now when I buy a 'system' I don't expected to have to buy other parts especially if they aren't mentioned. If Sullivan say to use the nuts in their instructions they should have it in their adverts as well. Ripmax/BM's reaction to the shortcoming wasn't what I would expect from companies that have good customer service as a core value. I wasn't aware that Ripmax imported this stuff until after the purchase but they should ensure that they and their retailers accurately describe their products and provide proper support and after sales service. I have now ordered some nuts from Modelfixings.