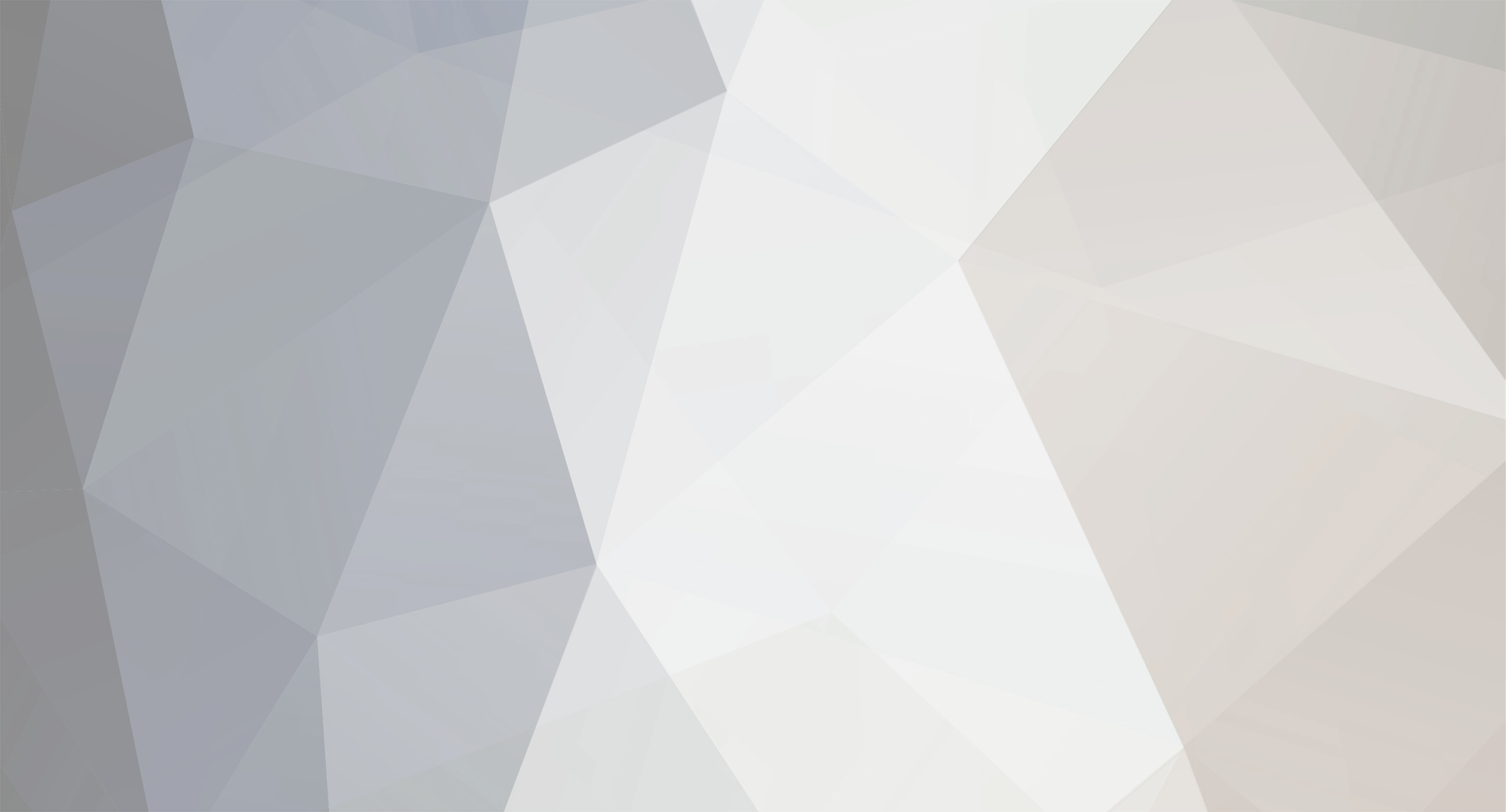
thomas oliver 1
Members-
Posts
119 -
Joined
-
Last visited
Never
Content Type
Profiles
Forums
Blogs
Gallery
Calendar
Downloads
Everything posted by thomas oliver 1
-
M3 threaded linkages HOW TO
thomas oliver 1 replied to Steven Butler's topic in Model Engineering and Accessories
I have used cycle spokes in the past, instead of piano wire. These can be obtained in 16swg ( 1/16th in)< 14swg, 12swg, and 10swg( 1/8th in). Spoke material is especially formulated for thread rolling and is tougher and stronger than mild steel and can be bent easily without fracture. It cuts nicely with dies without blunting them. Another source is the use of the wire, which is similar to spokes. TUO -
Rolls Royce were quite aware of the problem of the carburettor on spitfires. I worked on a small flight at Millfield in Northumberland in 1944, as I mentioned in my previous post, and the aircraft were Spitfire MKVs, fitted with fuel injection and we worked in cooperation with several Rolls Royce civilian engineers on these aircraft. The significant thing is that they also used 150 octane fuel instead of the usual 100 octane. These Spitfires had noticeable better performance. The fuel was heavily doped and after a few flights the sides of the fuselage got thickly covered in brown deposit which we had to regularly remove. I have never seen any evidence since that these engines were ever used in anger.
-
Try Fairy Power Spray. It is not too viciuous and does a good job. Tomol
-
As one who worked on Spitfires of all Marks at Eshott and Millfield in Northumberland during 1944, I can say that regardless of who manufactured the Merlins or where, they were a pretty reliable engine, and I only ever saw one with the pistons hanging out of the crankcase. They were not very easy to work on in the tight airframe, and the vertical starter motor had about three very inaccessible securing nuts. Maintenance sections had a full chest of special Rolls Royce tools. On the flights, we had lousy thick and clumsy Whitworth spanners and had to make our own special spanners of which quite few were required. ( In contrast, all the American aircraft I worked on overseas came with a full case of beautiful open/ring spanners and ratchet and socket sets, which we never even heard of or seen in England. Although,as I have stated the Merlin was pretty reliable,, it did not compare with the Pratt and Whitney Twin Wasps, as fitted to the Liberators I worked on. On my squadron, we sent 12 aircraft out on ops. every other day and over two years they all came back on four engines These ops. were from Bengal, over the Indian ocean, to Burma and Malaya and some as far as Vietnam, taking over fourteen hours or so in the air. At the end of this period a letter from Group Headquarters was posted on our notice board stating " Never in the annals of the RAF has a squadron achieved such serviceability as this Squadron (159) over such a period." This was not due to our servicing but to the utter reliablity of the engine, I have to admit. Of course, another factor in aircraft engine reliability is that aero engines are pretty low revving and only do around 2000rpm when cruising. Hope this throws some light on the topic. Tomol
-
DC Sabre prop nut is decidedly not as big as 0BA which, as stated, is 6mm diameter. It is 2BA which is 0.187 ins. in diameter. The nearest metric size is 5mm which in fact has the same pitch as 2BA but would be too slack. A nearer fit is No. 10 UNF which again has an almost identical pitch, but at 0.190 ins in diameter would be slightly slack, but might do the trick. tomol
-
Any advice for a Myford ML7 newbie?
thomas oliver 1 replied to Danny Fenton's topic in Model Engineering and Accessories
Danny, Sorry about the text c--up at the end of post. You will find good information on lathe work on the Yahoo Boxford site under "Files". There should be extracts from the Boxford handbook on tool angles which is very good as a guide. One method of obtaining a good finish which I use to good effect is to reduce the "Plan trail angle" by turning the toolpost. This is the clearance angle between the work and the cutting edge when looking vertically down. The larger this is the lousier the finish. The smaller it is, the better the finish. You see a lot of advocacy for using round nose tools for finish. This may be OK on large work, where a corner fillet is of little consequence, but for model work, sharp corners are usually the order of the day. When working on very small diameters, you will find that the metal springs away due to flexibility. I made myself a very small rotary tailstock centre many years ago and it is extremely useful for obviating this. They can now be obtained from RDG at reasonable cost I have used tools ground for mild steel on brass for donkeys years to good effect. They cut cleaner and give a better finish than the no back rake tools usually advocated. I have never found them to snatch. It also means you do not have to grind up two sets of tools. If you want to spend more time on the modelling as less on machining, then it is possible to save time with the right equipment. Tom -
Any advice for a Myford ML7 newbie?
thomas oliver 1 replied to Danny Fenton's topic in Model Engineering and Accessories
Danny, As you intend to try to produce things like retracts then you will need to produce both accuracy and a good finish on parts. You will find that normal mild steel or allow rod is one or two thousandths of an inch down on the nominal size. Silver steel which can be obtained in 13" lengths is accurately ground dead to size and will give good fits in reamed holes. Normal rod plus drilled holes will give lousy results and slop. You will need to investigate, as suggested, the proper top rake, side rake and front clearance angles for the metal you are using. There are lots of sources on the net for this. Alloy requires higher angles than mild steel. It also is prone to give a "built up edge" which destroys the finish. Use Paraffin or pure turps as a lubricant. If I was starting all over I would take the trouble to make an adjustable tool rest for the grinder. A diamond honing wheel of will improve cutting edges a lot and improve finish. You will find that if you have purchased a full set of number drills, 14 of these have no use whatsoever for tapping clearance or interfer is obliteratence fits. Signing off before this text is obliterated, Tom -
Any advice for a Myford ML7 newbie?
thomas oliver 1 replied to Danny Fenton's topic in Model Engineering and Accessories
Danny, Further to my first reply, Aluminium can be obtained as "Freecutting" alloy. Brass also as CZ121,and mild steel as EN1A. These make life a lot easier and produce a better finish. Start practising by making useful accessories such as a tailstock die-holder, a slitting saw arbor, boring bar holder, knurling tool shank, toolmakers clamps, morse taper centre drill holder. Make these with a knurled collar if possible to aid extraction. My number one requirement is a good accurate 3-jaw chuck, which makes it easier to achieve accuracy all round. Wood turning can be done as shown in one posting with nice sharp tools on a metal lathe. With a lot of practice you can even move both slides simultaneously to generate curves as in the spinner. Do however as advised and use a vacuum extractor if possible and scrupulously clean down after using wood. It does generate a lot of very fine dust as well as the normal cuttings so use a good mask as recommended. Most British hardwoods and fruit tree woods turn nicely. Beech is readily obtainable and oak from old chair and table. There are two distinct methods of hand woodturning - scraping and cutting. With scraping you hold the tool about level but this does not give good finish and relies on sandpaper to finish. The cutting method requires the tool handle to be tilted down. The bevel on the end of a skew chisel is allowed to rub, then the the tool slowly tilted back up until it begins to slice the wood and slowly moved along. There should only be one bevel sharpened on either side of the tool. Do not hone the edges only. -
Any advice for a Myford ML7 newbie?
thomas oliver 1 replied to Danny Fenton's topic in Model Engineering and Accessories
Danny, As a modeller and lathe user for over fifty years, I append some advise about lathe use: 1. Remember the golden rule is "Rigidity". Do not allow too much overhang of workpiece or tool. Always part off as close to the chuck as possible. 2. Cutting "rate" is dependent on diameter of work and rotational speed and is fixed for any given material. So small dia. work turned at high speed and larger dia. work at lower speed. 3. The material also comes into it. Aluminium needs a high speed, mild steel more or less medium, and cast iron low speed. So small dia. aluminium will need a very high speed. Large dia. cast iron very low speed. 4. Stick with HSS toolbits. They are much easier to regrind and to grind special form tools. Tungsten carbide only needed for cast iron or tougher steels 5. Do not be tempted to buy full sets of tools as you wll probably be getting some which will remain very redundant. Most work can be done with knife, round nose, chamfering and parting tools. 6. So called quick change tooling is not as quick as is made out. A four way toolpost is much quicker to index, if you can cope with the four tools mentioned. 7. Turning procedure:- Start with heavy roughing cuts and check regularly with mike. Get within 20 thou. of size. Then index in 5thou, taking off 10thou. Index 3 and take off another 6, leaving 4 thou. Then 2 cuts of 1thou to take down to size. 8. One of the big problems with old lathes is backlash in the cross-slide. Fitting a digital readout gets rid of this problem as it shows only the actual movement in or out of the crosslide. -
Steve, I cut inner piece out first to leave a the original large piece of material to hold onto when cutting out the gasket. If you cut out outer, depending on size of gsaket, you may have only a small circle to control and it may move or buckle. I have made many gaskets for small diesels successfully. Tom
-
To make either paper or alloy gaskets, I fixed a small sliver of scalpel blade in place of the lead in a draughtsmans compass. I set the inner radius accurately, place a piece of thin alloy ( I use the sealing caps off coffee jars etc) on a a piece of floor tile and spin the compass until the disc separates. Without moving the metal,(tape it down if necessary) I reset the compass to the outer radius and using the same centrenhole cut out the annular ring. i have made dozens of paper and alloy gaskets with this method. Tom.
-
Some years ago I was at the Woodvale Show and some guy sent up a small delta wing model which screamed around the sky at a terrific rate, doing vertical twinkle rolls. I was very impressed and when it landed I was close and could see that it had the Wankel engine fitted.
-
Diesels with sub piston induction will not throttle. I made a throttle for a Mills 1.3 and when I shut it nothing happened. I blanked off one exhaust port and it throttled beautifully. Interestingly, there was no apparent loss of power. It flew a 48" span radio model loaded with heavy home made radio gear ( servos had 21 transistors and boards were so big they were fastened externally on the casing). The Mills never stalled or skipped a beat in several years of use. I still have it and compression is still very good . Pickup was slower than gloplug however.
-
Contributors on other forums recommend Fairy Power Spray. I also find this very good. One Model Shop used to sell cans of engine cleaner which was some caustic liquid and it did work well but no longer available. I have also read that soaking in windscreen wash is effective, but haven't tried it as yet. Barbeque and oven cleaners work but tend to dull down the alloy surface. Do not leave cleaner on too long. I go along with Engine Doctor and start with heat, to get things moving, then oil, fuel etc. One point to watch is with r/c throttles. These also get badly seized up and you should not force them especially with plastic arms- these can break..
-
A good way to check that you have got the timing correct is to check that there is "overlap" at the end of the exhaust stroke and beginning of the induction stroke. To see this, turn the crank and watch the rockers. The inlet rocker will begin to open the inlet valve before the exhaust valve rocker has allowed the exhuast valve to fully close. Wiggle the crankshaft back and forth and the two rockers will rock together. This is to allow for the inertia ( reluctance to start moving) of the mixture and it ensures more complete filling of the cylinder and hence more power. The same sort of thing happens in the spark timing of a petrol engine -- the spark occurs before top dead centre to start the combustion early and allow the "flame front" to spread and get the expansion of the burning gas to begin as early as possible. You should be able to see the piston crown at the top of the stroke when this is happening by checking through the plughole.
-
Electric Flair Pupeteer
thomas oliver 1 replied to Danny Fenton's topic in Build Blogs and Kit Reviews
I once sprayed my Boxford Lathe with thinned down Hammerite and it did not display any hammered effect at all. I think because it dries too quickly. For what it is worth. -
Simon, Are you sure you havent got those ratios the wrong way round?
-
Cox Black Widow - Glow head availability?
thomas oliver 1 replied to John Falconer's topic in IC Engines
Sorry to disagree with some of the previous info. There is plenty of metal thickness in the head of the Cox. So much so that the head neads counter-boring to bring the plug through level with the inside of the head. Which of course means there will be no loss of compression. How do I know - I have just converted an old head - took about five minutes and looks OK to me. Modolit. -
Difference between two and four strokes
thomas oliver 1 replied to Craig Spence's topic in IC Engines
Craig, To answer the technical part of your question, this is how they work:- Four-stroke: 1. INDUCTION STROKE- Inlet valve beginning to open at top dead centre--Piston moves down cylinder and causes air to be sucked through carburettor, picking up fuel until valve closes just after bottom dead centre. 2. COMPRESSION STROKE -- Both valves are now closed--piston moves up cylinder compressing the mixture. 3. POWER STROKE-- Just before top dead centre, a spark occurrs igniting the mixture which burns and expands forcing the piston downwards- both valves still closed 4 . EXHAUST STOKE -- Exhaust valve now opens and upward moving piston pushes the burnt gases out of the valve. TWO-STROKE ENGINE:- Initially the piston moves up and suction in the crankcase fills it with fuel mixture, ase then the piston moves down compressing the mixture in the crankcase and forcing it up a transfer port into the cylinder. This might be called the priming phase. The two operative strokes now occurr-- 1. COMPRESSION -- the piston moves up compressing the mixture and at the top of the stroke the plug or spark plug ignites the mixture. 2. POWER- the expanding burning gas forces the piston down. The exhaust escapes through the exhaust port towards the bottom of this stroke. Note that while 1. is happening, a new charge is being drawn into the crankcase, and while 2. is happening, this charge is being compressed ready for transfer and a repeat of events This is a slight simplification of events. Tomol.