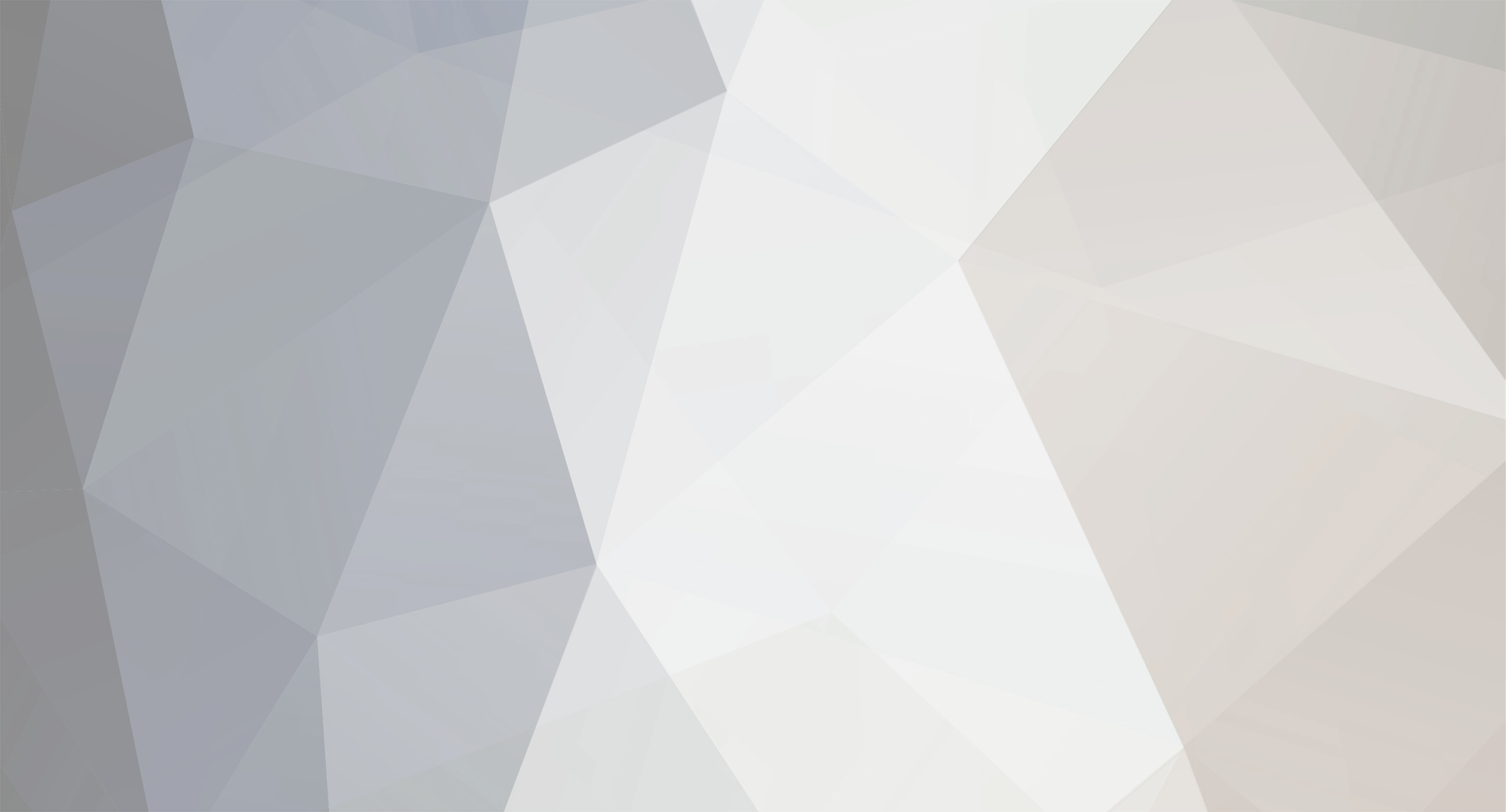
Artto Ilmanen
Members-
Posts
285 -
Joined
-
Last visited
Content Type
Profiles
Forums
Blogs
Gallery
Calendar
Downloads
Everything posted by Artto Ilmanen
-
Thanks, Jon. I just want to follow your instructions as rigurously as possible. 🙂 And as such, some modification, although pretty minor, is needed (lower the tank) to get the tank height as instructed by you. It's hard to know when and to what extent one can deviate from the official instructions. Thanks for the hint concerning the rx batteries. While I have never had any issues in the past when having them mounted inside the cowling, maybe I have just been lucky!
-
Thanks Ron, Yes, these models seem to be tail heavy easily. I try to avoid use of unnecessary ballast by mounting the rx batteries inside the cowling. We'll see. Anyways, I think I'll go for the side mount route with the 150. After second inspection I noticed that I don't need any more cut out of the wing at all as there is already some by the factory. What comes to the tank height vs carburetor I found a picture by Jon on the other thread so I believe it's clear now. The read line in the picture is "in the middle of the carb".
-
Thanks Ron. This makes sense. As a side note - have you been flying your Bearcat with the 240V? What are your experiences? I had been thinking of a 240V for my Focke but having spoken with Jon the 150 seems to be a better choice for the Focke
-
Thanks gents, I do not mind modifying the model if needed. The only thing I’m thinking is the wing - will it become weaker if I carve it 5-7mm to make room for the tank. If I Interprete Jon’s instructions right the second picture is how the tank should be in line with the carburetor?
-
Hi Jon & gents, I'm installing a Laser 150 on my ESM Focke Wulf If side mounted the top of the tank seems to be about 7-8 mm higher than the centre for the carb: see picture if no mods done If I understand your instructions correctly the top of the tank should be in line with the the spray bar? See the other picture Anyways, if I lower the tank as instructed I need to either find a tank which is not more than 50mm of height, which is the space available until the wing comes in way (the 12 fl oz Dubro in the picture is 57mm). Or I can modify the wing to have some more space for the tank. Anyways, the right size & shape tank might be the easiest solution. I came across this, Sullivan Flexi tank, any experiences? According to what the manufacturer says "they can be reshaped with a heat gun if desired." -> maybe this could help with reshaping the tank to fit into the 50mm space available. https://sullivanproducts.com/product/rectangular-flextank/ As a side note, for some reason I haven't been able to find a tank of 50mm of height as max (Sullivan, Dubro, Kavan) Another route to ensure the tank height is correct is I could, of course, rotate the engine somewhat so the cylinder would be pointing to 10 o'clock or something to help with respect to the tank height vs the carb. See picture. Not sure how elegant this is, though.. Any thoughts or recommendations? Artto
-
Hi Jon, Thank you for your advice - I believe what you wrote is good, not only for me but also for many other Laser enthusiasts as I happenen to be not the only one thinking of measuring Laser engine temperatures. I see - so the PTFE piston pads deforming is, like you write, pretty common. I thought my case more like an unusual case but I was wrong. Anyways, for that reason I may have overcomplicated things again. Sorry for that. I do want to follow your advice as you, as the manufacturer representative, know best the right use of the engines. This being said, this cooling / ducting / baffling theme and what are the associated good working practices can sometimes be "black magic". Hence the use of technology to prove things are fine can feel alluring. But anyways, I content with your help, Jon.
-
Jon, I see your point. This being said, as you pointed out in another conversation my the PTFE piston pads of my 300V had deformed somewhat indicating the engine had run a tad hot (while not overheated). The model on which the engine sits has baffling helping with cooling the engine. Therefore I feel tempted to try, maybe temporarily, the temperature sensors to tell me if my cooling ducting is working or if the cooling arrangement still needs some changes.
-
Thanks Frank, Yes, with Futaba you need to purchase the programming lead which is 29€. But then again, this is one-off cost that can potentially be used for other purposes, too? Anyways, so far this seems to be maybe the best alternative - at 49€ you get the temperature unit with 2 temperature probes. And the unit can handle up to 5 temperature probes (additional probes can be purchased separately for 9,8€ unit price which is quite reasonable). Anyways, much more attractive a solution compared to genuine Futaba which is 100€ for just one temperature probe. One thing that I do not like is the way the manufacturer suggest to mount the temperature probe: extract from the manual (https://www.powerbox-systems.com/uploads/tx_pbsdocuments/6621_BA_PBS-T-250_EN.pdf): "..The temperature sensors are designed to be attached to the cylinder head using a screw-lug. Drill a 3.5 mm Ø hole in one of the cooling fins, then fix the temperature sensor in place securely using a suitable self-tapping screw or M4 machine screw. A small quantity of heat-conductive paste under the sensor improves the temperature measurement." -> in no way I'm going to butcher my beautiful Laser engines! There must be another way to do this. A picture of the temperature probe: https://www.powerbox-systems.com/produkte/sensoren/temperaturfuehler.html
-
Thanks Dick! I will have a look on these
-
Thanks Dick, You are most likely referring to this: https://file.espritmodel.com/documents/pdf/jeti-mt300.pdf extract from the manual: "..Before tightening moisten the silicon tube with alcohol or white spirit in order to improve its sliding ability on the cables. Put the measuring object, for instance an engine cylinder, through the loop and tighten the loop strongly by means of the silicon tube in order to obtain a tight contact between the loop and the measuring object (for instance with cooling fins of an engine cylinder). After evaporation of the alcohol the silicon tube will firmly hold the loop tight. In order not to damage the sensor the dia. of the loop should not be smaller than 20 mm." Maybe this setup could work. I'm not sure if there are any Futaba FASStest compatible sensors other than genuine Futaba, though. But the principle of mounting the sensor can most likely be similar no matter what make sensor in question.
-
Sorry Paul, I'm not sure if I'm following you..?
-
Jon / gents, I would like to have measure engine temperature on my Lasers. Maybe not as a permanent solution but more like testing that the baffling is doing its job as expected and so on, for peace of mind. Anyways, do you gents have any experience on telemetry sensors such as this one or similar: https://futabausa.com/product/sbs-01t/ It may be difficult to keep the wire sensor close to the cylinder head, though. Maybe the optimal solution would be to have a tab on the copper glow plug washer to which you could attach a temperature sensor. And thus get a more reliable reading. Unfortunately, I haven't seen any sensor like like that on the market so far. Any thoughts or first hand experience on some set-up to measure engine temperature?
-
I used the traditional UI succesfully yesterday - a phone call to Laser Engines 🤣
-
Hi Jon, I hope you have a nice holiday - may I ask you when you are back at work? I just hope to get my 300v back from your excellent maintenance 🙂 btw, I just got a notification that my 150s have arrived at local post office.
-
Thanks, Jon
-
Jon / gents, What is the recommended fuel tank for a Laser 150? Is a 12 fl oz (350ml) ok or should I get a bigger one? I hope to get about 8min flying time with some reserve, of course? thanks, Artto
-
yes, counter clockwise and checking the piston height with a plastic tool
-
a question on tappet adjustment or setting the valve clearance: I have done this on combustion stroke when the pistonnis at TDC. I have ritated the engine until I see the intake valve opening, then I have kept rotating until the valve closes and the piston comes to TDC. I have then checked and if needed adjusted both valves to 0,05-0,1mm have I done the adjustment right?
-
It seems clear - and I will do the service on both heads. I just spoke to Jon and he thinks the age may have a contribution to the spring failure. Not any conclusive culprit, though. Anyways, as I need to demount the engine from the model to synchronize the carbs after remounting the head(s) I can do both heads for peace of mind as well. Jon will kindly submit me parts needed.
-
Great video - thanks Jon!
-
After having had a second look it is actually a posidriv screw. Thanks for notifying, Martin
-
Thanks Andy & Engine doctor good hint to use a plastic bag! Can you carry out the spring replacement without taking of the head?
-
Hi Jon, My 300v twin has just had an intake valve spring fail. Fortunately this happened on the ground before flying. I can't see any signs of rust on the spring (see pictures ). The engine was running at about 7700-7800 rpm max on the ground (Menz 20x7) so I don't think the rpms were too high. Did I just have bad luck or am I doing something wrong? Or is it an issue with a bad batch of springs or something and should I change all the springs for the peace of mind? Anything to be doen to prevent this happening again? Anyways, how do I carry out the spring replacement? Shall I loosen the small phillips screw in middle and then screw the axle out? Anything else that I should take in consideration? another thing: I'm planning to borrow one spring from my 240V to be ably to fly without much of delays - I suppose the spring is the same on both engines? thanks, Artto
-
Ok, it turned out my home tools did not seem to be up to the task to press & glue the pinion drive bearing in the crank case. So I went to a small machine shop where I got the bearing and pinion drive pressed in - and the adhesive used to hold the bearing in the bearing pocket is Loctite 638. First the bearing and then the pinion drive. No heating / freezing was applied. Anyways, neither of the parts (bearing or pinion drive) required much force to press them in place. For the peace of mind I measured the pinion drive flange to see if the pinon drive axle was straight. Both of the engines shew about 0,06mm play when measured. Now as the bearing itself has some play I hope this is ok. At least no excessive force was used.
-
Thanks, Jon