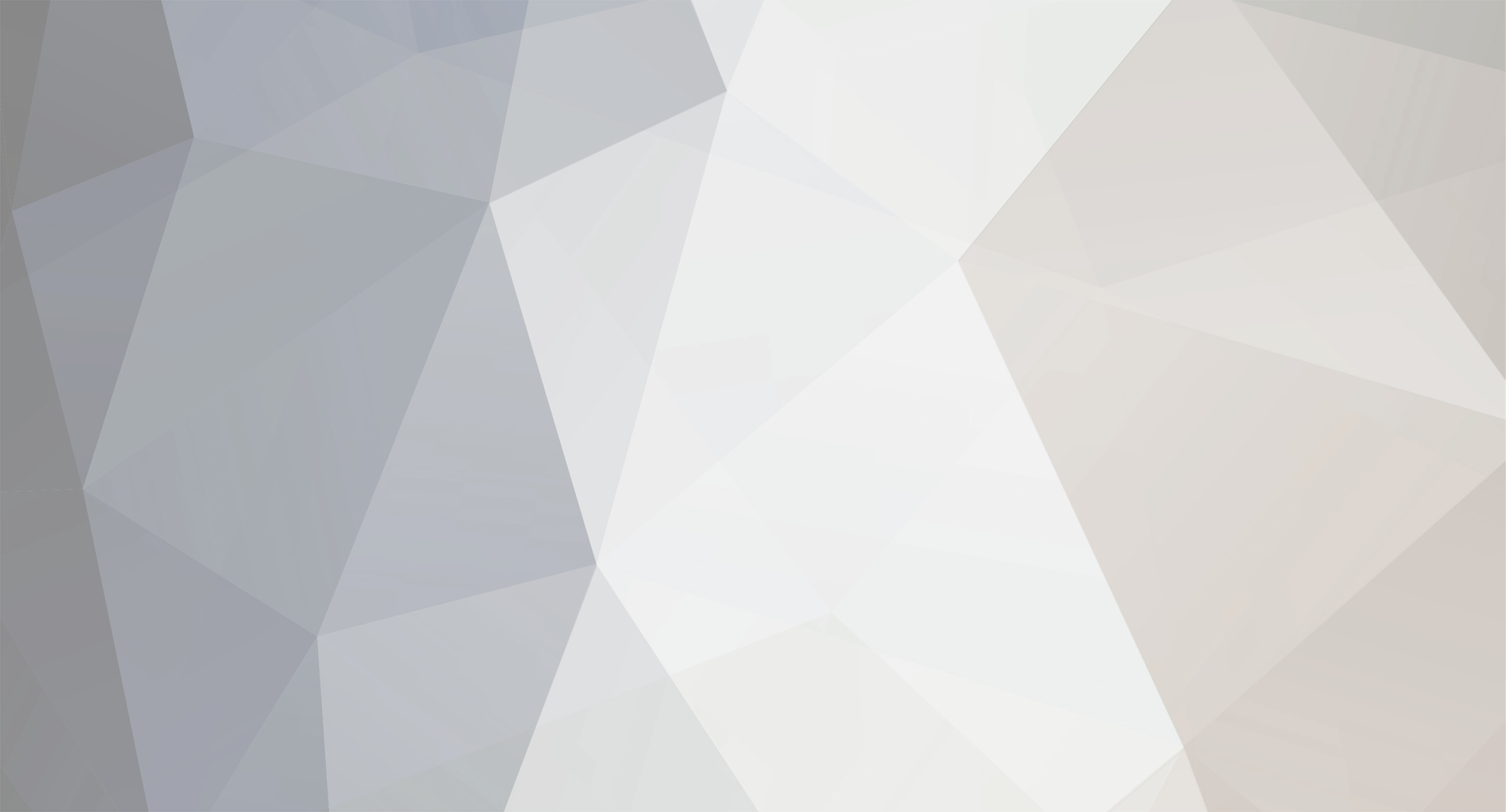
John Timmis
Members-
Posts
576 -
Joined
-
Last visited
-
Days Won
1
Content Type
Profiles
Forums
Blogs
Gallery
Calendar
Downloads
Everything posted by John Timmis
-
Hawker Hurricane by John Timmis
John Timmis replied to John Timmis's topic in Build Blogs and Kit Reviews
Hi all Last time we looked at the fuselage the basic structure had just been completed. All straightforward stuff. Next job was to make up a steerable tailwheel. I couldn't think of a way to make a really scale u/c so a simplified unit was made up using 1/4' x 1/16' brass & a wheel collet. It's a bit more convincing than a bit of bent piano wire Next a start was made on the fuselage stringers. I began with the underside . The formers were glued in place & then the stringers were added, starting with the center stringer & then adding one on each side in turn. The stringers were stripped from a sheet of hard 1/16' balsa. Slots can be cut with a thin file in the formers one at a time. Check that the stringer is straight & glue in. Repeat for the next pair until finished. It takes time. Cheers John. -
Hawker Hurricane by John Timmis
John Timmis replied to John Timmis's topic in Build Blogs and Kit Reviews
Hi all Joining the wing panels. I needed my extra long building board for this. The ailerons had been previously fitted, also the flaps had been hinged & of course the U/C mounts were in place. So we start with a careful check to see that all the ribs are flush & that the spars & ribs join neatly & with no gaps. Have a dry dummy run first with no glue & get the spring clamps & wing tip packing sorted out. The center section sits flat on the board on its rib tabs, a packing block is needed under the root rib tabs. I think I used gorilla glue on the ribs. The flap & aileron servos can be fitted & then all the bellcranks &wire links. Some care is needed to ensure that the flaps open & close in sync. Others might choose to use multiple servos but I stuck with the plan. The wing rib tabs have ensure that the panels have been built without warps. Until the wing s are sheeted,though, they remain very flexible. Balsa stand offs are tack glued to the front of the leading edge & the rear face of the rear spar. The wing can now be supported either side up while the bottom & top surfaces are sheeted. Rather than but the sheet over the joining rib I cut long splices over the center of the wing. The area above the flaps has been left open for now to provide access to the flap clevises. I had hoped that the flaps could be removable but it is looking unlikely because I can't get to the clevises from below & probably the wing underside will need to be finished & possibly painted with the flaps fitted before the upper skin can be finished. Leading edge can be fitted & shaped now. That's about it for now. Next back to the fuselage. Cheers John. -
Hawker Hurricane by John Timmis
John Timmis replied to John Timmis's topic in Build Blogs and Kit Reviews
Hi all, Just a few more words about the U/C. I've not tried to fit doors yet but so far it does'nt seem too bad. I wanted to fit sprung oleos so I was pleased to find a pair that looked as if they would do at a swap meet. A pair of eflight legs with a coil was also bought. I thought that I would be able to shorten the oleos a little if necessary. This proved to be impossible because there was insufficient material to allow another hole to be drilled & tapped. So 2 small compromises were necessary: the corner of the mounting u/c mounting flange had to be cut away slightly & because the legs were now slightly too long the wheels are a little bit undersized. All this could have been avoided if I had all the bits to hand before the u/c mounts were glued in place. Still, to make a virtue out of a necessity, it does give a bit more space in the wheel wells & the error will be hidden behind the wheel doors. Next time; joining the wing panels, bell cranks & linkages, skinning the wings. Cheers John. -
Engage brain before you turn on the machine. Sometimes the work will need to be held in a machine vice, sometimes in a hand vice & sometimes the vice will need to be bolted to the table. Some times the work if of a size, shape & weight that it can be quite safely held by hand. Experience will guide you. The work must always be held firmly down on the machine table. NEVER EVER let go because you will then be out of control. One difficult opperation is drilling large holes in thin metal with a twist drill. As the drill breaks through, the workpiece often tries to screw itself up the drill bit. A vise is essential here. To get back to the Forster bits. There is no particular problem. They are not inclined to snatch or grab the work. The downward pressure from the drill tends to press the work down until it breaks through. Don't release your hold until the bit is out of the wood. You could always fit a foot operated stop switch to your machine.
-
There is nothing wrong with Forster bits. I taught CDT in schools for years. I have a garage full of powerful woodworking machinery.All power tools need to be treated with care & respect.It is essential that the workpiece be held securely either in a vice, with a clamp or by hand. The workpiece must always be held down firmly against the machine table. NEVER let go of the workpiece until the bit is safely out of the hole. Once you let go you are out of control.
-
Woodworkers Forstner bits are very good. They will cut a flat bottomed hole if necessary. Because the are guided by the outside of the bit you can cut overlapping holes easily. Best used in a pillar drill.
-
Hawker Hurricane by John Timmis
John Timmis replied to John Timmis's topic in Build Blogs and Kit Reviews
Hi Adrian Yes you are probably right about the Typhoon. Don't doubt the retract angles either. My retracts were not unitract prices though. Proof of the pudding. Cheers john -
Hawker Hurricane by John Timmis
John Timmis replied to John Timmis's topic in Build Blogs and Kit Reviews
Hi all, For simplicity I decided from the start to use electric retracts. The LMS showed me some very nice units at not very nice prices. In the end I bought some from Whites for a very reasonable £17 each that I had seen at a show. They seem OK , time will tell if they stand up to the racket. I also acquired, from a swap meet, a pair of sprung oleo legs. These came as part of a pair of twist & turn Unitract pneumatic units. 5mm wire joiner was also needed to link the retracts to the Oleos. I wanted a wire leg with a coil Spring & eventually found a pair of Eflight legs. For the time being, however, I used a straight leg from B&Q mild steel in order to check the alignment. Mounts for the retracts were glued up from hard wood bearers with a a balsa spacer, drilled for bolts & the ends angled to fit the rake angle on the plan view. Balsa wedges were glued to the leading edges of the mounts to achieve the required side rake angle. The mounts could then be placed on the plan & the wing center section lowered into place. Check that the mounts were let deep enough into the wing ribs & using a dummy wire leg, that the retracted angle was OK. The outer wing panels could then be offered up & the outer corners of the mount chamfered to fit the lower wing profile. After much cutting & fitting (trial & error) the mounts were finally glued into the center section. The later photo shows the mounts in place & also the outer panels also glued . Flaps & hinges can also be seen. Observant viewers might spot a 'deliberate mistake'. Nothing too serious. Cheers John -
Hawker Hurricane by John Timmis
John Timmis replied to John Timmis's topic in Build Blogs and Kit Reviews
Hi all, Right then, let's have a look at the retracts. Let me say straight away that this is a first for me. Not done retracts before. Still the thought of a Hurricane flying around with the U/C down was a big NO. The full size U/C does not look exactly simple so there was a good deal of head scratching & it was very much a case of making haste slowly. Having seen many models where the under carriage either retracts into the wrong place or ends up sticking out a bit I knew that there would be pitfalls. One of the reasons for building the BT design is having the confidence that he would have it sorted. Anyway, the first thing is to understand the geometry. If you Google; "how to install retractable landing gear" you will find a very good article that explains , very clearly, all about Pintle Angles. The plan does not show any particular type of retracts but shows a typical position for the bearers. You are told that if the angles on the plan are followed than the wheels will be correct when up & down. Next time I'll try to show 'how I done it'. Cheers John. -
Brian Taylor Spitfire 69" - build only
John Timmis replied to Nigel Day's topic in Building from Traditional Kits and Plans
Hi Nigel Enjoy the build . I shall be watching. I might even talk myself into building one. My Hurricane is proving very enjoyable & I'm sure the Spitfire will be just as good. It would be nice to think that it might fly one day. Cheers John. -
Hawker Hurricane by John Timmis
John Timmis replied to John Timmis's topic in Build Blogs and Kit Reviews
Hi all, The flaps are simple enough. Just cut from .8mm ply. Ribs are from the same stuff cyanoed in place. The hinges are Robart pin type hinges with pockets to fit the hinges to the wing. This means that the hinges can be detachable, at least for now. I was hoping to retain this ability on the finished wing but because there is no access to the flap clevises from below this will not be possible. For now all that can be done is to ensure that each flap fits the wing & opens /closes fully. Linkages will come later after the wing panels are joined. That's another story. Will have a look at the retracts next time. Cheers John -
Way back in the early 70s Eric came to the school where I taught CDT to provide cover for a colleague who was absent for a year. Aero modelling soon began to feature on the curriculum. We had control line in the playground, RTP in the hall & chuck gliders on the field. What a character. Happy days. The wings of FRED folded for transport behind his Ford Anglia with the tailplane on the roof rack. Cheers John
-
Hawker Hurricane by John Timmis
John Timmis replied to John Timmis's topic in Build Blogs and Kit Reviews
H all, After that diversion, back to some building. Next the wing. There is no doubt that this is where the major part of the work lies. The wing is in 3 panels, there are 4 split flaps, ailerons, all with internal linkages plus retracts. So quite a lot to do. The wing has a very thick section (about 18% I think), it must have been the thickest wing of any WW2 fighter. Anyway, it means that we will end up with a very strong & stiff wing with lots of lift. I'm sure that if you wanted to simplify the build the flaps could be omitted , but , "Hey we're making a scale model". The basic structure is quite straightforward. All the parts are very accurately drawn & the wing ribs include jigging tabs so a straight , true wing is guaranteed. If a part does not fit then your'e doing something wrong. The ailerons are hinged on a wire that passes from root to tip & is supported I a brass tube bearing at each end. Having the basic fuselage to hand together with the wing means that the wing fixing can be sorted out now. No problems so far then. Cheers John -
Hawker Hurricane by John Timmis
John Timmis replied to John Timmis's topic in Build Blogs and Kit Reviews
Thanks Danny. It looks like I'm safe to stick with the one I have then. What a brilliant forum this is. Cheers John -
Hawker Hurricane by John Timmis
John Timmis replied to John Timmis's topic in Build Blogs and Kit Reviews
Hi Geoff, Danny. Thanks for your replies, I really appreciate the advice. Actually I made an error when entering the motor serial . It's a 2386 not a 2385 as I first said. I guess that will make it a bit better. Would you have another look & tell me what you think? Thanks John -
Hawker Hurricane by John Timmis
John Timmis replied to John Timmis's topic in Build Blogs and Kit Reviews
Hi all Geoff. I'm not an expert on power trains. Anyone who is please feel free to comment. I bought the motor unused from a friend, it looks quite chunky to me. 'Thunder Tiger ace RC ripper' , OBL 50 /50A 2385. ( where do they get tha names from?). Anyway the specs say: 520 rpm / volt, max surge current 58A, recommended prop 14/8, 15/8. I tried it out this afternoon. It showed about 840 W, but this was on a 14x7 prop & a very puffed up & clapped out Dynamic6S, 330C 4500mAh battery (all that was available). The voltage dropped to 18v under load. I think that I will probably need 1000W. What do you think? Am I in the right ball park? Cheers John -
Hawker Hurricane by John Timmis
John Timmis replied to John Timmis's topic in Build Blogs and Kit Reviews
Hi Trevor, Danny. This is an area of the model that I'm working on now. On the Hurricane, the whole of the fuselage forward of the cockpit was covered by removable metal panels, very convienient for us modellers. The top of the cowling will be removable, the area bounded by the tape. There is enough room to hold a party in there. There is also the possibility to create a similar space under the cowling, perhaps for a sound module? Cheers John. -
Hi I fancy coming , not to fly, just for a look. Can I just turn up at the gate? Cheers John