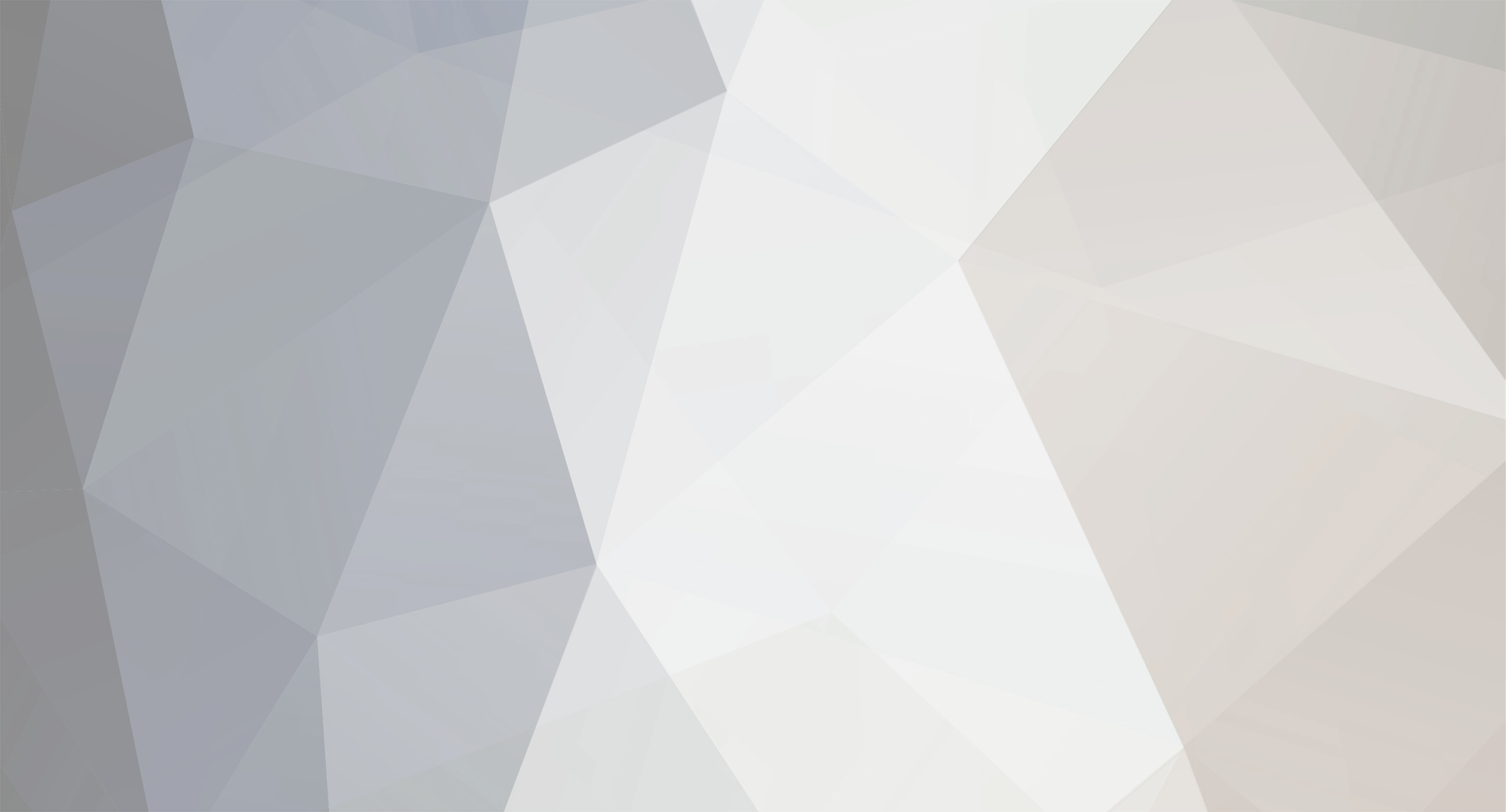
Dave Garrett 1
Members-
Posts
151 -
Joined
-
Last visited
Content Type
Profiles
Forums
Blogs
Gallery
Calendar
Downloads
Everything posted by Dave Garrett 1
-
Apache Aviation Monocoupe 90A Build
Dave Garrett 1 replied to Dave Garrett 1's topic in Build Blogs and Kit Reviews
Hi Everyone Not much done in the last 2 weeks. I have been to Spain for a short break (visiting museums The Amstels, The Estrella, The San Miguel ). On returning I get laid up with the dreaded flu . I have fitted the cabin roof &windscreen frames, the cabin side window & various strengthening pieces. All the frames are again interlocking & self aligning, No major problems have been encountered. I have also fitted the throttle linkage outer tube, supported by a bracket behind the firewall. If my calculations are right, there should be enough lateral movement of the inner tube for a free moving throttle linkage. If not . I have now came across a minor niggle with the kit. The larger CNC cut parts have been laser engraved with their identity. The smaller parts have no marking at all. The build manual does not contain maps for the routed sheets & it not always obvious from the plan what the part looks like. It took me 1/2 hour to find 2 small pieces The next stage is to blend the square corners of the formers & cabin floor to match the general shape and start the sheeting. I have a question for one of our experts on the sheeting process. The build manual tells you to cut 3" wide pieces to length for both sides & soak in water to make them pliable. The instructions tell you to glue the sheeting to both sides at the same time, staring at the rear formers & working to the front. This sort of makes sense as any framework distortion will be minimized. My question is what adhesive to use? Any advice would be most welcome. The poor weather last weekend put the mockers on any flying plans, but it did not stop little old Yeovil Town FC thrashing the once famous Nottingham Forest 3 - 1. Up the Green & Whites! Cheers Dave -
Apache Aviation Monocoupe 90A Build
Dave Garrett 1 replied to Dave Garrett 1's topic in Build Blogs and Kit Reviews
Hi Robin Yes I agree the Laser is a work of art. British as well, In my career, I spent about 15 years as a machining production engineer, and can really appreciate the work that goes into these engines. The quality of the machining and finishing is up there with the best I have ever seen. Everybody Talking about works of art, a Japanese example has finally arrived. The Monocoupe's receiver, a Futaba 20008SB. It never fails to amaze me how they manage to squeeze a 8 channel receiver into such a small package. Earlier in the year, I treated myself to the new Futaba 14 SG combo. The receiver supplied with the combo (70008SB) is telemetry enabled. I intent to use this in a large petrol model (LMA Sky 120 trainer), so I can keep an eye on the receiver battery voltage. The Monocoupe's wing has flaps, and uses 4 servos. I intend to use a separate channel for each servo so I have the ability to play with the aileron differential & reverse one of the flap servos to keep the linkage the same on both sides. 20008SB receiver has the Futaba S-Bus system, which could allow me to have just one wire to connect when the wing is fitted. However having just discovered the cost of S-Bus servos, it will probably 4 wires to connect Best Regards Dave -
Apache Aviation Monocoupe 90A Build
Dave Garrett 1 replied to Dave Garrett 1's topic in Build Blogs and Kit Reviews
Hi Everyone A bit more done. I have finished the firewall & cabin floor. The cabin floor is a substantial piece of 1/8" ply. It runs from the engine cowl to the back of the cabin. The floor is reinforced with a ply doubler at the undercarriage position. Captive nuts are installed for undercarriage attachment. An angled mount is fitted for the elevator & rudder servos. The throttle servo is mounted directly to the cabin floor. As the servo mounts are only 1/8" ply, I decided to add scrap ply doublers for the attachment screws. Pilot holes have been drilled for the servos. I have build the battery box and glued this to the cabin floor. With these 2 major sub-assemblies complete, building can commence The fuselage is built into sections. The front section runs from the engine cowl to the rear of the cabin area. This section is constructed as an interlocking framework of ply or liteply formers, cabin floor & alignment pieces. The framework is then fully sheeted with 1/8" balsa. The rear fuselage section is the traditional open framework structure. When finished the 2 pieces are glued together. Building starts with the front fuselage section. Tags on the firewall & the other formers slot into pre-machined holes in the cabin floor. Liteply spars run along the side of the formers. These spars interlock with slots in all the formers and are wide enough to ensure the formers are at the correct angle to the cabin floor. The radio receiver is mounted on a foam pad on the rear cabin former. The U shaped cut outs on the former are attaching the received with rubber bands. I have also glued 2 pieces of plastic tube to the former for the receiver antennas. This is first for me, engine & radio installation sorted before covering Next job is the cabin roof & windscreen structure. So far all the parts seem to fit very well & I have not encountered any major problems . I'm sure this will change! Cheers Dave -
Apache Aviation Monocoupe 90A Build
Dave Garrett 1 replied to Dave Garrett 1's topic in Build Blogs and Kit Reviews
Hi everyone Quick update. Spent the morning drilling the firewall to suit the engine mount & vibration absorbers. Thinking ahead (for once), I decided to sort out the throttle linkage and fuel pipe runs, The throttle linkage, is the normal plastic snakes, with a ball & socket joint on the throttle arm. After working out the best position, I drilled the fire wall to suit the outer tube. I then offered the engine up to the mount & connected up the throttle linkage. On checking for free movement, it soon became apparent, that the engine was too close to the firewall for the linkage to work correctly. As the throttle arm in very close to the engine cylinder & exhaust, it would not be possible to make a reversed connection. The solution was to open up drilled hole to a larger square. This gives plenty of clearance for free operation of the throttle. Later I will fit a small former some distance behind the firewall to anchor the outer tube. Looking at the position of the fuel tank on the plan, the best position for the feed pipe, is tough the lightening window above the carburettor in the picture. The windows are blanked off with balsa sheet, I will drill the fuel feed hole through the balsa later & strengthen both sides with thin ply. I have also drill an 1/8" hole on the mount centreline for a brass tube for a forward facing tank vent (Laser engines do not use exhaust pressure) Cheers Dave -
Apache Aviation Monocoupe 90A Build
Dave Garrett 1 replied to Dave Garrett 1's topic in Build Blogs and Kit Reviews
Hi Everyone I have made a tentative start. First job, drill the engine mount to suit the engine. Laser 70 engine mounting lugs drill to suit M4 bolts. We have M4 bolts & self locking nut in stock - result . Offer engine up to mount to check fit. Engine mount too wide for the Laser by about 8mm . It look like the kit mount is for a 90 size crankcase. Off to the LMS to buy a 60 size engine mount. Mrs G is off to the seaside for the weekend with my sister, mum & assorted nephews & nieces, leaving me home alone . So on the way home from the LMS, the car veered sharply to the left, and I find myself in Morrison's car park . not wishing to waste the opportunity, I went in and purchased some Fuller's finest aeromodelling lubricant! Engine successfully mounted. The only problem encountered is due to the length of the Laser's mounting lugs. The rear mounting holes end up going through the underside tapered buttresses. I had to file flats into the tapers to allow the washers & nuts to seat squarely. I used a generous radius to blend the flats into the buttresses to avoid stress raisers The engine's prop driver has to be 128mm from the back face of the engine mount. To make accurate positioning of the engine in the mount easier, I made a simple tool out of scrap liteply. I think the following picture explains how it works. The tool legs are 128mm long where did the rest of the afternoon go? Next stage is to drill the fire wall to suit the engine mound and vibration absorbers. When this finished, the worst 2 jobs in aeromodelling will be out the way already. I don't know why but I hate drilling engine mounts & firewalls! Wife away = Flying tomorrow, but I hope to do a bit more on the Monocoupe Percy Thanks for the offer of photos of your friends model, I Would be very interested. Off now for a glass of lubricant. Regards Dave -
Apache Aviation Monocoupe 90A Build
Dave Garrett 1 replied to Dave Garrett 1's topic in Build Blogs and Kit Reviews
Thanks for the reply Percy. The kit no longer contains molded undercarriage fairings, like your friends model they are now carved from balsa. the following picture taken from the plan shows how it is done. The aluminium alloy undercarriage has to be bolted to the ply support plate before the underside is sheeted. After sheeting, thick balsa blocks are glued to the fuselage and carved to form the upper leg fairing. The upper fairing blocks & underside sheeting is clear of the aluminium legs to allow flexure. The lower leg fairing is balsa sheet glued to the aluminium core. There is small gap between the upper & lower leg fairings. As the undercarriage is built into the fuselage, it looks like serious balsa surgery after that heavy landing, hatch or no hatch . I will probably drill holes in the underside sheeting inline with the undercarriage attachment bolts. If they shake loose, I can at least re-tighten them without to much bother. I have chosen to go with the Laser 70. Ordered Monday, arrived today. Great service If you follow the instruction manual, the first job is to bold the engine to mount & drill the firewall. I now have no excuses not to start the build. Best Regards Dave -
Thanks again for the Welcome Ade I also listen to Jean michelle Jarre (also his father's music). ' Magnetic Fields' is my favorite Regards Dave
-
Apache Aviation Monocoupe 90A Build
Dave Garrett 1 replied to Dave Garrett 1's topic in Build Blogs and Kit Reviews
Hi Andrew Yes, the kit is from Phil Kents design Regards Dave -
Hi Everybody I'm am shortly staring a Monocoupe build, is anybody interested in the build? I bought the kit from Apache Aviation before they the kit range to SLEC. It has been maturing on the self, waiting for me to complete other projects. I hope to start the build in mid October. I am very impressed with the quality and completeness of the kit. It includes every thing you need except for glue & covering. The major wood components are CNC routed from good quality light ply or balsa. The fiberglass cowl is nicely molded & incorporates the engine rocker cover blisters. The wheel pants are of the same quality and very light. Nothing in the hardware pack will need to be replaced. The hardware includes engine mount, engine mount vibration damping bushes, wheels, fuel tank, fuel filter & filler kit. The plans are CAD printed on 2 large rolled sheet. A very detailed instruction manual is also provided. Below is a photo of the kit layed out. I have a bit trouble deciding on which engine to use. The kit's recommendation is 70 - 90 4-stroke. The plans shows a Laser 70 installation, which fits inside the cowl with minimal cutouts. On my shelf I have any a used ASP70 & new ASP80 4-stroke. Both these engines are less compact than the Laser, so would protrude through the cowl. I also have a RCV90 in another model. This engine is also very compact so may be a good choice. As the model will be relatively light, I don't believe power will be a problem with either engine, just the ability to swing a larger prop. So gents what shall I do, purchase a Laser 70 or another RCV90 or make do with one of the ASPs? I have searched the internet for a build blog for this kit without success. If anyone out there has built this kit i would welcome any advice. Regards Dave
-
Thanks Gents It's refreshing to some of us still appreciate real music Skippy, you have me intrigued, I have got to check out Terry Wogan's 'In Dulci Jubilo' on You-Tube Dave
-
Let me introduce myself & tell you a little about me. I'm Dave from Yeovil, Somerset. I'm the wrong side of the big five O. I have been married to Carol for nearly 30 years. We have not been blessed with children. I work as a design engineer in the aerospace industry. I have been flying radio control fixed wing aircraft for the last 10 years. I mostly fly IC powered sports, acrobatic & vintage type models. I have dabbled in electric powered models, gliders & foamies. I enjoy the building side of the hobby & have have good success with a number of kits. I still put together the occasional ARTF if I'm desperate. I am the treasurer of the Westland & Yeovil district aeromodellers club & a member of the Ilminster club. I have been lurking on this forum for sometime. I especially enjoy reading the build blogs. As I'm about to start an Apache Aviation Monocoupe 90A, it's time to start giving something back. Outside of model flying, my other passion is football (watching only now!). I'm a season ticket holder for the mighty Green & Whites (Yeovil Town FC). This does however have an adverse affects of Saturday flying during the playing season. Other interest include traveling & holidays. I have been known to drink the odd bucket or two of real ale. We are blessed in the southwest with some wonderful micro breweries. I am probably the only Mike Oldfield fan left in the country. Regards Dave