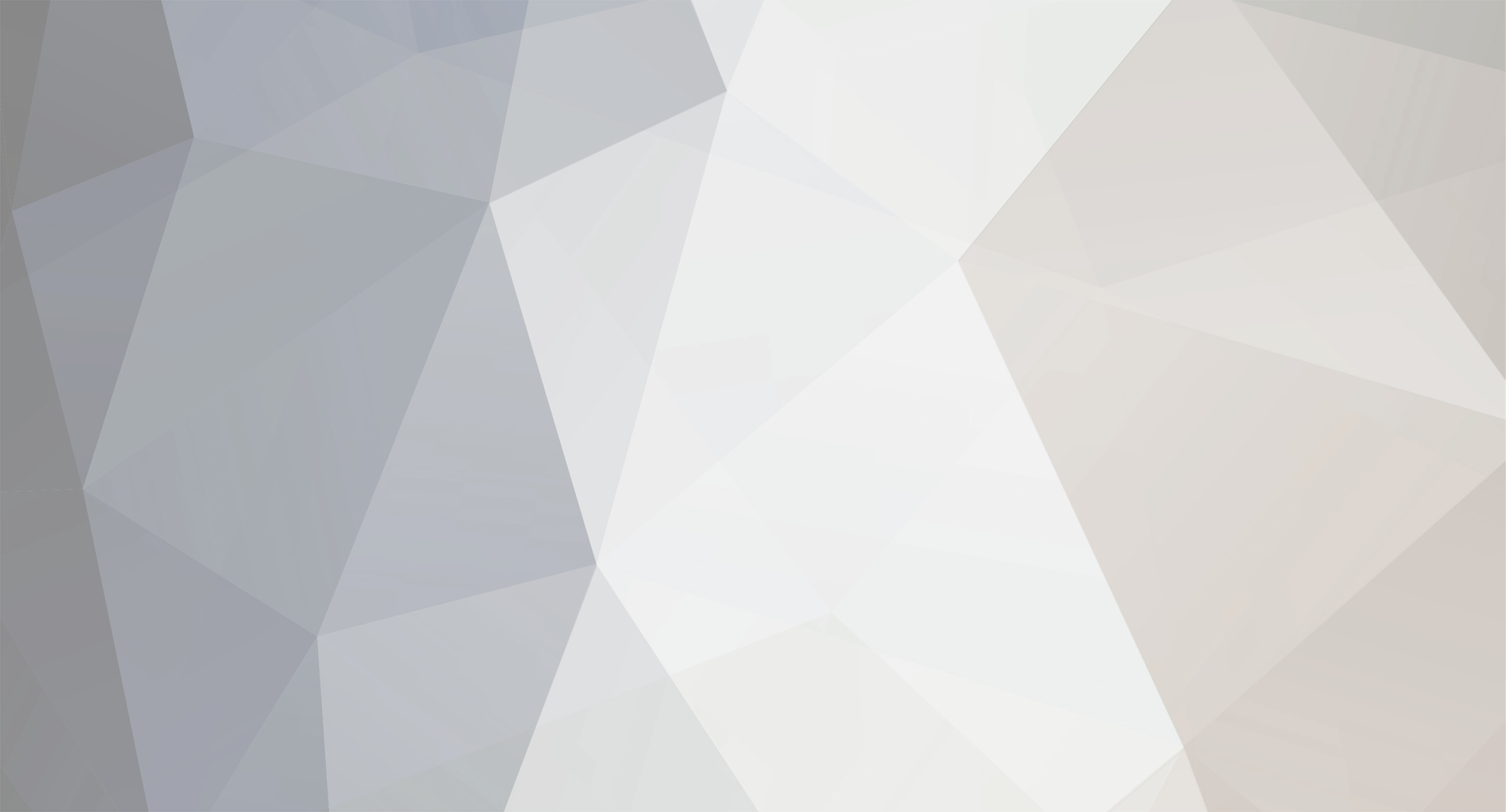
Grant Webb
Members-
Posts
41 -
Joined
-
Last visited
Never
Recent Profile Visitors
The recent visitors block is disabled and is not being shown to other users.
Grant Webb's Achievements
0
Reputation
-
Grant Webb joined the community
-
Hi Tony. As has already been said, it's a matter of coordinating the right amount of additional throttle to maintain speed, with the correct amount of up elevator to keep the nose from dropping. Even when sitting in a full-sized aircraft, this takes a bit of mastering. The aim at PPL level was to be able to complete the manoeuvre with no more than a +/- 50foot variation. The technique was to feed in a little extra power as you rolled into the turn, while applying back-pressure on the yoke to keep the nose tracking the line of the horizon. The steeper the bank angle, the more power and back-pressure that is required. Then reverse those actions on rolling out. Without the benefit of a "bum-on-seat" reference you just have to do the best you can to judge that from the ground in flying R/C. As for the wind, as Andrew stated above, outside of landing and take-off (and the effect of turbulence) you can pretty much exclude the effect of wind. All an airplane is interested in is that it has sufficient speed to maintain lift through the air mass surrounding it. If an aircraft is flying at 90 knots downwind it is flying at 90 knots relative to the air mass. If in this example there is a 10 knot wind as observed from the ground, then it's flying at a "groundspeed" of 100knots, but still maintaining an airspeed of 90knots. Cheers, Grant W. Edited By Grant Webb on 26/04/2017 09:58:25
-
Have to say I am firmly in the LiFePo camp. Having suffered model loss through "Black rot" in the wiring while using NiCad packs, I made the switch to LiFe cells a few years ago after research placed the blame on the Ni-Cad cell chemistry. From my research it was suggested that NiMh are of similar chemistry to Ni-cads and subject to the same potential problem. You can read a good description of it here. So, to be on the safe side I decided to switch to LiFePo4 technology for all my IC powered models. I still have two 27MHz transmitters waiting for re-wire due to the black wire rot. My 2 cents worth.... Grant W. NZ
-
Thanks for your advise, Denis. I'll try and take that on board. Peter, actually I now seem to remember that airfoil was used. Don't know how I let that slip. Thank you for the prompt. Actually, looking at the flat bottom of the USA35b, it's very much in keeping with the photographs of the full sized that I have come across. Wing now being re-drawn. Cheers, Grant W.
-
Well design progress is slow, but proceeding none-the-less. However, I'm unsure about the airfoil on this aircraft and haven't been able to confirm what was used on the original. I found another r/c model design which was described as using the NACA2415 section, so I have followed suit. I had previously used a Clark Y section, but that appeared too thin. But if you look at my screen captures below with the NACA2415 section and compare the wing thickness with that of the 3-views being used, it looks wrong/too thick. Thoughts please???? I have used 2.5degrees of washout in the wing, have double checked it, but that too seems distorted. Cheers, Grant W. Edited By Grant Webb on 08/12/2016 01:39:45
-
Posted by Braddock, VC on 24/11/2016 23:49:23: .... I have some thick black polypropylene corner protectors from a tumble drier .... I did much the same on my Seagull Savage Cruiser cowl, only I use a saddle hose clamp I had retrieved from an old garden sprinkler system installation which I'd partly dismantled. Just chopped out the two right angled elbows removing the hoop over the top. Works brilliantly. "Waste not want not" should be the hoarders mantra.... Grant W. Edited By Grant Webb on 25/11/2016 01:17:50
-
Thank you gentlemen for your input. Peter & Simon, I'm thinking now maybe a hybrid of your two ideas, with longerons tapering away to nothing in front of the tailplane. My reasoning behind this is to provide some strength at the transitional point at mid-fuselage where the tail-cone joins with the "jettisonable fuel tank" forward pod (if that makes sense). I do like the removable crutch concept as well and am considering the stepped crutch as used in TDM Model's Polikarpov I-16 to positively locate the formers length-wise as well. However I do have some 'T' section aluminium extrusion which might serve the purpose very well. But maybe a removable 22mm carbon tube would give more room for control push-rods later on? Just for interest, below is my 3D model of B. Schoefeld's rubber powered model as published in the Sept 1946 edition of Air Trails Pictorial. I found the design floating somewhere around the web (Outerzone maybe?) and 3D modelled it as a proof of concept (test my ability to produce a CNC model). May yet build it as a rubber model too. It utilises shaped scarf-joined longerons full length, maybe this could be used here too? Cheers, Grant W.
-
Thanks everyone for the feedback. I'll see how I can use your ideas to nut out my approach. Robin... you are spot on with your Piper Pa-8 Skycycle replica. Something about it really appeals to me as a lazy evening parkflyer. I'm looking to utilise this as my first foray into CNC using a friends machine. Cheers, Grant W.
-
Hi guys. I'm seeking some advice/ideas as to how to approach the construction of a tightly rolled rear fuselage. My model is being designed with a wingspan of 1300mm, which gives a mid fuselage outer diameter of around 95mm, tapering down to just 35mm at the tail. The full sized aircraft's fuselage was constructed using a F4U Corsair jettisonable fuel tank for the front half, with an aluminium alloy rear section. Any guesses at to what the aircraft is? I'm still in the early stages of drawing up my plan as can be seen from the attached picture, but need to consider my construction technique. My preferred method in mind would be some form of built up balsa tubing, probably planked over formers, then covered with light weight glass for strength, but I am conscious of keeping weight down as the power source is to be a .30 four stroke. Any ideas or comments greatly appreciated. Grant W.
-
I believe this is the same as the old ModelTech Dragon Lady which I built from a kit. I used to have one which I flew with a Saito FA-120S as recommended by my local model shop. Flew very well, wasn't short of power, but not over-powered either. Edited By Grant Webb on 27/09/2016 03:53:50
-
Hi all. Just wondering, has anyone tried a gyro in an autogyro? If so, what have been your experiences with this? Cheers, Grant W. NZ