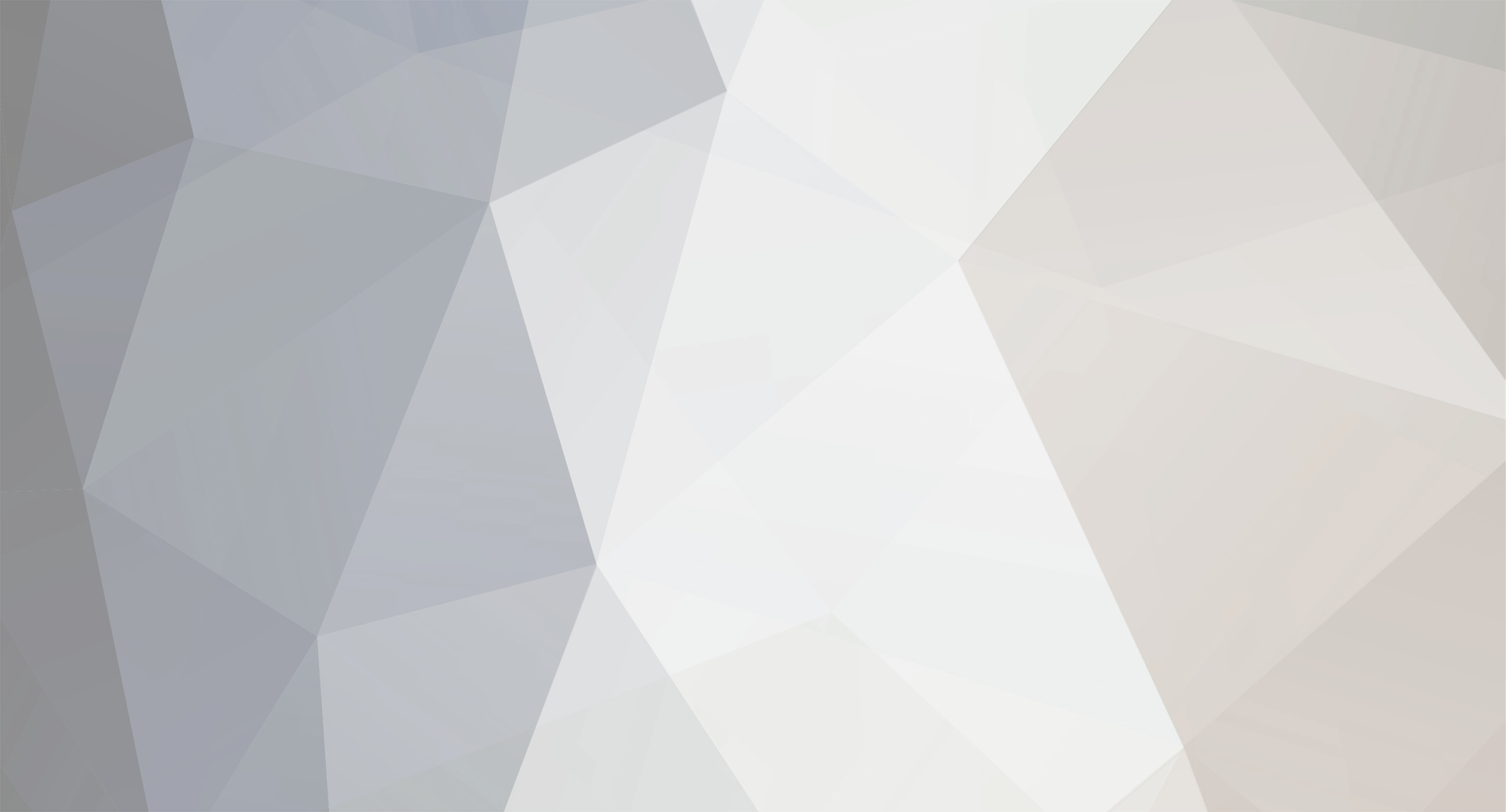
Brian Parker
Members-
Posts
536 -
Joined
-
Last visited
Never
Content Type
Profiles
Forums
Blogs
Gallery
Calendar
Downloads
Everything posted by Brian Parker
-
The fuel lines were inside the rocker cover because that was where the Lister had it's injectors. A failed turbo induction-side oil seal is also a known cause of diesel engine run-away.
-
Timbo, I thought your installation would be robust. I wonder what modulation protocol is used for downlink? It seems almost impossibly dirty, does it have type approval? I wonder if the downlink problem arises at the point before spreading and immediately after dispreading. If so, then thorough screening might be an option. Although the best option would be to bin it before Eric Bray finds out. (See his thread on the campaign for EMC). Erfolg, What does it mean? As a very loose comparison. You are standing at a locked door outside a room. If you have the key can enter. The room is hostile, standing upright presents an easy target but you have a very small 'footprint'(narrowband), by lying down (spreading) you become a small target but have a large 'footprint '(wideband). You can cross the room unseen by laying down and crawling. At the other side is a door, if you have the key you can exit the room and stand up safely (despreading). And yes, your world is in peril.
-
How is this happening? I've no experience of using a Video link, but if I may out of curiosity.. The video signal is 10mW=10db. The spread spectrum signal is 10mW =10db. The RC spread signal uses a very wide frequency band, the width determined by the processing gain. The processing gain can be the region of 60db or expressed as a ratio of power gain 1,000,000. Wanted signals can be in the noise (10mW video signal unwanted) and the wanted signal should still be received, the unwanted signals are not seen. The wanted signal/code is recognised/seen by the receiver and the data retrieved and processed by despreading. How close was the receiver to the video transmitter and was it electrically isolated from the rest of the equipment?
-
Martin, I too had a misspent youth tuning Bonnies Nortons etc. Recalling from memory initial trial settings were…. Methanol at 11:1 38 degree adv. Methanol at 13:1 34 degree adv 100 Octane 10:1 38 degree adv. Not sure if this has any relavence on the current conversions.
-
Believe me guys, a centre drill will do the job. If you must use a milling cutter a slot drill is better than an end mill. An end mill is a profiling tool. Also I remain to be convinced on the need to fit head shims but watch with interest.
-
Martin, Fully agree. An urban/rural myth. Gardner even specified a range of optional fuel pump governor springs to compensate for altitude running to maintain output power.
-
Doug, Start the hole off with a small centre drill (Cronos or RDG tools) guaranteed not to wander if you take it steady and cheaper than a prop driver. You can also get the magnets from ‘guysmagnets.com’ £3.61 for 20 post free. He also sells from ebay.
-
As posted above, I also fail to see how a 4 stroke glow engine is able to maintain reverse running. I have heard several stories over the years of Diesel engines, automotive, marine and stationary, running backwards. Also of stationary engines installed in engine/generator sheds where the air vents became blocked and the running engine caused the shed to implode. The problem I have with automotive/marine engines, perhaps I'm missing something, if the injection timing was advanced enough to 'back-rock' the engine then surly the timing in the reverse direction would be so retarded that the compression temperature would be insufficient to combust the fuel. Perhaps the long stroke of a Gardiner engine and its relative piston speed could maintain revolutions for a period. The two stroke diesel, (certainly the TS3 (as mentioned above) and also the Napier Deltic) that utilised a blower(supercharger) for scavenging could only run in the 'forward' direction.
-
Doug, Just reposition the magnet (or fit another) on the driver to give the correct timing. Remove the original if fitting a new magnet. As stated earlier, Neodymium fumes are toxic so take care if drilling the old one out. They are also very brittle.
-
Reversing Dynastarts were also fitted to marine outboard engines. Oil contamination of the brush gear and CB points tended to be problem, usually at the most inopportune moment as I recall.
-
It works but the response is rather slow. Closer lapping of the ‘barrel’ may improve things. Might try a mark2 version sometime.
-
The tone of the article surprised me. Not what we, as readers, are accustomed to from the Magazine.
-
Watching with interest. A few comments if I may.. Doug, What about a small centre drill to start it off? Mixture..At ¾ turn out thats not much oil per rev, almost a drought in the crankcase of a conventional 4 stroke. Gerry, Are you using synthetic oil or 2-stroke oil in the petrol mix? There is probably quite a fine line between insufficient oil for the bearings and an excess of oil clogging the exhaust valve stem if using the 2-stroke oil. The compression pressure requirements for glow and petrol are quite close and if necessary retarding the ignition slightly for a test run rather than stripping out the engine and adding shim gaskets might be worth a try even on a new engine. Satisfactory air/fuel(petrol) ratios for the ignition of 4 strokes seem easier to achieve than for a 2 stroke. While it may be safe to reduce the oil content of a 2 stroke a 4 stroke will need a close eye kept. Doug, Some before and after results on the new engine would be useful, also any ignition advance/RPM data would come in handy if possible.
-
The only common sense thing to do is to fit a proper engine in the Cessna and then send the Wankel off to me.
-
The actual ignition point of the CI engine is determined by temperature/pressure of the gas/mixture and our throttled engine controls the ability of the port to pass gas/mixture by combining the area opened with the elapsed time between opening and closing of the port, the 'time-area integral', ie. the point of maximum pressure/temperature within the cylinder is dependant on throttle position. Volume, pressure and temperature of the gas all change at the same time. The laws of Boyle and Charles are combined. P(i)*V(i) / T(i) = P(ii)*V(ii) /T(ii) Probably getting in to deep again.
-
Taking that the velocity of the gas through the port is to the piston speed as the bore area is to the port area. I assume that SPI is more effective in boosting long stroke engine performance V (gas): S (piston speed)=D squared (bore): d squared (port). Touching on ignition timing/compression radios and taking into account the above. On a throttled engine the ignition timing will be proportionate to compression pressures. ie. proportionate to the effective port diameter. All things being equal, if the compression screw is set for max RPM at full throttle then the engine should be responsive to the throttle and adjust its own ignition point/RPM accordingly. Currently, I only have two CI engines, a rather tired PAW 55BR RC that is happier running at full chat than throttled. The other is a home build. Neither have SPI (although inspired by this thread I may file the home build piston skirt and give it a go).
-
Engine use to charge flight batteries
Brian Parker replied to Delta Whiskey's topic in Gadgets and Electronics
You just need to couple a second brushless motor between the main brushless motor and the prop and wire it into the flight pack as a three-phase alternator. If you ignore efficiency losses you will have perpetual motion. -
SPI increases the time available for induction by combining the areas open during the induction elapse time. The more powerful engine at 1/16 confirms that SPI does work, there are sceptics.
-
FP-R105M (Psst its actually a 7 channel!)
Brian Parker replied to Peter 'Ivanna Crashalot' Savage's topic in Futaba
It's probably just a generic board and it will not be populated for the full channel spec. -
In reality a British Invention, Patent No 7146 (The Compression Ignition Oil Engine) taken out by the British engineer Herbert Ackroyd-Stuart in 1890, a full two years before Dr Diesel’s coal dust fuelled engine. By the way, as I understand it, a sub-induction piston engine is optimised to produce performance at high RPM (at the expense of poor low-end performance) and it is not designed to be throttled. Not tried it IanN, but not sure you can actually fit as many silencing devices as you like with minimal impact on performance.
-
Further developments..... Adding auto advance. Obtaining a reliable, smooth operating mechanical system that tracks a correct timing curve is not easy (read almost impossible). Conventionally the throttle arm moves backwards and forwards and the advance lever moves left to right. For ease of connectivity they need to be in the same plane (pun sorry). Best solution, use a PIC microprocessor, not difficult surely? That’s what I thought. The mock-up. Students of Irony will appreciate the use of an electric motor to develop an IC operation. Hall effect on arm detects magnet on rotating hub, white disc is stationary, cocktail stick in hub provides reference for counting RPM and yellow LED is visual indicator of output. The white object and small PCB on the right hand side of the scribing block simulates the coil and the ignition circuit. Prototype Vero board allows the programming of any 8-40 pin PIC microprocessors and also contains a 4Mhz crystal. Now all I need to do is to get my head round the program. The best result I've managed so far. Top trace (single pulse only shown) is hall input, lower trace is coil trigger/ignition point. This may take some time.
-
I have had the SIEG C3 (from ARC Euro Trade) for some time, bought when they had their 'Fully loaded' offer on. More than satisfied with it although I have done a few modifications. It is a simple job to commission it yourself, you don’t need to pay ARC to do it, plus it gets you to know the workings of the lathe. If you havn't any tooling etc then expect to spend almost the same amount again to set yourself up properly if you want to be able build engines etc. Mine has proved to be very reliable, only needing a new drive belt (oil contamination due to over-enthusiastic lubricating) although it does need regular adjustment with use. The most noticeable modification is to fit the Brass Gibs set for instant smoothness. The Book, 'The Mini-Lathe' by David Fenner takes you through the commissioning process, I wish it had been available when I bought mine. It details several modifications and has lots of useful information. The Lathe is actually a Chinese copy of a Russian Lathe.
-
EDF current draw in the air
Brian Parker replied to David Ashby - Moderator's topic in Electric Ducted Fan
I think the difference is between the pressure in a confined column and in a free surface/space. Dynamic pressure is probably involved somewhere.