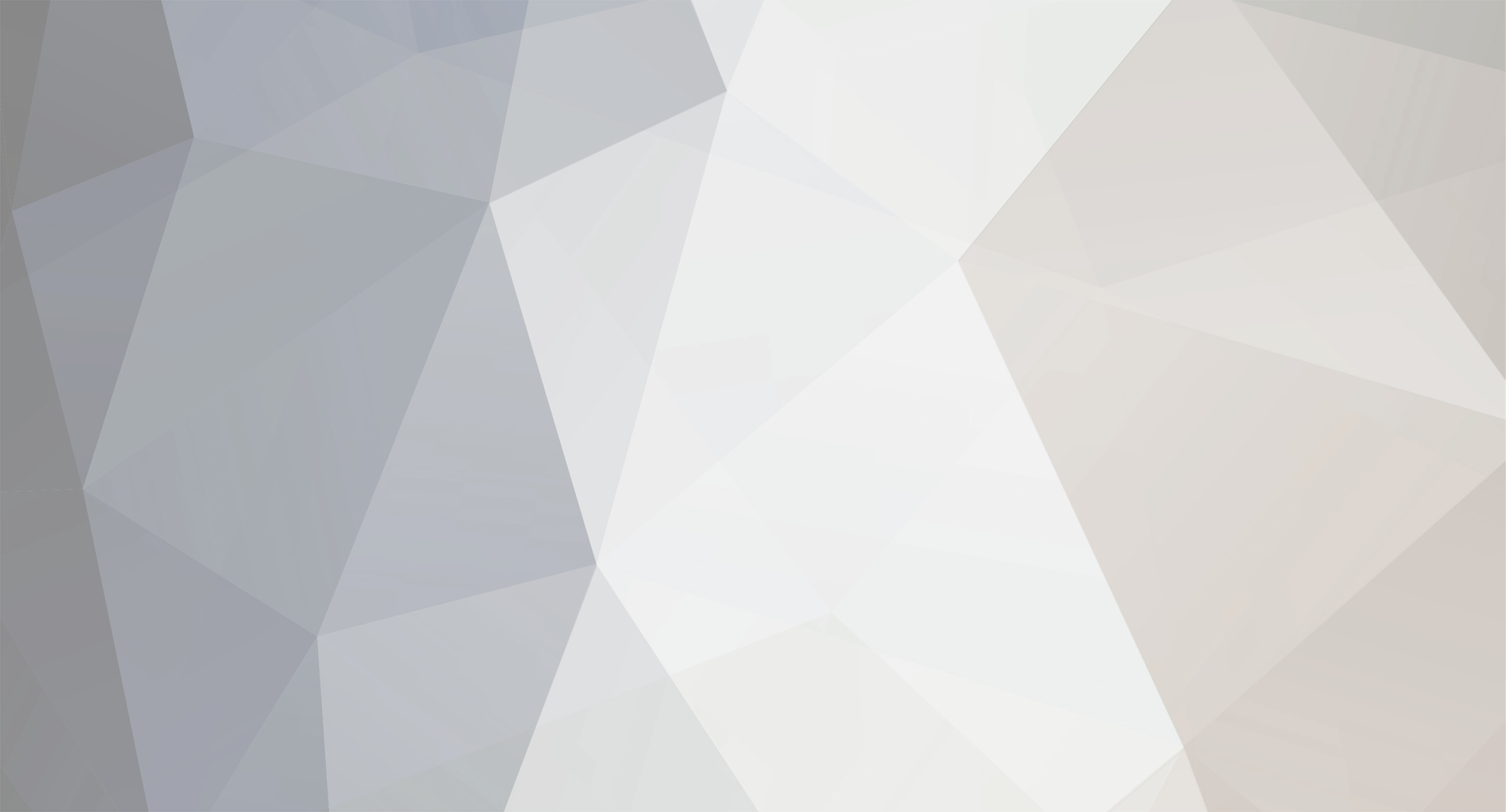
ROBERT BURLACE
Members-
Posts
51 -
Joined
-
Last visited
Never
Content Type
Profiles
Forums
Blogs
Gallery
Calendar
Downloads
Everything posted by ROBERT BURLACE
-
Cheap Chinese Laser Cutter
ROBERT BURLACE replied to ROBERT BURLACE's topic in Gadgets and Electronics
No need to generate a Gcode as such with Lightburn. It can talk directly to your laser using gbrl. Inkscape can save and open dxf, Dwg, svg, pdf, amongst others. -
Cheap Chinese Laser Cutter
ROBERT BURLACE replied to ROBERT BURLACE's topic in Gadgets and Electronics
My experience with benbox lasted all of 30 seconds when I realised just how useless it probably was. It is really a program for etching rather than cutting but the UI is terrible. Lightburn is fairly intuitive and allows you to do quite a lot. I do mainly use it for running the cutting, while Inkscape helps me to draw, design, take measurements, etc. Honestly they do everything between them that I think we could wish for in doing what we do. Try the Lightburn free trial. No changes to your hardware, no. I presume you have done all the initial trouble shooting.... wire connections etc? Were your stepper cables connected and tidied away securely? Possible the laser has cut one if not? -
Cheap Chinese Laser Cutter
ROBERT BURLACE replied to ROBERT BURLACE's topic in Gadgets and Electronics
Ahhh Ok- not sure how much of a difference it will make to your overall cutting time, but if you drop cutting speed down to something more like 120-180mm/minute it takes fewer passes. -
Cheap Chinese Laser Cutter
ROBERT BURLACE replied to ROBERT BURLACE's topic in Gadgets and Electronics
Additional thought- the fumes from MDF are not pleasant or good for you. I would suggest a swap for a piece of softwood ply for your waste board when you get round to it. Still not great but the resin in mdf is mean stuff. -
Cheap Chinese Laser Cutter
ROBERT BURLACE replied to ROBERT BURLACE's topic in Gadgets and Electronics
Posted by chris larkins on 25/10/2019 11:33:32: Success, I did as Robert suggested and tried again but this time raised up on 8mm rails, this time the parts dropped through once cut. Great stuff, glad it worked for your Chris. How many passes were you down to? What software are you on? If using Lightburn there is a setting in the device settings called “smax” this seems to default to 250 but can in fact be set to 1000. It controls the maximum power of your laser. The power on cut settings is relative to your smax setting. You may not be getting what you think is full power. Where did you find the plan? I do like Peter Miller’s models. -
Cheap Chinese Laser Cutter
ROBERT BURLACE replied to ROBERT BURLACE's topic in Gadgets and Electronics
A small blower will definitely help I use a pond air pump and machine lubricant hose - the fan behind probably isn't directional enough to clear debris from the cut path. In addition, try raising your material off the cutting bed. I use 10cm long pieces of aluminium angle. Air is a better insulator than wood, so will stop some of the energy being conducted out of your cut piece. In addition it will reduce the distance from the laser to the piece, increasing the intensity of the beam (assuming you can focus it at that distance). -
Cheap Chinese Laser Cutter
ROBERT BURLACE replied to ROBERT BURLACE's topic in Gadgets and Electronics
Thanks Allan, that’s what I thought- just nice to have confirmation. It’s easily done with the laser cutter. Rob -
Cheap Chinese Laser Cutter
ROBERT BURLACE replied to ROBERT BURLACE's topic in Gadgets and Electronics
Hi everyone, Sorry for my inactivity for a couple of weeks, the rugby has meant I haven't done much. How are those of you who are trying it out getting on? Setup instructions are a little vague but I found youtube to be my friend. I think we're all pretty technically minded so you won't struggle with it. Take care not to crack any of the acrylic. Belt tensioning with the stock parts isn't very good....there are alternatives available for anyone with 3d printers, or ooznest.co.uk are pretty good. A bit of an update on my spitfire... I tried several ways to build the wing centre section and finally settled on this. The ribs on the plan are weak at exactly the point the undercarriage mounts. With some dense XPS and laser cut ribs I hot wire cut the centre section, which will have spars and a 2mm balsa skin. Planning to router away and install the U/C mount in the next day or so. This opens a new problem to solve around wing joining. I think I will fix the centre section in place permanently, making the work around the fairings easier. I am thinking that I will use a tube through the middle to join the outer sections - any suggestions on getting the dihedral right with this method? Bending the tube (only possible with aluminium?) or displacing the joiner holes on the ribs? -
Cheap Chinese Laser Cutter
ROBERT BURLACE replied to ROBERT BURLACE's topic in Gadgets and Electronics
**Update** I have started cutting parts for my spitfire. Using 3 and 4mm poplar ply. The plan calls for a mix of 2 and 3mm liteply, but I hate the stuff. My spit will be slightly larger than the original plan too (1500 vs 1200mm). Most of the parts were cut out nicely but a few held on - presumably where adhesive was a little thicker. I have slowed the cutting speed down slightly for subsequent cuts which seems to have fixed the problem. Test fit on a few pieces to check that the tabs all go together - a tiny bit of sanding but that's all. They will all be cleaned up properly before the final assembly. A few of the other formers cut out and ready to go. I don't think I will set off multiple pieces on the same cut again. Some wing ribs I was cutting last night went wrong for some reason and all of the following parts were affected, wasting a big chunk of the ply. It's easy enough to set them off individually and position them to minimise waste anyway. -
Cheap Chinese Laser Cutter
ROBERT BURLACE replied to ROBERT BURLACE's topic in Gadgets and Electronics
Posted by chris larkins on 30/09/2019 11:37:25: Thank you Rob, I am going to download some software whilst I am waiting for it to arrive. How would you go about getting a plan onto your pc? I have an A4 scanner which will be ok for smaller ribs and formers but large wing ribs or a fuselage side will be too big for my scanner. Would a print shop be able to scan a plan and turn it into a pdf? Also for something like a long fuselage side that is too big for the engraver is there a simple way of adding some sort of finger joint in the software to join / align 2 pieces of wood together such as in this picture? Hi Chris, Scanning plans at full size, I think the print shop option as recommended above is probably your best option. But before you spend the money check and see if the plan you have is already done here: www.aerofred.com Or here www.profili2.com You may save yourself a few quid. If its a magazine type freebee plan, you could cut it into A4 sheets and piece together using software without too much difficulty, but it wouldn't be as accurate I don't think. I have never considered making finger joints because I am able to cut full length balsa sheets and anything up to about 1100mm long. However, I have made a few small boxes using a plugin (or extension as they call it) on Inkscape. Perhaps one of the box jointing options would work? There may be better alternatives available though, so don't quote me on that! https://github.com/paulh-rnd/TabbedBoxMaker Rob -
Cheap Chinese Laser Cutter
ROBERT BURLACE replied to ROBERT BURLACE's topic in Gadgets and Electronics
Posted by chris larkins on 30/09/2019 00:10:04: I just ordered one of these, 50x65 engraving area and with a 3000mw laser, worked out at £117.28 inc postage and insurance. LINK Good stuff Chris, by the looks of it, this should be expandable should you wish to make it larger in the future. Ask away if we can be of assistance in setting it up or using it. Rob -
Cheap Chinese Laser Cutter
ROBERT BURLACE replied to ROBERT BURLACE's topic in Gadgets and Electronics
Posted by James Green2 on 27/09/2019 17:51:25: I can only second the advice given by Robert. I had to buy a replacement control board for my machine as the first packed up. I went for the Eleksmaker and it seems good quality. My laser is a 5500mW, I don't know if this is good or bad or indifferent, but I went bigger thinking to would cut thicker wood quicker. The trick with these machines is to focus the laser correctly, this is the secret to nice clean cuts and thus nicely fitting joints. You will have to learn to do this a lot, for different thicknesses of wood. Robert, is that the Dave Phillpots Spitfire IX? If so, from what I have seen this is a lovely looking spitfire! Regards James Yes it is- I’ve had it on my computer for a while now. Cutting the parts by hand was the only thing preventing me getting going with it. Wouldn’t have managed it by hand. The laser has done a beautiful job though. I’m away this weekend but will post pictures when I get back. I’m planning on finishing it like the silver spitfire that’s flying around the world at the moment. I will probably go 5500mw if/when the 2500 packs up the extra power would be good for getting through ply a bit easier especially. -
Home Made CNC/Laser Cutter
ROBERT BURLACE replied to Geoff Gardiner's topic in Build Blogs and Kit Reviews
Nice one Geoff. It shouldn’t be an issue with screw drive steppers, and your corners look pretty solid, but might be worth considering that some flexing of the frame may take place with the cnc router. I have seen some people do similar with belt drive and it hasn’t worked brilliantly- the bit wonders quite a lot resulting in wobbly straights. -
Cheap Chinese Laser Cutter
ROBERT BURLACE replied to ROBERT BURLACE's topic in Gadgets and Electronics
Posted by Erfolg on 27/09/2019 14:52:29: It is not clear to me if the two links are to machines that will cut ply and balsa? Also how can you tell if the machines can be adapted to 36" balsa wood? Typically what will the postage be? The Eleksmaker A3 is what I use. It can cut balsa, poplar ply, liteply and birch ply. it runs on a combination of 20mm and 40mm v-slot aluminium extrusions. These can be purchased at pretty much any length you could wish for so you could make your cutter any size you want. Mine is sized for sheets of 300x900 ply, knowing that would be the biggest i’ll cut. i think postage was free when I ordered from eleks directly too! Banggood postage prices are generally reasonable. -
Cheap Chinese Laser Cutter
ROBERT BURLACE replied to ROBERT BURLACE's topic in Gadgets and Electronics
I use Mac OS and have had no issues with either bit of software. I had a cheap windows laptop spare which I run the laser off permanently now because it’s not much use for anything else. Leaves my Mac free to work on other things during long cuts. Geoff, I can only comment on the eleksmaker. There seems to be good support for it. I do remember reading that the more powerful laser on cheaper ones is actually just being run at higher currents, which could lead to premature failure and safety issues. -
Cheap Chinese Laser Cutter
ROBERT BURLACE replied to ROBERT BURLACE's topic in Gadgets and Electronics
**LINK** this is available on banggood as well. I bought mine direct from the maker and it was here within 3 days. additional parts for the extension to the cutting area are from ooznest.com be award that there are some imitation machines out there, particularly on eBay. Cheap and Chinese seems to have been ok so far but not sure I would trust a cheap Chinese imitation of a cheap Chinese machine! -
Cheap Chinese Laser Cutter
ROBERT BURLACE replied to ROBERT BURLACE's topic in Gadgets and Electronics
Hi Geoff, no problem and you raise a valid point about safety. yes- plans are pretty widely available. The aerofred and profili websites have been my main sources so far. They are variable in quality, by there are some gems there. There is also software that will convert a pdf to cad formats. I am yet to test, but if it works well, any model you can find a plan for would become possible. Perhaps others may be able to comment on that. I may one day try designing something myself- I want some of my physics and engineering students to enter the payload challenge this year so it might be a good opportunity. Rob -
Cheap Chinese Laser Cutter
ROBERT BURLACE replied to ROBERT BURLACE's topic in Gadgets and Electronics
The first image shows the plan on Inkscape. A useful bit of free software for dealing with cad plans. Here you can make simple changes very easily. I use the ruler tool a lot to check measurements against the plan which I have already had printed at 100% The templates have already been nicely laid out, but not for the 300x900 ply I have. I create a new document with the dimensions of the material and copy and paste plans into it - check orientation to grain and ruler tool to double check dimensions. Below is Lightburn, which I use to control the laser. You can see my 300 x 900 material sheet and the outer black line is the bed of the cutter in plan view. The controls on the right manage the power and cutting speed. The laser is meant to be an engraver so it spends most of its time at 100%. I found the following cut settings work nicely so far: poplar ply at 5mm/sec 1 pass per mm of material birch ply at 2mm/sec 1 pass per mm of material Balsa (medium) 10mm/sec 1 pass per mm of material. This might seem slow, but look at the cutouts on the plan and consider the time taken to do them by hand or on the bandsaw/scrollsaw I will set this sheet off tomorrow after work but I estimate about an hour for all fuselage formers in poplar.