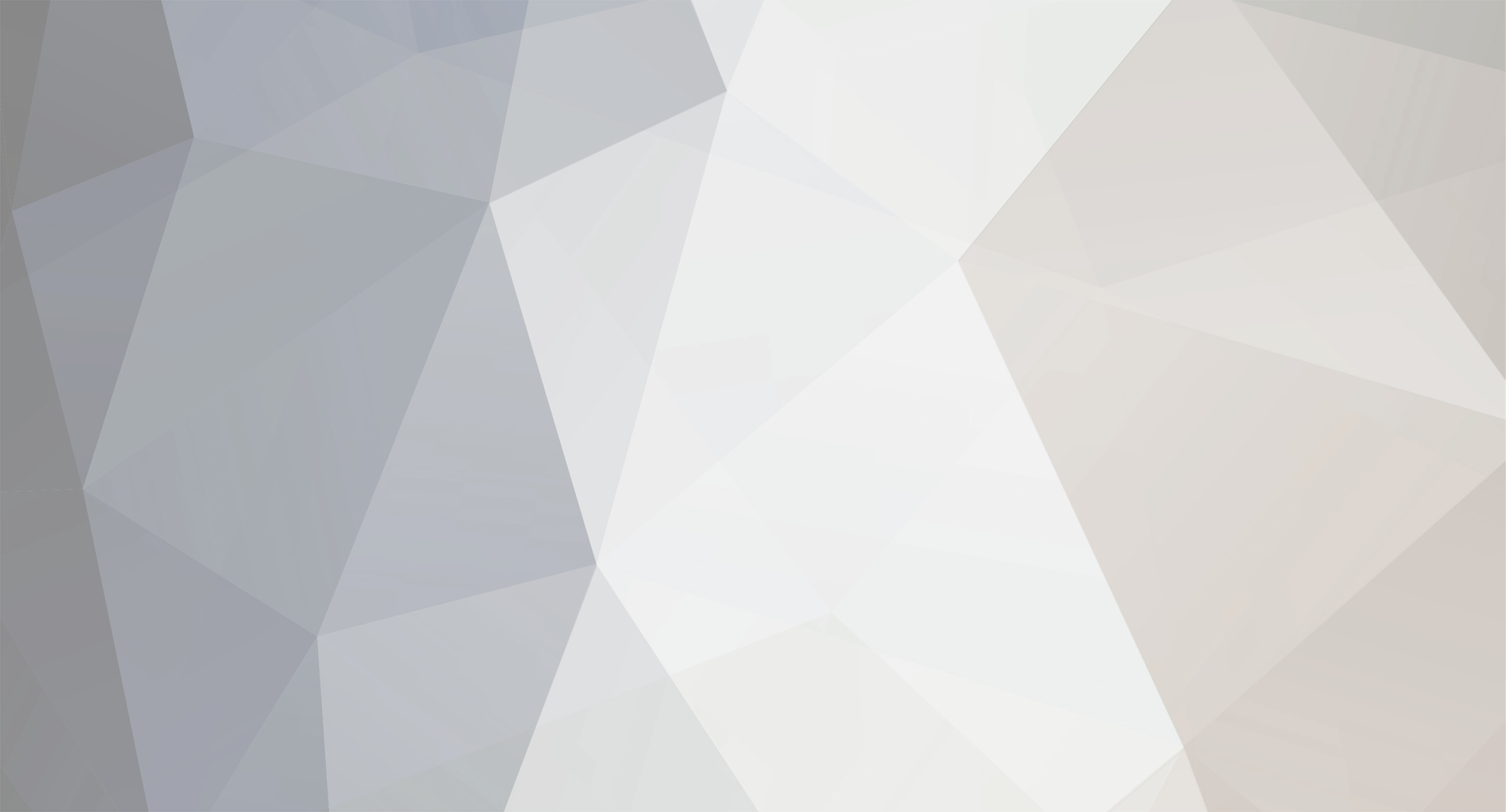
ROBERT BURLACE
Members-
Posts
51 -
Joined
-
Last visited
Never
Content Type
Profiles
Forums
Blogs
Gallery
Calendar
Downloads
Everything posted by ROBERT BURLACE
-
Cheap Chinese Laser Cutter
ROBERT BURLACE replied to ROBERT BURLACE's topic in Gadgets and Electronics
I agree, but people still get stung by those things is when they don’t follow a set of safety rules. A friend of mine lost a finger using a table saw- it just so happened to be the one time he didn’t have the guard in place. Same with a laser. The beam points straight down so you can’t accidentally look down it’s length, having a non-reflective cutting bed cuts out the risk of reflection too. But I still wear safety glasses at all times! Even on low power! An enclosure with extraction is a good idea and I will definitely be adding it soon. Im just preparing some cut files for those who are interested. I will post some pictures later on. -
Cheap Chinese Laser Cutter
ROBERT BURLACE replied to ROBERT BURLACE's topic in Gadgets and Electronics
Posted by Alan Gorham_ on 25/09/2019 15:25:44: Hi Robert I just wanted to say thank you to you for starting this thread. It is very interesting to see see your results using simple and low-cost equipment. I have always hand-cut parts for my models, but I have had a CNC vinyl cutter that I use to make paint masks for over 10 years now, so perhaps laser cutting could be my next move. I hope you do update this thread with future progress! Thanks Alan, i looked around and couldn’t find a similar thread, so thought I would set one up. I’ll keep updating as I go! -
Cheap Chinese Laser Cutter
ROBERT BURLACE replied to ROBERT BURLACE's topic in Gadgets and Electronics
Posted by Geoff Sleath on 25/09/2019 16:22:08: We used to use lasers as part of various measurement techniques at work (I've been retired nearly 25 years now). I was never very directly involved but several people in our department were and we had a Laser Lab where experiments and designs were tested. This was simply a partitioned room with no windows and a door lockable from the inside. The reason was to prevent anyone entering without eye protection when lasers were being operated. Lasers can cause serious (and permanent) eye injuries. I just wonder how safe laser cutters are. At work, anyone dealing with lasers was required to have an eye test before they worked with them. This was to protect the company from claims that any eye problems were caused at work rather than for the benefit of engineers. Anyone operating a laser wore special goggles. A laser cutter is an appealing idea but what measures do the suppliers suggest should be taken by users - particularly as regards eye protection? Geoff Geoff, the way way I see it, we have a hobby where we have spinning blades, carry highly volatile fuels in our cars and charge batteries containing lithium in our homes. Done safely, although they pose a hazard, the risk is minimal. The same applies to any form of cutting, including lasers. The kits I have did come with eye protection- I upgraded and bought a pair that I was sure we’re rated for the wavelength of the laser. MrsB isn’t allowed in the shed, so someone walking in on it won’t be an issue. Setting up a simple set of procedures can manage that risk to a level where it is acceptable, as was done in your workplace. I wouldn’t let the risk put you off- it can be managed quite easily. Rob -
Cheap Chinese Laser Cutter
ROBERT BURLACE replied to ROBERT BURLACE's topic in Gadgets and Electronics
I can't comment on the life of the laser, but hopefully if I manage to keep the thread going, it will give you a good idea. I follow a group of users on facebook who give them pretty heavy use, some even in small businesses. They will, inevitably burn out I am sure. But all cutting tools go blunt... They are relatively inexpensive to replace like for like and the kit can be upgraded to more powerful diode lasers and have even seen CO_2 lasers used. Nice tip with the card - it would allow a mock up before committing to wood. I am always careful to measure cad drawings against plans before cutting....its the same as making any cut...measure twice....you know the rest. I have a big order of wood from SLEC due tomorrow, so plan to get going with a lovely mk9 spitfire I have been wanting to build for a while now, but didn't have the patience to cut the parts! Will keep you updated. Rob -
Cheap Chinese Laser Cutter
ROBERT BURLACE replied to ROBERT BURLACE's topic in Gadgets and Electronics
Thanks for sharing James. it looks like you use yours for exactly what I intend mine for. I tried the Bencut software but just found that I got on better with the other two bits of software. There is is an option to add z-axis now for cutting thicker materials- it would allow the focal point to move down between passes. It should make cleaner cuts on ply especially. -
Cheap Chinese Laser Cutter
ROBERT BURLACE replied to ROBERT BURLACE's topic in Gadgets and Electronics
Hi Kevin, Thanks for the tip on Wintopo - I had seen a piece of software called scan2cad which seems to do a very nice job, but it isn't cheap. I will give it a go. As I said at the top of the thread - there is already lots of very good cad drawings around, but the ability to convert jpg opens up even more possibilities - does it work with pdf too? Yes, my post was a little inaccurate about the fumes - I should add that when cutting, I set the cutter up, set off on its way and leave the shed while it does its thing. I will build an enclosure that has extraction capabilities when I get chance to, allowing me to work while parts are cutting. Thanks Rob -
Cheap Chinese Laser Cutter
ROBERT BURLACE replied to ROBERT BURLACE's topic in Gadgets and Electronics
I should point out that my wife is yet to use it too..... -
Cheap Chinese Laser Cutter
ROBERT BURLACE replied to ROBERT BURLACE's topic in Gadgets and Electronics
In terms of preparing plans I am currently working between two bits of software - although not a perfect solution, it seems to work. The first is Inkscape - a free bit of relatively advanced CAD software which allows you to import your parts from a DXF (or other CAD file) and arrange parts onto sheets. I create a document the same size as a sheet of balsa, or ply that I am cutting on to, import parts, then arrange onto the sheet, making sure that they are oriented correctly for grain directions and as economically onto sheet as possible. Saving these files as .svg files allows the next piece of software to do its job... The second piece of software, Lightburn isn't free, but think it costs about 40 quid - I am still on the one month free trial and exploiting a bug that stops it counting down if you don't close it ( I will buy one day but i like to test stuff thoroughly before committing). This software controls the speed and power of the laser cut and creates a g-code which is the instructions for the controller to give x,y coordinates to the stepper motors that move the laser. -
Cheap Chinese Laser Cutter
ROBERT BURLACE replied to ROBERT BURLACE's topic in Gadgets and Electronics
A balsa rib - cut before I installed the air assist which really helps clean up cut edges. Air assist - fed by a small pond air pump Clean cut in some sample bits of 4mm ply - leaves a bit of a burnt edge but sands off easily enough and have had as bad on short kits purchased online before now. And this is the setup - the bare aluminium rails are stock from the kit, i extended the cutting area using the black ones to 1100mm- giving a workable cutting area of about 400mm x 1000mm -
Cheap Chinese Laser Cutter
ROBERT BURLACE replied to ROBERT BURLACE's topic in Gadgets and Electronics
Hi Graham, Yes that's right - the rails are available online in pretty much any length you can wish for, the rest of the parts are as they are in the kit. Just sorting out some photos. -
I recently bought an "eleksmaker" 2.5W laser engraver from bangood, partly for my wife to use for her wedding and personalised gifts business, but partly out of curiosity for model building. The laser comes as a kit and parts are readily available to expand as necessary. I have built mine to accommodate standard sheets of balsa and 300x900mm sheets of ply from SLEC. I have carried out a few tests so far and it has proved capable of cutting up to 4mm birch ply without too much fuss (although slowly), poplar, liteply and balsa with ease. Now - I am USELESS with a scroll saw. The other day, I used the laser to cut out some fuselage formers for a Cap232 that I am building and the accuracy and speed that i came out with them was far, FAR better than i can achieve by hand. Using the laser has the advantage of no balsa dust and as well as ventilation is good, no fumes. The full set up has cost me less than 250 quid and I have already cut parts for two sets of plans for winter build projects, so has probably paid for itself already. I don't plan to design my own models, there are plenty of good CAD drawings around online to keep my busy for a while. I will post some pictures and updates as they happen for anyone who is interested.
-
Thanks Geoff, so I built and very loosely fitted the motor mount today- that’s the easy bit as long as you can measure and have a bit of patience for adjusting nuts to get the prop adapter in the right place. It will all be snuggled up and thread locked in place when I’m happy. I have just tried to determine battery placement on the CG machine. The manual states that CG is 100mm aft of the leading edge at the root. Using this measurement places the battery almost at the front of the cowl. I remember reading a previous post about the chippy tending towards nose-heaviness. What position did you set your CG at? I’m using a 5s 5000 mah battery and setup that has served me well with similar models. It’s lighter than your 6s setup, but seems to be too big of a difference in placement to be accounted for by the mass of the battery. thanks in advance Rob
-
Hi all, sorry to dig up a long-quiet thread, but I have just started a conversion myself and wanted to say thank, you for all of the ideas that have been shared here as they have been an invaluable reference. I am not new to electric conversions, but this one is slightly trickier than hangar 9 ARTF and similar models because it was built with only I/C in mind as far as I’m aware. Geoff- sorry to hijack your thread, if you don’t mind can I share some photos and get your thoughts as I go? Thanks Rob
-
Hi Luccaaa thanks for the reply. That’s what I thought. I was actually planning on building my own electric conversion kit for it and making a similar electric installation to what’s on my wot-4 following the Chris Foss plan. cutting identical standoffs isn’t an issue so I’ll go down that route. cheers Bob
-
Hi everyone just after a bit of advice, I think I know the answer but just want confirmation. installing the motor on my new acrowot artf. The firewall already appears to have thrust angle built in. If I use standoffs all the same length and make the motor mount parallel with the firewall, will that give me the correct thrust angle, or is there any additional required. Or alternatively, does any need to be taken out for electric compared to IC? Thanks in advance Bob
-
I'm in - At what point does it stop being the Renaissance? I've been wanting to add an aerobatic biplane to my hangar for a while now. In a biplane configuration this would have a passing resemblance to a Pitts or similar. I know it's not as simple as dropping another wing on top, but is it doable? I'm moving house beforehand I can even think about another build- she thinks it's for a bigger kitchen, but the reality is that the garage is much bigger! Merry Christmas everyone.