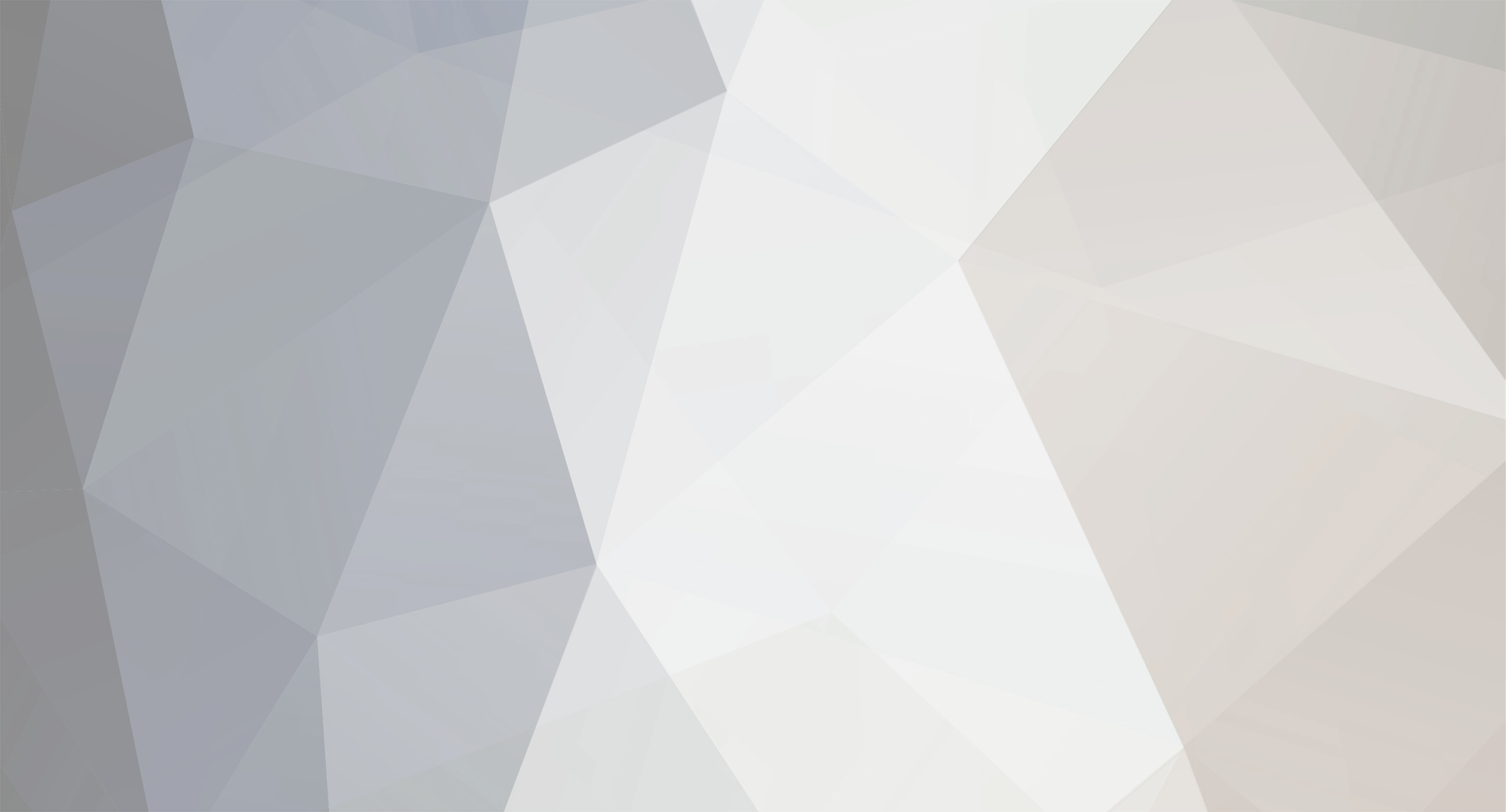
Dizz
Members-
Posts
208 -
Joined
-
Last visited
Never
Content Type
Profiles
Forums
Blogs
Gallery
Calendar
Downloads
Everything posted by Dizz
-
Posted by Erfolg on 19/10/2011 11:39:30:I was a little surprised "fly Navy", with respect to air pressure and its effects. I did not think anyone suggested that the pressure was constant. I would expect in accelerating of the air through the duct would cause a reduction in pressure as predicted by Bernoulli. Any expansion and contraction of the duct will vary the pressure, relative to atmospheric acting on the duct walls. As for the comments with respect to the fan, I do not know, yet suspect the fan is important. What is important I do not know and would be interested in a better understanding at a theoretical level, so as to be able to relate to what can be engineered at a practical level. I was using the example of the collapsing duct to illustrate that there is obviously a difference in pressures in the duct from that outside. For a unit mass of gas at constant temperature, if the pressure changes then so does the volume (hence density too). I have test stand power and efflux velocity figures for several different EDF and motor combinations which show that fan design definitely does have a bearing on the power consumed(lost) and efflux velocity. IMHO, without a wind tunnel and some pretty sophisticated instrumentation we are not going to be able to improve on what we can already achieve using basic static testing and fairly well known rules of thumb. Pete
-
I have been following this thread since it started and as you have asked what others think here goes: I don't think many of the assumptions are valid when considering modern brushless EDF power trains and this will impair your estimation process: 1. Air pressure does change through the ducting as indicated by collapsing intake ducts and exhaust ducts that press outwards. 2. In a 69mm fan at 30k rpm the blade tips have a velocity of approximately 220 mph - at 50k rpm (a fairly common figure these days with 6S EDFs) the tips are doing 368mph (M=~0.5). Drag (hence power required to over come it) is proportional to the velocity squared, so the prediction equations need to incorporate a rpm factor. 3. No allowance in the losses for how many blades, wetted area or pitch - all absorb power apparent as a "loss". 4. It is generally accepted that compressibility effects start to be noticed around 350mph - see (2). 5. Prediction results seem to be independent of airframe characteristics (drag) and intake duct geometry/length - in reality this is obviously not so. 6. In the static case intake air has to be moving into the duct: the mass of air being expelled has to be the same as the air entering the duct otherwise air propelled from ahead of the fan and out of the exhaust wouldn’t be replaced resulting in a vacuum ahead of the impeller…………….or given your measured low (tending to zero) intake velocity and high efflux velocity, the efflux flow has to be at a lower pressure than the intake (pV=constant or p1V1=p2V2– Boyle’s Law). 7. Finally………I would put money on the fact that the pressure inside your Hawk isn’t true static atmospheric pressure (probably lower) purely because of the shape of the fuselage and its relationship to the openings in it – static vents on full size aircraft are very carefully placed and carefully calibrated. Because velocities are squared, the effect of any measurement errors will be increased and lead to even greater inaccuracy. Regards Pete Edited By Dizz on 19/10/2011 01:54:14 Edited By Dizz on 19/10/2011 01:55:39
-
What is the C rating of the packs you are using? If they aren't up to the job a high current draw will drop the volage - possibly below the LVC. The pack voltage recovers when the load is removed. On many ESC these days you can set the cut-off point voltage, also what happens when LVC is reached eg hard stop, soft stop or "bliping the throttle". NB the BEC still operate regardless to provide power to the Rx and servos. Another feature sometimes associated with a hard cut is if you move the throttle stick all the way back then open again the ESC will give you enough power to achieve a landing. Pete
-
Could be the low voltage cut off on the speed controller. Was the second flight on a new pack? Or maybe the ESC has an over temp protection feature.
-
The Phase 3 F-16 will take a 70mm fan with the minimum of work and go like stink............if you can find the airframe only at the moment. Pete
-
I used the "e-mail me" link in the ad. Truth be I have too many projects waiting anyway Pete
-
No reply received to my e-mail and no post on here................. Pete
-
Matt Am interested, have sent you an e-mail. Pete
-
Well done! Looking forward to reading about the next 2 builds Edited By Dizz on 12/02/2011 17:12:07
-
I would say the Phase 3 (Ripmax) EF-16 fits your spec exactly. Plenty of info on it available on here. Pete
-
Try Giant Cod: http://www.giantcod.co.uk/edf-shafts-c-134_181.html Pete
-
To improve static thrust (helps hand launch) don't forget that there tweaks you can do to the intake - make sure the duct is as smooth as possible and the intake lip has a nicely rounded section. I know it is comparing apples with pears, but adding a rounded intake ring to a HET6904 on my test stand increased static thrust from 1.6 kg to over 2.2kg and the Watts jumped by 10% from 1266 t0 1389W. I also assume that you were both comparing installed thrust figures or test stand figures and not mixing the 2.Pete Edited By Dizz on 11/12/2010 18:12:05 Edited By Dizz on 11/12/2010 18:12:43
-
Drawing I told you about has arrived - not the factory one though, he couldn't find it. This one a scale drawing by J F Henderson. Wing plan and outer cross sections different to the Warpain book pull-out plan so now I have to work out which one is correct, Think I will start by checking against the Airfix kit. Pete
-
I swapped the stock fan in my Graupner (SAPAC) Typhoon for a 3900kV Red Cyclone last year. Installed figures I got were 575W steady state on Overlander 25C 2600 4S with 870g static thrust. I know we are comparing apples with pears, but gives a feel for the difference in the 2 winds. I actually bought 2 4300kV reds out here in Singapore on Wednesday to go in a winter project so I'm pleased to see Tim's test results. Pete Edited By Dizz on 11/09/2010 17:58:40
-
Nice one Stuey
-
1. Phoenix Model Products, Newton Abbot 2. Giant Cod 3. Phase3 EF-16 4. Horizon Hobbies
-
I didn't brand it as "really poor value" Tim, just that I think the F16 is far better. How do you assess VFM when you are in the super market doing the weekly shop? Pete Edited By Dizz on 07/07/2010 23:07:04
-
Posted by Gaz Elliott on 07/07/2010 17:07:05: However, my main question is: Why is this plane called "HABU" ? I think it maybe the link to the picture of snakes on the tail and wing....just a guess!!! Edited By Gaz Elliott on 07/07/2010 17:07:57 Ah yes, but what came first, the snake sticker or the name? Or the fact that IMHO it looks very much like the Viper jet? I think the Phase3 EF-16 v2 is far better value for money and it is scale(ish) too. Pete Edited By Dizz on 07/07/2010 18:28:22
-
However, my main question is: Why is this plane called "HABU" ? "Habu (波布?) is a Japanese name used to refer to certain venomous snakes ..." Like a Viper maybe?
-
link to RBC EDF kits: http://www.rbckits.com/shop/index.php?_a=viewCat&catId=2
-
Take a look at the RBC range, but the nature of the beast means that any "traditional" balsa/ply kit will require previous building experience. Also, all the kits I can think of are designed for wemo mini style 70mm EDF with mounting lugs. BTW, if you measure your Phase 3 unit you will find the fan diameter is approx 68mm. Pete Edited By Dizz on 28/06/2010 08:44:44
-
The WW Hawk is designd for a Wemotec Minifan or similar. It is a very nice and well made kit, but you need to have some previous experience building in balsa/ply before attempting. The Squall fan/motor/ESC combo isn't suitable IMHO. What about putting it in a Phase 3 EF16 fuselage? Just the foam parts, canopy, etc are available as spares from several vendors. I know the Squall EDF will fit - the latest EF-16 complete kits now come with the Squall 3S unit vice the previous 56mm diameter one (got a kit last w/e at Weston Park from Motors and Rotors) Pete
-
Posted by Shaun Chant on 21/06/2010 07:59:11: Cool. You do like your little edfs don't you? Yep!