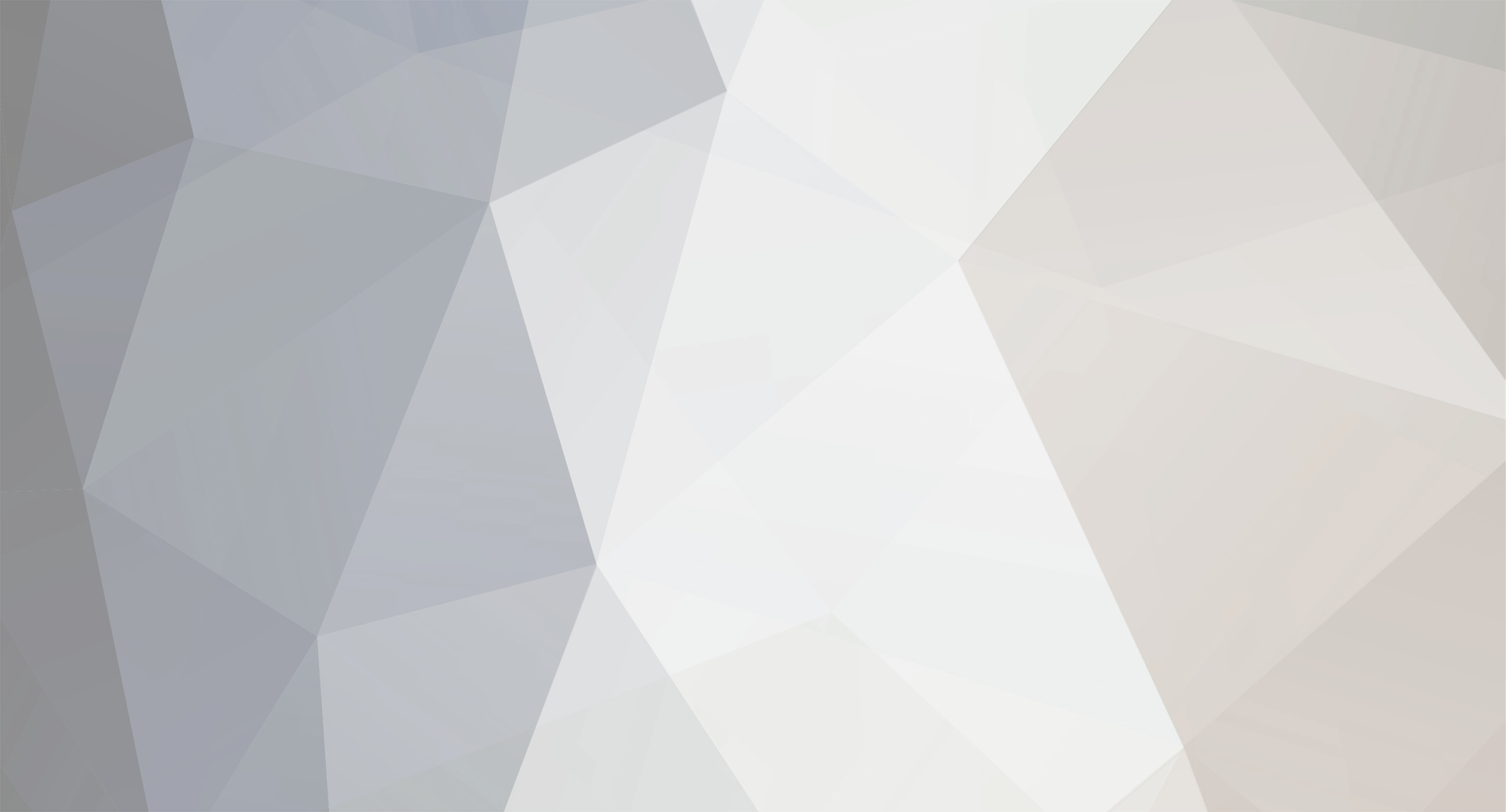
David Hayward
Members-
Posts
34 -
Joined
-
Last visited
Content Type
Profiles
Forums
Blogs
Gallery
Calendar
Downloads
Everything posted by David Hayward
-
Chargers for Cycling NiMH Batteries
David Hayward replied to David Hayward's topic in Gadgets and Electronics
Many thanks John for your reply - much appreciated. I rather suspected that any replies I received would be along the lines you have indicated. It seems that I shall probably just have to accept that technology fashions don't stay the same for ever. I too have old SM Services equipment - a Battery Master & a Battery Master 2 but, as you will know, each charge/discharge cycle has to be set up afresh each time and the max. charge rate is limited to 400 mA. -
Does anyone know of a battery charger which can cycle NiMH rechargeable batteries up to 5 times while still allowing each cycle’s discharge and charge mAh readings to be viewed once the cycling session has finished? I ask for the following reasons. I have been using an IMAX B6 (50W) charger for some years. It is actually a clone-type from China, not an original SkyRC type and is reported to have been manufactured with somewhat inferior quality components compared to the original; hence its lower price. It worked well for several years but then the cycling started to give spurious results although for just charging it is still fine. This is a Version 1 (V1) charger which, like the original IMAX B6 design, retained all the discharge and charge mAh readings for each cycle which could be readily viewed and noted once the cycling session had been completed. However, I have found that the latest IMAX B6 V2 chargers which are rated at 60W, while having some additional features, only now allow the final set of discharge and charge mAh readings to be viewed at the end of any multi-cycle operation. This does not give me any confidence that the cycling process has worked as it should, i.e. with gradually increasing discharge and charge readings with each successive cycle operation. I find this very unsatisfactory! I have had correspondence with SkyRC about this issue regarding their D100 (100W) charger and also Overlander who market a seemingly identical charger but with their own name on it. The software seems similar to that of the IMAX B6 and they have also moved from V1 to V2 designs which I am told now have the same limitation as the IMAX B6 V2, i.e. only the final discharge and charge mAh readings are now viewable following any multi-cycle cycling sessions. More disappointment! Any advice on what battery chargers, if any, are currently available to meet my specific requirement would be much appreciated. I fly a range of range of ic model planes and currently only use NiMH rechargeable batteries for Tx and Rx purposes although would ideally like to have the flexibility to handle LiPos in the future should I eventually move into electric flight.
-
I ordered some model aircraft accessories worth £39.45 including P&P on-line from RC Model Store on the 5th July '22 (https://rcmodelstore.co.uk) and paid with a credit card via PayPal. The firm is based in Stotfold, Herts. I have used them successfully once before. The order comprised a JP electric fuel pump and three remote glow cable assemblies (1 Fastrax type with metal glow plug connector and two Logic types), i.e. all standard readily available items. My on-line account states that the items are 'On Order with Suppler (paid)'. When I placed the order, some items were said to be in stock while others were said to be available from the supplier within 1-2 days. However, when I phone the company to check progress, all I get is an answerphone message saying their staff are not free to answer the phone right now and would I leave a message or send an e-mail. I have left numerous messages in recent weeks requesting that they contact me and have also sent e-mails but have received no response whatsoever. Does anyone know if RC Model Store are still in business? I am not sure what I can do next. At present, RC Model Store has taken my money without delivering the goods!
-
OK, all is clear - thanks Martin.
-
Martin M - Thanks for your reply. I have been able to access your 52 Atom Special photos by simply clicking on '895 photos' below your name/photo of yourself and going to the top of page 3, Looking at the ones showing a close-up of your home-made rotor heads, it looks as though pitch control is via a brass hinge parallel with the line of the fuselage whereas roll control at 90 degrees would seem to be below this via the lowest bolt which is connected through the top of the mast (rather than a separate rotating link above a rigid connection to the mast, as in the Hobby King C30 rotor head design). Have I got this right?
-
Steve J 2 - The plan arrived in yesterday morning’s post. Very many thanks indeed - much appreciated. I have no previous experience of building or flying autogiros, only sizeable fixed wing ic models and a couple of small indoor electric ones (Parkzone Night Vapor and a mini helicopter). I note the Hobby King C30 head (an obvious first choice of head unit for the Atom as it is part of the original Richard Harris design) is once again out of stock, both on the HK and coolwind websites. Could this still be the situation in several months’ time I wonder? In case of long delays with the C30 becoming available again, can anyone advise me what are the best tried and tested commercially-available alternative in-stock head units for the Atom - incorporating roll and pitch, and not just roll which would require designing in an elevator (too radical for me I think as I’m new to autogiros). I have read through this long thread a couple of times and note (with my head spinning) that there is passing reference to one or two commercial options mentioned including a laser cut wooden set of head parts (e.g. ref. R Harris on page 11) – but where can the latter be obtained and are there any instructions as to how to put the bits and pieces together and what bolts to use, etc? Also, now I have the plans, clearly I can cut my own wooden parts for the basic model but, out of interest, where can the set of laser cut parts be purchased if required, as illustrated for example, on page 67? And, is a pre-formed u/c available anywhere? I see on page 9 that there is mention of an Atom wood pack including fibreglass head plate and pre-formed u/c but who sells this pack nowadays? Sorry if I’m going over old ground which I’ve missed in the thread but would appreciate advice. David H
-
Onetenor - all noted, thanks. Steve J - many thanks; I'll confirm receipt when the plan arrives. Seasons greetings to you too. David H
-
Steve - My goodness, that's very good of you - many thanks. I'm quite happy to reimburse you for printing & P&P costs by say cheque if you care to give me your address. Alternatively, I can make a Christmas donation to a charity of your choice. My address is: The Nest South Town Road Medstead Alton Hants GU34 5ES David PS According to local legend, my house is made of leaves & twigs – but I’m glad to say that there is plenty of space for my large model-making room!
-
Can anyone suggest how I can get hold of a copy of the Atom Special autogyro plan which was issued as a freebie with the RCM&E Autumn 2014 Special magazine in support of the quick-build article featured in that issue. Unfortunately, I didn't keep my copy of the plan at the time but now, some 3 years on, I'm interested in tackling the build. The magazine puiblishers (MyTimeMedia) tell me that they can only handle such requests going back 6 months. They suggested I try Amazon or E-bay but unfortunately, the Autumns 2014 magazine + associated free plan does not seem to be currently available through either of these sources, although many other issues are. Anyone got any other ideas? I still have my copy of the magazine in question - it's just the Atom Special plan I'm after.
-
Thanks everyone for all your additional comments – all noted. Martin H – Re your Irvine Z-bender experience, yes, all a bit odd. I have checked by test Z-bends which I produced when I had my Irvine Z-bender. Taking the best of the bunch, I find I can just about be persuaded that I achieved 1.5mm deep bends on one or two of them (see photo with a ruler now included), better than the 1mm I’ve previously quoted, but, they still don’t sit at all well in a 2mm thick standard servo arm. I could of course add a small extra bend to bring the main part of the pushrod wire to the horizontal but I see that as a compromise too far. I certainly couldn’t achieve the 2mm+ Z-bend depth that you illustrate with your Irvine Z-bender. Maybe for some strange reason, I have been just unlucky with my particular purchase. However, since for my current build project, I really want to use a 2mm pushrod (M2.5 thread), I shan’t now be pursuing any Z-bender pliers option.
-
Non-ideal Z-bend test results using Irvine Z-bender with 1.6mm pushrod
David Hayward posted a gallery image in Member Albums
-
Z-bend test results with Irvine Z-bender pliers (best result)
David Hayward posted a gallery image in Member Albums
-
I have only just spotted that David Pearce 4 generated a discussion starting at 8/7/14 at 15.57.08 on this forum entitled ‘Problem with Irvine Z Bend Pliers’ which echoes my own – worth a read (NB No hyphen between Z and Bend in the title if you search for these postings). Nigel R - Yes, on studying on-line pictures of the Irvine and Prolux Z-bend pliers, I can see that the general shape of the jaws are different but, without seeing them both side by side, it’s difficult to determine any difference in the ‘Z’ dimensions within the jaws. If your Prolux pliers from HobbyKing work for you on standard Hitec and JR servo arms which, like, Futaba, are 2mm thick, I can only say that this doesn’t quite fit with the Prolux literature stating that their Z-bend pliers are only suitable for up to 1/16 in (1.6mm) wire! What’s the max. wire size as seen by the jaws of your Prolux Z-bend pliers that you have actually tried and been successful with? Ball link at both ends in my application? – hmm; food for thought. Ron Gray – Thanks, noted.
-
Thanks for all your follow-up comments. Nigel R - I am aware that the plain wire part of pushrods rods with threaded ends is slightly thinner than the threaded part so that M2 rods have 2mm gross diameter threaded ends with the plain wire part being about 1.6mm. Similarly, the threaded end of M2.5 rods have a gross diameter of 2.5mm with the plain wire part being about 2mm. See my attached photo below showing test results with the Irvine Z-bender I bought. Note that the two sizes of test rods (M2 & M2.5) described are old pieces which have had the threaded part cut off and so the plain sections of the M2 and M2.5 rods shown represent thicknesses of approx. 1.6mm and 2mm respectively. As mentioned in my original post, I couldn’t get the short middle section of the Z-bends to be more than about 1mm and so I couldn’t get either rod size to lie horizontally in a 2mm thick standard Futaba servo arm; hence, I would have the same problem with a 2mm thick metal bellcrank. Incidentally, for my sizeable biplane, I would prefer to use at least an M2.5 control rod rather than M2 as its more rigid/less flexible (this is in fact what is provided in the kit which is a ¼-scale DB Sport & Scale Sopwith Pup). Denis - the aluminium M3 clevises you illustrate are, as you say, a bit more heavy duty. To date, I have been a bit put off using this type. I imagine fitting the retaining clip when working in tight spaces within a fuselage could be a bit fiddly. Also, if I ever had to do an adjustment at my club flying field, I can see those tiny clips ending up getting lost in the grass! To pre-empt anyone who thinks of mentioning them, I originally thought of using a Kavan Z-bend coupler which can be soldered to the plain end of a pushrod (photo attached). These used to be available in two sizes – 1.5mm Z-bend with a 1.7mm ID coupler (ref. 6232) and 1.5mm Z-bend with a 2.1mm ID coupler (ref. 6230). Unfortunately though, it seems than Kavan have discontinued producing the larger size. Wilco – that’s the YouTube clip I have seen before which criticises Z-bend pliers for the reasons I have described (often producing less than ideal short Z-bend middle section lengths) and advocates the double 90o bend and final twist technique mentioned earlier by Geoff. Maybe my slight concern about weakening of the wire following the final twist is not justified? I’ll experiment a bit more with this option. At the moment though, I think I’m tending towards running with the sleep keeper option for attaching the elevator control rod to the bellcrank, with a clevis at the servo end. Use of a standard steel clevis, locking nut and coupler in place of a sleep keeper is of course a possible option. However, a clevis + coupler at the bellcrank/plain wire end of the pushrod and a clevis on the threaded end at the servo would not work so well for my current application - the control rod needs to be bent not far from the centrally-positioned bellcrank in order to reach the elevator servo mounted on one side of the fuselage while avoiding too sharp an angle.
-
Z-bend test results with Irvine Z-bender pliers
David Hayward posted a gallery image in Member Albums
-
Very many thanks for all your prompt responses – all noted. Geoff, Tom & John - the HobbyKing website states that their Z-bend heavy duty pliers, which physically look similar to the Irvine ones I originally purchased, can handle wire up to 1/16 in. (1.6mm); this is the limitation I have already highlighted. HK’s statement doesn’t therefore give me any confidence that their pliers will handle M2 (2mm) and M2.5 (2.5mm) wire. Dennis & DaveyP - I had overlooked the swing keeper possibility, not having used that option on any model for a long time and since I have only been used to using shortish ones which would not be so suitable for the size of fittings I plan to use on the sizeable ¼-scale biplane I’m currently building. However, the longer keeper type you show in your photos, which I see look like SLEC ones (?), would be fine - so thanks for that. Geoff – Using a vice, I had already tried the technique you describe re creating two 90o bends then twisting the second bend to bring it into line with the first, having spotted a YouTube video clip demonstrating it on-line. However, I was concerned (perhaps unnecessarily?) that I had weakened the wire at the second bend due to the final twisting stage. As for your warning about using clevises at both ends of the control rods, I have used that technique for many years on several models without problem but always include nuts at each end tightened hard up to the clevises and check them at least before each day’s flight. This approach has always worked for me. For my current model build, I was planning to use a clevis at the servo arm end, then a short control rod (M2 or M2.5) to a bellcrank with Z-bend connection and then a closed loop wire system thereafter down to the elevator – hence my interest in Z-bend pliers which would be a nice tool to add to my collection provided it can cope with the wire size range I have quoted. However, if I can’t locate Z-bend pliers which I can be sure will do the job, the swing keeper idea is certainly a good alternative – it’ll certainly of course be cheaper!
-
Please can anyone advise me on a reliable make of Z-wire bender for fitting a control rod to a 2mm thick standard Futaba servo arm or equivalent using M2 & M2.5 (soft wire) control rod. I recently purchased an Irvine Super Z-Bend Plier with Navigating Pin T-ZB01 which proved to be totally inadequate. It produced Z-bends easily enough but the short middle section of each Z-bend I formed was only about 1mm which meant that the control wire would not lie horizontally when the Z-bend was inserted through the selected slightly-enlarged hole I had created in the 2mm thick servo arm. I subsequently returned the tool to the supplier with photos to illustrate the problem and was promptly given my £10.75 back. Looking at other similar makes of Z-wire benders where there is a bit more specification detail provided, e.g. as offered by Prolux, the caveat often quoted in the small print is that they are only suitable for wire thickness up to 1/16 in., i.e. approx. 1.6mm, which is no good to me. Another option is the Du-Pro E/Z bender wire-forming tool, Model DB 481 with two different sizes of dies included to cover wire thicknesses in the range 1.6 to 2.4mm (Du-Pro also offer Model DB480 for 0.4-1.2mm wire thicknesses). However, bearing in mind they emanate from the USA, UK costs seem exorbitant at around £35, especially as I only need to make one Z-bend for the current model I’m building. Also, customer reviews for this product on Amazon are not particularly encouraging, suggesting that the product is not man enough, particularly at the upper end of its design wire thickness range – the orange plastic element seems prone to breaking or the plastic surrounding the metal die is said to become subject to wear, turning a square hole into a round one such that the product soon becomes useless. So, are there any other options I can explore for M2/M2.5 wire? I have tried creating the required Z-bends manually but find it is impossible to get enough force with hand-held long nosed pliers and achieve a good Z-bend which gives minimal slack once fitted to the servo arm.
-
Many thanks for all your responses. These give me the confidence to go ahead with the tailplane end mods as well as the cowl mods I have described. I have reservations about going further though, i.e. thinning the wing rib profile in view of the extra work required, particularly if undercamber is included which is moving into virgin territory for me and would make covering the underside more tricky. Also, I won’t be looking to achieve extreme aerobatics with this model! Like Jon (Laser Engines) says, so long as the model looks like a Pup ‘at 10 paces’, I shall be happy! As for the effect on C of G position following cowl + tailplane end mods mentioned by Donald Fry, all the C of G calculators I have come across to date only seem to allow plugging in of wing dimensions, not those of the tailplane (and fuselage) as well - am I missing something? Post-mods, I was thinking of simply sticking with the original design’s (safe) C of G of 122mm back from the top wing LE initially, as indicated on the kit’s fuselage plan, but mindful that other threads on this subject on this Forum (Feb 2013) have talked of up to 150-155mm, or even 162mm back from the LE, albeit with expo built into the elevator control set-up; moving the C of G back of course also helps to minimise extra lead ballast at the front.
-
As I have previously mentioned under a discussion about ‘grippers’ versus ‘turnbuckles’ for the rigging flying wires, I am in the early stages of building a DB Sport & Scale ¼-scale Sopwith Pup with an inverted Laser 155 4-stroke. As has been previously highlighted at http://www.ivyandmartin.demon.co.uk/pup_review.htm, as a flying model, it has an excellent reputation but, as a scale replica, it leaves a lot to be desired - 1) the nose is too long due to the long-chord aluminium cowl which has no doubt been done to minimise the amount of lead ballast the model may need to carry to achieve a satisfactory balance; and 2), the tailplane and fin/rudder are significantly oversized. Item 1) can be rectified by cutting the excess material off the back of the cowl (approx. 15-20mm say), mounting it immediately ahead of the front-section struts without the original front bulkhead, or at least with the centre of the latter cut right out. A new ply former can then be set inside the fuselage sufficiently far back to accommodate glass-reinforced engine bearers or, depending on the engine selected, to radial-mount the engine with the prop-driver just forward of the cowl. This approach also does away with the kit’s integral ply fuel tank boxing and integrated ply engine bearer with built-in 3 deg. downthrust. However, with a new ply bulkhead set back, the latter downthrust can be readily achieved by slightly angling the bulkhead during its fixing. Arguably, the downside of adopting the above cowl/bulkhead position modification is that more lead ballast will be required to achieve the require balance. However, in view of the long fuselage (moment arm) behind the wings, this latter problem can neatly be minimised by addressing Item 2), noting that a small decrease in tail weight = a much more significant reduction in upfront lead ballast which will otherwise be needed, particularly for a short-nosed model - i.e. by reducing somewhat the size of the tailplane and the fin/rudder (by approx. 8-9% and 11-13% respectively in order to match true scale proportions). My question is, will such a reduction in the tailplane/fin/rudder area be detrimental to the flying characteristics of this biplane model? The above-mentioned ‘ivyandmartin.demon’ link suggests ‘definitely not’ (and even talks about ‘further improvements’ involving modifying the shape of the wing ribs to introduce undercamber, which I’m not planning to do) but no supporting actual flying performance comments are mentioned to back up the suggested rear end modification. Also, this link refers to the original DB ¼-scale Pup design with two fixed wings rather than the latest design involving four-wing halves with working flying and landing wires. I don’t know whether any of the key dimensions of the original design have since changed - perhaps not? As a compromise, I could of course just leave the rear end of the model alone and just undertake the cowl modification described and then just accept whatever lead ballast penalty is required. But I would prefer to maximise the model’s scale appearance overall as long as I won’t be jeopardising its flying performance. Does anyone have actual flying experience with this model having undertaken the modifications described under item 1) and 2) above? All comments gratefully received. Sorry the above is a bit long but I wanted to get my concerns clearly across! David Edited By David Hayward on 02/12/2015 01:17:29
-
DB 1/4-scale Sopwith Pup
David Hayward replied to David Hayward's topic in Scale and Semi-Scale kits
Tim / Bert / Andy et al Yes, I fully appreciate that the dog clasp will need to extend approx. 1/4" beyond the length of rigging wire needed in order to fit it, with the subsequent slack taken up at the other end by the DB gripper,... or other means of adjustment such as a turnbuckle if an alternative is adopted. The current DB grippers seem to be a Mk 2 type with longer spring-loaded chrome-plated steel entrance tubes (25mm) than they used to be (ref. the wing section description on page 45 of Alan Hirji's build log for the 1/4-scale Pup on the DB Sport & Scale website which refers to Mk 1 & 2 types); these extend into a 7mm diameter x 10mm long gripper barrel. On the DB 1/4-scale Pup, part of the barrel circumference rests in a slot in a ply former, retained with a cable tie, and the spring-loaded tube extends just beyond the surface of the wing to allow the tube to be pushed in and then let go to grip the tensioned wire. Hence, no access hatches are required. It's worth recording that the gripper wire per se is a non-nylon covered type, the theory being that this will maximise gripping efficiency. The short gripper wire protuding from the gripper entrance tube (plunger) is then joined to the main nylon-coated rigging wire via a brass ferrule with both ends of the two wires looped round the ferrule prior to crimping, ideally with a touch of cyano for added security. I studied the DB Sport & Scale website 'How Rigging Works' & 'Pup rigging system' sections before I decided to purchase the kit, although the full details of how the grippers work only became apparent to me when seeing them 'in the flesh' and reading the instructions alongside the three plans supplied. A summary of the rigging components is set out in the second of Pete Lowe's five RCM&E articles about the DB 1/4-scale Pup - see RCM&E March 2012 on page 86. As mentioned in my original posting on 15/12/14, both flying wires and one of the interplane diagonal wires are adjustable via grippers. It is the landing wires and the other of the interplane diagonal wires which are of fixed length. Does anyone have experience of using the adjustable turnbuckle option instead of grippers? David -
DB 1/4-scale Sopwith Pup
David Hayward replied to David Hayward's topic in Scale and Semi-Scale kits
Bob - Thanks for your comments. I hadn't seriously considered the clevis option for the rigging, even with rubber fuel tubing sleeve protection commonly used on control rods using clevises to minimise the risk of the clevises popping off. If I'm going to move away from the DB kit grippers, I tend to prefer, at least conceptually, the turnbuckle idea on the flying wires (and one of the two interplane strut diagonal wires) to provide means of length adjustment/tensioning, with the wires fixed at one end and then using a DB stainless steel hook clasp (mini dog lead clasp) at the other. As well as being somewhat more scale-like, while noting your experience with your Jungmeister, this is principally because the DB instructions specifically state (in Red ink) 'IMPORTANT NOTE: While we realise that the stainless hook clasp is a bit fiddly to attach, it will not fail when locked on. However, if metal clevises are used as an alternative, they WILL fail and the aircraft WILL be lost. This has been painfully proved.' -
DB 1/4-scale Sopwith Pup
David Hayward replied to David Hayward's topic in Scale and Semi-Scale kits
Many thanks to you all for your useful responses (Jez, Tim, John, Jon & Andy) - so far, a mix of reactions it seems - some seemingly happy with the gripper concept and others not - Hmm...!! As I'm looking for a 100% reliable rigging system, the gripper system, I have to say, is making me somewhat nervous. I'll do some load tests with the help of a spring balance over the Christmas period before finally deciding how best to proceed. The main alternative seems to be to use adjustable turnbuckles instead - I have never used these but presume that they are pretty quick to link and tighten up? I don't want to bother with endless nuts and bolts as used, for example, on the Flair Puppeteer - too fiddly and timing consuming at the flying field.