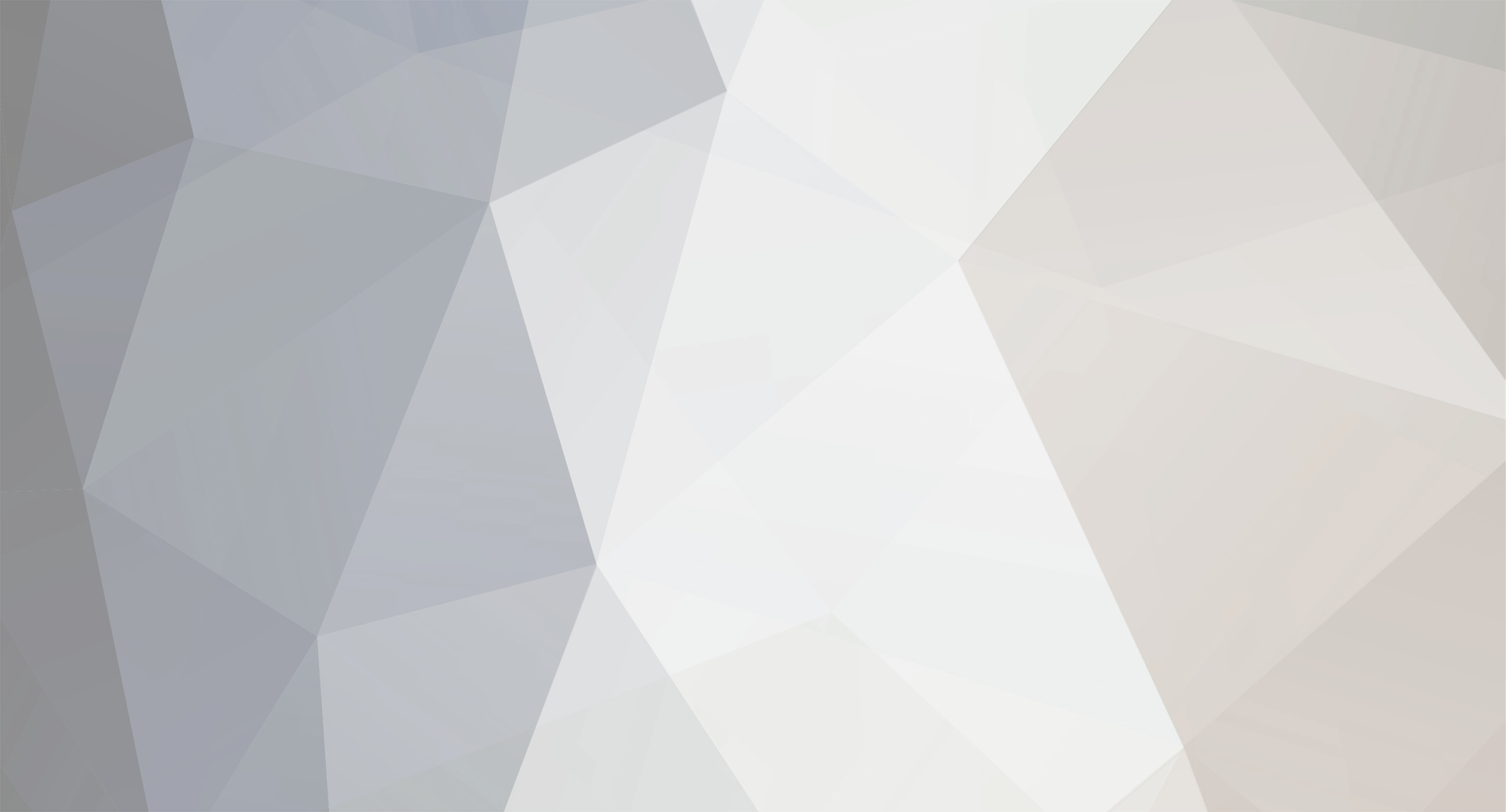
Bob Merrett
Members-
Posts
103 -
Joined
-
Last visited
Never
Content Type
Profiles
Forums
Blogs
Gallery
Calendar
Downloads
Everything posted by Bob Merrett
-
I too had a great bargain from Ikea (Bristol). It always pays to have a look around in their bargain corner as on this occassion my wife, yes, my wife, pointed out this small table top still in it's wrapping and said "Would this be okay as a building board" love her. It measures roughly 4'x2'x1&1/4" and was marked up at £5, tabletop only, no legs. It's light for its size and makes for a great solid, level surface to build on.
-
Which covering would you choose?
Bob Merrett replied to Bob Merrett's topic in Own Design Project Blogs
Yes BBC I know what you mean. There are some areas that I will cover with the card, but other areas I will have to stick with the 1/16 balsa as allowances have been made for just that. Maybe my next build I will look to make more use of the plasticard. -
I am looking to start sheeting my F9/37 this week and don't know why, but I just though I'd check out some weights. A sheet of A4 plasticard 10 thou/0.25mm thick weighs 17 grams and a sheet of very similar size of 1/16th balsa that I have pre-prepared weighs 19 grams. Still need to prepare the balsa after, whereas I could just paint straight on top the plasticard. All comments welcome!
-
Hi Ernie, it looks like the only picture edit that I have on this PC is Paint, and I can't see any function to enhance the contrast. Clearly I will have to make the lines bolder at this rate. My apologies for the lack of clarity in the photo's, I will look to address this as I progress. If anybody who has edit access and a suitable program wishes try and enchance, please feel free!
-
Just thought I'd post the bare bones of my Gloster F18/37 as I have just finished drawing up the fuselage pod. The main and tail planes will be taken care of via Compufoil3D. Edited By Bob Merrett on 02/12/2012 12:53:29 Edited By Bob Merrett on 02/12/2012 12:57:08
-
Who remembers Love Thy Neighbour! Wonder why I've never seen any repeats of that series. "I'll have a half" - Jacko. Where's the harm in that!
-
Don't forget me!
-
Hi folks, I am sharing this experiment as you may find a use for it or something similar in the future. Just for an alternative covering, while at the supermarket and browsing through the “craft” section with the wife, I saw some coloured tissue, which was marked up as gift wrap tissue, and thought to myself, for 99p I’ll give that a go. It’s been lying around for ages to be honest, but the other week, I bought myself a Guillows 16 inch wingspan Hawker Hurricane and was going to use it as my experimental aircraft. I eventually got around to building the Hurricane, and this week started to apply the silver tissue instead of the white as supplied in the kit. On opening the packet I noticed that one side was more shiny than the other, so naturally went with shiny side out. I assessed the grain to be running lengthways and duly started applying the tissue to the tailplane initially. The other part of the experiment was to attach the tissue and dope it with WBPU. To my surprise all was going well until it came to wet shrinking. It took hours for anything to happen, the water was just resting on the tissue like beads of rain on a freshly waxed car. “Just what is this stuff” I am saying to myself. Yes it was wet and crinkly, but not drying out (quick enough for my liking). Then in one last desperate attempt, I remembered the aeromodellers old favourite, steam! So, with the tailplane duly held over a boiling kettle, with long nose pliers I hasten to add (!), I steamed the tissue and put the tailplane aside to let it settle. Result, the tissue shrank as hoped, and I proceeded to cover the rest of the model. The photo you see is it drying out after it’s first coat of WBPU. It saves on painting (I’ll pretend it’s prototype K5083 and won’t have to fit the exhaust stubs then!). When I eventually get my F9/37 finished, I will cover the sheeting with this silver tissue and WBPU, that is my aluminium basecoat colour, then, if any camouflage chips off over time, I have some natural weathering! Well, that’s the plan………. Mmm, the worktop makes it look more grey than silver.......... Edited By Bob Merrett on 15/11/2012 13:44:07
-
Magnificent! **LINK** Have a scan around these pages while having a cup of coffee or something..... I have been following this development for years. He made some new concrete moulds from scratch as the concrete wouldn't move with changes in temperature compared to wooden ones. I guess that means that he can knock out as many as he wants now, he has everything he needs from building this one. Let's hope he builds eleven more and get a whole squadron up!. Every 8th of May they could do a flypast over Berlin or something. My most favourite of all aircraft. Was this the first true Multi Role Combat Aircraft? Who fancies clubbing together and getting this guy to build one for us all?
-
RC Shops near Gloucester?
Bob Merrett replied to Robert Armstrong 2's topic in R/C Retailers / Distributors / Manufacturers
Could I just add to Rentman's post. There used to be Gloucester Model Centre directly opposite the bus station, but that has stopped trading years ago now, or Antics is a minute or two's walk just around the corner. Not sure which one Rentman is referring to, but at least it gives you a landmark. -
RC Shops near Gloucester?
Bob Merrett replied to Robert Armstrong 2's topic in R/C Retailers / Distributors / Manufacturers
I live in Gloucester and apart from Antics, you have Clive's shop as listed below. Outside of that it is as Pete mentioned, Cheltenham Model Centre (@9 miles), Antics (Stroud @9 miles). haven't been to the other's that he has listed, Bream and Lydney are 20 odd miles from here. If you fancy a ride out somewhere, I've been to the one in Hereford (@33 miles from here), that's a good one, big too(compared to the ones here at least). Hope this helps. Bob -
Changing from tri-wheel to tail dragger
Bob Merrett replied to flyingman's topic in All Things Model Flying
Hello Flyingman, i was just trawling through some posts and saw that there has been no replies to this post and thought I'd give this a shot. I am not familiar with your particular plane as such, but basically everything revolves around the aircraft CG point as usual. Rather than try to sketch something out and photo it etc., I have had a quick trawl on the internet and found this image, which hopefully is self explanitory. Not knowing your models construction materials etc, I cannot offer up any specific method, but basically the main wheels get moved in front of the CG point. Exactly where that place would be, and be suitably robust enough, I do not know. It may be that you are simply not able to reposition without some homebrew major surgery. Hopefully you gain some inspiration by studying the attached image. -
Thank you for your kind words Graham. If i'm going to be honest, then I wanted to prove to myself that it could be done, and in fact, that I could do it. I am no engineer and have no special tools, just your average builder really with general tools, who just wanted to try something a little different. I just thought I'd post the idea as somebody might be able to use/adapt it for a undercarriage, swing wings etc on a project they might be doing or thinking of doing. It just means that you can dictacte how fast or slow you want something to operate. Another confession Graham. I too have now bought (I'm guessing) the same pair as you as the the prices have really dropped since i firsted the project. All right, all right, stop verbally abusing me. I keep changing loads of things as I go, and this was one of them. In the end I opted for commercially available stuff (the price helped) instead of bespoke, just in case others liked the model and wanted to build it.
-
Thanks for the tip off Steve, i'll keep a close eye it. That was kinda my thinking with such a short coupling (torque) tube though. For added security one could always solder, braze, epoxy, liquid weld etc the joint i suppose, once you've got your input and output shaft sizes sorted.
-
Cheap shaft coupler:- A 14 swg collet happens to be 8mm in diameter with a 2mm shaft hole. I managed to find some aluminium tube (1m in length, so plenty of coupling housings here, for less than a fiver!) in Homebase (or B&Q) that was 10mm in diameter with a 1mm thick wall, thus bringing the internal down to 8mm. Yes, just simply cut a length off the tube and pop the collets inside at each end, and hey presto, you have a cheap but effective shaft coupling. Well, not quite so simple, but simple enough if like me you don’t (but desire to) possess a lathe. The inside diameter was not quite 8mm (7.8mm) and after I cut a given length (11mm in this case) off the tubing, I clamped the tube in the wooden jaws of my workmate in ran an 8mm drill down the inside the tube. Measuring 3mm in from each end of the tube, I drilled a 3mm through one wall of the tube, this is to accept the grub screw that goes on down in to the collet. If you stick with the 2mm hole, the existing 3mm length grub screw will need to be replaced with at least a 4mm length in order to “extend” out into (and in this case)sit flush with the outside of the aluminium tube. This is to prevent the collet from spinning/slipping inside the tube, but quite honestly, it is such a tight fit anyway, I’ll let you make up your own mind. By the way, I used 11mm for my length of coupling as I thought that this would allow the collets to sit back to back and support each other and not move, but as I said, so I reckon that the tube could easily be any length you wanted. The standard hole can be bored out to 3mm or 4mm quite easily to accept different shaft sizes, I just centred up the collet first with a 2mm drill. I mounted my drill in a vertical drill stand, so it effectively became a pillar drill, and once centred and clamped, just simply bore out the hole in increments or just go for it with the right size drill. You then have two suitably sized collets to pop in to your coupling tube. So there you have it, you can bore out the collet hole to suit any size of shaft. The same process can be applied to larger diameter collets, or to form the basis of some home brew oleo legs, get my drift? Of course you do.
-
While working on my 1/12 scale Gloster F9.37, I have been looking at ways of converting mechanical retracts from direct servo to electric screw operation. “Why?” you may well ask. Well, I had mechanicals ready to use, didn’t want the snap they give, didn’t want to spend even more money on the new servoless ones that have come on the market and betted myself that I could get some everyday available items and make it happen, cheaper. I know things have moved on now and they can be bought for a very reasonable price, but I thought I’d still share some ideas as it may help you dabble or adapt for some other application. Option 1. All in one miniature geared motor, coupled to a threaded rod (please see cheap shaft coupler) and trunnion and microswitch operation. The motor cost £5, and as I have a tap and die set, I extended the thread that is already there on a 3mm coupling rod (that I already had, as will you too no doubt). Make up your own trunnion from something like a nylon adjustable aileron connector, 3mm t-nut, 3mm hex nut, 3mm thread insert in to wood or nylon, anything really that will wind its way up the thread. 3mm thread diameter is plenty tough enough for this operation and is easy to calculate the linear travel required. Example. The existing actuating rod and trunnion travel 25mm from up end to down end. The thread pitch is a very handy 0.5mm or 0.5mm linear movement for every revolution, two revolutions to make 1mm of linear movement. Still with me? Good. I was after something like a four or five second cycle time from down to up (and up to down of course), but how was I going to achieve this? Well, just substitute your values in to this formula, and away you go. Travel Length (say 25 mm) ÷ Time (in 5 seconds) ÷ Thread Pitch (M3=0.5) x 60 = RPM speed required from motor. 25 ÷ 5 = 5 ÷ 0.5 X 60 = 600RPM operation speed to achieve this. Let’s say the ungeared motor turns at 6000RPM, then I need a reduction gear ratio of 10:1 (12000RPM being 20:1 ratio). Motor RPM ÷ operational RPM. Easy mathematics I know, but you get drift. 3mm thread is also great for using as a fine tuning and adjusting thread as a half-turn would be 0.25mm of movement and a quarter-turn would be 0.125mm of movement etc. etc. etc. Option 2. Miniature motor (pack of 5 for £4), worm drive reduction with an internal thread, threaded rod coupled to existing actuating arm (via a fixed clevis in this case) and microswitch operation. Worm drives are brilliant and offer the highest single cog ratio reduction, plus they naturally form their own brake when not in motion. For that slightly bigger project just move things up a notch to M4. I found some M4 centre hole furniture cross dowels that would make perfect metal actuating trunnions, and they come in different lengths, just check out e-bay.