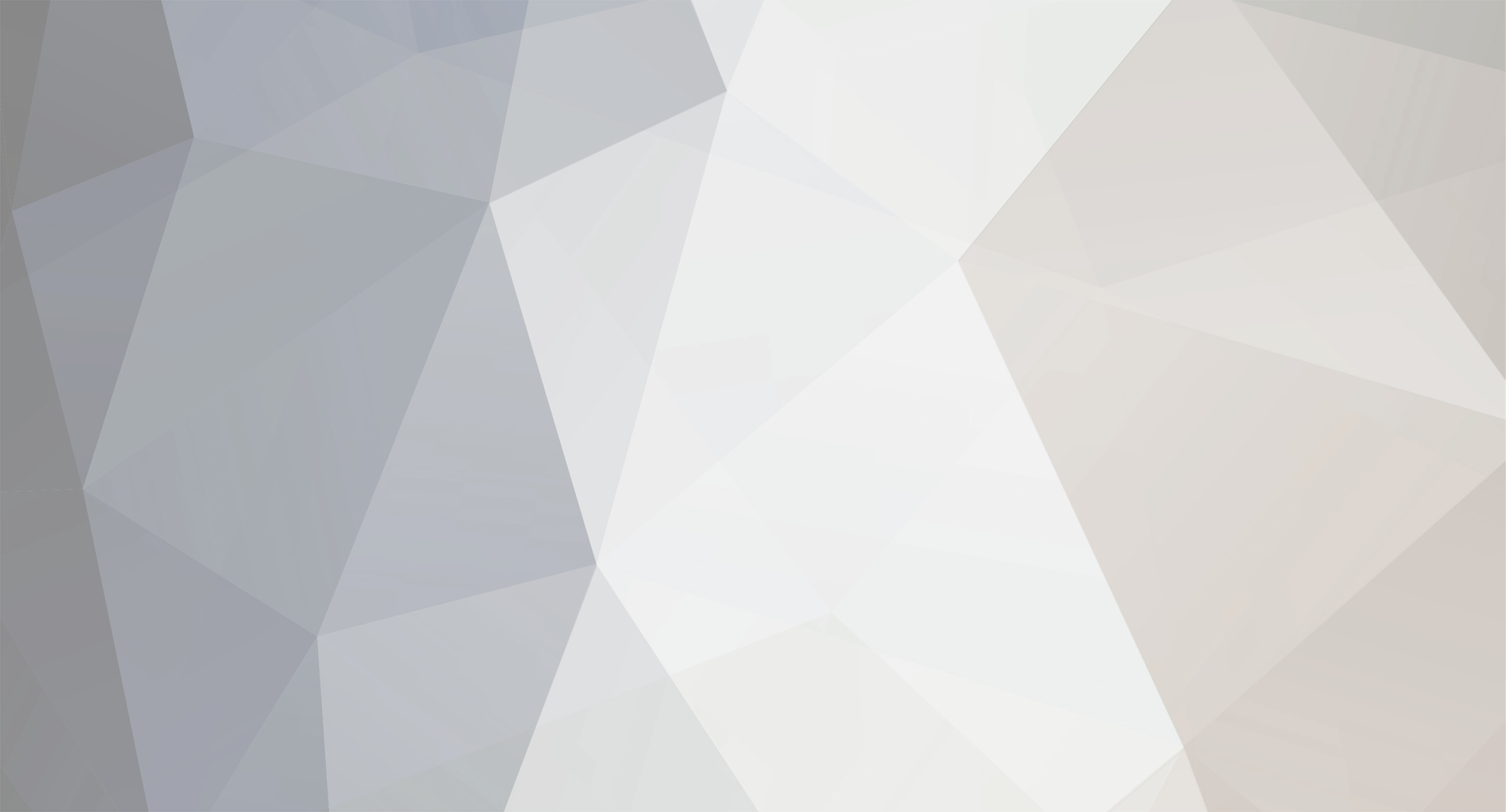
Paul Williams
Members-
Posts
467 -
Joined
-
Last visited
Never
Content Type
Profiles
Forums
Blogs
Gallery
Calendar
Downloads
Everything posted by Paul Williams
-
Topflite giant scale P47 Jug
Paul Williams replied to Paul Williams's topic in Build Blogs and Kit Reviews
Yeh but this is the first of two wing halfs so your advice is welcome, I will try it thanks mate -
Topflite giant scale P47 Jug
Paul Williams replied to Paul Williams's topic in Build Blogs and Kit Reviews
I have to say for the first time since starting this I really struggled today. The wing sheeting being the problem. The forward section was no trouble But then the instructions stated lay out the aft wing sheeting and trim to size, The sheet fits from the main spar up to the centre of the TE. The TE is 1/8 ply section so the sheet must be trimmed within a 1/32 tolerance. Its impossible to see the TE with the sheeting laid on the wing how the hell can you trim it to size. After 3 brews and a whiskey I could not figure out a method to cut the sheet without removing the wing from the plan and flipping it over so I could mark the sheet from the rear first. What a pain once cut I had to replace and re-pin the wing down. Perhaps someone has a method other than this help please. -
Topflite giant scale P47 Jug
Paul Williams replied to Paul Williams's topic in Build Blogs and Kit Reviews
Hi Neil, to be honest the wax paper is some thing I have had for ages in the garage I cant remember where it came from, I hate to say this but although the delivery time was quite quick from Robart I got stung with customs. Unlike our China friends the Yanks mark up retail price on packages and the old VAT army jump on them. It was quite a shock fella hope yours slip through. Fantastic quality though. Great model you have picked are you doing a build blog? Thanks for your feedback guys.Edited By Paul Williams on 18/02/2011 22:20:41 -
Topflite giant scale P47 Jug
Paul Williams replied to Paul Williams's topic in Build Blogs and Kit Reviews
Moving on to the wings, have to say still impressed with the building methods. I have not felt the urge to strengthen or change much up to now. The instructions suggest gluing up the wing skins while the board is free. I find a good method is to trim with straight edge then use the straight edge to hold flat while the edges are slid together have a look at next photo. I use cyano with this method and as yet have had no misalignments. Dont forget to put wax paper under joint. Pretty much normal and plane sailing up to this stage. -
Topflite giant scale P47 Jug
Paul Williams replied to Paul Williams's topic in Build Blogs and Kit Reviews
The retracts turned up today and I have to say it’s true the old cliché you get what you pay for. Brilliant quality there is no movement at all when locked in, the operation is smooth and precise. So now I can go back to finishing the fuse off. The tail wheel unit dropped in and piped up. I have reservations about the design here once the sheeting is applied this unit cannot be removed. Its possible to loosen it and get to the steering control arms but should anything happen to the air cylinder it will have to be cut out Oh well have faith in Robart Finished sheeting the fuse. -
Topflite giant scale P47 Jug
Paul Williams replied to Paul Williams's topic in Build Blogs and Kit Reviews
Trial fitted and shaped the canopy, I have to say the quality of this is excellent just need to paint in the framework. I can’t believe how long it took to mask up the canopy I always paint the inside it’s impossible to scratch it afterwards. A little tip, remove masking tape before the paint hardens or the lines will not cut when the tape is pulled, pull back the tape onto itself as photo to get a nice crisp line. It’s true what they say; about preparation work though I considered hand panting this but with the end result I’m glad I didn’t -
Topflite giant scale P47 Jug
Paul Williams replied to Paul Williams's topic in Build Blogs and Kit Reviews
Anyway I’m sure we can beef things up and with a lick of paint it should do the job cosmetically. I read through the instructions and apart from suggesting what colour it should be they are pretty useless. No reference at all on how to fit it to the fuse. Its going to be a make it up job as we go along. Right cut out cockpit deck Then figure out a way to support the new one the remains of former 4 lends itself to help here. The two sides plus front and rear have good contact areas so can be glued straight on to fuse. I guess how good this is going to be is up to how much time I put into it, here is how it should look I had read an article about cockpits and how to give the dials some good three dimensional perception. It’s really easy to do you just take some solder wire and wrap round a drill shank (correct dia) run a Stanley blade across to make up bevels. Pick up with tweezers and drop some cyano over joint place down on grease paper and carefully push the joint together. Bingo perfect circle, Pick up again and dab some thick cyano on paper dip in place over clock face. Have a look at picture it gives the cockpit face great depth. It only took an hour to do this time well spent I think Ok finished off some cockpit painting -
Topflite giant scale P47 Jug
Paul Williams replied to Paul Williams's topic in Build Blogs and Kit Reviews
I took receipt of the scale cockpit kit today and as usual it is a very cheep and flimsy thing for which they charge far to much money (Ripmax again). Edited By Paul Williams on 17/02/2011 21:36:16 -
I am the pilot who spent hundreds of pounds on such models, when I did so the club was in agreement I could fly them. In comparison its like the government coming along and saying I'm sorry but you may no longer drive your 3lt porche unless you take a test to prove you can drive it in a manner that you would never do anyway!
-
Ok point taken, I am venting off at a situation where I have never been responable for any near misses and the club seems to be penalising myself and ignoring others who have. I will do the B test this year if only to wave it in their faces. Thanks for your feedback.
-
Slow setting epoxy resin, 30min or longer is generally considered the best option. hope this helps
-
Our club committee has decided to update the club rules and we had a meeting to discuss the matter last week. One proposal is a blanket ban on models in the category of 7kg-20kg unless the operator has a B licence. I disagree with this my opinion is the risk of having an accident flying this type of craft is less than flying smaller planes. I base this on the fact that the planes are much more expensive so the pilots are less complacent, the regulations governing them are more stringent regards fail safes and servos ect. The planes are easier to see so the pilots less likely to become disorientated and personally I give a great deal more respect to a 22” prop then small ic engines. The other issue I have is with the B test being suitable. The test is principally the same as an A where safety and pit control is the subject, only the flying schedule is different and far more aerobatic than the planes would be expected to perform. I would not consider doing a three turn flat spin exiting in the same direction with my corsair. You could do a lot of serious damage with a 60-120 IC model the type we witness hitting the deck on a regular basis why pick on some thing with a good safety record? I would like to canvass other peoples opinions on this matter maybe I am bias because I love to fly these models and feel aggrieved that I now have to do a test to do so.
-
Advice on ignition module mounting please
Paul Williams replied to Paul Williams's topic in All Things Model Flying
Thanks for the feedback guys its fitted to firewall . -
Advice on ignition module mounting please
Paul Williams replied to Paul Williams's topic in All Things Model Flying
Thanks guys I think I will go for it there is enough room to fit a heat sheild so should be ok. Great pics very professional job. -
Hi all I am fitting a RCGF engine into a large scale P47. I am wondering if the ing unit will be ok fitted inside the cowel. I know this is not an ideal enviroment but there are numerous problems if I fit it behind the fiewall. It would be sited at least 2" from the exhaust. What are your thoughts please as anybody done this without problems.
-
Topflite giant scale P47 Jug
Paul Williams replied to Paul Williams's topic in Build Blogs and Kit Reviews
The firewall is lamented with ¼ and 1/8 ply to make up 3/8 they kindly centre punch the centre thrust line for you so mark out engine hole centres from this datum point and fit the captive nuts. I like to dill 2mm hole so they don’t stress the wood to much when you pull them in. Before gluing in the firewall, drill and screw through the sides this holds the wall in place as the epoxy is setting and gives the joint good strength Before final fitting I will fit the tank and look at throttle links, The tank is massive 32oz it should fly for hours with a petrol engine, the good news here is they supply a petrol bung and tygon tube as well as glow stuff. Nice touch that. Tank as been pressured tested in the sink and that’s enough for today. One of those days when you spend more time thinking than doing, I test fitted the engine and was quite surprised at the distance I needed to make up to bring the prop driver to the right position. At nearly 40mm short it meant the stand offs would have to be 85mm long. I did not fancy that I wanted some solution more robust. I ended up laminating some oak off an old headboard to extend the firewall I have a feeling using the lighter RCGF engine I will need weight up front anyway. I cant believe how much time is being eaten up making decisions like where to mount the IGN unit. There’s bags of room within the cowel but will it be effected by heat and oil? The trade off is to fit next to tank but the plug top is moulded on so a massive hole in the firewall would be needed. Grrrrr -
Topflite giant scale P47 Jug
Paul Williams replied to Paul Williams's topic in Build Blogs and Kit Reviews
My first niggle today the control rods would not run smoothly, the holes for the support tubes are pre-drilled in the formers I had to pull a line tight mark off and re-drill the tube support holes. All is well now and no binding is evident. Not much to write up as it was a nice afternoon I spent time with my Warhawk. Still trying to source some 5” wheels for this any ideas?