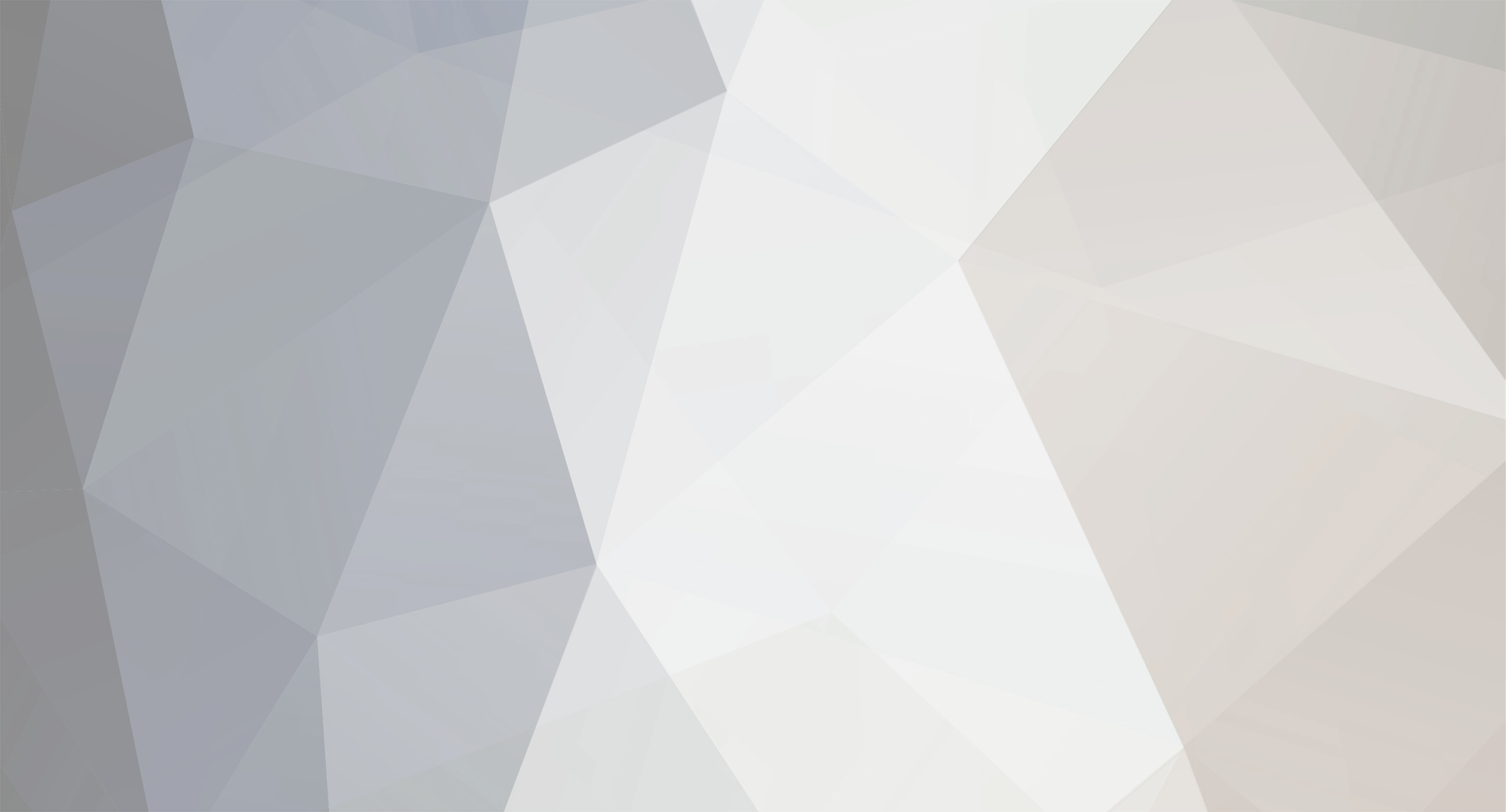
RedBaron
Members-
Posts
222 -
Joined
-
Last visited
-
Days Won
1
Content Type
Profiles
Forums
Blogs
Gallery
Calendar
Downloads
Everything posted by RedBaron
-
Further to the comments about Fusion360 above. I decided today to start exporting my designs from Fusion360. And........ There is no way to export designs AND drawings from Fusion360 unless you have one of their paid for options. In fact the drawings and associations to the solids are in the wind. If you are a Personal Use Only user then you are locked into a proprietary format with no escape for your work!! I have no desire to be locked into any product or format which makes me very happy to have recently chosen Rhino I can export the Fusion360 solids via STEP format, which I will do but I will not have the associated drawings!! For most designs this isn't too bad. Then I will close down my Fusion360 account.But a major swindles as I do nor remember being told this at the beginning.
-
This last post has nothing to do with The Ohmen, it is more to encourage people with printers to use them more and those without to get a basic one. After this Peter I promise to stick to the subject and thank you for your patience. I mentioned above about non modelling uses, such as replacing broken and irreplaceable household items. Well I should not have tempted fate. For about twenty years we have had two wooden geese (carved from bamboo root I think) that live in the garden next to the bird bath. This afternoon I went into the garden for some fresh air and noticed one of the geese lying on his side. I went over to stand him up and found to my horror that both of his feet had completely rotted way - no wonder he was lying down. Well it seemed to me that rotten feet qualified as irreplaceable. So after 15 minutes of designing and about 1.5 hours printing Mr Goose had a new pair of orange feet. Imagine doing that by carving lumps of hard wood.
-
I too have been using Fusion360 and very good it is but I have recently changed to Rhinoceros. It is always a struggle changing to a new UI. The Cowling was my first Rhino project.
-
If I may say so - not complex, just a load of simple sequential actions. If you have a printer all you need is practice, decide on some simple projects like design and print a servo mount to go in the Ohmen? and when that works another project. But from my own experience regular use is good The more you do the more you can do.
-
Bother I posted that without completing the thought: The first step was to scan key parts of the plan,. import the scans into the 3D program and set them up as shown above. It is then relatively easy to construct drawings and then to make the solid parts within the program. The parts are then exported as .stl files to ones PC desktop or anywhere. The .stl files then need to be processed in another program to produce the toolpaths for the 3D printer and there you are. I have been playing at 3D design for a couple of years but this cowling was the first project in a new design program (purchased) Does it cost a lot well yes and no. Where I have got to after a few iterations is: The free plan thank you Peter. The design program, there are lots of free ones but many are not up to the job, the one I have just acquired was wincingly expensive but less than the cost of a middling moulded glider The program that makes the tool paths, there are lots of free ones but I have settled on a purchased one I think it was about £50 The printer, there are lots of cheap ones but I have now settled on one that cost much as a medium sized electric model. Do not buy one that locks you into the manufactures consumables! For filament choose an established supplier and buy a medium to higher range filament, cheap filament will not do. So the whole lot cost a biggish moulded glider. I do enjoy making stuff in wood. But... Once you have designed say a servo mount it is very easy to modify it for another type of servo or another model. The same if you make a mistake. So I believe that embracing the new technology helps one to be a more efficient builder and it is a different sort of fun On the more mundane side of things stuff around the house often breaks and the plastic parts are completely unobtainable now I can design and print replacement parts in a lot of cases.
-
Thanks Peter for your kind remarks. I originally meant to just show the picture of the fitted cowl - but over my evening meal it occurred to me that some folks might be wondering how one gets from the free plan to the finished design. So it might be worth pondering that for a moment. As they say a picture saves a 1000 words
-
And another thing whilst on The Ohmen and 3D printing. The Ohmen wing has quite a nice profile and I am not very good at shaping leading edges. So I scanned a wing profile from the plan and used it in my trusty design program to make a custom sanding block. It then needed an appropriate grade of garnet paper adding and retained with a few blobs of UHU. This was quite successful as it very quickly created a perfect and correct profile:
-
And just for good measure the parts before printing as the appear in the design program:
-
Wowww don't know where the picture went, it was there when I posted the message?!? Try again two pictures now 1 the printed parts 2 the parts fitted
-
I have just about got my build complete. When I got to the cowling construction I just could not face all the balsa shavings and sanding dust so... I 3D designed a cowling and printed it. The accuracy was very good and the profiles match the plan nicely. I also designed a back plate for the cowling, this screws to the firewall and the cowling screws to the backplate.
-
Devcad and its related software packages
RedBaron replied to Andy.I's topic in All Things Model Flying
Presumably the parts that you can't do would be drawn in devCAD? -
Devcad and its related software packages
RedBaron replied to Andy.I's topic in All Things Model Flying
Profili three versions: Profili base version is the entry level version of the Profili family. It includes the most used functions for a hobbyist modeller, going to build rather simple airplane models. A full collection of airfoils is included, and you can print and export to DXF simple ribs, loft of ribs and foam cutting templates. Some functions to create, modify, import and analyse airfoils are also included. The database has more than 2,200 airfoils with precomputed aerodynamic characteristics, which really saves time in making airfoil comparisons. The user's ability to easily change the airfoils slightly (or even extremely) has been made effortless. The program will then compute the new aerodynamics resulting from your changes. It is interesting to watch the computations take place; you gain a "feel" for how the pressures are distributed over and under the airfoil. Profili XT This is the intermediate version of the application Profili. It includes all the functions of Profili, and adds: - Printing and DXF exporting from the Wing panel feature. - Three more functions to generate new airfoils. Profili 2 Professional The full featured version of Profili. Profili Pro is the full featured version of the Profili family. It includes all the functions of Profili XT, and adds: - creation of cutting files for 3 axys CNC milling machines - creation of cutting files for 4 axys CNC foam cutting machines - creation of STL files of wing panel molds - a full featured series of airfoil analysis functions - new functions to modify and improve airfoils performance There does appear to be talk about and assembly program that will join wings and fuselage together. -
Devcad and its related software packages
RedBaron replied to Andy.I's topic in All Things Model Flying
17/02/2014 CADing is stirring in my brain again. I have not been satisfied by the aero-modelling support in the CAD programs that I have used to date. Odd comments / reviews do turn up in the magazines but none of these tell the whole tale. So I have been trying to learn, from scratch, what is there to help us. I could not find anywhere a simple summary of what I wanted to know, so as always I had to do it myself. Below is what I have learnt this morning about CAD products for aeromodellers. Comment: The dev family of applications were developed with the co-operation of the Profili project. I am not quite sure what that means but suspect that it means that the airfoil functions in the dev programs are powered by Profili. See below for information on Profili. Also I think that if you buy a dev product you do not need to buy Profili. Profili is a product of the devCad business. Most of the information below was gleaned by cutting and pasting from a number of sources, any opinions implied are not mine (yet). The cost of these programs did not seem too bad to me considering the work that has gone into them. However it does seem that ones needs to think carefully about ones requirements before jumping in. The decision process may be eased as most seem to allow trial downloads. devCad Three versions: **LINK** devCad LE (Learning Edition) is a 2D full integrated Cad and Cam application. This software is the entry level of the main application DevCad. It was designed to help you learn more about the Cad applications and it has an very easy to use interface with many features. With this software you can get multi view interface (you can open more views on same document). devCad Pro is the full featured Cad application. It includes all the functions of devCad LE, the same interface and commands, but add all what is required to make a full featured 2D Cad application. devCad Cam Pro is a full integrated Cad/Cam system. It includes all the functions of devCad Pro, the same interface and commands, but adds all what is required to make a powerful Cam application for 3 axis CNC milling machines . The devCad Team developed new 'smart' technologies to improve the user's work. devWing three versions: devWing LE Using devWing LE you can draw in a very easy way a simple ribbed Wing and print its parts. The LE version manages 1 wing panel and the wing tip. The Wing plan can be drawn using a raster image or a DXF file as a reference, and complex shapes are managed. Sheetings, leading edge, trailing edge, D-Box, many types of spars and lightenings holes can be included. devWIng Using devWing you can draw in a very easy way a complex ribbed Wing and print or export to DXF/DC1 its parts. Using devWing you can create multiple panels, and every panel can have different shape, airfoils, dihedral and washout parameters. Vertical and angled ribs, geodetic ribs, sheetings, leading edge, trailing edge, D-Box, many types of spars and spar wizards, decks, aileron slots and lightenings holes can be included. devWing Cam is the most featured version of devWing. It offers all the features of devWing and adds CNC-CAM functions, to let you to create in a few minutes the right GCode cutting paths for your CNC milling machine. devFus three versions: devFus is an innovative application for drawing fuselages and other similar parts. Very complex shapes can be created, not only simple circular or squared section as other applications do. The application is easy to use and no Cad skills are required. devFus includes all the print and export functions, so devCad is not required. devFus Cam is the devFus version you need if you have a 3 axys CNC milling machine. All the features of devFus are included. Includes all the functions to manage the Cam Project, to have the machining preview and to create the right GCode, so devCad Cam Pro is not required here. Includes a wizard to create a Cam Project for every fuselage Project. A Nesting function allow you to place the parts to cut on one or more tables (plywood foils for example) , to avoid to waste material. Labels can be engraved on every part, and bridges applied to the cutting path devFus Foam, the new application to draw and cut foam fuselages. Using DevFus Cam you can create in a very simple way a fuselage drawing. The Project Wizard will drive you to draw the fuselage using a step by step approach. To draw the fuselage Side and Top view you can for example adjust the Outlines to follow a scanned image of the fuselage: -
Jet Provost Build by RedBaron
RedBaron replied to RedBaron's topic in PSSA Mass Build 2014 - Jet Provost
19/02/2014 - JP now shaping up a bit. Progress has been a bit slow recently due to the build of a new indoor GymStar temporarily having got control of the work bench! Also although I seem to have done quite a few hours on the JP nothing seemed to be photo worthy. Jobs done include finalising the snake lengths and fittings for the rudder and elevator, finishing sheeting the fuselage etc. Also a lot of planing and sanding to get the fuselage just about to it's various profiles. All of the control work is done so I guess that I now need to shape the fin, rudder and elevator and do the under wing block work and the intake blocks, the cockpit and canopy. Hmm quite a long list. -
Jet Provost Build by RedBaron
RedBaron replied to RedBaron's topic in PSSA Mass Build 2014 - Jet Provost
13/02/2014 My JP afterworks - After applying some more 3/4inch triangular section balsa in the tail plane seat area and some sheet scrap it was time to mark out some of the balsa to be removed and then remove it: As I am a bit sensitive to dust, I used one of the Gaskin Softbore tools to remove the curved bits a long knife blade helped with the straighter bits and only a small amount of tidying up with a Dremel sanding drum tool was necessary to get the job to this stage. This all went much more quickly than I expected. Now to figure out the most efficient way to do the external shaping. -
Jet Provost Build by RedBaron
RedBaron replied to RedBaron's topic in PSSA Mass Build 2014 - Jet Provost
13/02/2014 - Are Jet Provosts shy? Prior to starting on the exhaust area I thought that I would look at a few JP rear ends to set the details in my mind. I have just spent some time looking at literally 100s of JP photos and find that they do not like having their afterworks photographed. I really only found three pictures that were helpful, they do show that there are some variation in this section of the aircraft. So depending on the specific aircraft that you have chosen to portray you may want to check the details for yourself. Edited By RedBaron on 13/02/2014 15:17:07