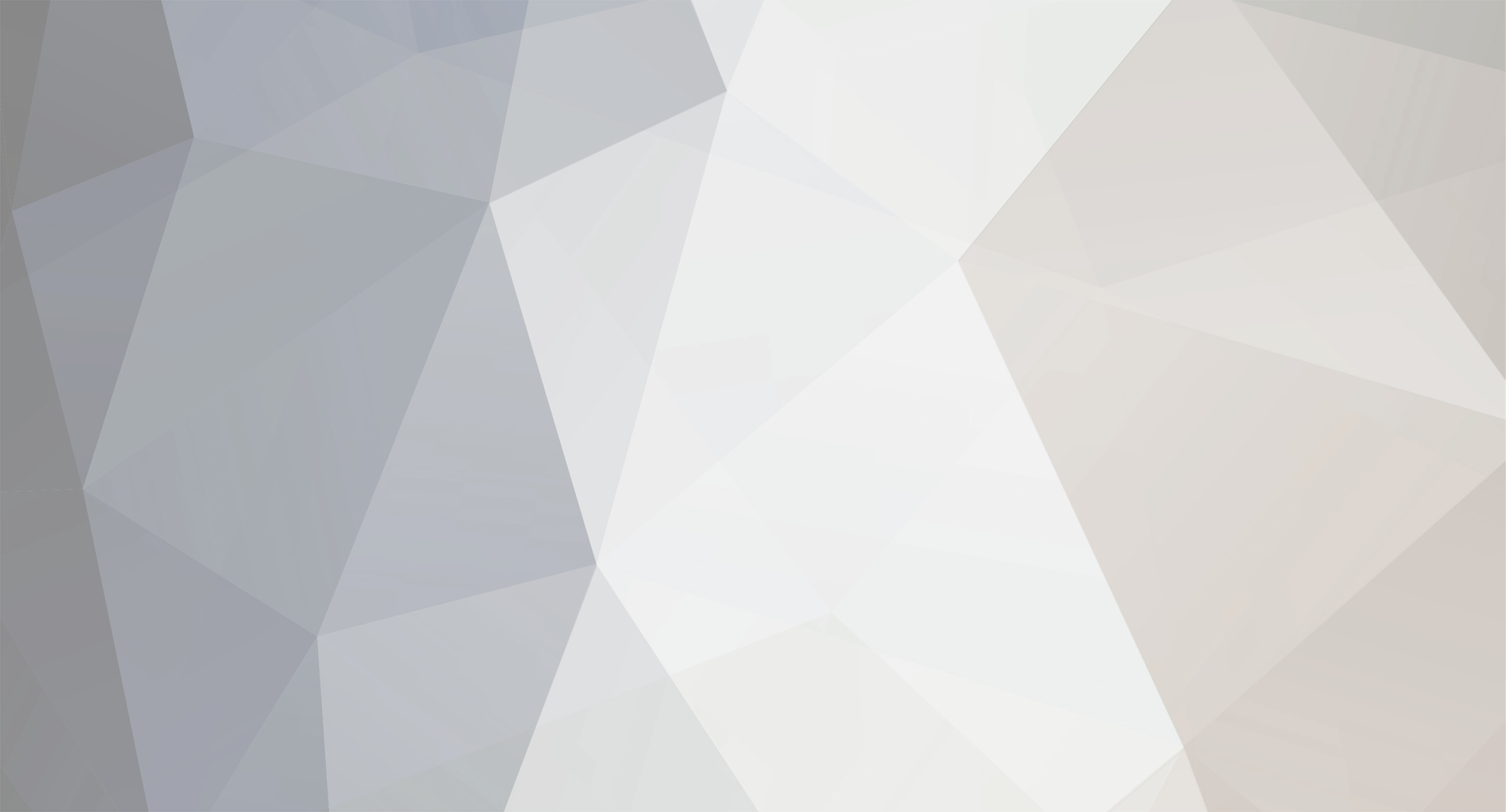
RedBaron
Members-
Posts
223 -
Joined
-
Last visited
-
Days Won
1
Content Type
Profiles
Forums
Blogs
Gallery
Calendar
Downloads
Everything posted by RedBaron
-
Phil's PSS Jet Provost - Build Blog
RedBaron replied to Phil Cooke's topic in PSSA Mass Build 2014 - Jet Provost
Nice one Phil. Andy did a good job on the plan and Traplet the parts Best wishes RedBaron -
Jet Provost Build by RedBaron
RedBaron replied to RedBaron's topic in PSSA Mass Build 2014 - Jet Provost
01/02/2014 - I did not fancy trying for 32 and 64 sides, so a change of approach is needed now. I felt it really was worth the trouble to make up some cardboard templates illustrated below. The fuselage will have to thread into the templates as far as the required station. I decided to do a bit of final shaping around the nose and F1 as a trial and it looks pretty straightforward given the accurate roughing out already done. The plane has been put away and I used two small sanding blocks medium and fine to remove the edges and a builders flexible sanding pad, rough one side and medium the other. This is best done in a strong slanting light to show up irregularities (lucky the sun came out for an hour). It may be worth drawing your attention to the black stuff on the building board. This is a sort of fine rubber mesh, I purchased it some while ago from a wood workers tools and supplies business, it is a soft anti-slip mat to go on the bench to stop materials sliding around. Just the job when handling soft balsa parts such as planing and sanding this fuselage. Edited By RedBaron on 01/02/2014 15:19:17 -
Jet Provost Build by RedBaron
RedBaron replied to RedBaron's topic in PSSA Mass Build 2014 - Jet Provost
Thank you David for commenting, it is much appreciated. 01/02/2014 - The fuselage progresses. The part over the wing bay is now covered. When I looked in detail at the curve (it is not a simple curve) I doubted my ability to sheet the area from one piece, so I planked it carefully. In the photograph below I have not done any sanding yet. The balsa plane has been working hard and the fuselage forward section is now eight sided. Follow Andy's advice and be bold with the plane (but only if you have marked all the guide lines for cutting). For the first time I can really believe that some elegant curves are hiding inside the balsa. I have now marked up the fuselage ready to make it a sixteen sided shape. If you do this use a coloured pen different from that used for the eight sided lines. I also made a 22.5 degree wedge to mark up the sections on the plan to aid transferring measurements to the model. Here is what it looks like at this stage: The top wing skins are ready to be cut roughly to shape and then be applied to the wings, however before that we must face the matter of the "Weenie Washout Wedge". This is going to get it's own section in my NoteBook. Not bad for such an apparently insignificant thing. I know most of this will be well known to most of you, but as a full size glider pilot I feel that there is still more to say on this subject. This section coming soon. There will also be a short test when you come to fly your Jet Provost Edited By RedBaron on 01/02/2014 11:44:25 -
Hi Rez, Looking good! I would like to apologise if I caused you to over order. Originally in my NoteBook I listed what I ordered (to stock up). I thought I had mentioned that. As I have actually used wood I have gradually changed the numbers to reflect what is really required. Instead of building 3 JPs why not one as per plan and then a twice size jobby? Best wishes RedBaron
-
Jet Provost Build by RedBaron
RedBaron replied to RedBaron's topic in PSSA Mass Build 2014 - Jet Provost
If you are new to this particular thread don't forget that my real NoteBook on the JP build is kept on SkyDrive. You can view it and see all the details by using this link: **LINK** On your first visit to the NoteBook, if you bookmark that page in your browser it will save me keep putting the link in multiple places here. Also it will be quicker for you to check the shopping list therein or any other sections. Manythanks RedBaron -
Jet Provost Build by RedBaron
RedBaron replied to RedBaron's topic in PSSA Mass Build 2014 - Jet Provost
31/01/2014 - More on Octagonals. With the forward block work complete, I squared everything up to the horizontal and vertical plan profiles by planing and by using the disk sander. Thinking further I decided that there was no need for octagonal templates. I marked up centre and datum lines on the forward fuselage. I drew 45 degree lines on the profiles on the plan and transferred the measurements to the fuselage and joined the dots. Careful work with the balsa plane and disk sander should give me a nice eight sided front fuselage as the next step to finished curves. I should note here that unless you are going in for a scale competition, symmetry and a pleasing shape reasonably close to that required will be quite satisfactory for happy flying. If anyone wants to measure your JP with a micrometre just draw their attention to the lovely finish. The following photograph shows what it looks like at this stage: -
Jet Provost Build by RedBaron
RedBaron replied to RedBaron's topic in PSSA Mass Build 2014 - Jet Provost
Thank you for your comments Techy111 - I am with you on the Bucc (with all the interesting optional armaments) My JP is going to be XN595 (because I can buy a decal set) If I like how it flies (don't tell anyone else this) but I have in mind a twice size one with flaps and all the working bits and perhaps a different colour scheme. But perhaps I had better finish my big B52 first.... I think XN595 is a JP T3A for more information see http://www.jetprovostheaven.com/index2.html and http://www.abpic.co.uk/photo/1124057/ -
Jet Provost Build by RedBaron
RedBaron replied to RedBaron's topic in PSSA Mass Build 2014 - Jet Provost
30/01/2014 - Wing and fuselage progress. Today the wings were joined as discussed above and are now awaiting their top skins. The block balsa for the forward section of the fuselage will be complete by the end of the day. Then after some rough planing, I plan to use my disk sander to "square-up" the fuselage to the horizontal and vertical profile. Because I am not much of a freehand carver I will be making templates to help complete the job. Firstly a set of "Octagonal" templates to get the bulk of the shape right and then a set of templates as per plan sections to get the final shape. The octagonal templates will be easy to make from the sections on the plan by drawing 45 degree lines just touching the section proper. I will do some photographs of the blocked up fuselage and octagonal templates tomorrow. -
Jet Provost Build by RedBaron
RedBaron replied to RedBaron's topic in PSSA Mass Build 2014 - Jet Provost
29/01/2014 More Stuff. I am really glad that I decided to play with dihedral at this stage, I kept thinking about it all through lunch, this did not help the Brownie Points situation with the Lady of the house! Here are some observations on setting the dihedral: I still recommend building the wings to this stage on the joined lower wings skins, but now is the time to carefully separate them. The instructions suggest skinning and then letting the ply joiner into the wing through top and bottom skins. There is nothing wrong with this but I doubted my own ability to do this neatly as a last step. Having separated the wing halves I checked the angle of the root ribs and did a trial assembly without the dihedral brace and found a really minor imperfection stopped me from achieving the correct dihedral. This was easily fixed using a big Perma-Grit sanding block and some very careful sanding of both root ribs. Thank you Traplet for including the dihedral jigs in the Cut-kit, but I do recommend adding some simple balsa feet (else they with drive you crazy with their falling over, and clearly mark the front edge of each jig. Next I decided to cut down through R1, R2 and R3 to trial insert the dihedral brace and found that the brace as supplied is only tall enough to fit between the wing skins not through them. I think that this is good, so Traplet please do not change a thing. It isn't easy to cut thin slots in structures. A search in the tool box found an old broken hacksaw blade that gave exactly the right width of cut. Using a piece of thick ply as a guide it was the work of moments to cut the required vertical slots down through the ribs. This made up my mind to join the wings now and skin the tops in a following action. Doing this means that the top and bottom skins will need not cutting or making good or further sanding after wing brace fitting. The next step was to glue some 3/32 in square section scrap balsa onto the lower wing skin next to the wing web. This means that the wing web the dihedral brace and the 3/32 square top spar and bottom scrap make a nice dihedral / spar box. I think that now that I have full access for gluing I will use PVA for maximum working time. Here is a picture of the whole wing jigged and clamped up ready to glue: Edited By RedBaron on 29/01/2014 16:01:44 -
Jet Provost Build by RedBaron
RedBaron replied to RedBaron's topic in PSSA Mass Build 2014 - Jet Provost
PS - A small accident: When I fitted the scrap balsa over the torque tubes I had a small accident with the Cyano!! A drop of Cyano ran down over the blue bearing and onto the carbon rod……. Ouch, luckily I spotted it as the drop was still running and spreading. Quick work stopped the bearing being seized. After a careful clean up with Cyano cleaner I decided to secure the blue bearings not with Cyano but with UHU (POR was all I had to hand) this gives good risk free grip for this job. -
Jet Provost Build by RedBaron
RedBaron replied to RedBaron's topic in PSSA Mass Build 2014 - Jet Provost
29/01/2014 Both wings now to the same state of build. The servo box frames have been installed, a last clean up over the spars done and also a careful shaping of the top edge of the false leading edge accomplished. Do keep the taper even and symmetrical for each wing. I can't think of a reason not to make up the top skins and fit them now. Maybe a play and check with the dihedral brace and the actual dihedral amount first. Here is what it looks like at this stage assembled with the fuselage to check adequate clearances inside. The Rx will probably be mounted with Velcro on the top of the fuselage servo plate between the two servos. If there is anyone reading this who has never done a scratch build before, then it is time for my first confession…. This is my first scratch build for forty years. Modern glues and materials are quite new to me in modelling applications. What was I doing for those forty years? Well I got side tracked into serious full size gliding and have only very recently caught the r/c bug again. This really is a beginners model to build, at least in my opinion. Here is my Skydrive Notebook link again to find all the updates: **LINK** -
Jet Provost Build by RedBaron
RedBaron replied to RedBaron's topic in PSSA Mass Build 2014 - Jet Provost
28/1/2014 - I have installed the first torque tube now. No problems here just mark out the tube centre line on the top of the ribs, this being inline with the aileron hinges. Using this as the datum mark out the cutting lines to suit your torque tube bearings and cut almost to the bottom of the rib. Use a sharp knife blade to remove required amount to line up the torque tube and hinges in this plane. Here is what it looks like now, note the aluminium tube in the aileron to take the wire snuggly. I still have to put the scrap balsa over the torque tube slots. Then repeat everything for the other wing, design the servo box / mount and I will be ready to fit the top wing skin. -
Jet Provost Build by RedBaron
RedBaron replied to RedBaron's topic in PSSA Mass Build 2014 - Jet Provost
25/01/2014 - I have had a busy week on other activities, but have still accomplished some progress on the wings. Nothing picture worthy yet, but you might want to see the detail notes in the build notebook: **LINK** -
Jet Provost Build by RedBaron
RedBaron replied to RedBaron's topic in PSSA Mass Build 2014 - Jet Provost
Thank you for your question Matt, Yes the gap is deliberate - as per plan. The tiny rib at the inboard end of the aileron is at right angles to the hinge line. The main ribs are not. After the top skin is applied a small piece of balsa is shaped to fit the gap (glued to wing) and is faced with 0.4mm ply. Hope that clarifies things Best wishes RedBaron Edited By RedBaron on 22/01/2014 12:37:36 -
Jet Provost Build by RedBaron
RedBaron replied to RedBaron's topic in PSSA Mass Build 2014 - Jet Provost
21 January 2014 Flying has been interferring with building, but I am not complaining. Basic wing structure done and one built up aileron installed. In my NoteBook link earlier in the thread I have included the extended wing tip ribs for anyone going this route. Having got this far with the wing it seems natural to use the lower wing skin as the wing trailing edge adding two staggered laminations of 1/32 inch hard balsa. I intend to keep the t/e quite blunt, not less that 1/16inch and with a sharp vertical edge. In theory this will control the boundary layer better (not sure at this size?) but whatever don't try to round off the t/e. Next will be finishing up the other wing and installing that interesting torque tube. -
Jet Provost Build by RedBaron
RedBaron replied to RedBaron's topic in PSSA Mass Build 2014 - Jet Provost
19 January 2014 Not a lot done this weekend as nice weather and flying all day hmmmm. Well I did get the lower wing skins joined, ribs and spars and webbing glued up (R1s not glued yet). What a beautiful little structure. I decided to build on the complete lower wing skin. Hopefully making the wing join - dihedral work simpler as root shapes will be truly identical. The thought being that I would cut a narrow V cut-out in the centre to accommodate the curve-up of the sheeting. Also at the point of setting the dihedral to score a shallow cut underneath the wing to facilitate the dihedral, and that the wing halves were never be completely separated. The other thought I had was that I would like to do built up ailerons, fit pinned-hinges and the torque rods getting them lined up properly before the top skin goes on. This may seem like a lot of trouble compared with the simpler sheet aileron idea, but I just like engineering in wood. Use the link to my NoteBook for all the details. Edited By RedBaron on 19/01/2014 21:57:49