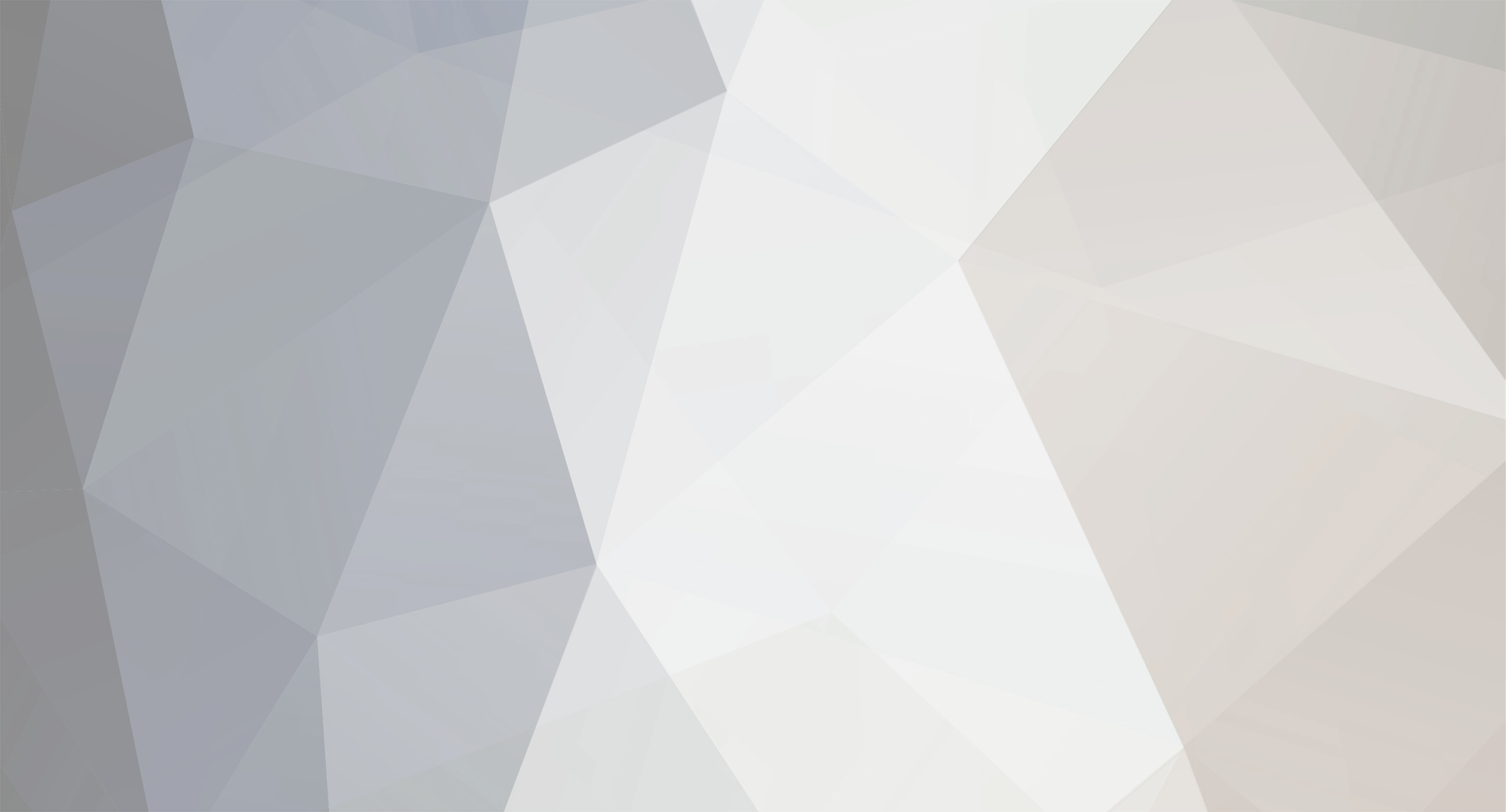
J.N.
Members-
Posts
122 -
Joined
-
Last visited
Never
Content Type
Profiles
Forums
Blogs
Gallery
Calendar
Downloads
Everything posted by J.N.
-
Posted by J.N. on 31/10/2015 15:23:57: I need to make up a glow plug removal tool due to choosing a model of glow engine that places the glow plug very close to the fire wall. I dare not remove anymore of the woodwork in the engine bay and by making up a section of hexagonal tube I will be able to remove the plug without having to first remove the engine. I am trying to source a length of hexagonal tube with an outside across flats width of 10mm and an internal across flats width of 8mm. The attached photo of the end of a glow plug tool is an example of what is needed. If all else fails I could buy a section of 8mm across flat width hexagon solid bar ( which is readily available) and use is as a former to hammer the glow plug tool around it. However, I much prefer to use hexagonal tube and cut to size but I have not had any luck in sourcing a suitable piece of steel hexagonal tubing . Does anyone know where I can buy a small length of steel hexagonal tube as above, or a full length fully formed box spanner, 10mm outside, 8mm inside. Thanks, I have resubmitted with a photo, a photo is worth a thousand words. As you can see there is not much room to play around with, around 18mm. If I can make up a section of tubing to slip over the plug I can then use an open ended spanner to unscrew the plug. I agree that it may be possible to use a tommy bar but it would not be able to pass through the tube due to fouling the plug.
-
I need to make up a glow plug removal tool due to choosing a model of glow engine that places the glow plug very close to the fire wall. I dare not remove anymore of the woodwork in the engine bay and by making up a section of hexagonal tube I will be able to remove the plug without having to first remove the engine. I am trying to source a length of hexagonal tube with an outside across flats width of 10mm and an internal across flats width of 8mm. The attached photo of the end of a glow plug tool is an example of what is needed. If all else fails I could buy a section of 8mm across flat width hexagon solid bar ( which is readily available) and use is as a former to hammer the glow plug tool around it. However, I much prefer to use hexagonal tube and cut to size but I have not had any luck in sourcing a suitable piece of steel hexagonal tubing . Does anyone know where I can buy a small length of steel hexagonal tube as above, or a full length fully formed box spanner, 10mm outside, 8mm inside. Edited By J.N. on 31/10/2015 15:25:17 Edited By J.N. on 31/10/2015 15:26:34
-
Posted by simon barr on 16/02/2015 09:43:31: Hello J.N. Yes, connect the right aileron to Ch 1 and the left to Ch 6. Then make sure that both the flap setting FLPR, and the flap trim FLTR are set to zero %. Scroll down to ELVN, and that should be just flashing three lines... That should now have connected the two aileron servos, which will allow independent setting up for each servo. Thanks. I needed to know which direction I was heading before I got around to twiddling with the computer thingie.
-
I have a Futaba 6 channel 6EXA 35MHz. and having difficulty in equalizing the wing aileron movement, driven by a single servo in a model I am building. An easy solution would be to fit an aileron servo for each wing half. In two recent articles in the RCM&E I have read that by fitting two servoes, one driven by channel 1 and the other driven by channel 6 will allow me to individually set each servo independent of the other. My instruction book for the 6EXA states that coupling channels 1 and 6 in the Flaperon mode will achieve the independent setting but servo travel will be reduced to 60% and 40%, I presume this has something to do with the Dual Rate Switch. All I want to do is to be able to have normal aileron movement as per the building plan for straightforward leisure flying. Can someone please advice if the Flaperon mode on my set is the way to do it. Thanks.
-
I am genuinely puzzled with regard to the following question and it is not an attempt to instigate a protracted discussion. I was about to solder some gold plated connectors then thought to check if a dedicated solder/flux was needed (as with soldering stainless steel) and then call in at Maplins to buy the necessary solder. I looked up the internet and read an interesting article on the Wikipedia site. It was stated that soldering gold plated connectors had its problems in that the gold and solder melt into each other to a greater or lesser degree, leading to complications. I know it is all very technical and way above my retirement pension grade but I will be interested to know what is what. In the meantime I will solder the gold connectors with my normal resin cored tin/lead solder.
-
I recall reading about the types of electric connectors in a previous issue of RCM&E. I thought it was a dedicated feature around mid 2014 however I have looked through the whole (less Jan 2014) of 2014 and the whole of 2013 and I cannot find it, unless of course it was in the Jan edition. Can anyone please point me in the right direction. Thanks.
-
Posted by Essjay on 23/01/2015 22:11:21: Probably too late now but Maplins have them Link Edited By Essjay on 23/01/2015 22:28:16 Edited By Essjay on 23/01/2015 22:28:39 Thanks. Yes I have ordered 2 x sets from another source. It appears that I had the wrong description for the U.K., these connectors are called SAE and only known as trailer connectors in the specialized motor trade.
-
Posted by J.N. on 22/01/2015 20:56:32: SORTED. Found a U.K. source. J.N.
-
Posted by Brian Lambert on 22/01/2015 22:52:14: Like these? Link Yes just like "these" however the postage is the problem. Thanks. Edited By J.N. on 23/01/2015 09:08:17
-
Does anyone know where I can obtain a 2 pole connector similar to what is shown in the photo. This particular connector is part of my Yuasa battery charger. Similar connectors are common in the USA, and called Cole Hersee Universal Trailer Connector 2 Pole, or bullet connector, however, having connectors sent over from the USA is a very expensive option. I want to make up a couple of dedicated fitting charging leads to enable me to use the one charger for various charging needs and need to source some connectors, failing this type of connector does anyone know of an alternative. Thanks.
-
The photo is a typical situation of the problem I have with drilling holes in tight spaces. In this particular instance I am using a collet holder with a 2mm drill, bit turned by hand to drill through 3mm light ply and then use a 4.5mm drill bit, on its own, by hand. In thin light ply I can manage but the problem arises when it is ply or wood in a space that is too small to use a hand. I am looking for a tool that will allow one handed operation and able to hold up to a 4mm drill in either a chuck or collet. I have looked at battery powered drill/grinder multi tools (such as the Proxxon) but you get a lot of bulk to power a small diameter drill bit. I am wondering if a flexible shaft drive is the way to go. Has anyone any advise. Thanks. Edited By J.N. on 19/10/2014 14:00:59
-
Posted by Ruprect Spode on 07/03/2013 11:37:14: Nothing beats a long cold soak overnight. Using heat/steam and chemicals only serve to break down the fibres and natural resins within the wood and when it dries it becomes brittle. OK they are only models and I suppose speed of construction is an issue. Yes it can be done. This is as per the bath. The balsa sheet is 3.25mm thick soft to medium grade and was slowly tightened around a former over a period of 2 days and then left to dry. . Edited By J.N. on 10/02/2014 10:53:47
-
What was the outcome of this topic. I bought a SHM glow support some years ago and have been pleased with its performance, backup and help from SHM. I need to fit another model with a glow support and although I am happy to stick with what I know ( if it aint broke type of thing) I wonder if I should consider a more modern offering. The price of a unit is not an issue.
-
Posted by Bob Cotsford on 14/01/2014 12:33:22: APC are a fair bit quieter than the blunt Graupner props on our club noise meter, and I'm pretty sure they give notably less thrust. Graupner Sonics are ok, they are similar in shape to APC. It did occur to me that the Graupner Sonic is similar to an APC. Perhaps Herr Graupner can throw some light onto the query. J.N.
-
On my glow engined models, ASP, OS LA, OS FX, and OS four stroke, I am using a mixture of standard Graupner propellers and standard APC propellers. I suppose the Graupner could be considered wide and the APC considered a scimitar shape, no matter, the two are shaped very differently. I am using APC because Just Engines recommended them and Graupner because I included them when I made up an order for Graupner bits and pieces. Since then, I have continued to buy both makes. I am aware that us mere mortals are advised to try different propellers but I cannot tell any difference, perhaps because I just plod around the sky. Can some expert please tell me why one shape of propeller (as above) is better then the other.
-
I have a small disc sander in my work room and have found it so helpful that I now want a small portable bench top; belt sander, or linisher. At the moment the belt sander will not have to deal with much work but as always, once it is in use I will ask myself why did I not buy one years ago. Unfortunately I cannot source a suitable belt sander, all the small machines I have come across are belt and disc. Does anyone know of a stand alone bench top belt sander fitted with a sanding table suitable for model work, or, can anyone recommend a combined disc/belt sander. My disc sander is a Proxxon and along with my other Proxxon tools I have come to realize that price is not always the best way to chose a tool.
-
Posted by christopher small on 06/01/2014 20:28:33: My workshop is 12 feet by 18,and is the end bay of a 3 bay barn,feather edge boarding on 2 sides,box profile tin sheeting on other 2 sides,i am currently insulating it with kingspan and 3/4 inch ply on top,but some mornings the cupboard doors are soaking wet as are my plane wings i have a small electric heater on at night that helps,but still very damp especially in this very wet weather,what can i do?does any one else have this problem? Chris I have 2 wood sheds a 24 x 10ft and a 24 x 6ft. Both have a; Ruby Dry DH 600 (b) UK, dehumidifier in place. The Ruby Dry is not cheap however it does the job and after buying and using the first one, I bought a second. It will run all day and every day, as long as you empty the collection tank and heed the instructions regarding the filter. It has 3 pre-set humidity levels plus a manual overide to lower the setting from the pre-set minimum. I recommend this dehumidifier, is is designed for cold situations and ideal for sheds, it will put a little bit of heat into the area and over the last 3 years has prevented freezing in the shed with overnight outside temperature of minus 7C.
-
Posted by PeterB on 09/08/2013 20:00:10: Hi, Were did last year go!!! and this year seems to be going the same way, but with a bit more flying!!! Anyway I did fly the Storch last year two or three times and the mods were just great, no wing movement. then I, not the aircraft, dropped a wing coming into land. More repairs, broken rear spar and a damaged flap and a couple of ribs. Root rib not damaged so repairs didn't take long. Full test flight carried the other day including flaps, no trim needed so I am really looking forward to flying her a lot more. I think one of the lads took a couple of photos so if I get a copy of them I will post them. Peter Very pleased to hear that you are making good progress. Trying to complete my Storch came to a halt early last year, the last 18 months have been filled with every family committment in the book. JN
-
I have to replace my sealed lead acid battery that powers my flight box (glow plug and starter). The battery is 12v 12AH and weighs around 4kg. I bought this battery in order to ensure that it would hold its charge throughout the day however I now wonder if I could use a lighter but smaller capacity battery. Can anyone advice as to what they would consider to be a minimum capacity sealed lead acid battery for a days flying. I believe the construction of a battery may effect its weight (such as a gel battery), or, are all lead acid batteries much of a muchness regarding weight. Thanks. Edited By J.N. on 02/03/2013 13:03:27
-
I have a Futaba R136F receiver with a snapped aerial lead 20mm from the printed circuit board. I am reluctant to re-solder the lead onto the board because of heat transfer even though I am familiar with heat sinks, I thought to bind and solder the lead together. Can someone please advise. Thanks
-
I thought to ask the likes of Peter Miller this question but decided to spread the net wide. I have built a model with the whole rear tail assembly in balsa sheet (Flair Cub), another with a fully built up rear assembly including elevators and rudder (Flair Magnattila) and yet another with a mixture of both (Jensen Das Ugly Stik). For the life of me I cannot see why one design is superior to the other, can someone please advise. In addition, is their anything to be gained by modifying such balsa sheet sub assemblies by say, cutting out sections to leave thick ribs in an effort to reduce nose heavy models.
-
Posted by RAF-P on 25/02/2012 19:53:21: Hi Some photos and info on my repairs Marked hole centres on wing root rib 1. These hole centres are the same on the fuselage centre section items 9 and 10. These 2 photos show the Tee nuts fitted with a 1/16 ply packer. The packer is required to allow just enough of the tee nut (see next photos) to locate into the holes drilled in the fuselarge centre items 9 and 10 I cut a slot into both sides of thr fuselarge at frame 7 for a new bracket (next Photo) The brackets are attached to Frame 7 inside the fuselage with epoxy and 2 servo screws( see photo) The last photo shows both wings refitted. Not easy as both nylon bolts have to go from the fuselage at frames 9 and 10 into the wing root!!! But it works with no movenent of the wings. I have up loaded these photos plus some general ones at My Photos in the Storch Repairs Album. I still have to recover the wings at the root and tidy up the rest, plus all the RC gear as to be refitted. My only bad thought is that it will not all that crash proof. I may have to think of a shear point, ie a waiste near the blot head. Peter Edited By RAF-P on 25/02/2012 19:55:43 Edited By RAF-P on 25/02/2012 20:13:03 Thanks for the time and trouble you have taken. You have a valid point regarding a sacraficial fitting for the wing anchorage, an alternative arrangement could possible be to make such a fitting bombproof. I am some way off reaching the point when I will have to decide. Jeff
-
Posted by RAF-P on 22/02/2012 20:17:45: Hi Just to let you know that I have started on my repairs. What I will try to do is work out everything on one side and then do the other taking photos at different interest/help! points. It looks like I will be going with two bolts at the wing root and replaceing the wing strut/fus connection with a dural plate. Peter Glad to hear you will let us all know how you progress. I was lucky not to have reached the stage of completing the fuselage planking down to the fuselage when I was warned of the undercarriage and wing support weak points. I have sandwiched the bottom part of all the above involved fuselage formers with 2mm ply and epoxied a 4mm ply sandwich around the 2 main undercarriage supports at the fuselage keel. The undercarriage linkage will be held in place in the fuselage former mounts with soldered on end washers. I received a new size 80 Laser this week for my Storch but will not get around to fitting it for some time yet. Regards
-
Posted by RAF-P on 18/01/2012 15:25:32: Posted by J.N. on 17/01/2012 20:29:23: Posted by RAF-P on 16/01/2012 21:48:40: Posted by J.N. on 16/01/2012 21:12:46: Posted by Seamus O'Leprosy on 16/01/2012 20:54:57: By the way mine are dural not carbon, the kit was purchased this year I wonder if this is significant, what thickness are your Dural wing connectors? RAF-P. I think it will make your life a bit easier Seamus. Not only I think you will not have the same wear problem at V slot, but also the carbon joiners really do flex forward and backwards a lot. I bought my kit nearly ten years ago!!! It seems that they must have had a few complaints and change the joiners from carbon to Dural. Peter Howabout dowels set into the Nose Ribs (item 9 and 10) to engage into the wing root rib as each wing is fitted, this would overcome the wing joiners flexing. It would also help if some means could be found to tighten the wings onto the Nose Ribs and hold them in place. I got my nylon screw size wrong the other day, 3mm really are too small. I think even 5 or 6 mm thread depth is to small to really have a safe pull. I sent for some 1/4-20 UNC nylon slotted hex head screws and 1/ 4 UNC-20 captive tee nuts. They arrived today and I think they are just right. Also one will be able to use a screwdriver or socket, which ever is easier for access. I don't think you will need to dowels then. If I remember I don't think that there is much space in the wing for the screw, so the tee nuts will be fitted in the wing with the bolts in centre section. How and were I don't know yet, it's just an idea. Peter @import url(/CuteEditor_Files/public_forums.css); I have always found that a socket cap head (allen key drive) screw is best suited for tight places. The cranked end of an allen key will give you all the leverage you need and if it is a really tight spot, shortening the working end of the key will give you more clearance. I am puzzled as to why you are using a UNC thread, is it because of convenience?Model Fixings have all manner of fasteners in all manner of threads, head drives and metal. The service is quick and you can buy small quantities. Please keep all of us informed.
-
Posted by RAF-P on 16/01/2012 21:48:40: Posted by J.N. on 16/01/2012 21:12:46: Posted by Seamus O'Leprosy on 16/01/2012 20:54:57: By the way mine are dural not carbon, the kit was purchased this year I wonder if this is significant, what thickness are your Dural wing connectors? RAF-P. I think it will make your life a bit easier Seamus. Not only I think you will not have the same wear problem at V slot, but also the carbon joiners really do flex forward and backwards a lot. I bought my kit nearly ten years ago!!! It seems that they must have had a few complaints and change the joiners from carbon to Dural. Peter @import url(/CuteEditor_Files/public_forums.css); Howabout dowels set into the Nose Ribs (item 9 and 10) to engage into the wing root rib as each wing is fitted, this would overcome the wing joiners flexing. It would also help if some means could be found to tighten the wings onto the Nose Ribs and hold them in place.