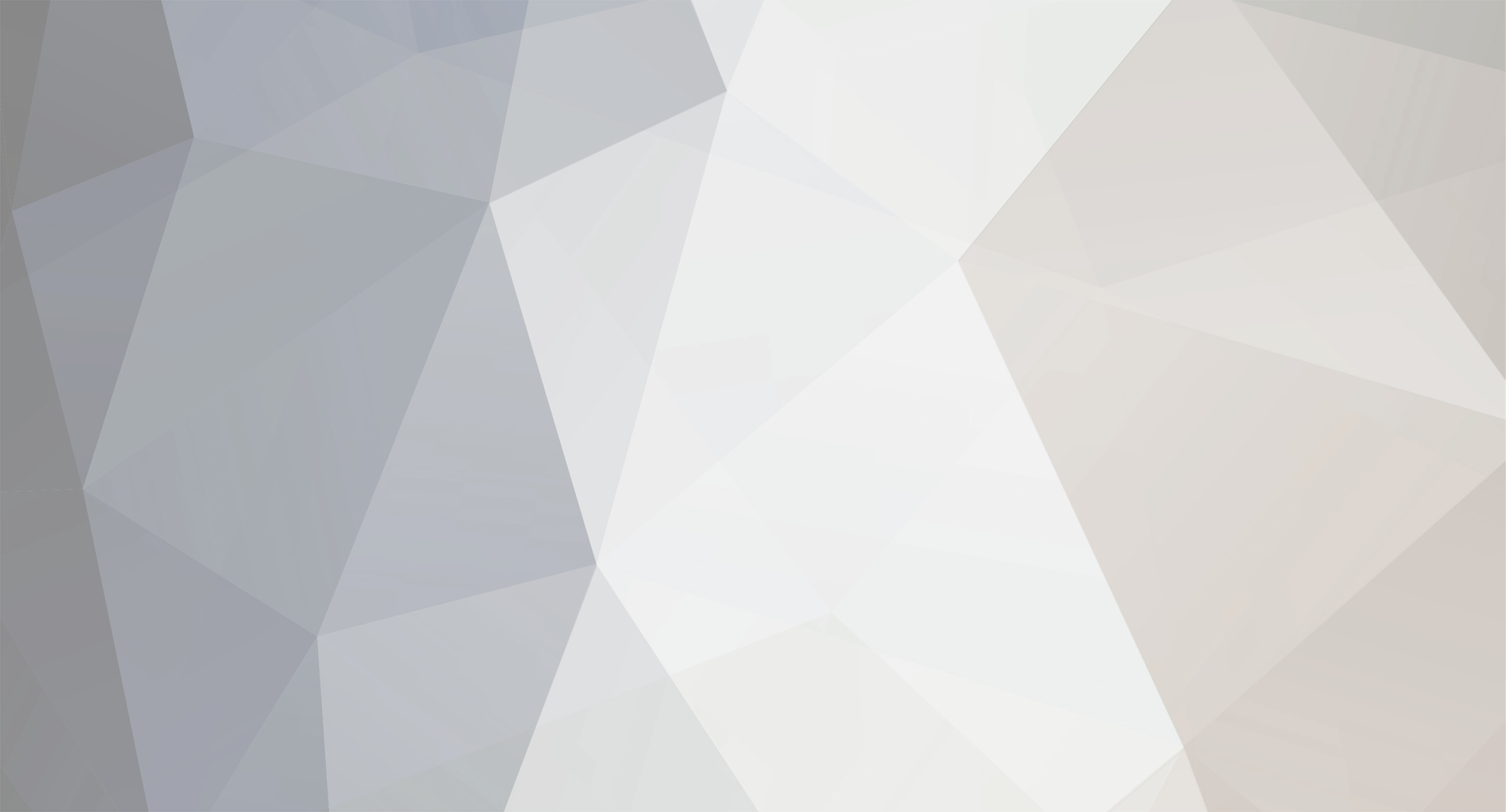
Roberto Gava
Members-
Posts
67 -
Joined
-
Last visited
Never
Content Type
Profiles
Forums
Blogs
Gallery
Calendar
Downloads
Everything posted by Roberto Gava
-
I had the .40 version of the Phoenix Tiger and It's quite similar to the Calmato. Mine is on the woods due to a faulty receiver (I changed the radio gear and did wrong the range test). If you feel that you will enjoy flying a model like the calmato, the Tiger is a very good choice. If you think in going for a more maneuverable model, then take into account the other recomendations in this thread. Also you can enjoy repairing your Calmato. It is in very good condition for repairing!Edited By Roberto Gava on 09/08/2010 22:09:39
-
Build of an old Graupner Eurofighter
Roberto Gava replied to Roberto Gava's topic in Build Blogs and Kit Reviews
Hello again. I'm here with more pictures of the build. Nose structure, glued with ciano, presented over the wings to verify the alignment before gluing it. Same with the tailboom structure. Both structures glued to the wings with white glue. Now, according to the instructions, it's time to start with the cockpit. I think it is to take profit of the waiting to the white glue curing time. In fact, it is different to the real one. I found this picture on the net. I still don't know if I will work on a new one more similar to the real one. I think I will do it first with this one to test its flying characteristics. -
Build of an old Graupner Eurofighter
Roberto Gava replied to Roberto Gava's topic in Build Blogs and Kit Reviews
I've been doing a few advances on it. During the week, I glued the nose and tailboom structures on plywood. Now I have to glue them over the wings. Tomorrow I'll put some pics of them. I'm stuck with a doubt on the instructions (they are only in German), so I posted in a German Forum asking for help. I hope soon it will be solved. Does anyone here can help me with the German translation? -
Build of an old Graupner Eurofighter
Roberto Gava replied to Roberto Gava's topic in Build Blogs and Kit Reviews
Today I just started the build. Before the Eurofighter I advanced with the reparation of the Olympic. Now some pictures of it! Foam beads joined to support the but join of the wing halves. Testing the join prior to put glue. I decided to use white glue. Wings glued together. Some weigth to fix them in place. -
Build of an old Graupner Eurofighter
Roberto Gava replied to Roberto Gava's topic in Build Blogs and Kit Reviews
Thanks Timbo. This Sunday I'll upload some pics of the progress on it. I just have some hours to work every weekend. -
I just bought the Multiplex at RCTecnic. It comes very complete and seems to work properly.
-
Last week I received from RCTecnic the motor, esc and basic things to start building this plane. Is an old Graupner kit designed for a .25 IC engine in front with propeller. I've decided to make it electric to keep propeller, but allow a much cleaner nose without cylinder head and muffler on the side. I hope next weekend I'll start building it. Here some pictures of the plane and materials. Out of the box Propulsion system (except the batteries, I'll buy a couple of 3700mA 4S LiPo) Detail of the motor (equivalent to a .32 2T glow) Last picture for today, the ESC. Y choose the battery-motor-ESC-Propellers combination to have the same weight as the OS .25 FSR + Full deposit + gas servo + receiver battery and to have a similar power as a .32 glow engine. I hope it will be enough. If you have any comment that could help me, please don't hesitate to make it. Advance will be slow because I only have some time on weekends.Edited By Roberto Gava on 09/06/2010 21:23:00
-
I have seen several IC props mounted on electric motors. You just lose some efficiency and gain a little weight.Edited By Timbo - Administrator on 08/06/2010 21:32:00
-
Hobbyking
Roberto Gava replied to Merlin spit's topic in R/C Retailers / Distributors / Manufacturers
I've read in an Spanish forum that there were a fire in Hong Kong airport due to a package containing LiPo's. So they are reviewing their policy and they started sending back to the sender all LiPo containign packages. -
Prop sizes for 2 completely different engines.
Roberto Gava replied to Braddock, VC's topic in IC Engines
For your particular question I think the 15x6 will suit your flying preferences quite well for the .91 Fx. Better could be a 16x5, but you have to buy it. Regarding the .36. For running-in the best is the smaller recommended prop, but 10x5 should be OK. The 11x4 will be better for slow aero flights. -
The first responsible of my love for planes and flying is Sebastian Bach with his books. I read them when I was young and they were inspiring. Then my brother’s godmother gifts me a German kit to mount a free flight model. After that, in the secondary school I knew my best friend Gabriel and we have the same passion for air modeling. We build some models in parallel. Most of them crashed on their first flight test. But we keep trying and building new ones. That’s my beginning as air models nut. Now I'm an Aeronautical Engineer whose passion for model planes is untouched. Cheers!
-
The more I read the more convinced I'm that calculation software can't be accurate because it starts from data as the motor Kv that it is not clear that it is stated with the same rigour by the different brands. There is also the problem of the propeller behaviour also difficult to calculate with enough accuracy. Very interenting thread. Thanks Tymbo for opening it and all of you for participate and share your knowledge.
-
Posted by Timbo - Administrator on 14/05/2010 23:47:08: I plan on flying the model again tomorrow with the smaller wooden 15 x 8 prop, so that I can compare the data as well as the flight performance. I will be using the exact same battery as with the 15 x 10 APC prop, and plan for a similar flight pattern and time. To recap and summarize the average high figures obtained so far. 4 minute STATIC Amps Watts RPM 15 x 10 APC e 47 650 6750 15 x 8 wooden 56 + 800 + 6500 - 10 minute FLIGHT 15 x 10 APC e 44 625 6700 15 x 8 wooden 50 725 6550 Edited By Timbo - Administrator on 15/05/2010 14:27:24 For me, those figures support my theory about props. The 15x10 prop lost 50 rpm between static and flight test meanwhile the 15x8 prop rose 50 rpm on the air because of the unloading by fwd speed. This can only be explained by the decrease of resistance to spin of the prop in the static test due to the stalled condition of the blade that reduced its induced drag.
-
I can ask him. Maybe I can put you in direct contact. He's working for Airbus in maintainability studies. I'll contact him durign this week and tell you something.
-
Yes, I live in Barcelona. I think the rent depends on the place on the city the flat is.
-
Posted by John Privett on 13/05/2010 21:45:32: OK - I'll stick my head above the parapet, and prepare to have it shot off! In a brushed motor, the commutator switches the power to the right windings at the right time to make the motor rotate. The speed at which the motor rotates (when no load is applied to it) is proportional to the supply voltage. The design and physical characteristics of the motor determine the 'revs per volt.' The brushless motors that we use are really just brushed motors that have had the brushes and commutator replaced by a box of clever electronics. The electronics switch the power to the windings just as the commutator does on a brushed motor. So the speed is still proportional to the voltage. For a given voltage the ESC is simply incapable of making it spin any faster than the kv rating dictates either by warying the timing or by any other means. To reduce the motor speed, I believe the ESC reduces the effective voltage supplied to the motor by very rapidly switching the supply on and off. So 'on' for half the time and 'off' for half the time is effectively half the voltage, 'on' for 10% of the time and 'off' for 90% is effectively one tenth of the voltage and so on. Right, fire away... Corrections and/or refinements to the above are welcome! I follow your explanation and I've a couple of doubts: 1 - In a brushed motor conmutator is mechanically driven by de shaft, so the conmutation speed is proportional to the rotation speed. So, in this case, the higher the voltage, the stronger the magnetic field and more revs is the result. 2 - In a brushless motor conmutation speed is defined by ESC (I don't know if it is variable or not) At this point I see two posibilities: a - ESC functioning at a fixed conmutation speed and reducing efective voltage as you said resulting in higher diference (slip) between magnetic field rotating speed (fix) and rotor speed. b - ESC is varying conmutation speed proportionally to the throttle stick position and maybe reducing also efective voltage to reduce motor speed and reaching a maximum conmutation speed and voltage at top throttle that, according to motor Kv rating results in actual maximum revs (always affected by slip proportional to the resistance of the prop to spin and inverselly proportional to the effective voltage supplied to the windings.Edited By Roberto Gava on 14/05/2010 21:38:23
-
The only answer I can tell you now is that I've a colleage from University living in a rented flat in Madrid with 4 beedroms and he's paying 1000 € per month. If you want any help from me, dont hesitate to ask.
-
Last weekend I saw in my club the RCTecnic Zlin Z-50. For me seems like a very nice any day model. Also I have the Phoenix Model Tucano (very similar to the PC9) and it is also a nice semi-scale all day model. This week I finished lowering the position of the deposit to avoid carburation changes from normal to inverted fly and carburettor leackage with the engine stopped.
-
Resuming the original topic of motor Kv. Can someone explain me why a brushless motor changes its rotating speed according to the applied DC voltage to the ESC? Correct me if I'm wrong. But I undestood that Brushless motors are similar to three phase asynchronous AC motors. If it is right, they create a rotating magnetic field by the combination of the three phace AC over different windings in the stator and the rotor magnets follow that rotating field. In this case, the speed is defined by the AC current frequency created by the ESC. Are the ESCs changing their working frequency according to their feeding DC voltage to emulate the behaviour of a DC brushed motor?Edited By Roberto Gava on 13/05/2010 20:44:56
-
Some specialized softwares such as Extended Prop Selector or eMotor tells you if the propeller is stalled or near to stall. @Timbo: McLaren F1 F-Duct technology is based on the drag reduction of the rear wing of the car due to the fact that the injected air stalls it. So, a stalled propeller will consume less power for the same revs that one that is not stalled. That's because stall reduces the induced drag. @Brian: stall occurs at a certain angle of attack. In a propeller if the pitch angle is less than the critical stall angle it is not stalled on static test. When the pitch angle is higher than the stall angle, then the displacement speed reduces the effective angle of attack and, being stalled on static it is not at certain speed. I.E. according to EPS, that 15x10 prop is stalled between 0 and 2.14 MPH, it is probably stalled (depending on its profile) between 2.15 and 7.38 MPH and is close to stall between 7.39 and 12.8 MPH.
-
I tend not to buy premium brands because I feel that I'm paying more than they really give. Usually I try to search for VFM brands. The problem is that in our hobby there is a lot of brands and it is difficult to separate good and bad ones. Specially if you are unexperienced as I am with electric flight. Thanks guys for your advice.
-
Hi Timbo, This is my first reading of this thread. Just a comment on your first measurings: A 15x10 prop is stalled in an static test. A 15x8 is close to stall, but it isn't. This should be the reason why you got more revs on the first one.
-
What is special about 'electric props'?
Roberto Gava replied to Nick Farrow's topic in Propeller Selection
As far as I know, IC shafts are subjected to strong torsional vibrations that should be supported by the prop. Also the prop works as a flywheel to give smooth idle. In electric motors there isn't those requirements so props can be lighter to give more acceleration and its shape could be optimized aerodynamically because there is less structural requirements. -
Talking about ESCs. Some tips on how to recognize a good ESC? Remarkable characteristics, brands, aspect?
-
For this I use Extended Prop Selector software. In my experience, I'm not shure of the figures of consumed power against declared power of most IC engines. I tend to believe that declared power data are very optimistic. Once I asked Thunder Tiger technicians by mail and they answered me that they declared power figures on 15% nitro fuel, low oil percentage and small props to get the engine into its high revs band. For example, they declare 1.4 Ps on a PRO .46 and this engine, with a 11x6 prop gets usually about 11500 rpm, that according to the calculations of the software is around 0.71 Hp.