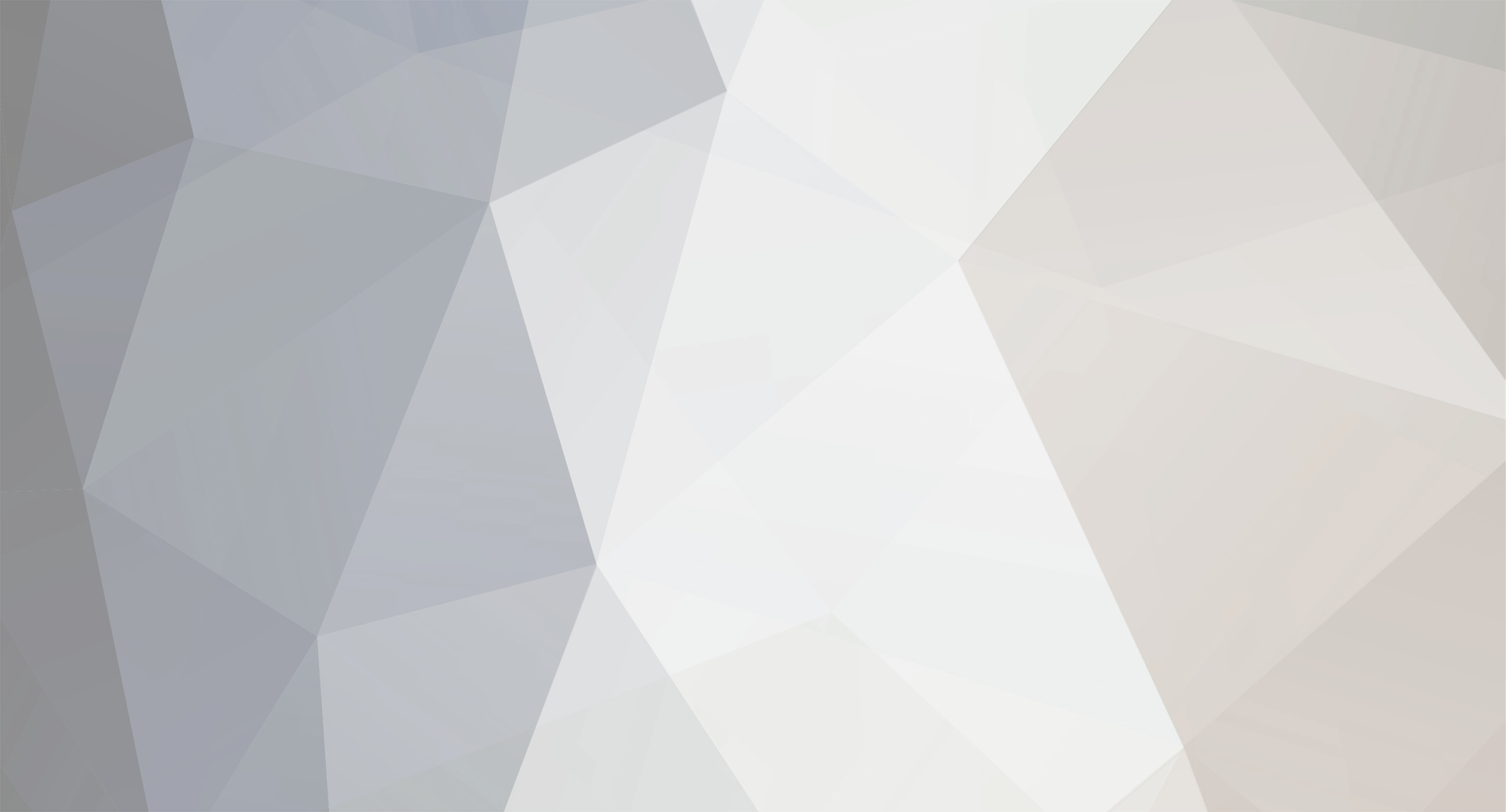
Idris Francis
Members-
Posts
32 -
Joined
-
Last visited
Never
Idris Francis's Achievements
0
Reputation
-
Idris Francis joined the community
-
On board glow driver
Idris Francis replied to Steve Hargreaves - Moderator's topic in Gadgets and Electronics
First, to Stephen Jones - I stll don't know what the flying widgets item you mentioned actually does! To Steve Olsen - many thanks for the detailed explanation. My Series 1 Flight Link Tx design used a valve output stage (in those days transistor output was only just beginning to give adequate power at acceptable cost so I played safe). A 2 transistor inverter used a hand-wound toroidal ferrite core as the HT transformer, from a single 6 volt battery. The HT winding was 1,000 turns of bi-filar wire, wound using a long thin frame that would just pass through the centre even when fully wound. Also a separate winding with far fewer turns to give 1.5 volts or so for the valve filaments...........and also the feedback voltages to make the circuit oscillate, at medium audiio frequencies I think.. The core plus winding was about 1" diameter by 1/2" thick, from memory, the output a couple of Watts or so. It was compact and efficient, and although not small by modern standards, a similar arrangement to step down 4.8 volts to 1.2 volts would be practical for say a 50" span aircraft upwards, being smaller and lighter than a 2000mA NiMh cell switch, harness etc. That said, if I used the Rx battery to drive it (and/or retract U/C that could jam and absorb high stall currents) I would definitely use a throttle fail-safe module that sends the throttle to slow when Rx battery voltage becomes low - but still with enough capacity to land. One of the problems in running a small electronics company, including not only design but manufacturing, sales, accounts and everything else is that there is no time to spare to keep up to date with electronic design, unless vital to the business to do so - which I would like to think (excuses, excuses) why I did not know in any detail, until now, how switched mode supplies work! As I may have mentioned before, Mick Wilshere of World Engines told me that he does not like on-board glows for precisely the reason discussed here - that applying extra heat when already hot from high rpm is not a good for the element - it makes sense to me. Of course we all do, from time to time when starting up and adjusting, but that is rather different from having it come on in flight at significant power settings. But a circuit that measures the temperature eliminates these problems. And of course those systems that switch the power on only at lowish throttle also to, to an extent. Even in the 1960s, it seemed to me, more models were lost due to engine failures at awkward moments than due to radio failure and given the massive increase in reliability of RC since then I suspect it is still true now. It certainly used to be for me (though part of that might of course have been due being less than expert in setting them up in the first place, as Mick is too polite to point out.). It was for this reason that I decided several years ago to try on-board glows and chose the Intelligent Glow unit because the concept made sense to me. Having found that it did what it said on the tin, however, I decided to design the simplest possible circuit to do that same job, at what turned out to be quite trrivial cost. And I am glad I did because they work reliably, give a more reliable idle (also slower if needed) and because it is a pleasure not to have to connect and disconnect an external glow lead, an inch or two from the prop. I set the desired temperature, using a preset, first just to give a visible glow, and then tweaked so that it will just allow the engine to start - by definition, hot enough to keep the engine running. Rather to my surprise, when then checked out of the engine, it turns out not to be the nice bright - yellow approaching white - we normally expect, but simply a dull organge. The LED indicator which glows when starting then flickers a little at idling rpm but does out altoghether at significantly higher rpm. And as mentioned here, using battery power only when it is needed makes sense in several ways, includding tthose mentioned here. I don't have the detailed knowledge to design a switched mode system to go with it, though I probably could an inverter using a toroidal ferrite core. If time permitted I would like to try, but as it does not, will probably not. Edited By Idris Francis on 27/09/2012 22:18:09 -
On board glow driver
Idris Francis replied to Steve Hargreaves - Moderator's topic in Gadgets and Electronics
First, to Stephen Jones - I stll don't know what the flying widgets item you mentioned actually does! To Steve Olsen - many thanks for the detailed explanation. My Series 1 Flight Link Tx design used a valve output stage (in those days transistor output was only just beginning to give adequate power at acceptable cost so I played safe). A 2 transistor inverter used a hand-wound toroildal ferrite core as the HT transformer, from a single 6 volt battery. The HT winding was 1,000 turns of bi-filar wire, wound using a long thin frame that would just pass through the centre even when fully wound. Also a separate winding with far fewer turns to give 1.5 volts or so for the valve filaments...........and also the feedback voltages to make the circuit oscillate, at medium audiio frequencies I think.. The core plus winding was about 12 diameter by 1/2" thick, from memory, the output a couple of Watts or so. It was compact and efficient, and although not small by modern standards, a similar arrangement to step down 4.8 volts to 1.2 volts would be practical for say a 50" span aircraft upwards, being smaller and lighter than a 2000mA NiMh cell switch, harness etc. That said, if I used the Rx battery to drive it (and/or retract U/C that could jam and absorb high stall currents) I would definitely use a throttle fail-safe module that sends the throttle to slow when Rx battery voltage becomes low - but still with enough capacity to land. One of the problems in running a small electronics company, including not only design but manufacturing, sales, accounts and everything else is that there is no time to spare to keep up to date with electronic design, unless vital to the business to do so - which I would like to think (excuses, excuses) why I did not know in any detail, until now, how switched mode supplies work! As I may have mentioned before, Mick Wilshere of World Engines told me that he does not like on-board glows for precisely the reason discussed here - that applying extra heat when already hot from high rpm is not a good for the element - it makes sense to me. Of course we all do, from time to time when starting up and adjusting, but that is rather different from having it come on in flight at significant power settings. But a circuit that measures the temperature eliminates these problems. And of course those systems that switch the power on only at lowish throttle also to, to an extent. Even in the 1960s, it seemed to me, more models were lost due to engine failures at awkward moments, and given the massive increase in reliability of RC since then I suspecy it is still true now. It certainly used to be for me - though part of that might of course have been due being less than expert in setting them up in the first place. It was for this reason that I decided several years ago to try on-board glows and chose the Intelligent Glow unit because the concept made sense to me. Having found that it did what it said on the tin, however, I decided to design the simplest possible circuit to do that same job, at what turned out to be quite trrivial cost. And I am glad I did because they work reliably, give a more reliable idle (also slower if needed) and because it is a pleasure not to have to connect and disconnect an external glow lead, an inch or two from the prop. And as mentioned here, using battery power only when it is needed makes sense in several ways, includding tthose mentioned here. I don't have the detailed knowledge to design a switched mode system to go with it, though I probably could an inverter using a toroidal ferrite core. If time permitted I would like to try, but as it does not, probably not. I set the desired temperature, using a preset, first just to give a visible glow, and then tweaked so that it will just allow the engine to start - by definition, hot enough to keep the engine running. Rather to my surprise, when then checked out of the engine, it turns out not to be the nice bright - yellow approaching white - we normally expect, but simply a dull organge. The LED indicator which glows when starting then flickers a little at idling rpm but does out altoghether at significantly higher rpm. -
Servoless electric retract installation
Idris Francis replied to leccyflyer's topic in Gadgets and Electronics
Yes, indeed they do. I did not mean to imply that leadscews have no uses, only that (unless using ballraces) the frictional losses make them quite unsuitable for transmitting power when efficiency is important -
On board glow driver
Idris Francis replied to Steve Hargreaves - Moderator's topic in Gadgets and Electronics
Looks neat - but what does it do? I can find no information on the flying widgets site (though not infrequently I find that the minds o web site designers work in a different way from the way mine does. On the face of it the earth tag and the crocodile clip suggest glow plug connections, and perhaps those wires are thick enough for the currents involved, but as there are no thick wires for battery connectiions the implication is that the glow plug current comes via the Rx, the Rx switch and at least 3 plug and socket connections. Surely not? The PCB and component count do not seem large enough to include switch mode operation in effect to convert 0.7 amps at 4.8 volts to 2 amps or so at 1.5 volts, so I am both puzzled and interested. Edited By Idris Francis on 26/09/2012 01:09:26 -
On board glow driver
Idris Francis replied to Steve Hargreaves - Moderator's topic in Gadgets and Electronics
Thanks, Bob. Bog standard off the shelf components - for the life of me I do not know what a PIC is, but that inherently means it does not use them! Essentially surface mount components hand soldered onto a simply PCB about 1.3'' x 0.5", single sided for simplicity 1 off dual comparator 1 off transistor (to drive the LED monitor) 1 off FET About 6 resistors, plus 1 off 0.1 ohms in parallel for current sensing 2 or 3 low value capacitiors 1 off LED 1 off 2k preset for setting plug temperature. It is necessary to connect to the Rx for 4.8 volts supply, and to any control pulse, which triggers operation. On loss of signal, if no pulse is present it switche off. On any 2.4ghz with fail-safe in place, the pulses continue of course (unless there is a spare channel and it can be set, unlike others, not to have fail safe operatiing. If the fail safe pulse eepts it live, then so is the glow plug until the battery goes flat.... In the 1980s and early 1990s I used to manufacture the world,s first inductive joystick which had no moving contacts so never wore out or deteriorated. (RS compoinents Part No 162 984 until only a few years ago) and from 1991 used surface mount PCBs at the rate of 8,000 a month, so I am familiar with production of this sort of thng, just not that way inclined any more! I had thought of a DIY article for RCME - my only other one Super Dual Proportional (which morphed into Flight Link RC) was published Nov.Sec 63 (last of the small format mags) and Jan 64, first of the large ones - almost 50 years ago - not exactly prolific! "an engineer is a man who can do for half a crown what anyone can do for £1" -
Servoless electric retract installation
Idris Francis replied to leccyflyer's topic in Gadgets and Electronics
I must have a look at the Hobby King units, see what problems others have found, and see what the mechanism is. If a leadscrew I would not be at all keen, due to inherent inefficiency, and high drain if they do stall. -
On board glow driver
Idris Francis replied to Steve Hargreaves - Moderator's topic in Gadgets and Electronics
In response to Johny Olsen on switched mode drivers. I have no direct experience of switched mode circuitty, other than pulse width modulated drivers for hydraulics. However at that point in the circut where the switching, from fully on to fully off occurs, ie square edges pulses of current, it is inevitable that the maximum current is many times the average - ie (On current x On time/total time) = average current. If those peaks of current do not come from the battery, which sees only the average current, then those peaks can come only from the capacitors and inductors between the battery and the switching circuit. Not having been involved, as I say, in such things I find it rather surprising that capacitors and inductors of a size and weight suitable for this application could handle the sort of currents - several Amps - we are talking about. Though the higher the frequency of operation the smaller they would need to be. Perhaps its just that I am way out of date - does anyone know the details? If the circtuitry switched on the plug only when its temperature dropped to near critical level, the system would cover many more than 2 flights. re plugs and catalytic effects - no idea - but Mick Wilshere of World Engines told me that he does not like on-board glows, because when they ad extra heat to an already hot plug they oxidise the element through overheating. -
Servoless electric retract installation
Idris Francis replied to leccyflyer's topic in Gadgets and Electronics
In rely to Bucksboy - I am pleased of course that you have had no problems, but many others clearly have had. Just a few points as no need to repeat previous postings: The drive mechanism is a leadscrew not a wiorm drive. The first is in effect a nut driven along a thread, the second is a thread revolving against the edge of a toothed worm wheel. Both very inefficient, but the leadscrew is the worst. Unless of course large enough to allow ball or roller bearings to eliminate the basic problem, high frictional losses at the rubbing surfaces, As others have reported and I found, the sliding fits of the cross-shaff in the machined slots can be too tight in places, due to less than perfect machining. Can be fixed with a file, but it is necessary to disconnect from the drive rod to be able to feel where the tight spots are. Not easy. On mine the sideways clearance for the blocks to pivot were non-existent, causing more friction. The result of the very poor efficiency is little pull in reserve to overcome friction, the need to fit stall-protection that would otherwise not be necessary, and all too easy to trip the stall protection and trigger unwanted cycles. Also, for whatever reason, one a cycles starts - due to a glitch or wyhatever - the design is such that it cannot instantly reverse to correct it, but has to complete the cycle - a second or two. I experienced many unwanted cycles just on the bench when installing. In response to Graham, I have no experience of the Hobby King units, but others commenting on these matters elsewhere have reported problems. I do not need stall protection on my retract servos now bolted direct to each unit, stall current is not that bad. -
Just bought one - wish I hadn't! Buttons to small, zero setting often does not work, but most of all why did they put the PCD display and the biuttons on the SIDE, so that have to kneel down to read or use them instead of on the top where they woud be easy to use? Surely they should know that we work at benches looking down? Edited By David Ashby - RCME on 25/09/2012 08:47:05
-
Servoless electric retract installation
Idris Francis replied to leccyflyer's topic in Gadgets and Electronics
see http://www.modelflying.co.uk/forums/postings.asp?th=48091&p=2 for all sorts of problems with E flite electric retracts - exceessive current due to lead screw drive, hit and miss operation, mechanisms sticking to to inadequate margin of torque and tolerancing problems Also Y leads that come apart under their own weight, Never ever use off Rx battery - asking for trouble -
Futaba 6EXA set up with HAL auto pilot
Idris Francis replied to Jim Burton 1's topic in Gadgets and Electronics
I have been using HAL for 15 years or more, with great succes - BUT ONLY after modifing them by adding filtering to stop the 12mhz microprocessor signals interfering with the 35mhz RC gear! No problem on 2.4 ghz, though, as far as I have seen so far. This test is VITAL! And I mean VITAL!!!! and is mentioned in the instructions but simply not emphasised enough. Carry out a normal range check without the Hal connected at all. Then do the same check with the Hal connected. Any one of the leads to the Rx is enough to put power into it. In my experience, with single conversion Rxs, range will drop by anything from 5% to 70%, and how much can depend critically on which RF channel is in use - I guess depending on how the interference mixes with the various Rx signals. DO NOT FLY if range is substantially reduced - say by more than 10%. If it is more than this, try another channel until you find one that is OK. The only dual conversion Rx I have tried with a Hal - a Futaba - was very badly affected indeed range with Tx aeral collapsed nomally 100 yards, fell to about 6 feet!! No I am not joking, it really was that bad. The problem with the Hal design - as I told the makers 15 years or more ago - is that the 12mz micro section of the PCB is not isolated at all from the rest of the circuitry so those interfering signals get out through all the leads. I found a way to cut the PCB in several places, and reconnect the micro via chokes and with capacitorss to ground. Even then, depending on channel, it could stll be badly affected eg channels 61 and 62 remain unusable, 66 to 70 are fine. Not an easy fix. N -
On board glow driver
Idris Francis replied to Steve Hargreaves - Moderator's topic in Gadgets and Electronics
Having paid 30 or so some years ago for an Intelligent Gow Switch,, which worked fine, I was not prepared to pay so much for so little (in component terms) so designed my own and have now made and used about 10, on a small batch of PCBs, using surface mount components. I spent some time reducing component count to minimum - and no, it does not need a microprocessor. The circuit uses simple analogue circuitry to sense the resistance of the plug and therefore its temperature and a FET driver ensures it does not drop below the desired level. Component cost less than 2. Glow is adusted using a small pot, to a dim glow, or what is just enough for enable the engine to start - by definition, all that is needed. This takes only 1 amp or so. from a separate 2000mAh NiMih so ample for any flying session. Good not to have that trailing battery lead or to have to disconnect the cable from the plug when the engine is running. A LED indicating when the driver is operating shows it is off almost all the time, coming on only when necessary at low idle speeds. It also helps revving up from idle if mixture is a bit on the rich side, by preventing the surge of fuel reducing the glow plug temperate below the critical level. Idles speed can safely lower than without the driver, though the main reason for it is of course to reduce the risk of engine stoppages. It also has the advantage that it never overheats the plug - as for example when leaving the usual external battery connected at high rpm. I had thought in odd moments about marketing it, but don't want the hassle. If anyone is interested, let me know. A few words about the 4.8v unit that started the thread: Nobody would use a 4.8v battery with a dropping resistor or similar to drive a 1.5 volt plug - that would waste 2/3 of the energy. A "chopper" circuit would be better, either on or off, on only enough to heat the plug to the normal extent. Trouble is, when on, current would be at least 5 amps perhaps 8, albeit on only 1/3 or 1/4 of the time. But it would surely be fatal to take pulses of 5 amps from a Rx battery! Another method, better but more complicated, would be an inverter ie convert to AC into a transformer to give 1.5volts - efficiency would be higher and current drain at 4.8 volts would be only 1/3 of what the plug sees - say 0.5 amps, arguably tolerable. Best of all would be a combination of inverter and automatic temperature control like my circuit, ON current of only 0.5 amps and then only at or close to idle - only then in my view sensible to run off the Rx battery. -
Electric Retracts for 120 size bird
Idris Francis replied to Snorbitz's topic in Gadgets and Electronics
Re E flite electric retracts - see **LINK** for a great deal of information on those problems, caused primarilu by the high currents needed becaue of the ineffiticient lead screw arrangement. But lots of other problems too -
This one just to tick the box for notification of any response
-
You will find a great deal of information on problems with E flite electric retracts, from me and others and including link to US sites identifying similar problems, at **LINK** In brief: Lead screw drive is dreadfully inefficient leading to high currents, voltage drops, need for overload tripsn which then trip out and cause the units to cycle. Also machining tolerances have to be very good indeed due to the forces involved and there being little power/torrque to spare - and unfortunately they are not, with various parts tight and prone to stick. It became all too clear to me that mine would never be reliable, enough to fly, but as it would then have been difficult to substitute a different type removed the electric system and fitted a powerful retract servo to each unit - now works perfectly, though not yet quite ready to fly Also - I was puzzled when working on them that every time I turned the wing over the leads came apart - turned out that the fits were so slack thhat they were unsafe.