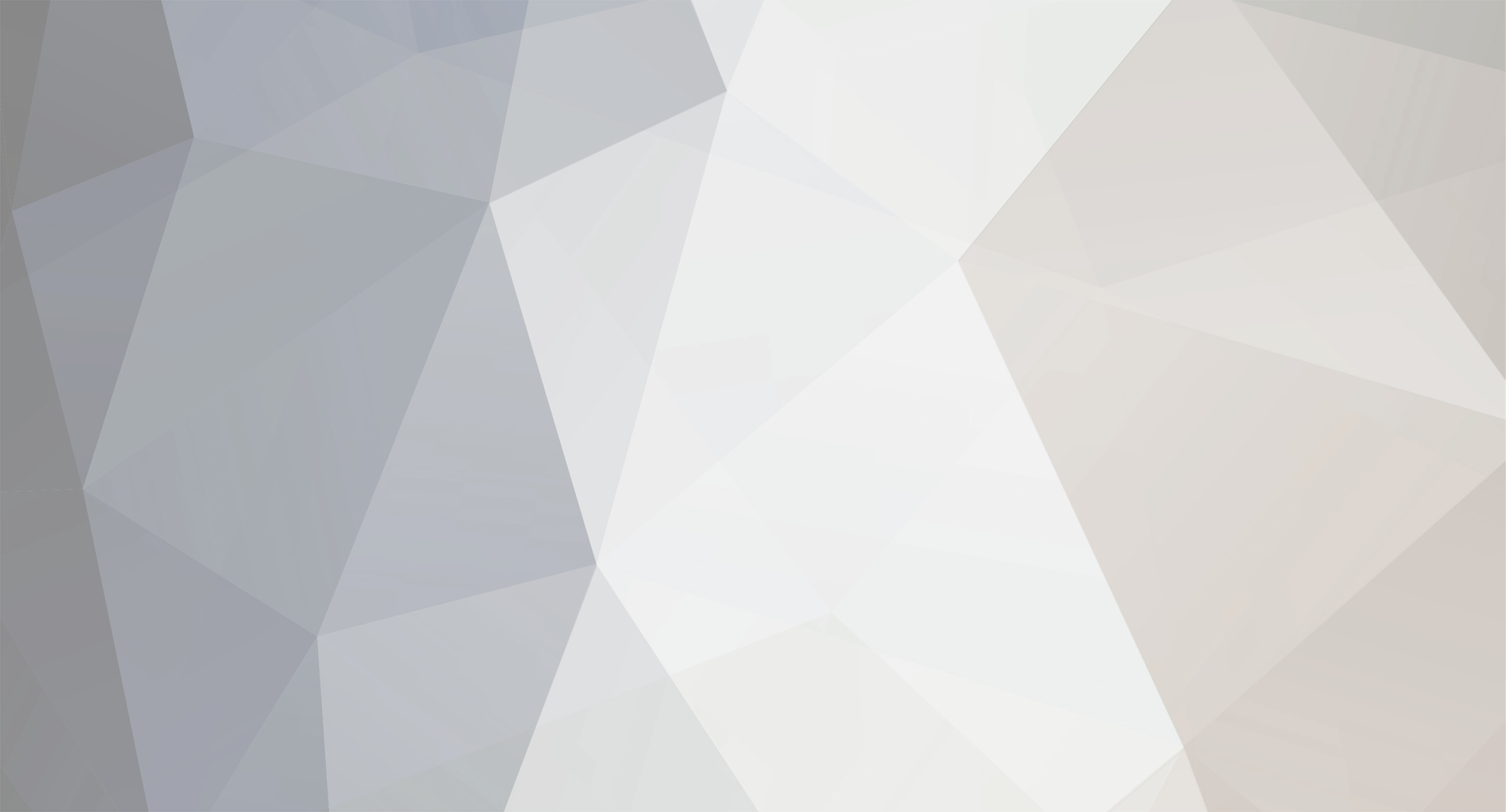
Lucas Hofman
Members-
Posts
1,183 -
Joined
-
Last visited
Content Type
Profiles
Forums
Blogs
Gallery
Calendar
Downloads
Everything posted by Lucas Hofman
-
I know....
- 223 replies
-
- 2
-
-
- peter miler
- rans s-9
-
(and 1 more)
Tagged with:
-
Now! Laminating is fun! At the top of the picture the box with wax that I use to prevent the laminate to glue to the mold or the wedges. Tomorrow the last one!
- 223 replies
-
- peter miler
- rans s-9
-
(and 1 more)
Tagged with:
-
I have never build a model with a tapered wing. With a constant chord wing I have always made 2 ply templates and made all ribs as a block. When doing the same with a tapered wing all edges will not be square and thereby give bad glueing front and back. What is the best way of creating the ribs? Regards, Lucas
- 223 replies
-
- peter miler
- rans s-9
-
(and 1 more)
Tagged with:
-
Let us wait with the praise until it comes off the mold…. (Or not)
- 223 replies
-
- peter miler
- rans s-9
-
(and 1 more)
Tagged with:
-
Have you already flown Geoff? Lucas
-
And the first frame for the canopy is in the "mold". It is a joy to use the little proxxon circle saw to make the strips. I am using it more than I expected. I waxed the "mold", the plate and the wedges. We will see tomorrow if the frame releases clean. Those who look well see 5 laminations. Here in Norway one buys plywood in mm (and this is 1mm). Tomorrow I will start on the fuselage sides. Since this S-9 is 110% I have to glue some strips to a standard 100mm flake to get enough height. Cheers, Lucas
- 223 replies
-
- 1
-
-
- peter miler
- rans s-9
-
(and 1 more)
Tagged with:
-
Some progress today: at last the firewall is ready. I always pull the nuts in using the X-frame from the motor to be used. Then one is sure things will fit. There is no point (I think) in hammering or pulling the T-nuts completely in, it only destroys the fibres in the wood.
- 223 replies
-
- peter miler
- rans s-9
-
(and 1 more)
Tagged with:
-
Good luck Geoff!
- 223 replies
-
- peter miler
- rans s-9
-
(and 1 more)
Tagged with:
-
Somewhat childish maybe, but I do have pleasure in laying out all parts of the "kit" out on the drawing: However in this case it proved very useful: You may remember this is a 110% rans S-9. Apparently I managed to open the 100% size PDF when printing out the template for C1, F7 and F8. A lot better to find out now! Regards, Lucas
- 223 replies
-
- peter miler
- rans s-9
-
(and 1 more)
Tagged with:
-
Ready with the tail surfaces! Well, they are glued together. Still some sanding, camfering and hinging to do.
- 223 replies
-
- 1
-
-
- peter miler
- rans s-9
-
(and 1 more)
Tagged with:
-
Like this:
- 223 replies
-
- peter miler
- rans s-9
-
(and 1 more)
Tagged with:
-
Amused myself this afternoon by checking if MotoCalc (the calculator I used to predict motor and model performance) does agree with actual measurements: It was way off and predicted much higher current than measured. However, when measuring the internal resistance of the (by now quite old) batteries things became clear. The internal resistance was about 3 times as high as the values I had put in MotoCalc. Those came from the website of the supplier. They may have been accurate though, the batteries are 7 years old and have quite a few cycles on them. I will use a Turnigy Aerodrive 4240 740kv with a 5S 4000mAh battery driving an APC12x6E propeller. This gives 750W when fully charged, but dropping to 500W at the end of the flight. Now the battery is know I know if the battery plate needs changing (and thereby the formers it rests on). Cheers, Lucas ps. Running a motor/propeller at full speed in the workshop give a hell of a noise!
- 223 replies
-
- peter miler
- rans s-9
-
(and 1 more)
Tagged with:
-
Basil, I always start by making a scan to PDF of the drawing. Up to now at the local copy shop, but for the Rans Peter was so kind to mail me the PDF files. Having those you can - using Acrobat Reader - force display at 100% and pan to the part of the drawing you need. Then you can print it on your own A4 printer. Doing this for everything that needs cutting out gives you the paper templates to glue on the wood. I am lucky to have access to a large plotter so I also can print a copy of the whole drawing to build the wings on. Hope I managed to make myself clear. Lucas
- 223 replies
-
- peter miler
- rans s-9
-
(and 1 more)
Tagged with:
-
Is «trace» metal wire?. That is what I have used for closed loop rudder control. Do you crimp on both ends or have a little turnbuckle at one end in order to adjust the length? Cheers lucas
- 223 replies
-
- peter miler
- rans s-9
-
(and 1 more)
Tagged with:
-
This weekend. How do you fasten rigging wires? And what are they made off.
- 223 replies
-
- peter miler
- rans s-9
-
(and 1 more)
Tagged with:
-
Some progress tonight: nearly done with the tail: I bought a little Proxxon tablesaw, and that turned out to be very handy
- 223 replies
-
- peter miler
- rans s-9
-
(and 1 more)
Tagged with:
-
Easiest way to cut out all parts is to print them and glue them on the wood needed: I used 3M's remount spray glue. After the part is cut out one can easely remove the paper.
- 223 replies
-
- 1
-
-
- peter miler
- rans s-9
-
(and 1 more)
Tagged with:
-
At last the first bits are in place: I like build up construction. And it is a great way to use the remains of previous builds! Just so that everybody is warned - I build slow. So sometimes it is more pictures than pieces..... Cheers, Lucas
- 223 replies
-
- 1
-
-
- peter miler
- rans s-9
-
(and 1 more)
Tagged with:
-
Out with the building board. I use cling film to prevent the construction from gluing to the board:
- 223 replies
-
- peter miler
- rans s-9
-
(and 1 more)
Tagged with:
-
This drawing has only one half of the stabilisor. Since I would like to have the trailing edge continous I need also a drawing of the right half. My printer driver cannot print mirror images, so I used a trick I have read somewhere: wet the paper so that the lines are visible from the back. But I do not remember what fluid to use. I tried polypropanol., since it would not distort the paper. That works like a charm, but as it evaporates the effects dispappear, so you need to mark enough points you can place all the bits:
- 223 replies
-
- peter miler
- rans s-9
-
(and 1 more)
Tagged with:
-
Purchased the missing balsa sheets. When building Ballerina I used the wrong thicknes for the fuselage sides. To prevent this happening again I have now written which sheet is for what:
- 223 replies
-
- peter miler
- rans s-9
-
(and 1 more)
Tagged with:
-
Rans S-9 Chaos. Peter Miller's new design blog
Lucas Hofman replied to Peter Miller's topic in Peter Miller plan builders
I started a build thread: Most likely there will be a gap in the building from beginning of June until September (sailing season). But it should be possible to get something done before that. -
I will not (yet) be modelling the modifications Berntsen made to LN-SNI, so it will be an S-9 in disguise. The first steps were getting the drawings on paper at 110% size. Since I could not get the large plotter to co-operate I hade to print at A3 and patch the tiles together. The printer is not completely accurate, so not everything lines up perfect. but it will have to do. Next is finding out what is needed, and what of that I have in stock and what has to be bought. I always create a bill of materials for this. It gives me overview since you need to study the plan well to make one. If anybody wants to do this too feel free to copy the attached document. For the last scratch builds (Ballerina and Skywriter) I purchased about 50% extra from the Balsa Cabin, and it turned out nearly all wood needed is already in place. Bill of Materials Rans S-9 110%.docx
- 223 replies
-
- 2
-
-
- peter miler
- rans s-9
-
(and 1 more)
Tagged with:
-
The following has been clipped from the Norwegian Aviation Museums website: The aircraft was assembled by electrical engineer and aircraft enthusiast Reidar Berntsen from Tønsberg. After 1,800 hours’ work the plane was ready in 1994. It was approved for use and registered as LN-SNI. Berntsen flew the plane himself and it was a popular feature at aerobatic displays and air shows in South Norway. Rans S-9B is a modified version of the standard model Rans S-9. The nose has been extended and the rudder moved further back for better stability. In 2012 Berntsen designed new and shorter wings, specially adapted for airborne docking of free-fallers wearing wingsuits. LN-SN1 is the first and probably only aircraft in the world to be approved for this type of use. The parachutist grabs onto a handle on the wing and hangs there. The extra weight of the parachutist is borne by the jumper's wingsuit, while the aircraft just contributes forward speed. Because of the changes to the standard model, the Norwegian Civil Aviation Authority wanted ‘B’ added to the type designation of Berntsen’s aircraft, so that the original Rans S-9 became the S-9B we have on display here. After twenty years and 350 flying hours LN-SNI was retired in 2014. For a couple of years, it was displayed at Torp Airport, Sandefjord until Berntsen donated it to the Norwegian Aviation Museum in 2016.
- 223 replies
-
- peter miler
- rans s-9
-
(and 1 more)
Tagged with:
-
This is the build thread for the Rans S-9 as published in RCM&E, but enlarged to 60 inch span (110%). The plane will be modelled after a full size that has been flying on the same airport where I started flying after moving out of the city.
- 223 replies
-
- peter miler
- rans s-9
-
(and 1 more)
Tagged with: