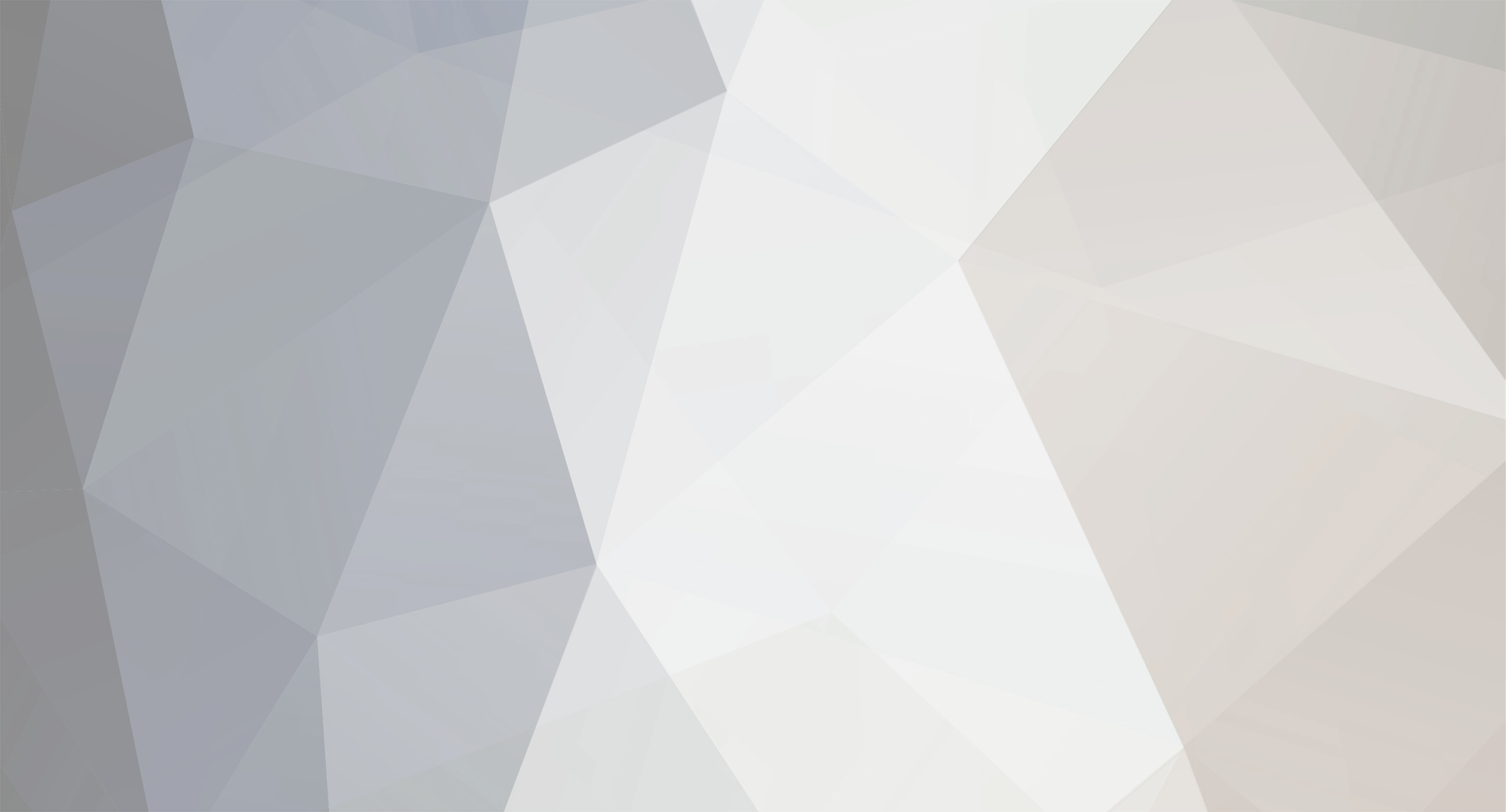
Bryan Anderson 1
Members-
Posts
32 -
Joined
-
Last visited
Never
Bryan Anderson 1's Achievements
0
Reputation
-
Bryan Anderson 1 joined the community
-
Yes, Frank, and, at the moment, some solar/wind power is not being used because the thermal guys cannot turn off the power. The greens are being paid to not produce electricity. I would be interested to find out how much more power could be available for less money than at present. An investment in energy storage would of more economic benefit that building incredibly expensive nuclear stations for 20 years hence at huge costs per kWH and with no sensible plan for decommissioning.
-
The problem of our (everyone's) electricity supply is that demand is not constant. It has peaks and troughs that are not matched to the capabilities of either nuclear or large-scale carbon-fired power stations. We have to waste power during the night. I used to live within a few miles of a coal-fired power station. A common occurrence was a very loud roaring noise as it blew off excess steam because demand had fallen. These old stations get damaged if they are allowed to cool down. So off-peak charging is a boon. Small-scale, local gas turbines would be more reactive and, possibly, get rid of the NIMBY syndrome, especially if their waste heat could also be harnessed. The push to smart meters is not what the government says. The ultimate goal is to allow dynamic pricing to "encourage" you to only use power when it is available. They may even switch your power off (as soon as they can manage it) if they have a problem. This is the future and it might make electricity cheaper or, more likely, enhance company profits. Telsa have already installed Li-Ion batteries in Australia to quickly switch between charging and discharging in order to iron out demand problems. They have proved to exceed the promises made and saved a lot of money. As mentioned above, tens of millions of EVs with the capability to be used as either sources or sinks would also helps. It just needs the will and some infrastructure.
-
Posted by David Mellor on 19/10/2018 09:37:30: Posted by Peter Christy on 19/10/2018 08:57:06: And this whole argument is ignoring the enormous elephant in the room: Where is the electricity to charge all these vehicles going to come from? As of March 2018, there are approximately 38 million vehicles in the UK, of which 31 million are cars. Looking at the cars-only situation, each car consumes on average a little over 40 kilowatts of power (whether diesel, petrol, LPG, electric or hybrid). So the total maximum amount of power required to move our existing UK fleet of 31 million cars is 31 x 10^6 x 40 kilowatts, which equals 1,240 million kilowatts or 1,240 Gigawatts. The figure you want is 40kWH (KiloWatt Hours) not 40 kW. This is the battery capacity that gives over 100 miles on a single charge. The following numbers assume that every car totally discharges and charges that capacity every single day (annual mileage 36500 so extremely pessimistic). The energy (GWH) of 1250 GWH might be replenished off-peak over, say, 12 hours. The power needed is 1240 / 12 = 124GW from our hard pressed power stations. Still a large figure but not as unreachable as your figure implies. Factor in an average mileage per car of 10000 miles and the figure is down to about 34GW. Edited By Bryan Anderson 1 on 19/10/2018 13:01:18
-
Mike, I agree that the ripple current rating of the capacitors is also a concern. There is no doubt that using minimal-length battery leads is desirable but not always possible. The extra inductance of longer leads would exacerbate the capacitor heating problem and this would not be helped by an added zener diode which only helps protect from over voltage. Any added capacitors should have a voltage rating of at least twice the peak battery voltage. Using longer leads and added capacitance is not without another problem. The inductance and the total capacitance form a parallel resonant circuit as far as the FET drivers are concerned. The extra capacitance and inductance lowers the resonant frequency of this circuit and there is the added danger that it will get closer to the rate at which the FETS are pumping currents into it. Driving such a circuit at resonant frequency increases the currents and voltages by the Q factor and the heating effects by Q squared. Not good. A belt and braces approach would be to decrease also the lead inductance by using more copper. Rather than just fatten the conductors which is not very efficient, it would be better to use another "twisted pair" in parallel to halve the inductance. In fact, more pairs would achieve even more reduction. Not very elegant and not a nice solution though it would help to reduce resistance losses in the leads.
-
Posted by Geoff Sleath on 13/04/2018 14:48:14: I guess thicker wire has a lower inductance which reduces the resonant frequency but increases the Q. Geoff To a small extent. The impedance and hence inductance of a length of transmission line goes as the log( 2 * s / d ) where log is the natural log, s is the conductor spacing and d is the conductor diameter. You need roughly 4 times the weight of copper to halve the inductance. And, as I am sure you know, the smaller the inductance, the higher the resonant frequency and the Q if other things stay equal.
-
Posted by Geoff Sleath on 13/04/2018 13:28:55: That's very interesting, Bryan. Thanks for that. One term I don't understand is the S factor of the esc. Is that the number of cells? ie the maximum input voltage? So the zener should be chosen to be the rated maximum voltage plus one extra cell - ie (say) 4v for LiPo? The input capacitors on the esc I have on my desk (Black Mantis 60 amp) are 2x220mfd in parallel (so 440 mfd) 35v working. You estimate a 4S LiPo as having an ESR of less than 20 milliohms. In the measurements I've made 5 milliohms per battery is quite low and they can go up as high as 10 milliohms/cell before they're virtually useless as sourcing a decent current. So I think your estimate is perhaps a little on the low side. Geoff Yes Geoff, I meant the S rating of the ESC. I do not know how different manufacturers decide on these ratings. I hope that 4.2 times the S factor is less than the voltage ratings of the capacitors and FETs. A few volts more for the zener above that S equivalent is all that it should take. What is the S rating of that ESC? How does it compare to 35V (read off a capacitor?). If that is a 4-S rated ESC then it corresponds to twice the battery voltage. QED. The ESR of a Lipo battery is very temperature dependent. It is high at low temperatures and low at high temperatures. My 2200 mAh 3S cells measure about 5 mOhms per cell at 25 C. My numbers are meant to be illustrative. YMMV. In any case, a good engineer should always consider the worst case. Edited By Bryan Anderson 1 on 13/04/2018 14:26:23 Edited By Bryan Anderson 1 on 13/04/2018 14:47:43
-
Summary The thing to worry about with long battery leads is the turn-on transient. The turn-off transient can pit, even weld, the contacts of the circuit breaker but will not over stress the capacitors in the ESC. The turn-on transient can double the battery voltage at the ESC for which the capacitors, possibly even the FETs, are probably not rated. Rather than use an extra capacitor when using long leads, it would be better to protect the ESC by using a power zener diode to clamp the excess voltage. A zener capable of dissipating a few watts (e.g. 3W) in the steady state should easily absorb the transient power without the need for a heat sink. Choose a zener voltage to match the S-rating of the ESC plus 1S if you trust the supplier. Better yet, see what the voltage ratings of the capacitors are and use a matching zener diode. Reasons The battery leads are a pair of parallel conductors that should be kept close together to minimise magnetic coupling to nearby components. They act like a transmission line and have an equivalent inductance of about 10nH per centimetre. So, battery leads about a metre long have an inductance of about 1 microhenry. I guess the total capacitance in a typical ESC is about 100 microfarad. Together, the inductance and capacitance form a series resonant circuit that resonates at about 16 kHz. The Q factor of this resonant circuit is only about 5 if the net series resistance is about 20 milliohms (4S battery plus ESR of the capacitor(s) in the ESC). Neglect the parallel loading of the ESC: it barely matters if the motor is off. Arcing at the contacts would increase the series resistance and decrease the Q factor. When the battery is first connected, the currents in the leads increase and the voltage on the capacitance also increases. If the total series resistance were zero, the voltage across the capacitance would rise and overshoot, oscillating about the battery voltage with a peak amplitude of the battery voltage. Hence the factor of two, the battery voltage plus the oscillation amplitude, mentioned in the opening paragraph. With a finite and low Q factor, the oscillations would quickly die away leaving the capacitance charged to the battery voltage. But surely this applies to any length of lead? Yes but the Q factor of the connection is lower for shorter leads and this will decrease the amount of overshoot. The reason why the turn-off transient is less stressful is because a) the current from the battery is usually minimal when disconnecting b) the energy stored in the capacitance would typically be an order of magnitude greater than that in the inductance so the ability of the latter to cause overshoot is minimal.
-
Posted by Martyn K on 03/04/2018 07:57:33: Hi I am setting up one of my e-gliders for contest use. I have two timers running, one counting up and the other counting down. Both are triggered to start on activating the throttle. An Aerobic Altis 4 stops the motor after 30 seconds or 175m. At that point I set the throttle back to zero and set the override to prevent an inadvertent restart. The timers should keep on running I want to be able to manually stop them (simultaneously) by triggering a switch and I cant work out how to do that. I don't want to use the throttle lever. Any suggestions? My only thought would be to use a switch instead of a throttle lever for the throttle (i.e. on or off) and then I can use the throttle lever for Spoiler control but that is not the way I am used to flying. Thanks Martyn Assuming you are using OpenTX, you could control your timer(s) using a Sticky logical switch. For V1, use your throttle enable switch and for V2 use whatever switch you want. V1 going True sets the LS True and V2 going True sets the LS to False. Have you seen the guide to LS that I posted some weeks back?
-
Posted by MattyB on 04/03/2018 10:43:44: Looks good, but you will probably get a lot more readers if you publish the HTML version as a website - Google will then feature it more prominently in related search results. Thanks. The problem is finding somewhere to host it. RCGROUPS does not accept HTML as far as I can tell. Neither does modelflying again as far as I can tell. Suggestions would be welcome. I have converted into one long HTML file - it is about 70KB. If anyone wants it, please PM me with their email address. The PDF is fine except that PDF page breaks from HTML leave something to be desired.
-
It seems that there are quite a few users of OpenTX who are scared of what seems to be the complexity. One of the most powerful features of OpenTX is logical switches. I have written a guide to try to help these people. It is intended to be comprehensive and accessible, useful for novices and experienced users in need of a refresh. It is not a cookbook. It is not intended to get absolute beginners up and running. It is assumed that the reader can navigate through the menu systems of the transmitter and has learned the significance of short and long button presses. The original is in HTML but it has been converted to PDF. You can find it at **LINK**
-
FrSky X10 - Taranis replacement?
Bryan Anderson 1 replied to Chris Bott - Moderator's topic in FrSky
Posted by John Privett on 26/02/2018 22:37:04: Thanks for the input, folks! OpenTx sounded the sensible option - comments above have confirmed that. My Taranis screen hasn't actually broken, it's just suddenly working in very low contrast which makes it awkward to use. So it might be the screen itself, though I suspect it's more likely something on the mainboard, or perhaps the connecting cable, though I have unplugged and reconnected that. It just may be feeling cold. Some LCD screens go dark when cold. -
Posted by Mike Freeman on 17/01/2018 06:37:33: Posted by Tom Sharp 2 on 17/01/2018 00:36:54: How about terminals But the terminals are always labelled + & -, the cathode and anode..... I mean electrodes attached will have either a +ve or -ve charge depending on whether the cell is being charged or discharged. An anode is always positive, a cathode negative regardless of whether it is being charged or discharged. Check with a voltmeter. On charge, the current flow is reversed because the electromotive force ( open circuit voltage) of the charger is greater than that of the battery. On discharge, the emf of the battery drives the current through the load. The currents are reversible but the voltage is not. Using incorrect terminology is potentially dangerous if it misleads people as to polarity.
-
Suitable glue for Phoenix plastic fus
Bryan Anderson 1 replied to David Hall 9's topic in Foam models
See a post from McG in Belgium who answered this some while back. Take a look at **LINK** -
OpenTx - Questions and Problems
Bryan Anderson 1 replied to Biggles' Elder Brother - Moderator's topic in FrSky
Posted by Trevor Crook on 28/07/2017 19:29:59: Bryan, you are a star! Worked a treat, although very non-intuitive. I'll now have a go at setting up channel 6 as a 3-position flap switch. In a MIXER line, using a switch as a source and also as a switch in that mix does not work as you have found. To make it more intuitive, consider the lights in a stairway that can be operated by a switch downstairs and one upstairs. What would happen if both switches were thrown at the same time? Answer: no change. That is exactly what that MIXER line was doing. -
OpenTx - Questions and Problems
Bryan Anderson 1 replied to Biggles' Elder Brother - Moderator's topic in FrSky
Posted by Trevor Crook on 28/07/2017 16:48:44: Bryan I've deleted the mix I originally had for channel 5 on my QX7 to attempt to get the string you gave in your post. My Mixer screen seems to have a different format, see screenshot below. The OpenTx version is 2.2.0 Trevor, As I suspected. I showed what you would see using Companion. Yours is what is shown on the transmitter. Your line shows I05 (that is Input 5) as the source and SF as the switch. You do not need to feed switches through the INPUTS page. Just use them directly as SOURCES. You should delete the I05 line in INPUTS. You should edit that MIXES line to change the source to be SF and to leave the switch source as blank ( "---" ). It should then work. Alternatively, through the wonders of OpenTX, you could leave the INPUTS as they are and just edit the SWITCH part as above. But why have lines on two pages when only one line on one page is needed. There has to be a MIXES line in order to send something to the receiver. Edited By Bryan Anderson 1 on 28/07/2017 17:11:36 Edited By Bryan Anderson 1 on 28/07/2017 17:12:25 Edited By Bryan Anderson 1 on 28/07/2017 17:12:58