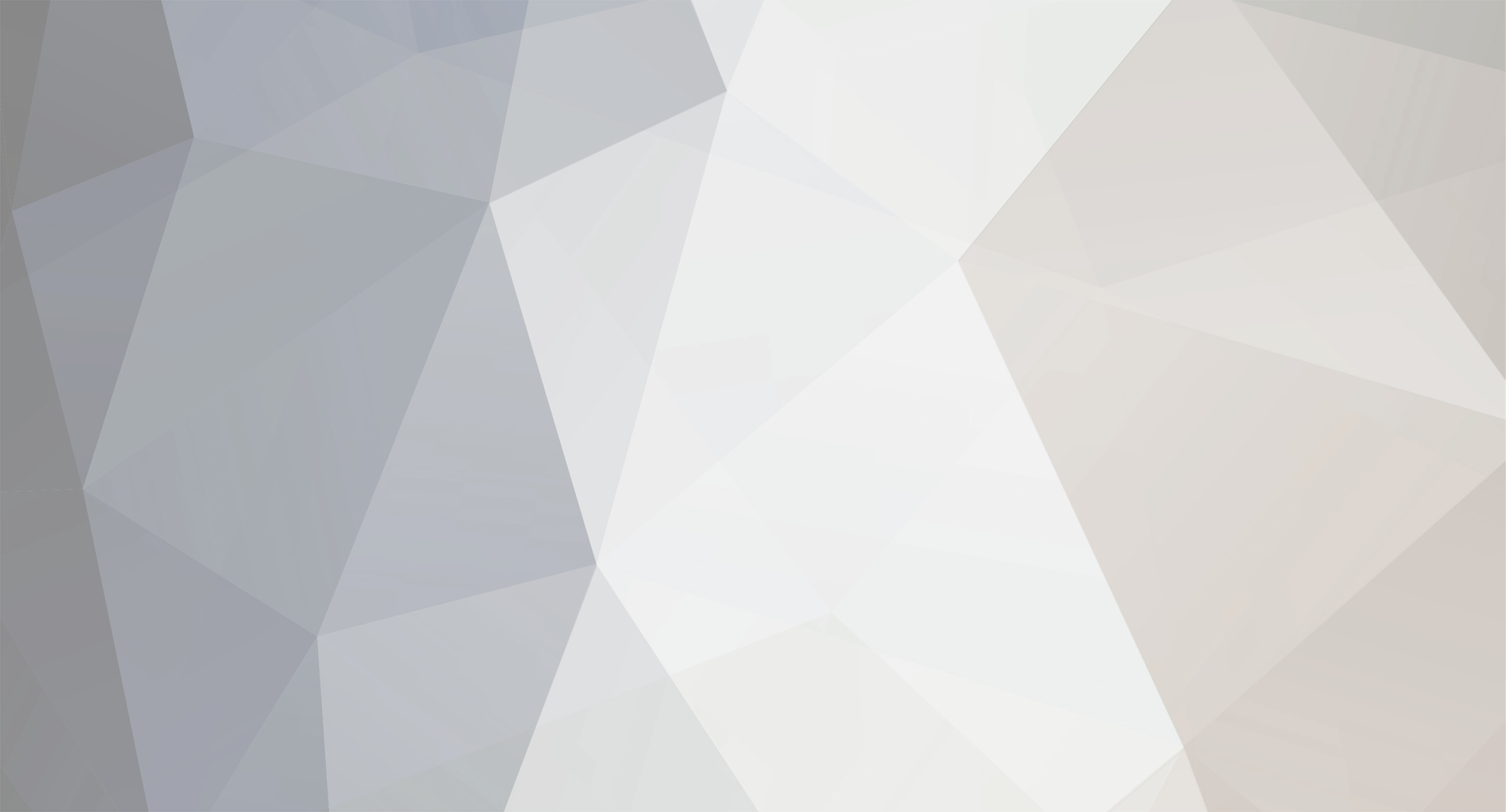
Brian Parker
Members-
Posts
536 -
Joined
-
Last visited
Never
Content Type
Profiles
Forums
Blogs
Gallery
Calendar
Downloads
Everything posted by Brian Parker
-
. The powered Fox, single top mounted aileron servo, side mounted elevator servo and lipo positioned for correct CoG. Plenty of room inside. Note the magnet for canopy. Glider has twin aileron servos. Note the cracking of wing at stress point by the inner termination of aileron, appeared after several hours use over more than 12 months. Note, I have used piano wire,(didn't have any carbon at the time, now think that the wire is better), reinforcing for the wings, ailerons and tail on all models. They will try to fold if not strengthened. Having said that, they will take some punishment. Even more room inside. Battery sits inside.
-
Looking good so far. Do you have a publication date?
-
Yes Mathew, The weasel it is, rather to many models stacked along that wall. Pound for pound, the weasel is the best fun you can buy.
-
I have three chuckies, one Fox on sub micro servos, one Fox on sub micro servos with a folding three blade three inch prop, Tornado inrunner, 10Amp ESC and 450mAh 2S Lipo. One Graupner Discus on sub micro servos. Actually the Discus is the better performer of the two gliders. It was originally set up with wingerons, but was a pain to keep the wings attached on landing. There was a recent thread on small models and power consumption so I have connected a meter to the 3 servo Fox and given the sticks an enthusiastic stir that would equate to several minutes in the air. Standby current 0.01A. One servo up to 0.07A, two servos up to 0.14A, three servos up to 0.2A. Current draw 0.02A to 0.15A simulated normal flight. Volts remained well above 5volts(210mAh. Battery). On the Graupner Discus Chucky each servo took just under 0.18A. All on 35Mhz Corona synthesized receivers. I tend to use the 210mAh battery in a bit of a blow and 120mAh in light winds. All need a healthy launch. Canopy held by magnet and peg. Ailerons etc. cut right through, (not as some advise, partial cut through using top surface as hinge) and hinged with Scotch tape this give less resistance. A few spare batteries in the pocket come in handy.
-
Bill, If you search you should find previous threads on this Forum on reflected/masked 2.4Ghz signals and the need for correct orientation/polarisation of antenna. Our signals are low power so signal reflection with correctly setup antenna (both Tx and Rx) should not be a problem. Contrary to popular belief a stronger signal could cause more problems when flying in a restricted location.
-
Black Magic and twin diesel build
Brian Parker replied to John Payne's topic in Build Blogs and Kit Reviews
Frank, welcome. I, and I'm sure others, would be interested in details of the method used for the crankshaft manufacture. Also some information on the equipment at your disposal would be interesting and would, I suspect, make us all jealous. Thanks for sharing the build with us. -
By chance happened to read those posts before they were deleted. Not the kind of thing I expected to read on this forum. Hope she is soon back.
-
Anyone recognize this delta wing?
Brian Parker replied to John Horsfield's topic in All Things Model Flying
That’s the general method I use for CoG calculations and it serves me well. -
It is surprising how long they do last even in cold temperatures. The Fox is only a chucky and input is minimal.
-
Phil, Timbo, My little Multiplex fox flies happily on 120mAh with 2 sub micro servos and a Corona RP4S1 receiver. Current draw is low even when wiggling the sticks (did measure it at the time, but forgot the actual figure). I just carry a couple of spare packs in my pocket, made up from cells from the Component Shop (see Andy's link above).
-
Elapor, Cyano and a good day ruined
Brian Parker replied to Brian Parker's topic in Gliders and Gliding - General Discussion
On reflection and with due respect to all, I don't think it was flutter. The dive was as straight as an arrow with no oscillations of fuselage. There was absolutely no slop in any linkage. The break was at the exact instant of my input and she failed to pull out. To me this is catastrophic structural failure. The break was clean with no sign of repeated compression, tension or torsion. I am still of the opinion that the lack of flexibility due to the cyano was a contributory factor. If you look at the photo, the crack starts at the rear of the tail where it meets, and is glued to, the rear of the fin (localised stress point) it moves forward and outwards equally on both sides of the tail to meet the leading edge. Bearing in mind the resultant forces, I would have expected the crack to be more parallel to the fuselage. Anyway, as I posted earlier, although not as pristine, she still performs well with her new carbon splints and she cannot expect to be confined to easy glides in the future. -
Stephen, Has that guy just been scalped by the prop?
-
Elapor, Cyano and a good day ruined
Brian Parker replied to Brian Parker's topic in Gliders and Gliding - General Discussion
Peewhit, I forgot the anemometer but the wind speed was probably in excess of 12 mph gusting to 18mph perhaps higher. Tried it out today, wind speed 10mph (measured) with the odd higher gust, plenty of lift (more than Tuesday). Gave it a good wringing out and she certainly seemed more responsive. Perhaps with the carbon reinforcing in the tail she was more able to hold she own. Also had my Weasel out on both occasions, highly recommended and excellent value for money. I have it fully taped and she is a little overweight (she initially ended up tail heavy) but is superb. I intend to send for another and keep uncovered for lighter/lazy days. My fusion also carries a lump of lead in her belly and she is all the better for it. Eric, Thanks for input. I only had the tail fail in mine; control is via snakes and MG servos. Andy had the ailerons freeze. -
Elapor, Cyano and a good day ruined
Brian Parker replied to Brian Parker's topic in Gliders and Gliding - General Discussion
Chris, Definitely no prior damage either due to storage or transportation. -
Elapor, Cyano and a good day ruined
Brian Parker replied to Brian Parker's topic in Gliders and Gliding - General Discussion
Peewhit, Have a Fusion. The dives were quite a long and steep (almost vertical) . I have reinforced the tailplane and elevator with carbon strip and used carbon pegs on the join. I had expected a light breeze, but it was fun while it lasted. Andy, Perhaps I need to act my age -
That about sums it up. A bit worrying isnt it. There is in fact an excellent thread on this forum by Simon Chaddock on a positive lubricated four stroke build by his father, the late Prof. Chaddock.
-
Elapor, Cyano and a good day ruined
Brian Parker replied to Brian Parker's topic in Gliders and Gliding - General Discussion
Because the cyano, being rigid, is not allowing the Elapor to flex at a localised stress point. It may well be that the model was driven too hard and the cyano was not to blame. Object of posting was to invite comment or to see if anyone else had suffered the same. -
Yesterday I felt the need for some relaxed soaring, so took the EasyGlider out for an airing. Conditions, despite the forecast, were perfect with plenty of lift almost to the edge of eyesight (my). After some enjoyable soaring and several manoeuvres later the limits of the EasyGlider were revealed. Or was it the limitations of Cyano? She failed to pull up out of a steep dive, the left tailplane detached, hung on to the elevator for a moment, freed itself and fluttered down on its own. The EasyGlider was previously in perfect condition with no added ballast. Later inspection at home revealed that the right-hand side of the tailplane was almost detached, cracked exactly at the same point as the left hand side. (Hard to see in photo). Obviously a localised stress point. The impact was heavy at about 20 degrees from the vertical but was into longish grass/moss and peaty soil, although, all equipment, including the servos (spot cyanoed in) were ejected. She looks surprisingly clean but is a bit green under her nose. It is now repaired and looks like new (well almost). Was this a direct result of the lack of elasticity of the cyano glued joint? Would she still be in pristine condition if flexible glue had been used? Or was she pushed to hard? ps. Sorry about the oily building board, 'tis the engineering board, not the construction board.
-
Grant, Just found your Airbus A380 build thread.
-
Grant, Out of interest and I suspect of interest to others. What is the setup, are you operating near the limits of the ESC? What was the original length of the cables and have you increased the gauge of the cables to the same degree? Sparking on connecting is caused by the current rush/serge. Spikes are caused by the switching within the ESC and are smoothed by the input capacitors. Increasing cable length can often impose additional loading on these capacitors.
-
Mystery BAE Slope Soarer
Brian Parker replied to Brian Parker's topic in Gliders and Gliding - General Discussion
Thanks, Fitting the charging jack etc. will be straight forward. Hope I keep mine in one piece. Just waiting on the wind direction. -
Mystery BAE Slope Soarer
Brian Parker replied to Brian Parker's topic in Gliders and Gliding - General Discussion
That sounds a good idea and saves removing the canopy for charging. -
This has all been covered many times before (and above) and perhaps we need to keep a sense of proportion here. Brownout is voltage induced not RF induced. On Spektrum systems the receiver drop out voltage is 3.5volts. It does happen. It is not common and is unlikely on a correctly installed system. It does matter when it happens. If the receiver is not ‘quick connect’ enabled it can take several seconds for the receiver to re-establish contact, important is the ground is less seconds away. If the voltage is habitually dropping to those sorts of levels then doom awaits whatever the system 2.4GHz or 35MHz. Digital servos will not be very happy either.
-
Also, Coiling will not turn an omni-directional antenna into a directional antenna. It will only detune/retune.
-
Mystery BAE Slope Soarer
Brian Parker replied to Brian Parker's topic in Gliders and Gliding - General Discussion
Eric, Thanks for the reply, will leave as is.