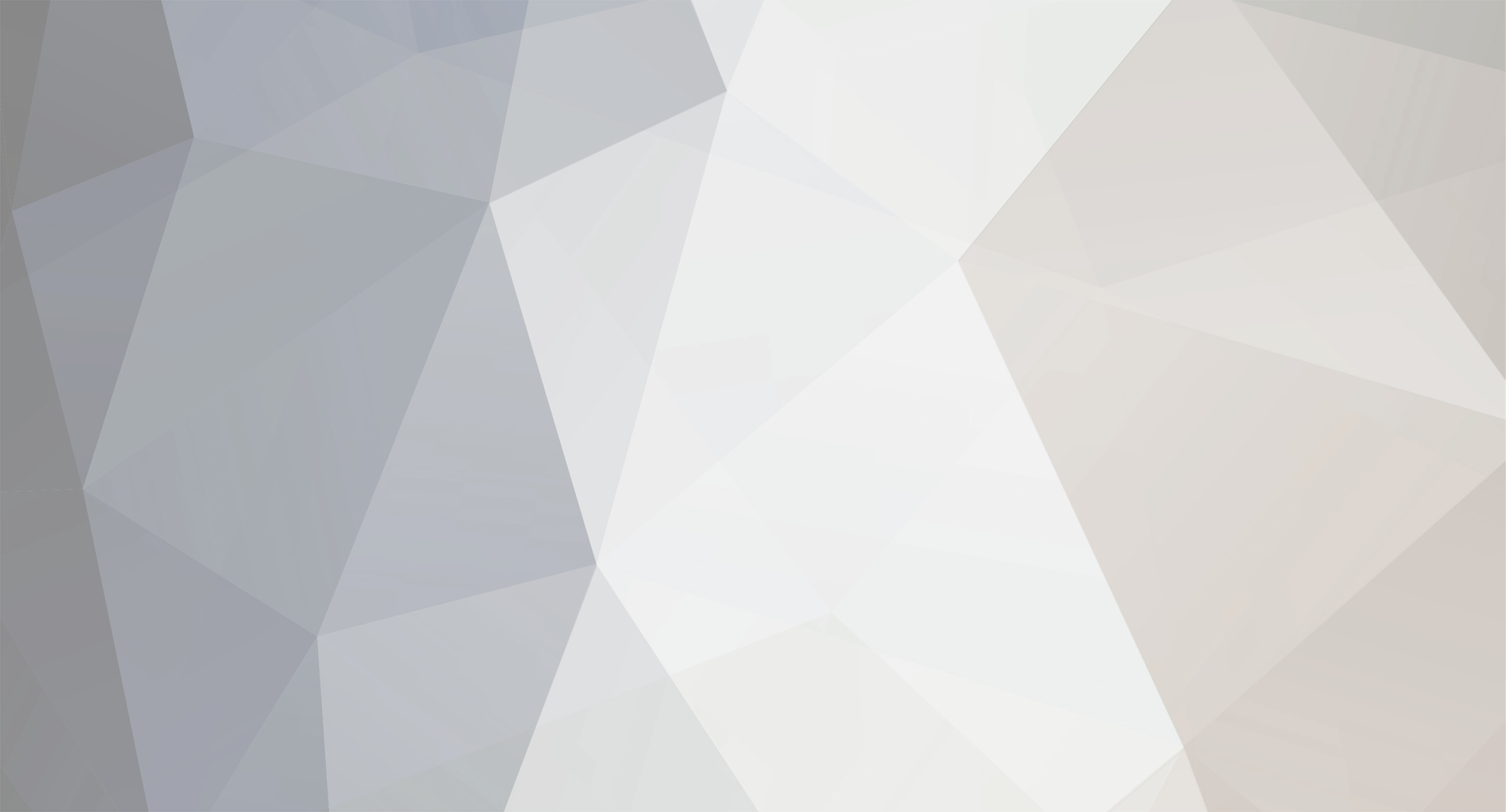
Simon Bulk
Members-
Posts
12 -
Joined
-
Last visited
Content Type
Profiles
Forums
Blogs
Gallery
Calendar
Downloads
Everything posted by Simon Bulk
-
Laser engines exhaust pressure nipple retrofit (for pressurized tank)
Simon Bulk replied to Simon Bulk's topic in IC Engines
Very good hints, thank you very much. I wonder how Jon figures out that I am on the extreme low end of the slow run needle…That might indeed be the case. Is the backfire an indication? Launching the model inverted is definitely possible, I’ll try that after experimenting again with the slow run needle. A fixed landing gear is not really in scope, but the dolly thing is something I’ll might give a try. Another interesting fact I must add: the problem has gotten worse over time. This year the problem has become way worse than it has been the year before… The only thing I’ve changed this year is the airscrew, now I got a slightly heavier load (13x8 G-Sonic, still revs very good at over 9,000 rpm). I guess that contributes negatively to the “sensitiveness”. Edit: vent tube is facing into the airflow. -
Laser engines exhaust pressure nipple retrofit (for pressurized tank)
Simon Bulk replied to Simon Bulk's topic in IC Engines
Interesting thoughts, gentlemen. But with space left to extend in the tank and with the vent completely open, why should the fuel press against the fuel line? My observation when dead-sticking at launch is very close to an engine dying due to a lean cut… But of course I might be wrong with my assumption. -
Laser engines exhaust pressure nipple retrofit (for pressurized tank)
Simon Bulk replied to Simon Bulk's topic in IC Engines
I tried with all lower settings and, indeed, got better results with the throttle 60% open. But still, lots of fails… -
Hi Laser enthusiasts. Unfortunately the "Laser - Technical questions"- thread was closed until further notice, so I try my luck with opening a new one. Here's my problem: I got a Laser 70 engine (made at the beginning of the 2000s, 2 head screws, black carb, old main needle without spring), which runs truely perfect. The engine is mounted on a 140cm selfmade spitfire and fits beatifully to that model. The airframe is very light and not equipped with any landing gear, so it must be hand-launched, which generally is absolutely no problem at all with the loads of power the laser provides. Now comes the problem: In that moment the model is launched, the fuel flow seems to be cut due to the launch impulse, no matter how soft it is launched. This causes the engine to stop abruptly. Unfortunately the success-rate is very poor: I would say more than 50% of the launches end with a deadstick landing directly after launch. Tank has already been lowered, so perfectly in line with the carb as Jon has always described. All of my smaller, also handlaunched models, with OS engines (.15 - class, all with a pressurized tank) have no problem at all. So, as first time in my life I am considering to retrofit a pressure nipple on the Laser 70 silencer. The silencer seems to be made of aluminium cast. Unfortunately I cannot reach the interior of the silencer to tighten the nipple by a counter nut. I've seen some laser engines with that mod. Is there any experience, whether a cut thread in the aluminium is a suitable solution? I hope this message finds Jon and he can maybe help me out what nipple type was used at laser and how they have been fixed. Thanks in advance and best regards Simon
-
If memory serves, the theory was as following: The spray bar is only able to create bigger drops, which are not very ignitable. Engines need to run finest vapor, highly ignitable because it’s well mixed with air. The inner surface of the intake manifold during running is colder than the surrounding and lets the big drops (coming from the spray bar) condensate there into finer ones. The rushing airflow through the intake takes these finer drops and converts them into a fine vapor which is needed for the combustion. Therefore you need a minimum length of the intake manifold to make that magic happen. If this minimum length is not given you just flood the engine with the big drops coming from the spray bar. That’s what the whole story is about. I don’t really believe that. Why? Because during starting process we all choke the engine and (until a certain point) we flood it and it starts… Let me check if I find the book. Then you’ll get the official version.
-
I widely agree with all mentioned above. Especially with the tendency to overthink things instead of enjoying them. Perfectionism sometimes is not very beneficial in that matter. I still believe that our glow engines are still in parts an undiscovered world because the market is just not big enough… I mean we do not speak about commercial engines that are sold millions of times worldwide, big companies spending billions of $ in R&D to entirely understand and perfection their design. I still believe RC IC engine market is mainly based on professional try and error by chaps pursuing their vocation. Nevertheless the outcome are really good running engines and that is the most important part of it. Back to the topic: I still don’t get the following point: If nitro helps to cool the combustion process, why does the use of highly nitrated fuels several times come along with shimming the engine? That’s a bit agains the theory I understood. Another interesting thing I thought about is the following: A very popular German Professor back in the 80s published several books about model engines. He described that our 4C engines need a certain intake manifold length to condensate the fuel vapor correctly on the cold intake side. Too short manifolds will not work, he stated out. Even though Laser carbs manifolds have a certain length (the part that get stuck in the head) they seem quite short … but nevertheless it works perfectly despite of being “sooo short”.
-
Interesting, thanks Jon. So, seems there is reason in special combustion design (such as hemi heads)… I pretty more get the impression that all 4C engines -despite of their specific design features- work equal and react very similar to certain changes in fuel composition etc. That means: Running a Saito on high nitro % serves as inner coolant, allows a slightly richer needle setting at peak power without loosing too much rpm (due to the additional oxygen by the nitro component). That works especially well on high compression ratio as the Saito’s have. Same applies to Laser, but they’re less critical due to the lower compression ratio. Detonation (knocking) is mainly caused by overheating and not by too much nitro in the fuel. Nitro allows cooler running and even prevents knocking. Shimming lowers compression ratio and allows furthermore higher nitro % resulting them to run cooler. anything wrong here in that theory? best Simon
-
Hi Jon. Thanks for clarification. another question regarding the Glow World. Maybe that has already been discussed before, but I didn’t find clear references… What is the design secret behind Lasers zero-Nitro philosophy? Is it the combustion chamber design (cylindrical) with a moderate compression ratio? OS has a similar design (parallel valves) and they run also well on moderate use of nitro (5%). Saito’s design with the hemispherical head integrated in the whole cylinder as one piece with a high compression ratio seems to make a difference here. They run well on >10% or more nitro. Even Saito itself recommends that, maybe for power improvements. Nitro serves as detonator and should not be used vastly in engines with a high compression rate. But that’s the point where my theory does not work in Saito’s world. Can someone help here? Especially regarding laser? Best Simon
-
Hi Laser-Guys. One question does not let me sleep and I did not find anything about that on the internet. Can the (not longer available) Laser Diesel Engines be run on Synth Oil? Or is Castor still the ultimate choice due to the higher combustion temperature or for whatever reason? thanks for an Info and best regards Simon
-
Ok Jon, thanks for the prompt reply. One additional question to the prior topic of engine gaskets / sealings: As far as I know you use loctite / silicone for all engines (at least mine are all sealed with liquid silicone). Is there any particular reason to do so? I would have expected cutted paper, silicone, OILIT, teflon or whatever fuel and heat resistant gaskets. Best regards Simon
-
Hi Jon. The FT310 is really a beauty of an engine! Here are 2 short questions: 1. If I see right, in contrast to the instructions of all other Vee engines you use a a Y-Adapter for the fuel supply. So: One Tank, one fuel line, one tank clunck. Right? Why was that changed? Is there anything different in the Twin design that you can easily get rid off the prior solution with 2 fuel lines or 2 tanks? 2. Maybe this one has already been discussed in another thread, but: Even though more complex, have you ever considered to built a real boxer FT? So, 2 individual, opposed crank throws? Best Simon
-
Hi Jon, I am the proud owner of a Laser 200V, mounted in a Seagull YAK 11. The engine runs perfectly and swings a Graupner G-Sonic 18x10 at around 7800-8000 rpm if memory serves. Plenty of power and torque at 6,5kg TOW! The Graupner G-Sonic airscrews are a bit on the low load's end in regards of their stated size, so for example in a direct comparison a 18x10 APC is definetely a heavier load. Nonetheless it harmonizes very well. See here. Before that I had a OS GT33 mounted in that airframe and I had my doubts whether the 4-stroke Laser 200Vee can keep up with the OS at same displacement. And, suprisingly, yes! It did very well. The OS GT33 swings the same prop maybe 300-400rpm higher, but that does not really matter because it's definetely a question of sound and emotions... Nevertheless, I got an unemployed Laser 240V is my hangar and it matches with the engine mounts of the 200V. The extra weight would not be any issue. Is there any significant gain I can expect by replacing the 200V by the 240V? I mean the YAK 11 is a racer and it my expectation is that it might harmonize even better with the 240V? Best regards & thanks in advance. Simon