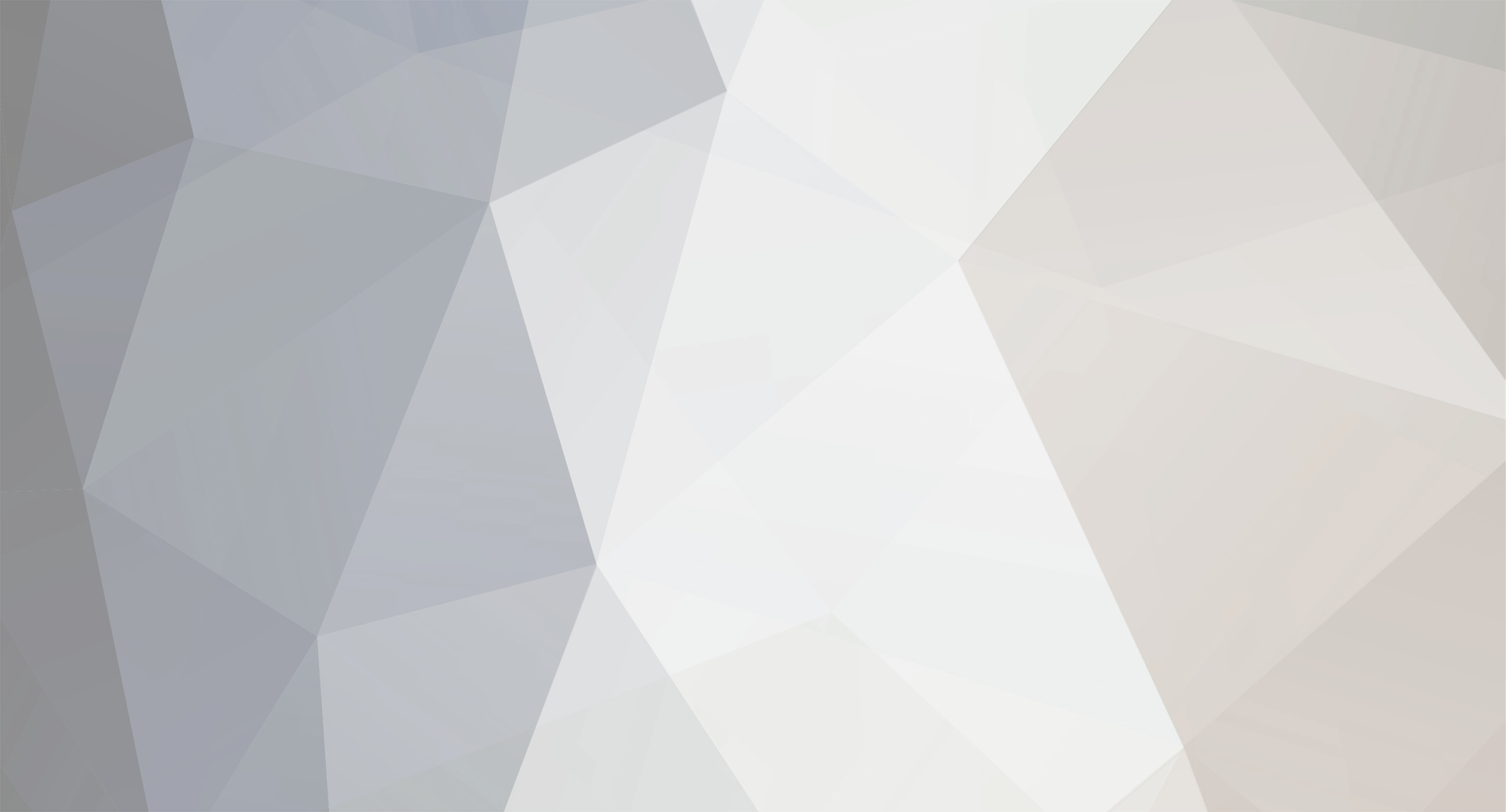
Andy Blackburn
Members-
Posts
1,002 -
Joined
-
Last visited
Content Type
Profiles
Forums
Blogs
Gallery
Calendar
Downloads
Everything posted by Andy Blackburn
-
Pete, that looks really good. > What is the wind range Andy? I've not found the wind speed limits yet, because every time I've chucked it off a slope it's flown OK. All slopes are different of course and will provide different amounts of lift with the same windspeed, so it's difficult to give any hard limits. However, it will fly higher in the same lift than my light-ish 2nd Jet Provost (silver and dayglo) and Hawk T1a (the grey one, SD6060 wing) so if a JP or Hawk will gain height, then the Cranberry should do too. I've chucked the first prototype JP (slightly lighter) off the Orme in a lot less than 10 mph and that took a bit of concentration, but it did gain height. Having said all that, though, you really need a decent amount of lift for a maiden in case you need to sort things out so I'd just go with what you're happy with.
-
I've used JR and then Spektrum, but I suspect that you use Futaba(?) so this might not make all that much sense, but on my Tx you can either do it using end point adjustment, or on the Tx screen where the dual rates are set-up - you can set-up different amounts of movement for up and down elevator by holding up or down stick whilst adjusting the movement. I'm afraid I did it on end-point adjustment - something like 100% down and 80% up ...
-
On the prototype I had the model set-up with two elevator servos exactly as Phil describes above; the only time you need to use a Y-lead is if you haven't got enough channels. BTW, I also used one channel per aileron so that it was easier to adjust them, so there were a total of 5 channels used: Left Aileron Right Aileron Left Elevator Right Elevator Rudder + a small amount of aileron-rudder mix as described in the original article, and I think I had about 2:1 aileron differential. Also a small amount (~10%??-ish) of expo to get all the surfaces back to a linear movement with the sticks. Might also have had a little bit extra expo on the elevator because you don't need very much movement at all - it's quite a short-coupled airframe. HTH
-
Posted by Peter Garsden on 01/10/2018 08:12:23: Thanks Andy - I did all of this apart from gluing the wing root to the fuselage, which was a bit obvious when I think about it, and would have helped a lot. Just goes to show how just a small obvious missed step can make all the difference. Ah! ... Well, that might do it. Colour scheme starting to look very nice indeed, BTW.
-
Posted by Peter Garsden on 30/09/2018 07:40:34: The handy balsa trimming tool Andy made and shows in his article works really well - a blade glued between 2 pieces of 3mm balsa, but I think you could us 2mm? What did you use Andy? I just CA'd a new scalpel blade to the bottom of a piece of thick balsa (like, 1/4" or 3/8" ) so that it could be easily held, then just ran the resulting tool along the wing surface (that is, the blade is in contact with the wing surface) so that it cut through the soft balsa that had been stuffed into the gaps. BTW, I'm a bit puzzled by the problems you're having with this bit, I thought it might be the worst part but - for me - it turned out to be quite straightforward. Here's what I did, from memory: Tack-glue the ply root facings to the inside of the wing ribs with tidy dots of CA or balsa cement - can't remember which. Install the wings on the fuselage and glue the root facings to the fuselage where they touch the fuselage. There'll be a gap at the trailing edge, stuff a small (but sightly oversized) bit of medium balsa into the gap (wrap some sandpaper around the fuselage to get the right curvature so that you have about 6-9mm of balsa supporting the TE of the ply root facing. Cut the bit of supporting balsa to the right profile using the tool. From now on it should be plain sailing because all you do is repeat the following until there are no big gaps left: find a short (2-4 inches) gap, sand a chamfer on a slightly oversize bit fo soft balsa, stuff it in the gap (squashing with fingers if necessary), tack glue it to the root facing (because we don't want glue mess on the fuselage), cut it to profile with the tool, then glue it in place properly. Run a new blade between the wing root and ply root facing to separate them, and then remove the wings. Fill in the inevitable small gaps with filler. When dry, sand and cover quickly in case one of your mates comes around an makes an unkind comment about all the filler. HTH A. Edited By Andy Blackburn on 30/09/2018 11:28:15
-
That does look like a nice set of turbine blades! However, bear in mind that my engine intakes were flat so would very probably have had lower drag, if you find it's an issue then I recommend the use of an acetate disc with a small circular hole cut in it for the starter fairing - you'll still be able to see the intake detail but the air won't.
-
Does Mrs Scotty know about the illegal and provocative use of the kitchen table? A.
-
> So question Andy - is my maths correct? Without checking the numbers, the principle is correct - apart from the middle bit of the fuselage that's parallel, the ends of the planks taper in the same ratio as the former size. Just don't forget to chamfer the edges a bit so that if there is a gap between planks (perish the thought!) then it's on the inside and will be filled with glue. However, you don't have to be dead accurate with the planks because you can always make a couple of odd-shaped planks to get everything back to where it should be.
-
> The rudder servo is the trickiest because one cannot get at the horn and adjustment once the planking is on. I am trying to work out how to adjust the clevis if need be... You probably won't need to adjust it at all, but if you really think you'll have to then you can use a ball-link rather than a clevis. To adjust it, you pop the ball-link off using a screwdriver or bent bit of metal and remove the servo, make the adjustment (fingers/needle-nose pliers), pop the ball-link back on using fingers and then re-install the servo. > Incidentally, much better to make the battery box using the battery as a former. Quite difficult to get square. I am sure I have seen them in other kits with tabs, which make it easier to assemble - Andy don't know how easy it would be to redesign? Well, the design is now the property of RCM&E so a re-design isn't on the cards... However, I've never had a problem getting a square battery box; assemble it first using a bit of masking tape inside a couple of the formers with square holes, then square it up at each end with a couple of the square off-cuts rammed into each end (shimmed with masking tape if the laser cut is a bit wide) and then hit it with a bit of cyano. Using the battery as a former might be a bit risky because as you have discovered, they're not necessarily square. Edited By Andy Blackburn on 12/08/2018 20:36:18
-
Another Andy Blackburn PSS Canberra
Andy Blackburn replied to Devon Slopes's topic in PSS Build Blogs
Posted by Devon Slopes on 28/07/2018 10:13:44: Finally F11, the former right at the end of fuselage was designed when Andy thought the bottom tail region was going to be planked, so I made a new one which is round. You can see all these bits in the picture below. In my own defence, I feel that I should point out that I'd corrected that on my own set of printed parts but obviously forgot to change the plan, which is what Sarik obviously used to generate the new parts. Mea Culpa. A. Edited By Andy Blackburn on 07/08/2018 08:52:38 -
I had a long conversation with the tech guy at Sarik about this; between us, we eventually sorted out what was going on. Don't know if you've spoken to them but I should think that they'll be happy to send you some replacement parts that are of the right size. I always put a couple of 100mm lines at right-angles in the top left-hand corner of the plan to guard against scaling issues, but after this experience I think in future I'm going to do the same on the printed parts patterns. However, if you decide to just go with it as it is I think it'll be fine, just remember to assemble the finished wings onto the bare fuselage structure to check that the holes (2 incidence pegs, wing joiner and servo lead hole) are all in the right place. The worst that you'll have to do is to either move some formers by elongating the slots or shim the incidence peg locations. There's a fair margin or excess strength in the fuselage so as long as you fill any large slots, it won't make any difference.
-
I used to have an 2006 Mondeo 2 litre, it was a hatchback but still had loads of space and the seating position was excellent. You could do worse if you can find a good one from a good garage with an up to date service history and a mileage reading that you can trust.
-
BMW 3-series Touring (estate), which is fine - wanted a 5-series as it's a bit bigger but Mrs B made it quite clear that it was too big for her to drive.
-
The 2018 Transmitter Survey!
Andy Blackburn replied to Biggles' Elder Brother - Moderator's topic in Model Flying Polls
Posted by Julian Thacker on 23/07/2018 12:39:50: Andy I had no idea Spektrum rxs were so pricey. I have just bought what I thought was a very expensive rx - the R7014SB - a 14 channel Futaba FASST/FASSTest rx for £166. I only have one model that uses 14 channels and I did not want to get into SBUS. I have been checking out the relatively cheap T-FHSS rxs this year and so far I have noticed no difference in reliability over FASST/FASSTest. Julian Well, no, neither did I until I started looking for a 9 channel Rx and was rather surprised by the asking prices. I had always assumed that Spektrum receivers were going to be relatively cheap, but apparently that's no longer the case. The one I looked at had AS3X so that's maybe why, but it was very difficult to find one without AS3X and I'm starting to wonder if the "normal" receivers are going to be phased out. A. -
The 2018 Transmitter Survey!
Andy Blackburn replied to Biggles' Elder Brother - Moderator's topic in Model Flying Polls
Posted by Mike Blandford on 23/07/2018 09:53:03: Andy, what is it about the "Taranis" programming you don't get on with? I'm guessing you mean openTx programming model. ersky9x open source firmware also runs on the Taranis and may be easier to follow: <snip> Yes, it is. But the last thing I want to be doing with a transmitter is updating the firmware - as far as I'm concerned, it's a black box that has to work 100% of the time without anybody meddling with it. I don't even risk doing a normal software update because I've seen other people's transmitters that no longer work correctly after having had an update. Having said that, I'd be happy sending it to be serviced and also having a software update because then it's their responsibility and if they mess it up I can get my money back... A. -
The 2018 Transmitter Survey!
Andy Blackburn replied to Biggles' Elder Brother - Moderator's topic in Model Flying Polls
Transmitters are of course very personal things. I currently use a Spektrum DX9 after years of using JR - my beautifully ergonomic JR DSX9 was retired after what appeared to be transient radio failure and to be honest the only reason that I'm using the DX9 is that I found that I could usually guess how the programming worked without reference to the manual. I don't bother with telemetry and the voice is just an unwanted feature that I've had to pay for but never use. However, I don't really like the feel of the DX9 and I don't want AS3X, which I object to paying for in receivers, especially 9 channel receivers which are far too expensive at nearly £180. I don't get on with the Taranis programming model which is a shame because it would otherwise be - on paper - the perfect solution, so I'm now eyeing up Futaba. But I just can't afford an 18SZ... -
Posted by Chris Walby on 06/07/2018 22:12:29: Andy, Would that be the same H9 that should have a 60 size in it And I thought putting a 70 in a Speed Air was OTT . Total respect for such a outrageous idea, just be careful in those long steep flat out dives.... Sort of... Yes, it's officially a Hangar 9 Messerschmitt Bf 109F-2 60, but since it weighs nearly 12 lb - quite a lot of which is nose weight - I think even the most powerful 60 is going to struggle. The recommended four stroke is a Saito 125, so I should reluctantly admit that it's not nearly as outrageous as it might initially appear.
-
Hangar 9 Messerschmitt bf109F, spans 63", powered by a Laser 120 Turns a Master Airscrew 15 x 8 at 8000 rpm in hot weather, running on Model Technics Laser 5. The model weighs a ton (11 3/4 lb) but there's enough grunt for some really good verticals. I think it's a great motor. Edited By Andy Blackburn on 06/07/2018 20:52:03
-
Versatile slope soarer
Andy Blackburn replied to Rob Kelly's topic in Slope Soaring and Dynamic Soaring
+1 for the Phoenix Model Products kits; a mate of mine had one of these that was bought second-hand several years ago (might have been a Carrera) and it was lovely to fly, really nice in light winds and thermally conditions (<5 mph) but went like the clappers if you pushed the nose own. -
I hesitate to add more fuel to the fire than is strictly necessary, but here's my experience; I usually use 4 cell 2000+ mAH Eneloops sourced from somewhere reputable (like Overlander) and the biggest, simplest switch I can find with 4-8 standard size digital servos and have never (yet!) had a problem. I've used 5 cell Eneloops on a couple of occasions and whilst there might be a small difference in servo performance (difficult to tell without a back-to-back comparison), there wasn't much difference between that and a 4-cell pack. But some servos don't like 5 cells, particularly on a full charge. I've been using Spektrum receivers for years and have never had any sort of receiver failure or brownout when using a receiver battery, but I've had a failure that appeared to be due to a failed BEC in a speed controller. I think you'll be absolutely fine with a large (or very large, if you need the nose weight) 4 cell Eneloop as long as it's a quality one because if it fails it'll take the model with it. Same applies to the switch harness. A.
-
Deluxe Eze-Kote
Andy Blackburn replied to Graeme Poke's topic in Building from Traditional Kits and Plans
I have used Deluxe Eze-Kote for joining standard fibreglass wing bandage on several occasions and it's fine (the strength in in the glass, not the resin). The only thing you have to be careful of is letting the wing get too wet because the veneer soaks up the resin, expands, and then sets like that - so if you're not careful, you'll get wavy veneer on the centre section. For that reason, what I normally do is: Give the centre section of the wing a very thin coat of Eze-Kote and then take off the excess with some kitchen towel and let it dry properly - at least an hour. This should seal the surface and limit the amount of resin that gets absorbed in subsequent coats. Apply the fibreglass in the usual way using just enough resin to make everything wet, and let this dry for an hour or two - overnight is best. Apply subsequent coats (anywhere between 1 and 8, depending on the finish required) with at least an hour between coats, possibly longer for the later coats. HTH Andy -
Well... £43 on a motor that loses it's magnets doesn't sound like very good value to me... So personally, I'd take a deep breath and spend the extra at 4-maxx. Edited By Andy Blackburn on 27/04/2018 21:03:47
-
Another Andy Blackburn PSS Canberra
Andy Blackburn replied to Devon Slopes's topic in PSS Build Blogs
Posted by Devon Slopes on 07/04/2018 19:05:02: The First Plank. I'm trying to follow Andy's instructions as closely as possible as this is my first from-the-plan build, and apparently there has to be a small ceremony to mark the laying of the first plank. As you can see I've managed to source a "Keep Calm and Carry On" mug, but will the build be irrevocably compromised by the use of Chocolate Orange rather than ginger nuts? ... The sharp-eyed will spot that I've started with a plank at the top (not on the side), I'm not quite sure why. Well... I don't know about the build being irrevocably compromised, but it might get a bit messy as the ceremony does involve dunking... There's nothing wrong with starting the planking at the top (and it's easier to do that, actually) as long as great care is taken to keep everything straight and square; the basic un-planked structure is a bit wobbly, so I advise checking straightness and squareness after adding every plank until a reasonable number of planks have been installed.