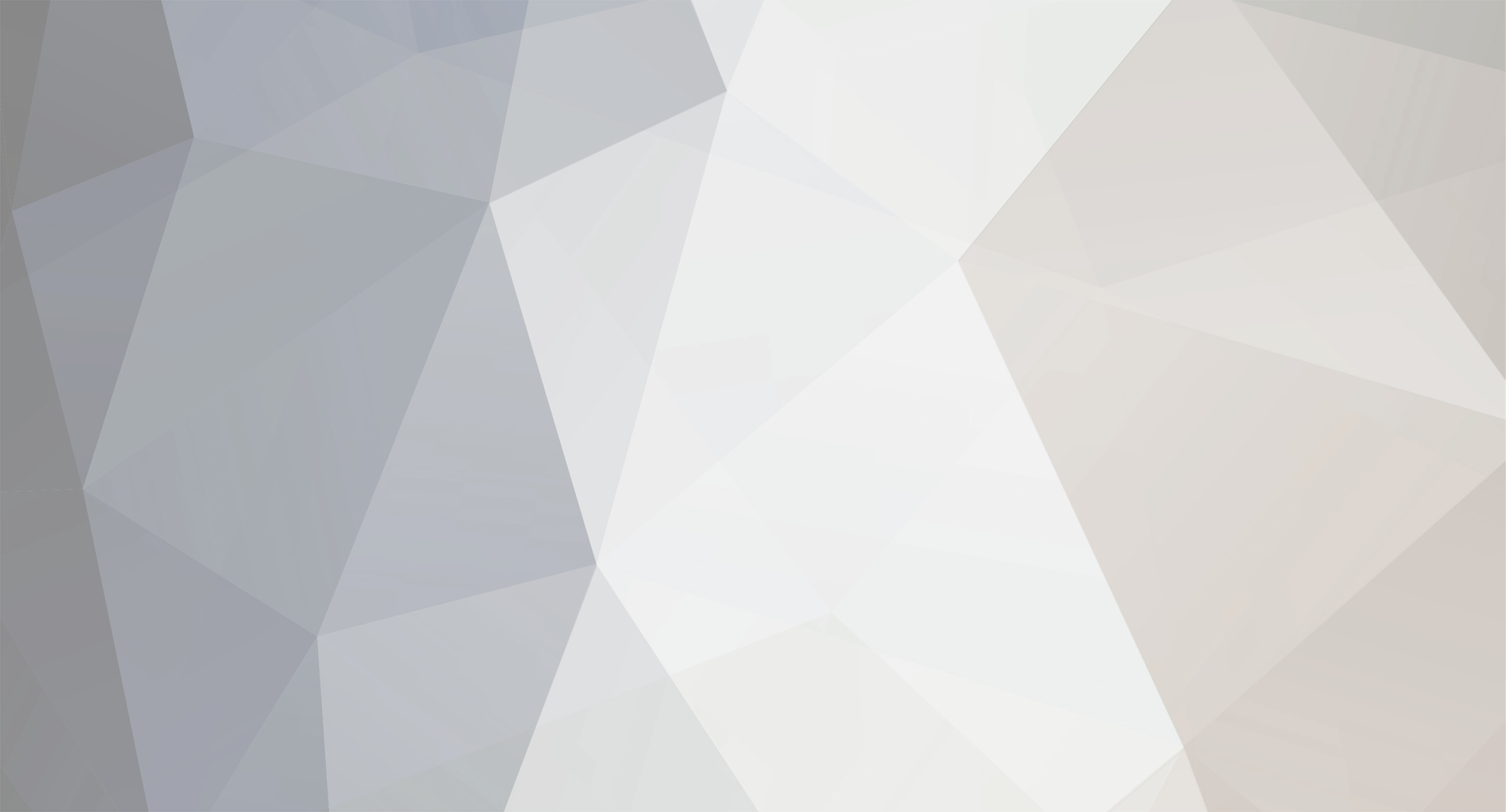
Artto Ilmanen
Members-
Posts
285 -
Joined
-
Last visited
Content Type
Profiles
Forums
Blogs
Gallery
Calendar
Downloads
Everything posted by Artto Ilmanen
-
Yes, this is true. I was more concerned about excessive pressure ruining the seals. But then again, testing with conservative pressure readings should turn out good. And by the way, is there any rule of thumb for the air pressure? I checked the ESM manual but did not see any factory recommendation for the air pressure. I have been thinking of 85-100. I wonder if this is good? Robart recommends 110psi for their gear.
-
Thanks Stu, Good remark. In order to get a conclusive test result I actually connected the whole system and submerged the air tank, both cylinders and the control valve. I operated the valve manually and kept the pressure at 80-100psi with a air compressor: The only spot where the system leaked was the air control valve, as expected. But is was nice to notice both cylinders were good and the pistons moved back and forth without any leaks, despite they had been sitting on a shelve for 10+ years..
-
Thanks Paul, I actually happen to have similar one - I just need to solder a deans connector to run it on a Lipo But I suspect one should have a more reliable air pressure gauge? It's hard to believe you can trust on the gauge on these cheap chines air pumps.. I came across this: https://www.lindinger.at/en/AIRPLANES/AIRCRAFT-ACCESSORIES/Landing-Gear/FESTO-PRESSURE-GAUGE-0-10-BAR-4MM-ID-1PCS./91528 It seems to be a pretty expensive, though
-
good remark - now that you say it it's obvious. Will try again although I do believe the problem persists
-
Ok, thanks for everybody for valuable advice - I certainly know how to fix my air control valve issue now. Another thing: I need to get a pump to fill the air tank at the airfield. I have been thinking of a Robart hand pump or some electric ones. My starter runs on a 3S lipo so maybe I could use it as a power source for the pump. Also, a quality gauge is obviously needed. What kind if setups do you gents use at the field to fill the air tank?
-
I tried again - I also dismantled the thing but no aid - it leaks from both ends. I also tried to play with the slide bar one more time. see video. ESM air control valve 2.mp4
-
Oh, I see - Paul did mention that. Thanks Paul & Ron
-
Ron, although it was not seen on the video I did try exactly what you write - no help, unfortunately. But I will change the O-rings. With any luck I should be good, if not, then a new valve. But I also need to ensure I use proper grease - any recommendations? Just normal vaseline or something else?
-
Thanks - then most likely I should be good with new quality O-rings. Let’s see
-
Thanks, Jon, So you have had better luck with ESM similar control valve units? Anyways, easy to test now as the system is now at hand.
-
thanks Frank what is the secret sauce of the Jetronic electronic valve?
-
Thanks Paul, I may try new O-rings as I need not get them in other sizes, too. If it doesn’t help then a new one, most kikely a Robart blue
-
ok - I played with the air control valve moving the spool in different length manually. No help, see video air control valve.mp4
-
Yes, I have operated it only by hand - although I have not played with moving the spool at different lengths. But, as I have operated it by hand there is no excessive force or side play applied. But, I can try again. Let’s see.
-
Sorry Ron - not being a native speaker I may have used a wrong word here, although I do have seen others using the same word for the valve that controls the gear system. Anyways, the air control valve I’m having is causing issues and I wonder if it is worth the efforts to fix it or should I just shop a new better quality one (which?). As this is my first air retract project I’m pretty much in learning phase
-
This is my ESM air valve (at least I think this an ESM one) This thing just has 2 O-rings doing the job - no spring whatsoever. I tried to apply grease but no help. Maybe new O-rings could help, I dunno..
-
Thanks Jon, Mine is leaking very bad - the pressure drops from 80-90 psi to about 30-40psi in 3-5 seconds. If I wait for 30 seconds I barely get the gear up. I’m using the standard ESM air tank which is smaller than the Robart one. But, I believe it’s ok as long as I get the leaks (air valve) sorted out so the gear performs in a manner as you write If I can’t fix the ESM valve, then, what might be options for replacement valve? a Robart blue valve?
-
Ok, I tested the system for leaks and it is the air valve which is leaking. I need to dismantle it and see if it can be fixed. Or, alternatively, I need a replacement air valve
-
I just installed ESM air retracts on my ESM Focke Wulf 71" - at 85psi plenty of power to operate the gear even with the original ESM wheels that are quite heavy. But, I seem to have some leaks so I need to sort them out. I already moved the air tank from the fuse on the wing so I was able to get rid of the air connectors between the fuse and the wing (another source for leaks). Anyways, carrying out maintenance of the air cylinders is ok but can you do anything with the ESM air valve? (see picture) Or, are you gents replacing the ESM air valve with a more quality stuff, such as Robart air valve etc?
-
ESM Bearcat - powered by Laser
Artto Ilmanen replied to Ron Gray's topic in Scale and Semi-Scale kits
Have you Jon experience any issues such as balsa covering stripping of due the airstream? Or any strange flying behaviour when gear down due to open structure causing some turbulence (potentially?) extract what Ron's wrote: "..the wells themselves need work to them as they are just an open structure and my concern, if flown like that, would be the slipstream getting inside the wing structure and possibly blowing the covering off." I'm not using the plastic wheel wells with my WSM Focke Wulf due to the very same reasons: more scale without them and they do not fit well in anyways. I'm tempted to save some weight & work and just paint and fuel proof the open structure. -
Sorry Jon - I believe there is a typo here and you meant 5/16x unf? ( as we spoke on the phone?)
-
Ok, thanks for everybody for the hints and sharing experience. It seems that both OS and Laser 155 have longer prop threads than Laser 150. With a Laser 150 the single dome nut might the most straightforward way to go as Chris pointed out earlier. I try to ensure the dome nut, whatever I buy, is made of good quality aluminium and not from the most cheapest and softest chinese stuff.
-
Thanks Chris, Sounds promising. I have never used a lock nut with Laser engines and I have never had any issues. The only thing that was puzzling me is the dome nut is of aluminium and thus less capable to take stress of tightening the prop vs a steel nut.
-
Jon, Gentlemen, I'm learning something regarding dome nuts - maybe this is of interest for other Laser enthusiasts, as well: I want to have a dome nut for my Great Planes Super Chipmunk and Laser 150 so I contacted Sarik Hobby and Just Engines. It turned out Just Engines have 2 options: one option is to use a dome nut that can be recessed so steel propeller nut + washer can be used to secure the propeller in place: The dome nut is recessed so it just covers the single steel nut (5mm or about 4 threads left to tighten the dome nut): https://www.justengines.co.uk/shop/accessories/spinners-domed-nuts/medium-domed-spinner-nuts/?v=f0aa03aaca95 the other option is to leave out the steel nut and secure the propeller with a washer + dome nut. In this case 11mm of thread length left to secure the propeller - and no recess of the dome nut (as no steel nut to cover) hmm.. could one of these alternatives work? Also, when an electric starter is being used? Which might be the best one? Some pictures of the propeller axle thread lengths with and without a steel nut
-
Savöx 6V servos with unregulated 2s life?
Artto Ilmanen replied to Artto Ilmanen's topic in All Things Model Flying
Thanks Phil - this all confirms what is said earlier: safe to use unregulated Life with standard 6V servos