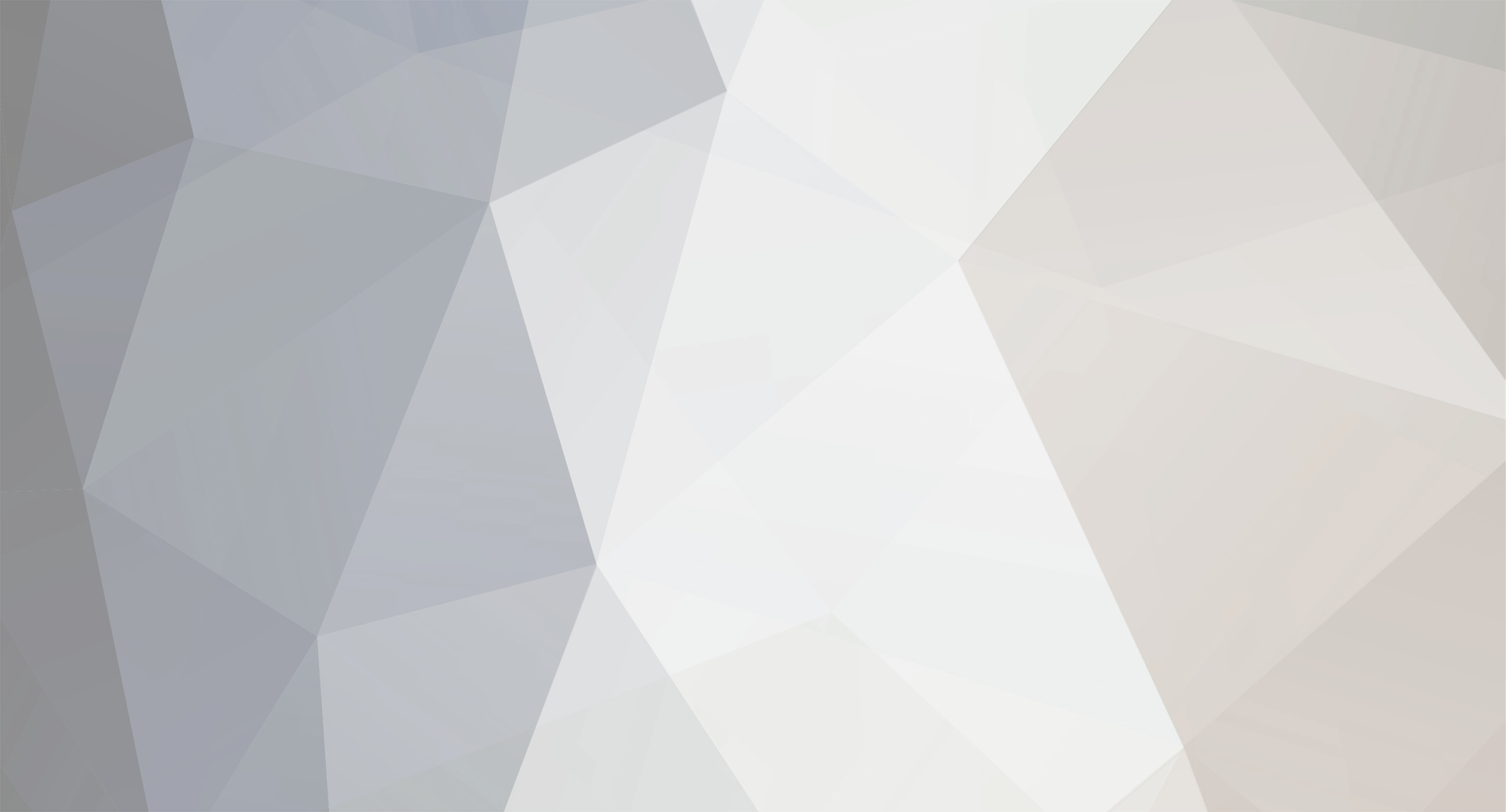
Clive Hall
Members-
Posts
137 -
Joined
-
Last visited
Never
Content Type
Profiles
Forums
Blogs
Gallery
Calendar
Downloads
Everything posted by Clive Hall
-
Airbrush, paint solvent.
Clive Hall replied to Erfolg's topic in Building from Traditional Kits and Plans
I have been spraying models with cellulose since about 1948, airbrushing more recently with art acrylics. When it comes to cleaning equipment used with acrylics I find household ammonia works well. If a paint is soluble in ammonia then it can be useful for slight thinning. -
Barry and Mike both have it right. My biggest problem was that nothing I could do would make the Taranis respond. Companion could not get through to it, and whether I turned it on normally or with the three finger boogie all it would give was the plain white screen and continuous buzz. Anyway, problem about solved. It is more or less working again. I went back to the PC running W7, loaded companion 2.0, attempted to restore 2.0.17 and ended up with it working again on 2.0.20. Don’t ask me how. The Haptic keeps burping intermittently but not enough to be troublesome, and the SD card is empty, so there is work to be done, but the end is in sight. Many thanks to everyone who pointed to solutions, they really saved the day.
-
I am in Cheddar, Somerset, 20 miles south of Bristol.
-
B.C. thanks for the pointer to the video; I did follow it EXACTLY, made sure the STM32 BOOTLOADER was in the right place, made sure that I selected Taranis Plus, and it all went precisely in step with the video until I clicked on ‘Write firmware to radio’. At this point the progress box outline appeared, empty, then after a short time the progress bar appeared. However it ran across the screen instantly and was immediately covered by a box stating ‘Could not check firmware from radio’ with an ‘OK’ button just below. When I click OK it all disappears and returns to the ‘Write firmware to radio’ page. I can not make it progress beyond that. I tried reading the firmware from the radio and there is something there. Saved it, looked at the contents in Notepad, saw references to 2.1.9 among all the code. If I try turning the radio on it still gives the blank white display panel and the Haptic will not stop until I switch off. I am baffled. Perhaps I should give up on 2.1.9 and try to reload 2.0.20 – does this make sense? I am using a Windows 10 PC this time, perhaps that is the problem. I am inclined to go back to Win7 and try the older firmware.
-
I apologise if this is an old question, but I have not found an answer yet. I have an early Taranis which I have easily upgraded from 2.0.20 to 2.1.9 , direct PC connection with it turned off, using Windows 7 Pro. I had a bit of trouble getting a copy of dfu-util.exe into the right folder but once that was done it took only a minute to flash the new firmware. I repeated the exercise with no problems on another two Taranis for friends. Then I acquired a Taranis-plus which had 2.1.6 on board. I tried the same flashing method but failed to remember that a Taranis-plus would not accept the Taranis firmware. It didn't. Now all it will do is light up the display plain white, and the Haptic vibrates continually. Some voice comes through from an earlier model when I move a stick, so an eeprom must be there. The STM32 BOOTLOADER is present so I tried to write 2.1.9 for a Taranis-plus with the battery removed and a direct connection to Win-7. It appears to begin to write the firmware but then a message appears "New firmware is incompatible with the one currently installed". I do not know what to try next, so help would be most welcome.
-
It makes me so angry!!!!!!!!!!!!
Clive Hall replied to Rocker's topic in R/C Retailers / Distributors / Manufacturers
I had a particularly good experience recently with Pegasus models. I ordered some Koverall on line, and then remembered a propeller I should have included in the order. A few minutes later I placed a second order, wishing I had remembered it in time to have to pay only one postal charge. Later that day the phone rang – it was Pegasus, who had spotted that two orders were to go to the same address. They also said the prop I wanted was out of stock so they suggested an alternative that they considered better, and at a lower price. They further said the two orders would be in one package, and later I received refunds for both the less costly prop and the difference in postage. Pegasus is now my first choice when ordering on line. -
What is it? Glass Fibre fus
Clive Hall replied to Alistair Taylor's topic in Gliders and Gliding - General Discussion
First there was the Algebra 8 with bulbous front end and plug-on wings – I made all Sean Bannister‘s F3B fuselages, then he designed the smaller wooden fuselage model which I think one of the magazines published as a plan. John took over and produced the glass version for Dick Edmonds. Neither design was anything like the mystery moulding. -
My post on 26/06/2017 was only to give you an idea of what that rib family looks like, I did not think of it as having any practical use. What you need is a paper print of this file, or even a .DWG or .DXF file by email. What you suggest is really doing it the hard way. Here is a revised version of the ribs, all separated and including a 2mm skin thickness to reveal a true shape for cutting. Or I can post you a full size print on paper – very easy to do.
-
I changed a few input numbers slightly - I think this is closer to the original drawing:- The ribs can be printed individually on a larger file with skin thickness and spar slots, which can then also be used for laser cutting.
-
Steve, I have generated two possible rib sets for the Stuka. The lower one has a symmetrical tip section, the upper one a non-symmetrical tip. Also there are slight differences in the root section; any combination or adjustment is possible. These ribs may differ slightly from the drawing, but they will fly the model.
-
Steve, I have a software solution to this problem - did you get my PM, with details?
-
What is it? Glass Fibre fus
Clive Hall replied to Alistair Taylor's topic in Gliders and Gliding - General Discussion
I checked with John Hall this morning (I’m his dad) and his terse comment was “Nothing to do with me”. Sorry, but I can’t help beyond that. -
What is it? Glass Fibre fus
Clive Hall replied to Alistair Taylor's topic in Gliders and Gliding - General Discussion
Alastair, I have to eat crow pie: it is not a Cascade, though very similar. When I dug out the black fuselage to take a photo I realised I had been mistaken, too long since I looked at the model for ancient memory to be reliable, so please accept my apologies. For what it’s worth, here is a shot of the Cascade bits. The fuselage length is 1130mm; the wingspan is 1520mm, root chord 200mm and tip chord 180mm. The wing and tail parts are all foam/obechi, covered in glass/epoxy. To finish your model I would suggest scaling these components to the length of your fuselage, and cutting a foam wing with Eppler 193 section. The radio fit was always going to be tight when the only battery choice was NiCd. With a 500 mAh 2S lipo and suitable radio and servos it should become a comfortable fit. I hope that goes some way to make up for my error. -
What is it? Glass Fibre fus
Clive Hall replied to Alistair Taylor's topic in Gliders and Gliding - General Discussion
I am happy to be able to say that I recognised it instantly. It is a CASCADE, produced by John Hall during the time when he was making the Algebra fuselages for Dick Edmonds. I have one, moulded in black, in my workshop at present, left over from the days when it was a project for a kit, and my part in the venture was to build one and write the kit instructions. The model is still unfinished but I can provide more information as the completed wing is standing in a corner and the tail bits are in a bag on a shelf. I can post photos if anyone wants to see them. -
I agree that the right mode to fly is the one which is the more comfortable. As I said, I began on m ode 2 and flew it for a while, and was quite comfortable with it. However once I had made the jump to mode 1 and was getting used to that I realised I was more comfortable with mode 1 - so I have stuck with it. Slight change of topic– I think the comparison between mode 1 and full size flying does not really hold up. In a full size cockpit a flight can easily last two hours, and a two stick mode would not work. Also there are aircraft which lightly built pilots would be ill-advised to try because of the muscle needed, some Slingsby gliders, for example. There are too many other jobs to do which need a spare hand while the other one flies the craft with one stick:— switching radio frequencies, changing fuel tanks, frequent adjustment of trim wheels, handling maps, and at crucial moments selecting flaps and retracts. A pilot couldn’t possibly fly twin sticks and have to pump a slow manual retract at the same time. Then there’s the little matter of the rudder. With a model an average flight time at the club strip is about 6 minutes and all the sticks, knobs and switches on a tranny are placed close together, within easy finger reach. I understand the feeling about full size, but it’s really a romantic illusion. Perhaps we should call it the Biggles syndrome.
-
Posted by ron evans on 05/01/2017 10:29:47:. I wonder if deep down mode 2 users are frustrated full size pilots. Not mode1 users of course, I can only think of one full size mode 1 aeroplane.....the Wright Flyer. I have heard that all the early flyers were mode 1 until Bleriot invented mode 2, so it has a good ancestry. I find the claim of equivalence to full size flying dubious, and will continue to do so until I see the Mode 2 lot working the rudder with their feet. I learned to fly Mode 2, carried on with it for the next 7 years, then moved from East Anglia to the Southwest and joined a Mode 1 club where I was persuaded to try converting. A buddy box helped, and it did not take long. At a halfway point when I was equally at home with either mode I had no doubt that Mode 1 suited me better and I am still with it today, though I can still fly Mode 2 and take over from someone who is having problems. Not being frivolous, I think trying the other mode is worth a serious try, but calls for genuine determination and the abandonment of anti-mode prejudice. With a bit of persistence it’s possible to master an alternative mode. Only after doing this is it really fair to think of pronouncing one or other mode superior. Even then the old arguments will probably never die out.
-
The ailerons are now ready to fir, and the cap-strips are on the ribs. Impact glue is ideal for this as it removes the need to use pins, so no split wood, and no danger of a strip lifting once it is in place. Just the thinnest smear of adhesive is enough on the rib edge and the inner face of the cap strip. Leave about 3 minutes to dry, then put in position, and the strip is fully fixed.
-
Ballerina PET is back in action. The dodgy wrist has recovered enough for careful use, so I have completed the wing centre section sheeting and now I have begun to make the wing tips. I like to use laminations but regard balsa as a bit flimsy, so I use obechi veneer as used for skins on foam wings. I cut strips about 8mm wide then laminate them in groups of 7 in a temporary jig made of pins. I knock the pins into the printed outline of the part, prepare the strips by damping them in water, glue them together with white glue, and then hold them in place with another inner row of pins. It helps to reduce the glue drying time if the lamination is left a few minutes to allow the glue to grab, and then lifted a small distance clear of the bench. When dry a hard solid component lifts out and is replaced by another batch of glued strips. Once finished the pins go back in the pin box. The next set of laminations will be the tail group outlines, made the same way.
-
Ailerons and centre section sheeting are now fitted, but no more posts for a while. The build has hit the buffers – problem with left hand, the doc says no more modelling for at least a week; can’t even play with the simulator.
-
I heard rumours that the bureaucrats in Brussels had forbidden the sale of contact glues containing solvents: not true, today I bought a new tube of my favourite. The wing skins are on at last; here is the rest of the detail for the method. The wing sits on cradles that can be pinned to the bench. It helps to use masking tape to hold the ribs down on the cradles. Note two extra small cradles have been placed under the leading edge to keep it straight. I apply the contact glue by putting drops from the tube at about 20 mm intervals and then spreading them quickly with a finger-tip. This spreads the glue at the right thickness. Just make it go as far as it will freely then add some more drops for the next bit. Apply it to all the frame edges and all the marked areas on the sheet that make contact, then return the frame to the cradles and glue two cocktail sticks into place in the holes in the spar. Place pieces of newspaper over most of the glued frame to protect it from premature contact, leaving about 1 cm gap between the edge of the paper and the spar. If it is too close to the spar it can be difficult to pull away later. Lower the skin gently on to the cocktail sticks. This will ensure exact placement of the skin, so press it down evenly along the spar. All it takes is gentle pressure. Once the two surfaces meet the joint is made. It can be pressed more firmly later - it will not move after the first contact. Next withdraw the paper and use the edge of a piece of wood to press the skin on to the ribs working progressively from the spar to the leading edge. A piece of 1/2 inch balsa sheet will do for this. Finally make sure the leading edge has made contact along all of its length by running a finger and thumb gently along it to make sure it is squeezed together.. That does it. The skin is now firmly and accurately in place, but the wing will still have some slight ability to twist until the other skin is attached. Cut off the cocktail sticks close to the surface and sand them to the level of the newly applied skin. Any internal wing installations can be done now, before the second skin is applied. The panel is next turned over and settled in the cradles for the other surface. This is the critical stage where the cradles are most important, as the attachment of the second skin removes any twisting flexibility in the panel and finally sets the incidence along the panel. For this reason I usually apply the lower skins first as they have less curvature. The cradles can be designed to include washout if it is required. Use the same skin attachment method again as was used for the first skin, making absolutely certain that the panel is firmly settled in the cradles and that the cradles are standing on a flat surface. Then repeat the process for the other panel. That’s it. It works for any kind of wing, parallel, tapered, delta, and to some degree even for elliptical. A useful tip is to sand the outer surface of the wing skin before doing anything else.