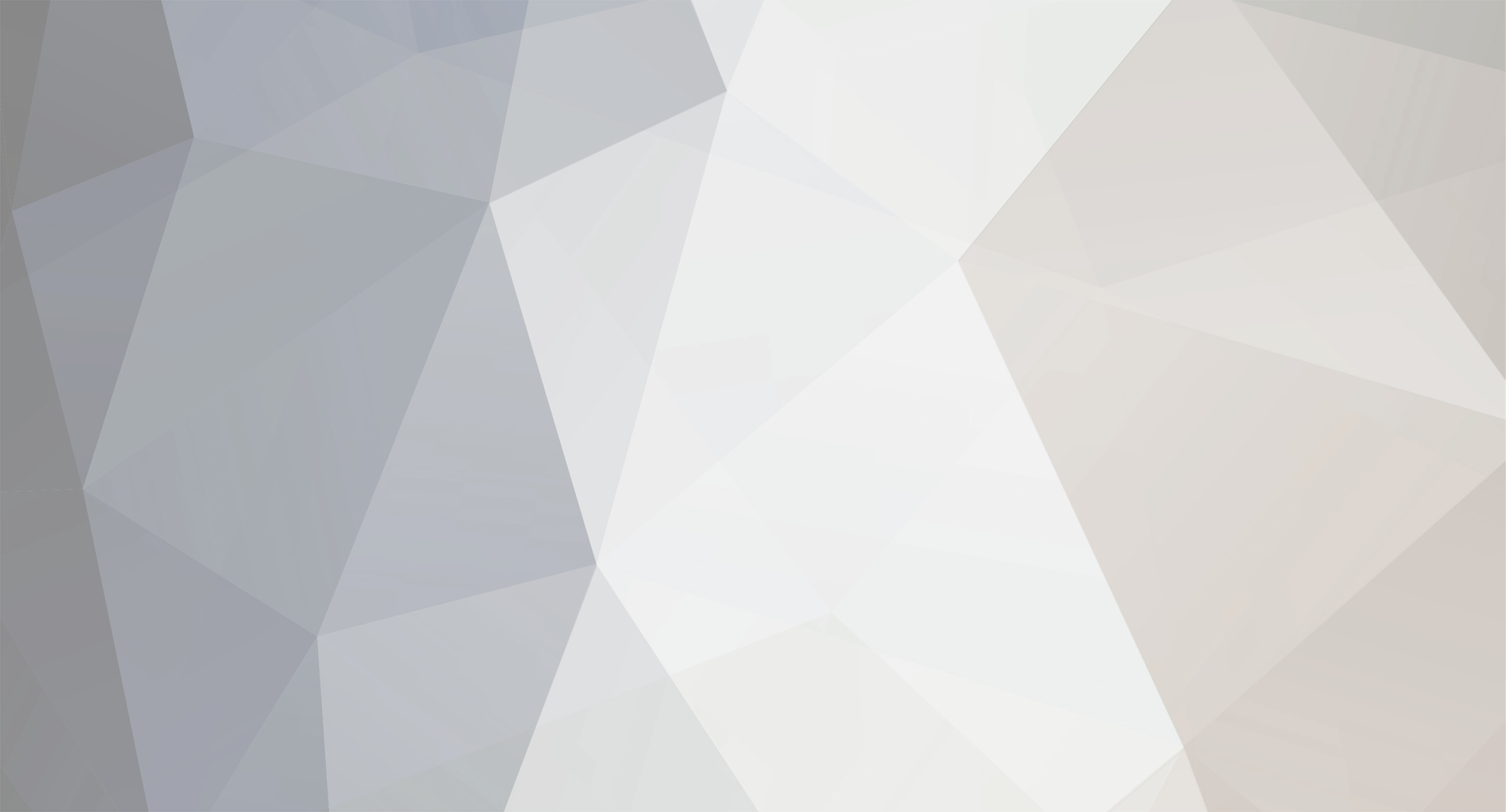
John Wh
Members-
Posts
19 -
Joined
-
Last visited
Never
Content Type
Profiles
Forums
Blogs
Gallery
Calendar
Downloads
Everything posted by John Wh
-
Hello, I've just seen this post. I have a Laser 45 and a Laser 50 that I've been renovating. I changed the bearings on the 45 and tried to bench test it but it wouldn't go, maybe need to grind the valves a bit. Can't remember where I'd got to with the 50; I think the exhaust valve needs some valve grinding too. I made a bit of a hobby of buying old gunked-up Lasers and renovating them, before selling them on. (Even though I only fly electric?!?) David, are you still interested if they need some more work?
-
More Good Service........
John Wh replied to Former Member's topic in R/C Retailers / Distributors / Manufacturers
Get neck ache when I visit there. -
The old, pre-digital solution would be to use a logarithmic potentiometer, sound pressure-to-volume is a logarithmic relationship, if I'm remembering correctly. Is your current rotary switch a linear pot. ?
-
Testing clone of the TowerPro MG996R Servo
John Wh replied to John Wh's topic in General Radio Discussion
Thanks Paul. The servos I tested were each drawing 2Amps when taken to their maximum of 10kg.cm torque loading. The temperature never got above 60°C on the outside of the case (measured using a IR temperature meter). I always test servos now before putting them in my aircraft. You can get cheap servo testers which will constantly cycle a servo through its full movement . Every servo I get is run for 20mins or so with some loading on it to check it's not going to burn out. If we're prepared to buy cheapo equipment nowadays (I am!) then I think perhaps we have to take responsibility for testing everything ourselves. Futaba would be concerned if one of their's burned out, can't imagine the clone companies caring so much... Edited By Whisperit on 27/10/2016 19:21:57 -
Testing clone of the TowerPro MG996R Servo
John Wh replied to John Wh's topic in General Radio Discussion
The servos I tested came from an Amazon seller called Proster, or Proser or Prozer (it's actually very easy to change your selling name on Amazon, I think they've been 'developing' theirs!). A lot of the similar looking things sold on Amazon are actually the same and from the same factory (in China somewhere), but distributors buy their own Barcode numbers and print theitr name somewhere on it and try to pretend its unique. So, from your comments and a bit more research, mine are very likely clones. Perhaps Towerpro didn't trademark the MG996R name, or perhaps the clone distributors are trying to get away with it. Looks like Towerpro's have Aluminium shafts now. [by "vertical play" I meant the play in the vertical servo horn shaft expressed as the angle of up/down movement this causes in the servo horn. How much movement this causes in your connected push-rod/snake depends on how long your servo horn is.] Never actually tested a servo before, trying to think of what else to do. -
Question about adding web between wing spars
John Wh replied to DavidKP's topic in Building from Traditional Kits and Plans
The other function of the webs is to prevent the top and bottom spars trying to 'slide over each other' as the wing bends. (The webs resist the shearing forces between to top and bottom of the wing.) They make a big difference to how much the wing will bend up in flight. (Imagine an I-beam without the vertical piece joining the top and bottom parts together.) The actual stress direction on these webs, for both resisting wing bending and wing twist, is 45° to the spars. So, for maximum strength you should actually align the grain of the balsa at 45°, rather than horizontal or vertical - but it won't actually make much difference. (This is why you sometimes see steel I-beams with criss-cross struts instead of a solid web - making the beam lighter overall with the same strength.) By far though, the main advantage of webbing is to complete the front wing-box; combined with the top and bottom sheeting on the front quarter of the wing the torsional stiffness increases by several hundred times (do the maths, and in a theoretical case, it's actually 1000 times stiffer in resisting twisting forces). John -
Testing clone of the TowerPro MG996R Servo
John Wh replied to John Wh's topic in General Radio Discussion
Torque testing ! : -
Testing clone of the TowerPro MG996R Servo
John Wh replied to John Wh's topic in General Radio Discussion
Torque test: I built a test rig with a heavy weight hanging from the end of a 4cm servo horn. As the servo turns the torque builds up and the mass and angle at which it can't turn any more tells us the maximum torque. After several tests with 3 of these servos the maximum torque is 10kg.cm @ 6.6V (high discharge battery - no voltage drop so this is the servo limit and not the battery. Speed Test: This is very hard to accurately measure, so I just tested it against a Futaba S3003 servo. These MG996R servos are slightly slower in a 'race' test between maximum deflections. Freeplay: Rotation free play is approx. 0.7° Vertical play on servo horn is 1.4° - this is VERY BAD for a servo. Would not use this for an elevator. Resolution: The resolution is not good enough to move for each click of the trim on my transmitter. In general, it only moved every two clicks, but it did move by two click amounts, so it the electronics are registering the new position angle but mechanics can't respond so precisely. BUT, this is as good as the new Futaba S3003 I compared it to. -
I was asked to test these for an Amazon review. Thought I'd share my findings with you. The main thing to note is that some adverts say that these have double ball bearings- they do NOT!! They only have a bushing that does not stop a lot of shaft wobble. In Summary: Maximum torque measured = 10 kg.cm @ 6.5V Speed: Slightly slower than a Futaba S3003 Freeplay = 0.7° rotation and 1.4° on the shaft Bearing: One brass bushing, no ball bearings anywhere inside. Resolution: Movement every two trim clicks (same as Futaba S3003) Weight = 58 grams (without fixings or horn) OVERALL: I think these should be regarded as high torque, metal geared STANDARD servos. But with poor free-play and no ball bearings. So for applications where high torque is constantly required, the bearings in these are not good enough. The free play can be expected to increase slightly with use and the plastic surround wears. Construction: Brass gears that seem well made. No glue on soldered connections, vibration resistance an issue? Motor has worked well. I tried running these for 20 minutes under a high loading, the casing around the motor reached 60°C but steadied at this temperature. The servo still worked well after this. Fixings: Servo horns are thicker than usual, and a normal clevis won't clip shut because of this. The shaft will take Futaba horns. The brass eyelets are TOO LONG! They stick out by about 1mm from the rubber grommets and hence will cause too much movement in the servo on the mounts. The mounting screws are too short! They only stick out by 4 mm from the brass eyelets!! Nothing like long enough to securely hold the servo, especially if you are intending to use the high torque these servos are capable of. I'm using one for the rudder with pull-pull wires (nice and tight so the shaft slop doesn't matter. Would use these instead of standard Futaba servos, if it wasn't for the wobbly servo horn shaft.
-
Posted by Dave Hopkin on 05/03/2015 00:09:37: Theoritically tf the tail is canted to one side, it shouldnt create any yawing effect when the elevators are in neutral, but as soon as the elevators leave neutral as well as creating a pitching effect they will also induce a slight yawing force, though saying that there would have to be a significant cant to be noticable - with a left canted tail this would be yaw to the left with up elevator and a yaw to the right with down elevator There will be a yawing moment with the elevators in neutral still, because the tailplane will be producing a downforce in flight to keep the aircraft trimmed. (The wing always has a pitching moment around it which causes the nose to pitch down, the tailplane balances this and the other pitching moments about the aircraft.) The constant yaw caused by a canted tailplane can be easily balanced with the rudder - so Tim, you probably haven't noticed it in straight & level flight. Thrust line angles are still worth checking, even if you do find a twist in the wing.
-
Hi, A left lean on the tail (so port side of tailplane down) would produce a small nose-left yaw, since the flow over the tailplane comes from above (downwash behind the wing). The tailplane will be producing down-force to trim. Have you checked the thrust line on the powerplant recently? Has it got out of alignment? I don't know which way the propeller goes on the Skywalker (it's the one with the pusher prop just behind the wing?). If it hasn't got the required right/left thrust this will cause a yaw, which if nose-right will cause a right roll. John
-
thrust line for Bristol scout, 54" by David Womersley
John Wh replied to GrahamWh's topic in Scale Matters
Hello, As far as I understand things (from what I've read and remember from uni days), right thrust is to counteract the following effects due to the rotating propeller: 1. Torque reaction of the propeller (varies according to mass of propeller, revs, and mass of aircraft (or more accurately its moment of inertia around the motor shaft - i.e. if you had heavy wing pods for some reason the propeller wouldn't be able to roll the aircraft round so fast). Torque reaction causes a LEFT rolling moment. 2. Swirl behind the propeller. As the propeller goes round, as well as thrusting the air back, it is also dragging it round with it. The high speed air goes over the fuselage and past the wing root, fin, tailplane all in a slightly rotating motion. So, the port wing (and tailplane) experiences a slightly higher AoA on its inner part which is in the prop. wash, and the starboard wing a slightly lower AoA. Propeller swirl causes a RIGHT rolling moment. 3. Upwash through propeller disc. The air flow into the propeller 'disc' is not straight and level. Due to the lift of the wing(s) air is drawn up from below the front of the aircraft (upwash in front of an aircraft and downwash behind it). So, the air drawn into the propeller disc comes in at an angle from below. This means the downward moving blade (starboard side) experiences a slightly higher AoA and the upward moving blade on the other side a lower AoA. This means the propeller disc produces a yawing moment to the LEFT. The first two effects can roughly cancel each other out (depending on lots of factors - how much of your flying surfaces are in the prop. wash, etc.). The third effect depends on the lift coefficient you are flying at (higher CL (low flight speed) means more upwash through the propeller disc). You may be flying at a low throttle setting for low flight speed (at high CL), or you may be at high throttle as you approach the stall (doing a high nose-up fly-past!!), so high CL and high propeller left yaw. (complex!) Yes, right rudder will counteract the upwash effect on the propeller but not necessairly in a proportionate amount depending on your flight condition and the particular design on your aircraft. Using right thrust (typically 2° for model aircraft) instead of right rudder trim is a more reliable and consistent way of counteracting all three effects. (I started to think about what happens for inverted flight and got a headache!)