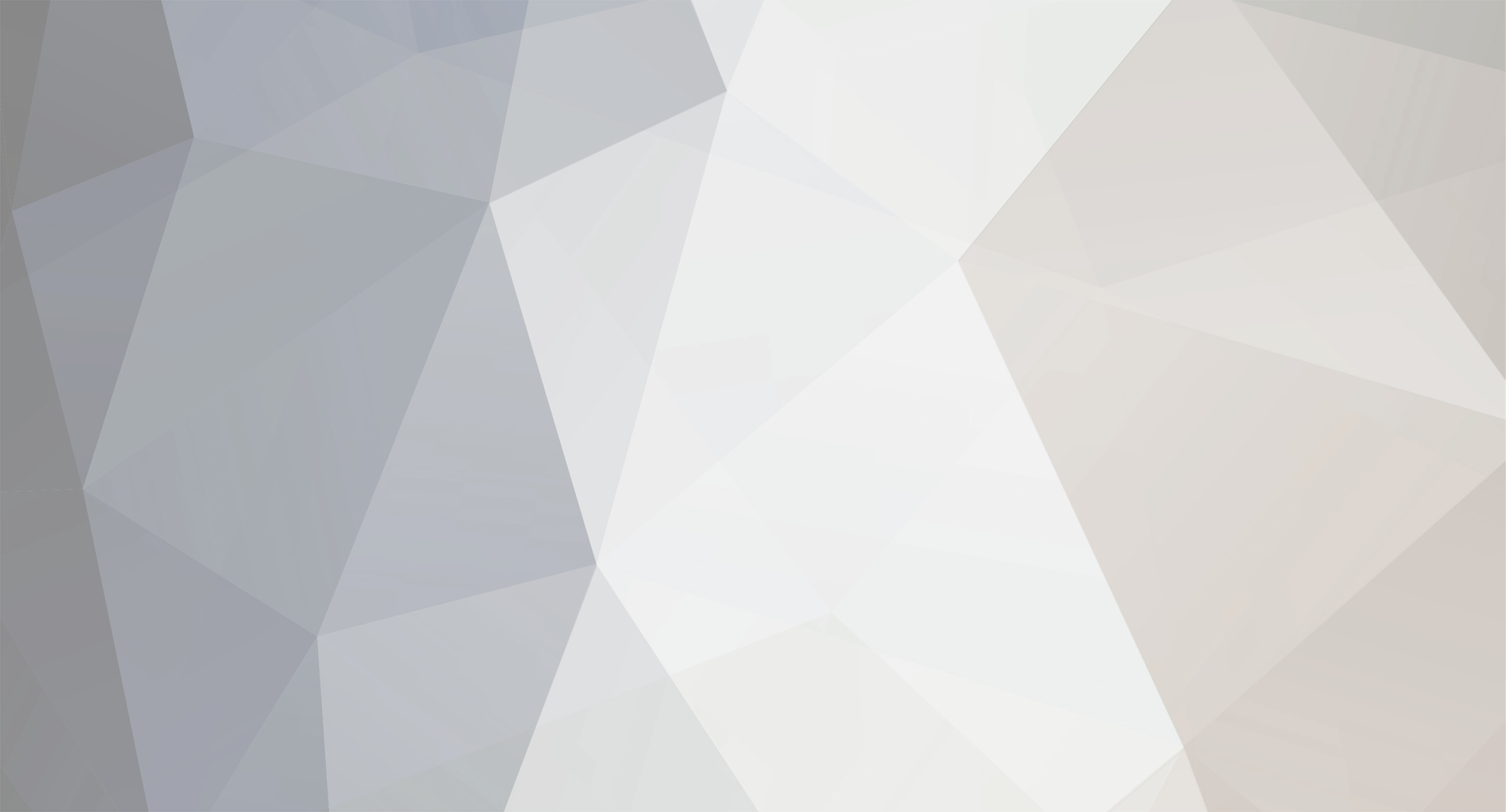
Delta Foxtrot
Members-
Posts
621 -
Joined
-
Last visited
Never
Content Type
Profiles
Forums
Blogs
Gallery
Calendar
Downloads
Everything posted by Delta Foxtrot
-
Scratch building, or is it?
Delta Foxtrot replied to Depron Daz's topic in Build Blogs and Kit Reviews
My definitions for what they are worth: Drawing up and building from your own plan: scratch build. Starting from a plan: plan build. Starting from a kit: kit build Assembling an ARTF: assembly. I am sure there are other shades and that this is subjective, but the words ought to describe what is involved in the process of making a model aeroplane. Edited By Delta Foxtrot on 13/04/2016 12:19:35 -
I thought he was trying to commit suicide by slashing both wrists simultaneously at the start of the video
-
Caption time again!
Delta Foxtrot replied to Beth Ashby Moderator's topic in All Things Model Flying
You're gonna need a bigger elevator! -
Craig's first build Ballerina
Delta Foxtrot replied to Craig Thomas's topic in The 2016 Ballerina Mass Build
Every plan I have shows balsa formers with the grain across the fuselage width. Perhaps someone should tell the RCME draughtsman, to be fair I think most plans I have seen are the same. Given the number of models that Peter has designed and built, I would follow his advice on these matters. I suspect that once the fuselage sides are in place it will have adequate strength in either direction. -
Craig's first build Ballerina
Delta Foxtrot replied to Craig Thomas's topic in The 2016 Ballerina Mass Build
Not according to the plan on Craig's wall, see a few posts up. -
Craig's first build Ballerina
Delta Foxtrot replied to Craig Thomas's topic in The 2016 Ballerina Mass Build
I think you want the grain in the other direction on your formers, that makes it stronger laterally and less likely to break like that one did. -
Rules of thumb for electric flight
Delta Foxtrot replied to Geoff S's topic in General Electric Flight Chat
One correction: Power is proportional to N^3 and D^5 not D^4 Thrust is proportional to N^2 and D^4 where N is rotation speed and D is the diameter. Edited By Delta Foxtrot on 15/02/2016 16:51:40 -
If you are new to building then it might be worth buying something like this: **LINK**
-
Safe Discharge Dodgy Lipo
Delta Foxtrot replied to Tony Smith 7's topic in Electric Flight for Beginners
Posted by MattyB on 13/02/2016 16:45:12: Please, can we knock this salt water bunkem on the head once and for all?! It is just a bad method - the contacts on the battery will oxidise long before it is fully discharged, and piercing cells is never a good idea; there's always a risk of fire unless the cell voltages are absolutely zero, and polluting lithium salts will be released as it degrades. The solution is simple - just discharge the battery to 0V with the appropriate load (12v bulbs in series or parallel to match the pack voltage are good), cut the contacts off, tie them together and dispose of at the local tip in the battery disposal bin. Simple, non polluting and completely safe. I completely agree with you on this Matt. -
Mixing brushless motors, ESCs with water!
Delta Foxtrot replied to Delta Foxtrot's topic in General Electric Flight Chat
Posted by Simon Chaddock on 21/01/2016 21:35:07: Delta Foxtrot My concern is not that an air prop won't work in water but with its efficiency when doing so. An air prop is designed to work well in a very low density medium and has relatively thick section high aspect ratio blades. whereas a water prop has very wide low aspect ratio blades that have a very thin section. A water prop is that shape for sound hydrodynamic reasons. With only limited 'human power' available you would be well advised to use the most efficient design of prop for the medium in which operates. Simon, The Reynolds numbers for a prop operating at the same non-dimensional conditions in water are only 1.5 times that in air, so very similar so the boundary layers would likely also behave very similarly. Similar here in this context is used in an aerodynamic sense. Therefore if the prop does not suffer from cavitation, and I now think this most unlikely, the efficiency should be quite similar. As for the comments of prop shapes marine vs aircraft see john and my earlier posts -
Mixing brushless motors, ESCs with water!
Delta Foxtrot replied to Delta Foxtrot's topic in General Electric Flight Chat
Posted by PatMc on 21/01/2016 22:19:06: DF, have you considered using oars ? No! Not within the rules for this record. -
Mixing brushless motors, ESCs with water!
Delta Foxtrot replied to Delta Foxtrot's topic in General Electric Flight Chat
John, Thank you for your considered response, your thoughts are very close to my own. I have some professional experience in the aerodynamic design of aviation propellers, but not marine propellers. My initial thoughts were to design to the largest practical diameter to achieve a high Froude efficiency and design the blading to achieve minimum induced drag. some compromise on diameter may be needed if the blading looks non optimum or impractical and I may need to drop the blade loadings if the efficiency characteristics looks too peaky. The codes I plan to use are very similar to the methods used to design the propellers for successful human powered aircraft. The idea of testing model aeroplane propellers is perhaps unlikely to deliver the optimum solution, but it will provide a link to some existing wind tunnel data which could help with design trades and it will allow us to shake down the test rig which will be needed to test a bespoke design. It would be good if there were off the shelf propellers for human powered boats to have a look at as a bespoke design could be costly and take some time to develop. I would be very interested if anyone knows of anything that might fit the bill Your comments of the form of marine propellers is very helpful and confirms some of ideas I have picked up from text books and others forums. -
Mixing brushless motors, ESCs with water!
Delta Foxtrot replied to Delta Foxtrot's topic in General Electric Flight Chat
Posted by Dave Hopkin on 20/01/2016 23:31:38: Relatively clean water shouldn't affect the electrics - but the density of air at 0 degrees is 1.2 Kg per cubic meter, water at 0 degrees has a density of just under 1000 Kg per cubic meter - so spinning a air prop under water require about 833 more energy than in air, that increase can only come from one place, current out of the Lipo........ hope you have a REALLY big ESC! Dave, yes, however you do not spin the prop that fast in water. power scales with density and rpm cubed, so given propeller operated at a given input power in water will be spinning much slower than in air. The guys pedalling this 3 man boat are likely to be able to provide around 400 watts continuously so the challenge is to match the prop to that sort of power, so the esc requirements is not as large as you think. -
Mixing brushless motors, ESCs with water!
Delta Foxtrot replied to Delta Foxtrot's topic in General Electric Flight Chat
Colin, Thanks for that. The video Pete linked to clearly shows ESCs must be kept dry as you say. -
Mixing brushless motors, ESCs with water!
Delta Foxtrot replied to Delta Foxtrot's topic in General Electric Flight Chat
Pete, Thanks very much, that video was very useful and answers all of my questions. -
Mixing brushless motors, ESCs with water!
Delta Foxtrot replied to Delta Foxtrot's topic in General Electric Flight Chat
Posted by Donald Fry on 20/01/2016 20:16:05: Delta Foxtrot, you are as mysterious as Mata Hari on a Saturday night. What is this about, have you found a route to cold fusion? Didn't she get shot by firing squad? I am not aiming for cold fusion, just doing a bit of research into propeller performance for a human powered boat. I am looking at how well off the shelf aeroplane propellers fit the bill. Marine propellers usually look very different, but a look at some data on large APC props suggests that they might do the job. Looking at HPB sites the propellers used on similar craft look more like aircraft props. One potential problem is cavitation, so I want to check this out using a simple test rig. If the propeller performance is close to that predicted in wind tunnel tests after due allowance for the difference in fluid properties then this might just be good enough, if not then I will have to design one. The prop does not need long life, just enough for 24 hours use, but it does need to be quite efficient. The propeller will be turning much slower in water so ideally I need a low Kv setup. The test rig doesn't need a long life, just enough to get the job done. More than that cannot say or I will suffer the same fate as Ms Hari -
Mixing brushless motors, ESCs with water!
Delta Foxtrot replied to Delta Foxtrot's topic in General Electric Flight Chat
Thanks Allan! 18 inches is a useful extension that may just be enough for the present. It will be tested in a lake from a boom attached to a boat. -
Mixing brushless motors, ESCs with water!
Delta Foxtrot replied to Delta Foxtrot's topic in General Electric Flight Chat
Posted by Delta Foxtrot on 20/01/2016 19:39:11: Posted by kc on 20/01/2016 19:37:22: You could ask the question on the Model Boats forum...... Which one would that be? Found it! I did not know that there was a forum just like this, but for boats. -
Mixing brushless motors, ESCs with water!
Delta Foxtrot replied to Delta Foxtrot's topic in General Electric Flight Chat
Posted by kc on 20/01/2016 19:37:22: You could ask the question on the Model Boats forum...... Which one would that be? -
I need to make a test rig to measure propeller performance underwater. I would like to test the concept with a quick and dirty prototype. The basic idea is to mount a brushless motor off a pylon with esc, along with speed controller and watt meter and submerge to measure thrust and power input at various water speeds. I could design a pylon to house the esc etc to keep this dry, but for a quick look see I wondered what would happen if the components were submerged. I suspect that the motor would run ok for a reasonable length of time, but not sure about the esc. The test would be in fresh water. I also would like to know how much I could extend the esc to motor wires as I may have to do so to keep the watt meter out of the water. I know that this is an odd query, but I know that there is a huge amount of practical knowledge on this forum.
-
Good to see the Mossie on the list, as if it was ever in doubt. I can strongly recommend Graham Simons book: Mosquito the Original MRCA, this contains some very interesting data comparing the Mossie with other RAF bombers. The mosquitos, with a 2 man crew, could carry a 4,000 lb bomb load to Berlin at 265 mph compared to the B17 which could manage a 3,500 lb load at 150 mph using a 10 man crew. The loss rate per sortie for the mosquito was also considerably lower than any other RAF bomber, and probably all other bombers of the era, which given a two man crew vs five to ten in most other bombers makes it a spectacularly more economical in terms of aircrew losses. This was clearly much more than a bomber carrying out duties as diverse as ferrying ball bearings and Neils Bohr from Sweden whilst in service with BOAC during the war.
-
What about the Fokker D-VII? The respect in which this was held by the allies is made clear in article IV of the armistice agreement, listing war materials to be handed over at the end of the First World War. The D-VII is the only aeroplane to be specifically listed. The Fokker D-VII was one of the first aircraft to utilise a thick aerofoil section after the Dr-1. Previously designers chose to use thin sections in the mistaken belief that these would be superior, however research carried out by Ludwig Prandtl et al at Gottingen demonstrated the superiority of thicker sections at representative Reynolds numbers of the time. This is probably the point in history where the science of aerodynamics really started to have an impact on the design of the aeroplane. It would therefore be in my top 10. Edited By Delta Foxtrot on 30/12/2015 19:03:49
-
Aileron induced wing flutter
Delta Foxtrot replied to Delta Foxtrot's topic in All Things Model Flying
Strange how a posting on flutter led to Mick Potts, but he was a nice guy and I am glad to hear you had lots of good times with him. Dave -
Aileron induced wing flutter
Delta Foxtrot replied to Delta Foxtrot's topic in All Things Model Flying
Geoff, I remember when I first got in touch with Mick Potts about joining and arranged to meet at the Palm Court roundabout one Sunday morning. It was pouring down and no one but Mick was there, he obviously only turned out for my benefit. We met up with a couple of the Broadway lads and rode out to Elton Cafe, Mick left us before the cafe having made sure I was ok riding with the others. I met Mick a few times over the years after leaving the club and was sorry to hear about his health problems and later his passing. David Edited By Delta Foxtrot on 29/12/2015 20:20:14 Edited By Delta Foxtrot on 29/12/2015 20:20:45