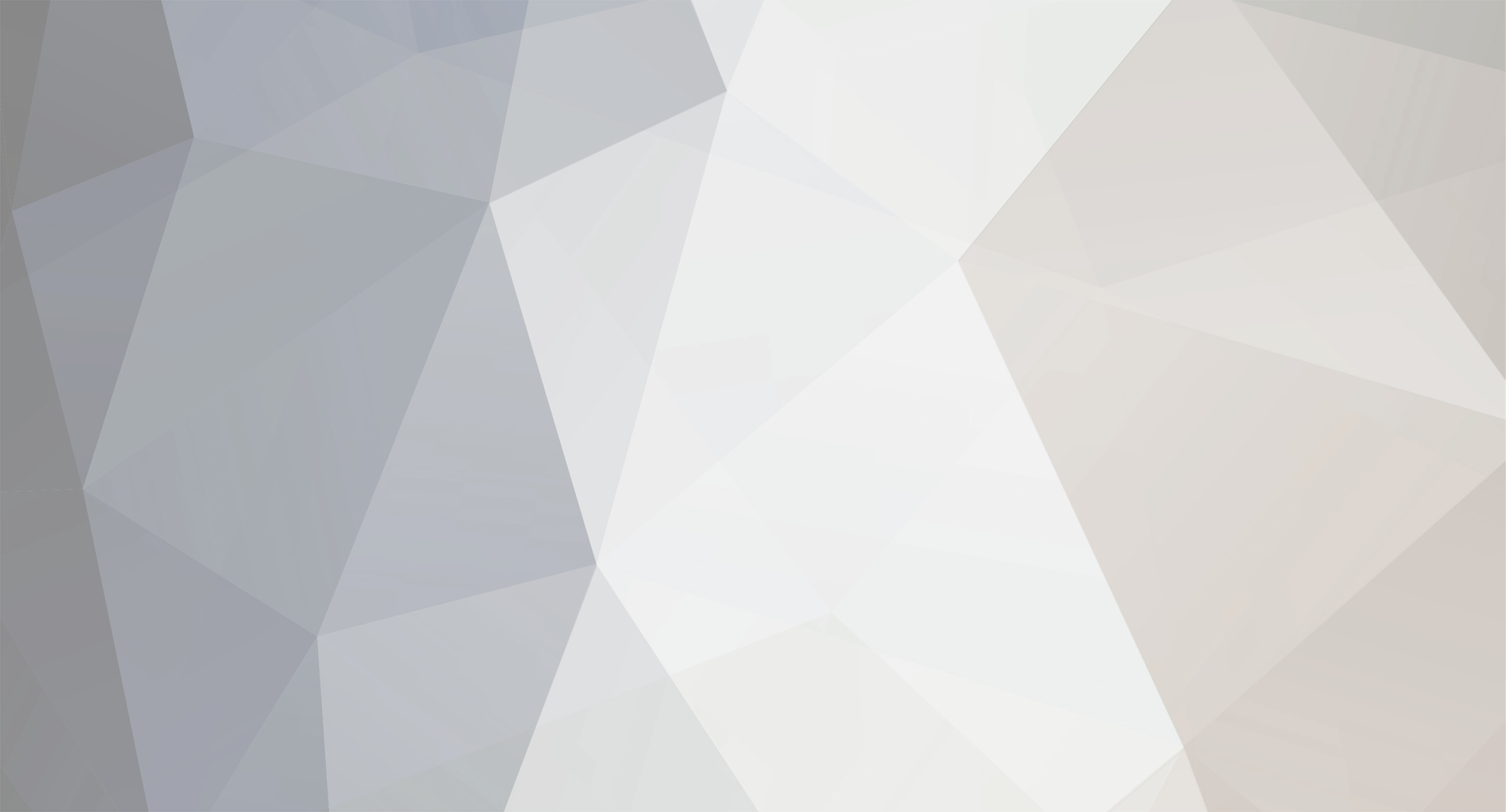
GrahamWh
Members-
Posts
418 -
Joined
-
Last visited
Content Type
Profiles
Forums
Blogs
Gallery
Calendar
Downloads
Everything posted by GrahamWh
-
Magnum 52 FS Speeds Up When The Exhaust Pressure Pipe Is Disconnected.
GrahamWh replied to David Davis's topic in IC Engines
Sounds fantastic David. I look forward to September's account. The four strokes will certainly sound the part more than the 2 strokes and maybe now the permitted size has gone up more people will go that way in the future. -
Unlucky Tim - that's a real shame. I've found that if you put the parts away for a while after a crash then come back to them later it all seems much more mendable than it does on the day.
-
Interesting to see such fine models at this size Timo. Thanks for pointing out the importance of washout on smaller models too - I'll remember that. What kind of pins are you using? I have glass headed ones but the heads are too small really.
-
Thanks Daren
-
Interesting Daren. Any links to the engines?
-
How do you buy your Balsa?
GrahamWh replied to Former Member's topic in Building from Traditional Kits and Plans
Until recently some form a model shop in about 20 minutes away which has a very wide selection, but is not open to the public much, and some from about 5 minutes away which concentrates on railway stuff so doesn't have much balsa to chose from. My latest lot was from Balsa Cabin. It came so well packed and with the different strips carefully held together in individual bunches with masking tape that I am now going to buy most of mine from there. Excellent service. I'll just get little bits from the local model shop. -
Thanks Cymaz. LMA guys would get the retracts working though!
-
Here is how I got the longerons bent at the right position - I cut through the ply doubler ("Don't do that it'll weaken it!" ) and applied ply braces at the relevant points with epoxy again (where the clothes pegs are). I kept these on the inside of the longerons to prevent them showing in the solartex later. I then re-strengthened the ply doubler with a fibregalss cloth strip. Back to the tail parts - I have at last got the main parts sanded. I may try and lighten these as they weigh 127g already. Perhaps some more holes. Edited By GrahamWh on 14/04/2019 17:28:09
-
Having cut out the slots in the ply doublers for the formers, I made a start on the fuselage. The longerons are of spruce, though the plan does not specifically say the lower ones are. It is assumed that they are in the April 2010 Flying Scale Models article so that'll do me. You would like to think that having built the front part of the sides, it would be an easy matter to pull the longerones together at the tail, but no so. The plan calls for a tight bend in the upper one just behind the ply doubler which I supported with an extra ply brace epoxied in place to the left of the dotted line below. The top view also calls of a tight sideways bend in all the longerons at the dotted line. More of that in a mo. Anyway, the two sides came together at the front around the formers without much trouble. The fuse. was set upright next to get the sideways bend in the formers done with clamps etc whilst keeping the centre line correct above the plan along the length of the fuse..
-
Building Brian Taylors Cessna 120
GrahamWh replied to Dwain Dibley.'s topic in Build Blogs and Kit Reviews
Great choice of pilot Dwain! -
Thanks again gentlemen. I will think more about a new Tx Paul. I guess the pots do also wear out after some years and maybe a new one would be a good idea soon-ish. Thanks Peter for the info re Polymorph. I'll fibreglassing the aerial this time as that's the material I have ready to hand. Even before it broke, the supplied aerial was not very good - it was too floppy and would flop to the horizontal position so it pointed at the model after a couple of year's use degrading the signal pattern the Rx would have received. Some tape even at that stage would have been an improvement, but something more long lasting like polymorph or fibreglass would be more reliable. Thanks for the reassurance re the 700 mAh packs Denis and Andrew. While I wait for a battery I can get into the battery box I'll put a bit of duct tape over the wire on the back of the Tx from the existing external battery to the battery box to eliminate any chance of it catching something. I have noticed on friend's Dx6is that some have had to put a bit of tape onto the battery box cover to stop it falling off as they seem to get loose. I expect that could lead to the dry cells simply falling out if the Tx is knocked in use. Nigel I think I will delay chucking the Rx and keep it for a lightweight electric model that will not be able to fly the distance to our boundary fence if the signal is lost to test it over time, thank you. Edited By GrahamWh on 10/04/2019 17:48:55
-
I must admit I think my Tx is now safer than a new set with dry cells and those contacts. The aerial will be done with fibreglass which will be fine, Does anyone have any idea if 700mAh would be sufficient for a battery - if so I could put one inside the battery box where the dry cells originally fitted rather than have this larger one fitted outside? Edited By GrahamWh on 10/04/2019 06:54:29
-
I can get a 700mAh LiFe battery that would fit inside the battery box - would that be sufficient capacity do you think? It would avoid the need for the wire outside the case to the existing LiFe battery. A new TX is not an option financially at the moment. As mentioned earlier, I will get the aerial fixed in a better way.
-
Posted by Capt Kremen on 09/04/2019 17:20:17: IF it's just the (weak) plastic 'axle' pin that's broken, (as mine has done a few times!), then it's a simple matter to insert a suitable size diameter dowel/wire. Then, 'Robert's Your Uncle', no need to shell out circa £15-00 for a pretty plastic bagged replacement. Yes I did this fix about 3 years ago - there was further damage later unfortunately! Thanks though.
-
Posted by Simon Chaddock on 09/04/2019 14:43:25: A point about the reliability of wires connecting a battery pack to the Tx. Its not the solder joint that is likely to fail but the strands next to the joint from fatigue unless considerable care is taken to ensure that the individual strands cannot move using some form of strain relief. Even then it is important that any bending of the complete wire is not concentrated to a small area close to the joint. The drawn copper wire as used in multi strand flex is significantly work hardened so is surprisingly susceptible to fatigue failure. This is a good point Simon. I've addressed the issue in my battery box with the use of hot glue to hold the wires still between the servo connector and the solder point - more visible in the second picture of my first post than the first one. The only exposed part of this wire after the battery box lid is replaced is about 5cm long and should not flex about much: Edited By GrahamWh on 09/04/2019 18:56:17