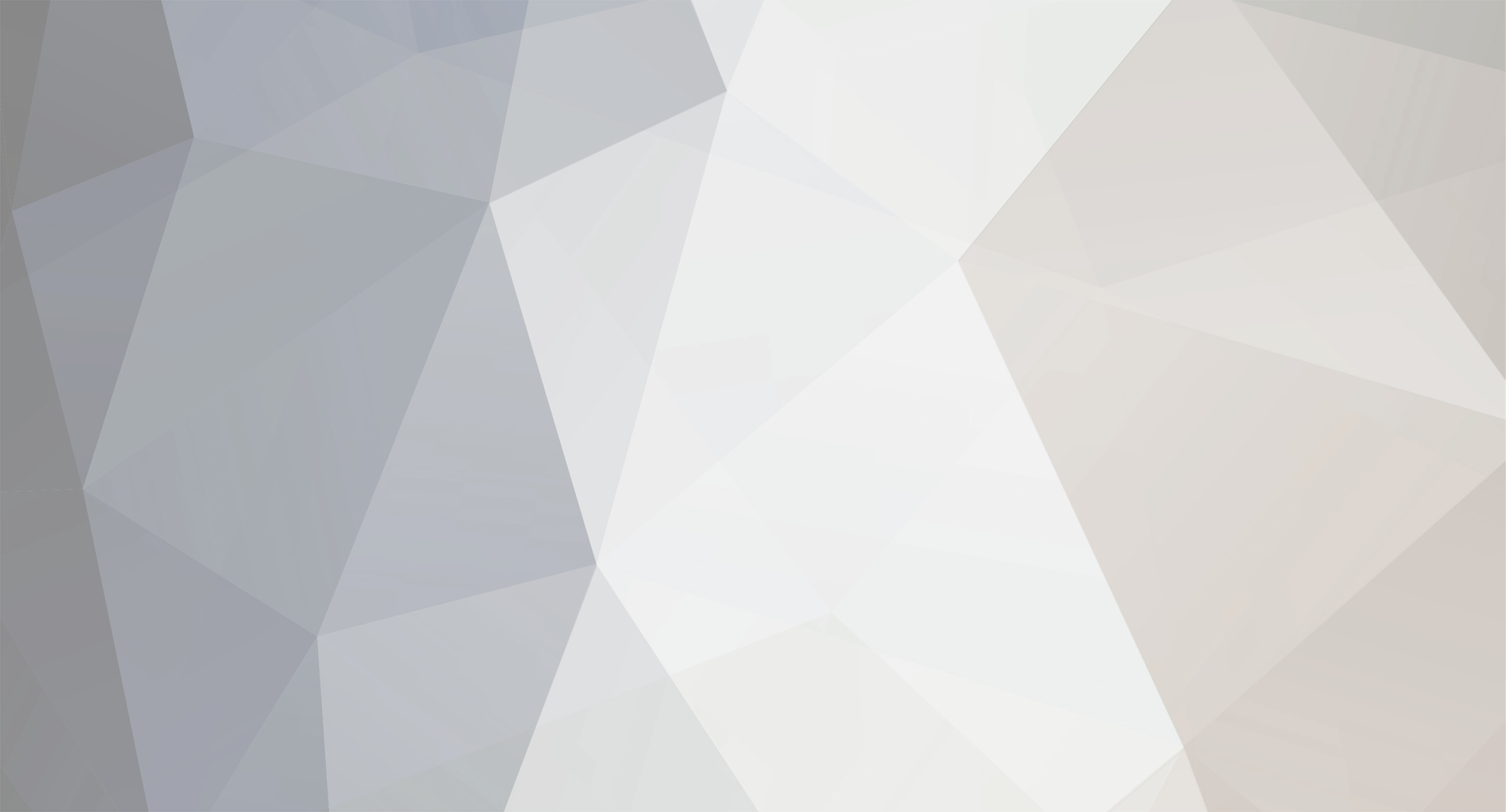
Focae
Members-
Posts
45 -
Joined
-
Last visited
Content Type
Profiles
Forums
Blogs
Gallery
Calendar
Downloads
Everything posted by Focae
-
This one: www.facebook.com/Scramblemagazine/posts/rare-hawker-hunter-from-brazil-arrives-in-the-united-kingdomhawker-hunter-aviati/2389912957701891/
-
Hunter?
-
and I have been reading much more and coming to the conclusion that I may have to eat humble pie and come round to your way of thinking....
-
Aren’t theoretical discussion here fun.....I for one usually end up saying things then reading them back, thinking that’s not what I meant..... Mike, you are right, I shouldn’t be quoting Kirchoff’s law in this case. I can also see that there are varying theories on how brushless motors work. My thoughts are that they are essentially brushless ac synchronous motors supplied by a sine wave like output from mosfet circuitry in an esc. The esc output is pwm square wave but the inductance of the motor windings make the signal more sinusoidal (not a perfect sine wave). The speed of rotation is controlled by the frequency of the rotating field. The pwm voltage controls the torque as speed increases with the current being limited by the back emf. I stand to be corrected with all of this of course. Here is a link showing oscilloscope waveforms. https://youtu.be/Jdhgi5_kmvk
-
You are on the right track Dave except where you say that the current in one phase can be three times the input. Kirchoff’s First Law says that all the currents leaving a circuit must equal the currents entering it. As there is only one input supply, the battery, no current in one leg can ever exceed the battery supply current. You are right that the calculations in a three phase inductive ac circuit aren’t simple and for our motors are further complicated because we aren’t using a true sine wave. It is easier to accept that the manufacturer of most low cost esc’s have already determined the wire size for you. There is little point on substantially increasing the wire size that they have already soldered on for you.
-
Sorry Mike but you have a been grossly misinformed about how brushless motors and esc’s work. This is really getting beyond the scope of the OP’s question but here we go anyway..... Brushless motors as used in rc are 3 phase ac motors with the windings 120 degrees apart and connected in ‘star’ configuration. The 3 phase ac power is created by the esc which converts the dc battery input into a sine wave like output by pulse width modulation (pwm)using mosfets. The speed of the motor is controlled by varying the pwm ouput frequency. The output voltage (and ultimately current) is controoled by the width of the pulses. The higher the frequency, the faster the motor turns. Although the pwm output is created by switching the dc on and off, the output becomes more like a sine wave due to the inherent time delays in the esc circuitry and because of the motor’s inductance. The capactitors on the esc input are there to smooth the ripple that is created in the supply dc due to the switching of the output. They do not provide any additional ‘kick’ to the output. They protect the esc from self induced spikes. You are correct about motor multiple strands but you misunderstood what I was trying to say as I didn’t explain very well.....typically, an esc’s output wires will be thicker than the wires at the motor it is being connected to. To get back to the OP’s question, the current on any one of the output wires will be less than the total current if measured at the dc input. A good guide to wire size is to use the same as the wires that exit the output of the esc to the motor.
-
Posted by Mike Blandford on 09/09/2018 00:19:22: Posted by Focae on 08/09/2018 09:41:05: The output wiring from the ESC to the motor does not have to be the same wire size as the input wiring from the battery. The input wires have the continuous current.....the output wires have a switched load so the current is less. . . . I'm not sure I agree with this! Suppose that at full throttle you have 30A in the input wiring. Now you have 3 wires going to the motor, let us call then A, B and C. For a third of the time you have 30A going out on A and in on B, the next third of the time you have 30A out on B and in on C and the last third of the time you have 30A out on C and in on A. Yes, the average current in each wire is less, but the current, when it does flow is the same as in the input wiring. Now suppose you reduce the throttle to have only 15A in the input wiring. The ESC has done this by only driving the output for part of the time. I think you will find you actually have 30A out on A and 30A in on B, but for only half of the first third of the time, and similarly for the other 2 thirds of the time. So the output wires are actually carrying more current than the input wires! Mike Mike, the output current can never exceed input current. A certain gentleman named Kirchoff determined that in one of his Electrical Laws. ‘The sum of the output currents must equal the input current’. You will also never have the same current in two legs of the motor wiring. Outrunner motors are essentially three phase ac motors. The rotating field is created my rapidly switching dc to the legs in turn. The voltage and therefore current in these legs will never be instantly at the dc voltage because the motor windings, being inductors will cause the voltage to rise relatively slowly creating a sinusoidal wave in each leg. Because the windings are 120 degrees apart, you never have all of the current in one leg being opposed by an equal and opposite current in another and you can never have all of the current flowing in one leg. Also consider this, how thick are the wires that form the winding? They are essentially just a continuation of the wires that connect them to the esc. If you did have all off the current flowing in one leg for longer than the ‘average’ switched time, the smoke escapes, usually at the winding because it is thinner than its supply wires.
-
The output wiring from the ESC to the motor does not have to be the same wire size as the input wiring from the battery. The input wires have the continuous current.....the output wires have a switched load so the current is less. I have never had any problems using anything more than 16awg with a 40A ESC. Thinner cable is much easier to route to the motor and weighs less.
-
I use a 12x6 APC with my Irvine 53 on my Mk3 WOT4
-
I am so impressed I may have to get another....one for coarse, one for fine
-
Suction port on mine is excellent....no dust at all when connected to vacuum
-
I started this hobby in the modern era of lipo batteries, brushless motors and foam artf’s. I was a diehard leccy flier until I bought a balsa model with a two stroke ic engine at a bargain price. I was hooked in an instant! The balsa model is far more satisfying to fly in any wind and for all the problems with mess and starting etc that have already been voiced in other posts, I prefer that to the one big disadvantage of electric flight.....battery management. I still like my electric models but charging up a set of batteries, or worse, discharging unused ones is very time consuming. Added to that, the cost of anything larger than the ubiquitous 3S 2200mAH lipo is a game changer for me. I don’t see ic dying just yet.
-
The anode is positively charged. The cathode is negatively charged. In electron terms, electrons flow from the cathode to the anode. (Negative to positive). The problem is, when electricity was discovered, they thought that the current flow was the other way round, from positive to negative. Unless you are a scientist or electronics geek, we lesser mortals always talk in terms of 'conventional' current flow - positive to negative (anode to cathode). It really is just one of those things that as a young electrician, we had to accept and not over think.
-
Anode is positive Cathode is negative
-
Also, forget lead free solder....it really doesn't make good joints. It is getting harder to find but the best is rosin cored 60/40 solder (60% Lead, 40% tin). I know that the health and safety conscious will shudder at the thought of using lead but I am afraid lead is what makes solder bond to the wire. For heavy duty wires, 80 Watts is good. I can manage with 50W but the wire wants to suck all the heat out of the iron so it is much harder to avoid dry joints.
-
Posted by Stevo on 17/09/2017 14:58:23: Sunday relaxation beckons. Final sealing.. Seal up any gaps, it shows white here as it's acrylic sealer, but dries transparent. Don't squirt too much on, and use a coffee stirrer to form the slight radius in the corner. Also pay attention to the engine bay; mine had a hole in it where the push rod for the (not used) steerable nose leg was! Wipe off any surplus but don't use thinner, you will wipe off the print What is the trade name for ‘acrylic sealer’.......I’ve not come across it before?
-
Posted by Peter Miller on 13/09/2017 19:48:55: Your local office supply shop or EBay which is cheaper Thanks Peter, the shortest I can see on eBay or Amazon is 11mm which I guess will do just fine. In wildest Cornwall on holiday so I will look at a stationers when I get home.
-
Posted by Peter Miller on 18/01/2017 12:10:50: As I keep telling people but no one ever seems to listen The secret is MAP PINS. Small, plastic headed pins about 6 mm long, You can push them home and they hold the plank down. Where do you get 6mm map pins Peter? I can only seem to find 12mm pins.
-
Aileron servo for non ARTF Acrowot
Focae replied to Focae's topic in Building from Traditional Kits and Plans
Thanks for your responses.....I am cutting the torque rods as I figured it would be easier to install the pair of servos rather than trying to mess around with the torque rods, but I take your point. I will ponder.... -
I am renewing the covering on my balsa Acrowot. It has a single servo with torque rods. I will be removing the ailerons to make the covering easier and replacing the single servo with dual servos. (I will have to cut the torque rods so I figure this will be easier). I have three pairs in my box of spares to choose from... HS80MG, HS81MG and HS82MG. Which of these would be most suitable or should I put std size servos in? Edited By Focae on 22/08/2017 12:50:09
-
If Patmc's instructions don't work.....close throttle with tx switched on, connect model battery and wait for the esc to settle into its constant beeping, then trim throttle fully back using trim button on tx and it should then initialise properly. Once you have got it to initialise, then disconnect model battery, reset tx throttle trim to neutral, turn tx off then back on and then follow Patmc's instructions. As others have said, it's almost certainly a throttle range issue.
-
Where JST connectors are used on LIPO's, the wires used are usually quite thin too and probably have a similar current rating to the connectors.
-
Re-covering an Acrowot kit
Focae replied to Focae's topic in Building from Traditional Kits and Plans
Thanks guys....all good info. I guess I will just have to get stuck in. My main concern was the control surfaces and the problems associated with renewing the CA hinges... One of the hinges can be moved along a bit. The others may be a bit more problematical. -
Re-covering an Acrowot kit
Focae replied to Focae's topic in Building from Traditional Kits and Plans
I'm doing the whole fuselage but don't need to do the wings. I stripped the fuselage completely as it had a bit of hangar rash that needed sorting while I was at it. I will try and get help for my first attempts. -
Re-covering an Acrowot kit
Focae replied to Focae's topic in Building from Traditional Kits and Plans
Thanks John.....I took it to the LMS and they said it looked like Solarfilm. This is the kit Acrowot not the ARTF. Any advantages of Profilm over Solarfilm?