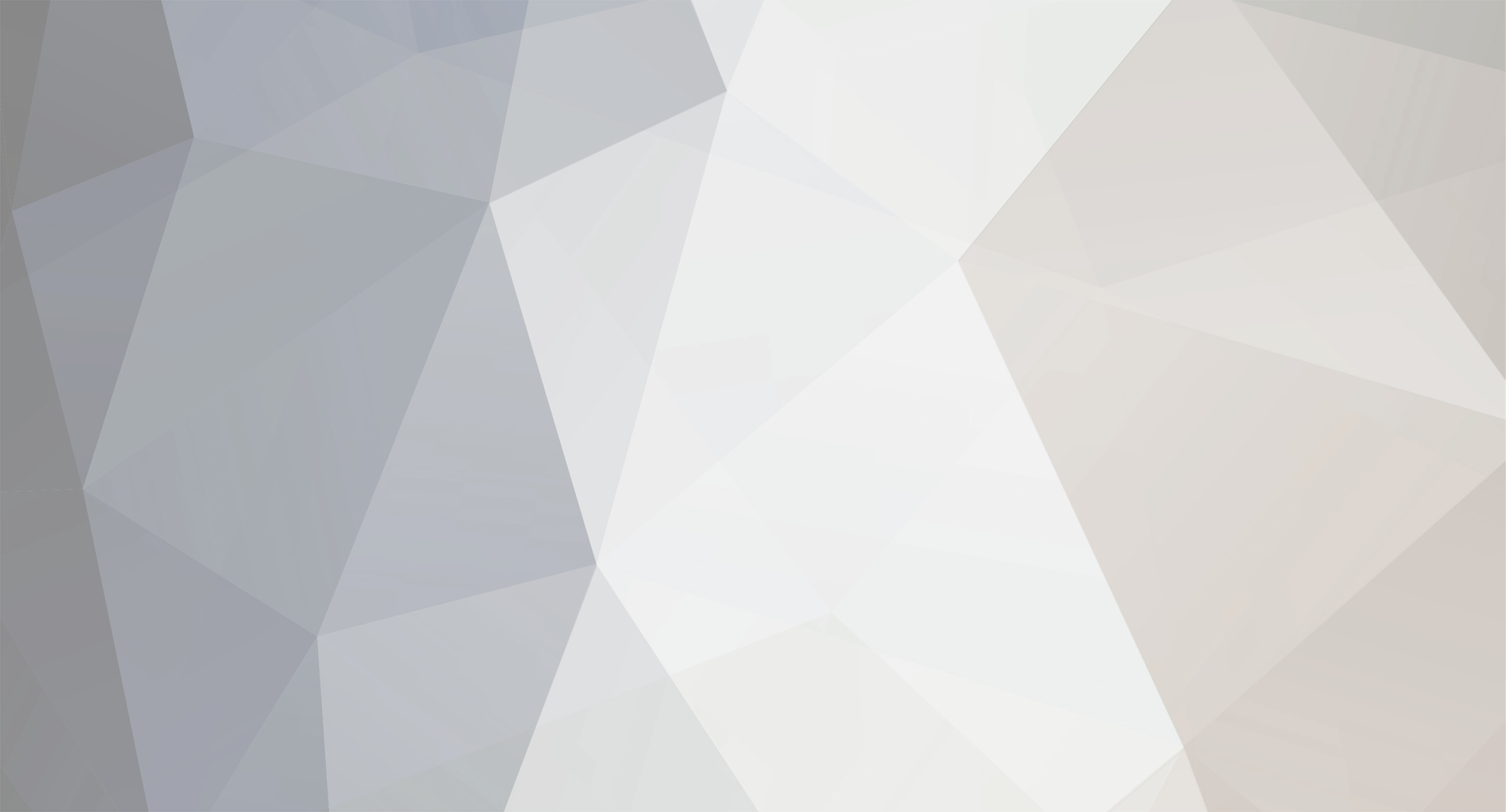
Martin McIntosh
Members-
Posts
5,865 -
Joined
-
Last visited
Content Type
Profiles
Forums
Blogs
Gallery
Calendar
Downloads
Everything posted by Martin McIntosh
-
Shaun, back to your engine mount. If the rear end fits then it is normal for the front to have to be bent out slightly but you should not have to force the motor in such that the front end then splays outwards. If this is so, then get a different mount or relieve the rear end a bit The motor should sit parallel without too much stress on the mount. I normally use No.6 self tappers on a nylon mount, which will require drilling to 3mm. Good idea about the glass tape. 2-3" wide should be about right but ensure that you use epoxy rather than polyester resin cos the latter will disolve the foam underneath unless it is fast setting. Use the minimum possible ammount of resin. If the wing is already covered you will need to remove some covering around the centre.
-
Most of today`s so called trainers seem way overpowered, fly like missiles and are a compromise re dihedral to keep them stable, or lack of to make the ailerons work. It does make a novice fairly competent by the time they reach their A test though. I would recommend something like a Limbo Dancer or a Cougar, with greatly reduced throws, since they are very forgiving and easy to fly, and do not have that silly, weak, noseleg which `trainer` manufacturers insist on fitting. Of course there is always the sensible Super 60?????
-
Shaun, please do not ever try to glue a clevis of any type to a metal rod unless you know a lot about types of adhesive and suitable etching fluids. I would go with the solder bucket adaptor. Most control rods are about 1/16" dia. made of very soft steel and can be Z bent with a strong pair of long nosed pliers. If you wish to solder steel, as I do, use Telux flux from a hardware store-do not rely on flux cored solder for this type of job. It is too important.
-
Try that with a YS!
-
Thanks to your much appreciated help. Used Corel photoshop 1X in the end. Martin.
-
Timbo, I use the TO 220 plastic package because it is a lot cheaper and the 4mm ali lid to the box forms the heatsink.
-
Only just looked at this post - the mere thought of wobbly artfcumdontknowhowtodoitanyotherway plastic snakes just makes me cringe!
-
Having tried many methods including glowsticks which I regard as being under voltage for a 1.5V plug, downright dangerous when they decide to fall off and of low capacity, I now use a home made unit using a LM338K variable regulator which can be switched between 1.25V and 1.45V. I have only needed the 1.25V setting so far, because it is regulated no matter what the load. It requires a minimum input of only 3.6V derived from any old `past it`nicads, even used in parrallel and only two or three other components with a three position switch and can be strung together without the need for a circuit board. Cannot give drawings here, but if any R/Cers want to try it just contact me at [email protected]
-
gliders
Martin McIntosh replied to Former Member's topic in Gliders and Gliding - General Discussion
Wot if one servo fails at full travel? Hold full up/down and hope for the best! -
Scott, you do not have to spend £200 on a camera system. A 10mW 100M range set can be readily bought for £21, and a 200mw, yes, 200! for £28. I have tried the 10mW in a 35mHz set up and it exceeds its stated range but would not care to try either in a 2.4gHz model since even the low power unit would surely swamp the Rx. I totally agree that these should only be used under controlled conditions when no other 2.4 equipment is in use. I do not really foresee people wanting to video every single flight - just occasionally when other fliers should be made aware of the situation.
-
Balance point
Martin McIntosh replied to john corcoran's topic in Building from Traditional Kits and Plans
On low wing models I use a piece of string lightly clamped between the fus. and wing to suspend the model from. Measure from the LE to the string to get each side the same.