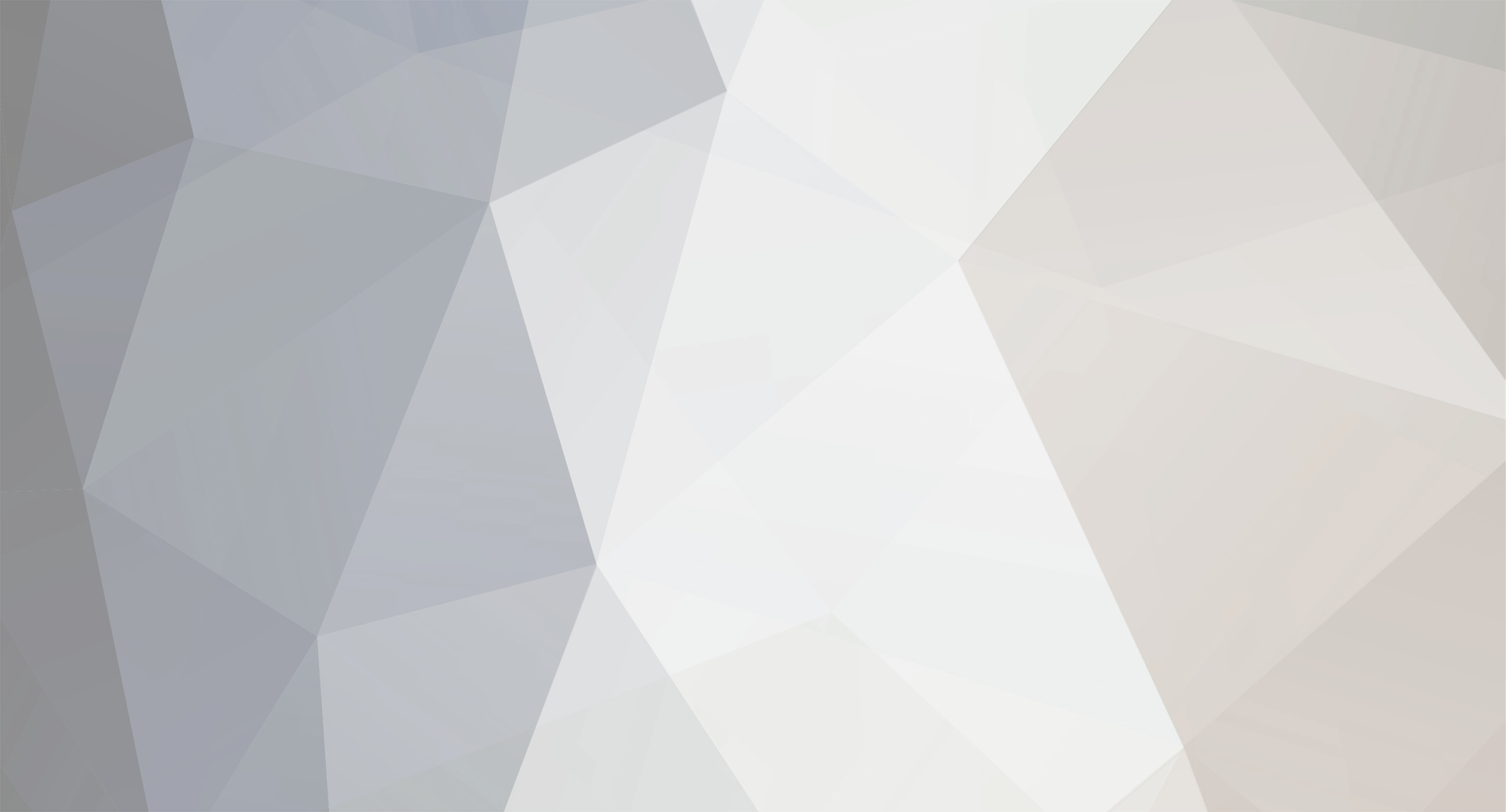
Gordon McConnell
Members-
Posts
185 -
Joined
Content Type
Profiles
Forums
Blogs
Gallery
Calendar
Downloads
Everything posted by Gordon McConnell
-
Warbirds Replicas FW190 - the 2023 version
Gordon McConnell replied to Ron Gray's topic in The 2024 Forum Mass Build
Hi Richard, Please put me on the list for the retracts mod kit. I think I will fly without the retracts initially and then do the mod. Gordon -
Warbirds Replicas Focke-Wulf 190 Build Log
Gordon McConnell replied to Gordon McConnell's topic in The 2024 Forum Mass Build
I eventually removed the bubbled covering on one wing and replaced it. What seems to work is using Balsaloc on the wing skin veneer prior to applying the PVA coated, brown paper. I am also convinced that the Gorilla PVA is not the best for this job and next time I will buy some cheaper PVA from the builders merchants. I have got to the painting stage now and will final fit the flying control surfaces prior to the finishing paint coat. I have used Halfords white primer on the lower surfaces and grey primer on the upper surfaces. -
My vote, if I am allowed one, 😀 would be for a Sea Fury. P47 would be second. Bearcat would be nice but listening to the comments on the twist and turn retracts, maybe not. Getting back to working on the FW190 this week.
-
Warbirds Replicas Focke-Wulf 190 Build Log
Gordon McConnell replied to Gordon McConnell's topic in The 2024 Forum Mass Build
Thanks Richard. I am going to do that as I had a look at it again this morning and it is really a bit of a mess on one wing only. 😀 Away for a couple of weeks so it will have to wait a bit. -
Warbirds Replicas Focke-Wulf 190 Build Log
Gordon McConnell replied to Gordon McConnell's topic in The 2024 Forum Mass Build
I have experimented a bit further with the Gorilla PVA. I thinned it very sparingly with only a couple of drops of water and applied it very liberally to the BP. I did not leave it long before applying to the veneer. This has worked much better with no bubbles. I also have done one wing with applying a thin coat of Balsaloc to the veneer and letting that dry before applying the BP/PVA. That has worked well too. I think as Stu has said there are several variations of the method which can be used. In my case, with no previous experience, I am getting used to the process and the finer details which guarantee success. Having expert advice from those on the Forum is a great help to progress quickly up the learning curve. Thanks. -
Warbirds Replicas Focke-Wulf 190 Build Log
Gordon McConnell replied to Gordon McConnell's topic in The 2024 Forum Mass Build
LiPo Man and Ron. Thanks. Will try the aliphatic glue solution as well. Some of the bubbles are very small and good to know they may not be noticeable. -
Warbirds Replicas Focke-Wulf 190 Build Log
Gordon McConnell replied to Gordon McConnell's topic in The 2024 Forum Mass Build
Thanks Ron. I think you are quite correct on the thinning of the PVA. I tried another panel with hardly any water in the PVA and that worked much better. No bubbles visible. Maybe trying to cover the whole semi span was ambitions. Perhaps I would have found it easier to try to do it in two parts to avoid the adhesive drying out. I will try the repair as you suggest. Lots of bubbles to work on!! Thanks again for your good advice. -
Warbirds Replicas Focke-Wulf 190 Build Log
Gordon McConnell replied to Gordon McConnell's topic in The 2024 Forum Mass Build
Having gained confidence, I then started on the wings. I cut out the paper to do a lower and upper semi-span separately, there was no chordwise joints. I am uncertain whether this was a good idea. I slightly thinned the PVA with water and brushed it onto the brown paper. It seemed to start drying on the paper quite quickly so I hurriedly positioned it on the wing and used my finishing iron to smooth flat. All seemed well at first but after drying overnight, a lot of bubbles appeared. I applied the iron again and they went away but only to return later. I am contemplating try to strip the paper off and start again but I might try to cut the bubbles and stick the paper down again. Any repair tips will be gratefully received!! -
Warbirds Replicas Focke-Wulf 190 Build Log
Gordon McConnell replied to Gordon McConnell's topic in The 2024 Forum Mass Build
Getting a bit impatient to get on with the covering, I started on the fin and tailplane. I have not used brown paper before so I was at the bottom of the learning curve. I watched Ron Gray's video a couple of times before starting. The brown paper is from Amazon and is used as masking for car spraying. I also tried some from Hobbycraft but this seemed to soak up the PVA an wet the other face. The fin and tailplane came our well and gave me confidence to complete the ailerons, elevator and rudder. The PVA I used was Gorilla Wood Glue. -
Warbirds Replicas Focke-Wulf 190 Build Log
Gordon McConnell replied to Gordon McConnell's topic in The 2024 Forum Mass Build
The wing dowel is embedded in a block which was epoxied into a slot cut in the leading edge and then reinforced with the wing bandage and epoxy laminating resin. I think that has worked out well and should be stronger than sinking the dowel into the foam behind the leading edge balsa section. As others have done, the rudder and elevator servos have been mounted on bearers made from scrap ply which are glued to square section balsa supports on the fuselage inside walls. The control rods are made up to length and holes cut in the aft fuselage sides to exit to the elevator and rudder control horns. -
Warbirds Replicas Focke-Wulf 190 Build Log
Gordon McConnell replied to Gordon McConnell's topic in The 2024 Forum Mass Build
Slow progress over the last few weeks. I have completed the wing root fairings and filled and sanded them to shape. Also, I have attached the wing servos on their mounting plates with hardwood blocks and small wood screws. The servo wiring has been run in the slot cut in the lower wing surface. I have filled in the slot with some balsa strip as I think that is structurally more sound than leaving it open. The downside is that I would need to cut into it again if I ever have to replace the wiring. Servo replacement is possible as I have made a plug joint in the servo bay cavity. -
Warbirds Replicas FW190 2023 version - a VLOG of the build
Gordon McConnell replied to Ron Gray's topic in The Video Channel
Ron, Great to see a very successful first flight of your Warbirds FW190. It looks super and it seemed very fast in the flybys and even on landing! I am sure all of us following your build videos are very grateful for the massive effort you put into making these informative videos. Personally, I learned a lot. Thank you for taking the lead and spending so much time of your time on behalf of others. Good luck! -
Excellent Dave. You have set the standard!! 😀
-
Warbirds Replicas Focke-Wulf 190 Build Log
Gordon McConnell replied to Gordon McConnell's topic in The 2024 Forum Mass Build
Ron, I do have a floor board saw somewhere but I was too lazy to go and find it!! -
Warbirds Replicas Focke-Wulf 190 Build Log
Gordon McConnell replied to Gordon McConnell's topic in The 2024 Forum Mass Build
Next job was one I was looking forward to completing. After marking out the position of the servo boxes, I carefully cut the veneer and pealed it off to expose the foam. Ron Gray posted a great tip to remove the foam which is difficult to dig out with a knife. Ron uses an electric soldering gun with a loop of piano wire as a tip. I tried this for the first time and it was so easy! Melting out the slot for the servo cable was just one pass with the wire tip. Well worth the investment in a cheap soldering gun as I have a Warbirds Hurricane with a similar foam wing to build next. 😀 Thanks Ron. I bonded in the ply servo box and frame with Gorilla glue. -
Warbirds Replicas Focke-Wulf 190 Build Log
Gordon McConnell replied to Gordon McConnell's topic in The 2024 Forum Mass Build
I sanded the wing LE and tip to shape. Its probably the job I dislike the most but the result is always satisfying in the end! The wing tips are always the most difficult but it is a case of taking ones time and removing small amounts with checks all the time on the shape. I use a razor plane initially and then a Permagrit block followed by fine grade sandpaper. -
Looking good Dave. I am going try spray painting with a spray gun for large areas and an airbrush for detail. Not near that point yet!
-
Warbirds Replicas Focke-Wulf 190 Build Log
Gordon McConnell replied to Gordon McConnell's topic in The 2024 Forum Mass Build
I decided to start the wing build as I will need the assembled wing to attach to the fuselage to be able to install the wing root fairing. Anyhow, a change is as good as a rest from the fuselage! I bonded on the LE balsa strip, the wing tip block and the aileron cut out facing and held them in place with masking tape. I used Gorilla Brown adhesive as it is friendly with foam. I was bit generous with the adhesive as the foam was not so smooth from my cutting efforts. This adhesive foams on contact with moisture during cure so it fills any voids in the bond line. It also oozes out of the joint! You can see the result. Fortunately, it come of easily with a knife and sands down smooth. Moral of the story: a little goes a long way! -
Warbirds Replicas Focke-Wulf 190 Build Log
Gordon McConnell replied to Gordon McConnell's topic in The 2024 Forum Mass Build
Some other little job. As others have done, I added some scrap balsa support to the cockpit sides where they splay out to join F2. Like wise, I also added a balsa top deck over the aft of the cockpit area to better support the cockpit side panels. I think this was faired in on the original aircraft. I will add a pilot and instrument panel later before finishing the model. -
Warbirds Replicas Focke-Wulf 190 Build Log
Gordon McConnell replied to Gordon McConnell's topic in The 2024 Forum Mass Build
That was when I realised that I had made a mistake in trimming the ABS battery access cover at the front end. It should come right up to the forward cowling aft edge with no gap. Guess who cut it back to the rear face of F1? You can see that I glued in a little strip of plasticard on top of F1 to fill the gap. I have trimmed the top gun cover moulding to fit but I am going to leave it until later to glue it in place. -
Warbirds Replicas Focke-Wulf 190 Build Log
Gordon McConnell replied to Gordon McConnell's topic in The 2024 Forum Mass Build
After a bit of trial fit and trimming, I glued the aft cowl ply onto the stringers and bottom plate. I held it all together with elastic bands and clips until it was set. I used PVA wood glue. When it was dry, I trial fitted the nose cowl. The wrap around ply on the aft cowl needed to be trimmed back flush with the forward face of F1. When that was done, the front cowl was a good fit to the aft cowl with almost perfect alignment. -
Warbirds Replicas Focke-Wulf 190 Build Log
Gordon McConnell replied to Gordon McConnell's topic in The 2024 Forum Mass Build
I checked the battery fitting inside the cowling. I may use an Overlander 4S 3900mAh battery and this just fitted and allowed the hatch to be closed.