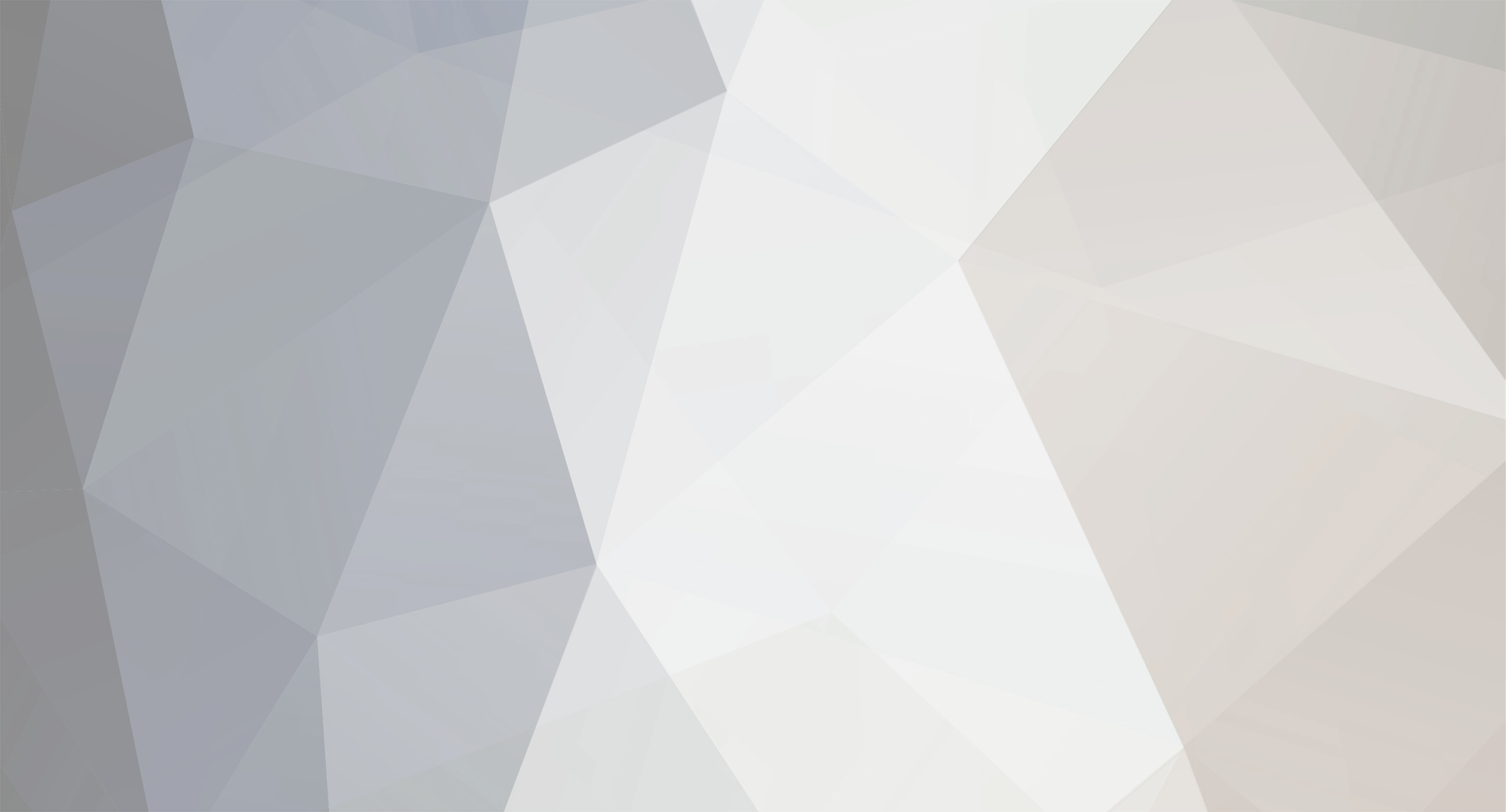
Martin Roberts
Members-
Posts
88 -
Joined
-
Last visited
Content Type
Profiles
Forums
Blogs
Gallery
Calendar
Downloads
Everything posted by Martin Roberts
-
Piper Twin Apache PA23 -150 74"
Martin Roberts replied to Danny Fenton's topic in Own Design Project Blogs
Hi Danny, I am back after a few years away, looking real good, never mind the windows, just take a deep breath...no, not whilst you are mixing the resin!!!!! -
Piper Twin Apache PA23 -150 74"
Martin Roberts replied to Danny Fenton's topic in Own Design Project Blogs
Hi Danny and Ton, hoping you guys have had a great Christmas - and great to see you back on line, if you look at the pivot point pics on page 19, and the comments I posted then... "As far as my tuppence goes, I probably would have designed the 'hinge' as 'a single rod running through the aileron with a z bend to (the appropriate center point that you calculated) a bearing fixed into a cleat each end, a cleat similar to a control horn soldered midway to the rod would be located to a bearing soldered onto a rod located similar to the detail in the photo (above) for the flap ... ok so the detail would not be perfect but far simpler to model and the same outcome as your design and the rod passing through the aileron would stop any warping of the aileron.." This would allow for the aileron to be fitted up after skins, additionally there is in the same group of pics, a view of the wing/fus intersect (top angled view) which shows the flap pushrod attachment...., maybe I should draw a detail of my interpretation and send same to you Danny for your thoughts Marty -
Piper Twin Apache PA23 -150 74"
Martin Roberts replied to Danny Fenton's topic in Own Design Project Blogs
Hi Danny, Ton and everyone reading his thread Merry Christmas and a Happy New Year to you all from Marty Down Under -
Piper Twin Apache PA23 -150 74"
Martin Roberts replied to Danny Fenton's topic in Own Design Project Blogs
Hi Danny, if you import those sections into Turbo and use the offset command at 4 mm, select the line then click inside the line, you will have the cut out (4 mm = 2mm for the outer skin of the fus + 2 mm for the inner (false) skin so that the window cut outs can lie on top) no need to CNC these parts, and if the profiles are cut from 2 mm balsa or ply, the space would have to be 18 mm, 18 + 2 = 20, this is because the 'surfaces' Ton is cutting have no 'thickness' as such just like a piece of tracing paper - Marty -
Piper Twin Apache PA23 -150 74"
Martin Roberts replied to Danny Fenton's topic in Own Design Project Blogs
Danny, at 20 mm this would be 300 mm, you forgot the starter with zero thickness plus 15 x 20mm. I have made that mistake many years ago cutting material for balustrades LOL, oh well at least I can weld steel back together - harder in hardwood - Marty -
Piper Twin Apache PA23 -150 74"
Martin Roberts replied to Danny Fenton's topic in Own Design Project Blogs
Hi Dan and Ton, yes you guys are on the right track, nice idea to go with the foam if you were making a fiberglass mould, unless you are skinning the foam with ply/balsa? Either way, I obviously explained well enough for you two to be on the right track... Hopefully Ton has cut the sections to the inside of the fuselage and then take off thickness of balsa or ply skin so that when the window panels are laid on this 'inner skin' the plastic will form up to the inside of the real fuselage. Personally I would be use either 0.3 or 0.5 PETG, at 0.5 thickness the windows would be very rigid but still light, don't forget to trim the ply/balsa windows by 1.5 times the thickness of the PETG all round so that the radius of the PETG (after the forming) has enough room to sit nicely inside the 'frame'...Just thinking ahead Danny, Have we allowed enough on the window cut outs to 'feather' the fiberglass skin into the window openings for a smooth finish and still have room enough ? Marty -
Piper Twin Apache PA23 -150 74"
Martin Roberts replied to Danny Fenton's topic in Own Design Project Blogs
Hi Danny and Ton, I almost bought Rhino myself some time ago, a lot cheaper than AutoCAD, but at the time I had several versions of AutoCAD, Turbo Cad, ArchiCad, blah blah under my belt, then I changed jobs from building design to working for Council, had to learn 13 new software packages that year and to be honest I couldn't at that time see the benefit of yet another Cad learn - maybe I will have to remedy that - looks like I might have to down load the trial version..... Anyway, onwards and upwards Danny, keep up the good work and remember Santa is on his way hey hey ... Marty -
Piper Twin Apache PA23 -150 74"
Martin Roberts replied to Danny Fenton's topic in Own Design Project Blogs
Hey Ton, what is that software you're using? Marty -
Piper Twin Apache PA23 -150 74"
Martin Roberts replied to Danny Fenton's topic in Own Design Project Blogs
Hi Danny, no postcard - message in a bottle LOL, for thought and planning..... you need to make the side ribs for the cabin less 2 mm, form up an new side frame and layup the new 2mm dummy skin, which is now (outside) a plug matching the inside of the cabin wall, I am sure that Ton can send an alignment template for the cut out sections of window less say 0.5 mm all round and cut the window panels in 1.5 mm sheet then fix onto the plug using the template, now when you vac the new window 0.3mm clear or black, it will fit almost flush minus say 0.2 mm inside the outer skin, I am sure Ton could model that up in about 3 minutes including the strong ply stringers top bottom and middle (nice and strong for the Vac as is the 2 mm dummy skin, Marty -
Piper Twin Apache PA23 -150 74"
Martin Roberts replied to Danny Fenton's topic in Own Design Project Blogs
Danny & Ton, could always sand down a block of hard balsa for the tip - na! - just kidding, unfortunately being down here we don't get the freebies, or I would have subscribed when the building jig was up for grabs..... I do admire your sense of art - the colour scheme you so patiently applied when clamping the fuz was to say the least impeccable LOL, mine are big black so-and-so's... Didn't you use a stringer behind the side panel join, or did you misalign the bottom panels to the stringer? Could be a good detail or notation to utilize for the final plan. I also like using 2 mm, as it is firmer to work with and still sands back to about 1.6 finish if you're not too harsh, so there is still enough meet for the glass to hang on without going concave between the bulkheads.... now outside to bash some Australian Hardwood into shape on my deck or I won't live til Xmas.....Marty Edited By Pete B - Moderator on 19/12/2013 09:55:52 -
Piper Twin Apache PA23 -150 74"
Martin Roberts replied to Danny Fenton's topic in Own Design Project Blogs
Hi Danny, you are getting close - how about a few 'exploded' shots, showing the 'whole model' as is so we can all see exactly where you are at - doesn't need to be pretty, I'd send you a few more clamps - but Santa might beat me there - just remember it is not a case of not having enough anything else - it's a case of not having enough space to store all the stuff and still have enough space to work. My double car garage is full to the eye balls LOL Marty -
Piper Twin Apache PA23 -150 74"
Martin Roberts replied to Danny Fenton's topic in Own Design Project Blogs
Hi Danny, firstly a big thank you to Nick for the information, another point for the ailerons being so 'awkwardly' hinged is that although this aircraft had a 'never exceed speed of 240 knots', that is still quite fast. I am not sure at what speed control surface buffeting cuts in but having the pivot point so far back would probably offset any induced buffeting by way of counter balance (amount of aileron in front of the pivot point) also counter by a balance of the air pressure on the forward area of the surface...now readers please don't mistake what I am saying here for the sort of buffeting from a higher performance military craft, this aircraft was an at the time high performance civilian commuter, so any buffeting from the ailerons that could cause discomfort to a passenger would have been designed out, especially when the other benefits as identified by Nick also come into play, of course the last part which would have been carefully considered by the designer is that the force needed to be exerted on the control surface by the pilot is also further reduced by the balance of air pressure on the surface which would make it more comfortable for the pilot as well. As far as my tuppence goes, I probably would have designed the 'hinge' as 'a single rod running through the aileron with a z bend to (the appropriate center point that you calculated) a bearing fixed into a cleat each end, a cleat similar to a control horn soldered midway to the rod would be located to a bearing soldered onto a rod located similar to the detail in the photo (above) for the flap ... ok so the detail would not be perfect but far simpler to model and the same outcome as your design and the rod passing through the aileron would stop any warping of the aileron.. Back to you Danny Marty -
Piper Twin Apache PA23 -150 74"
Martin Roberts replied to Danny Fenton's topic in Own Design Project Blogs
Hi Danny and Ton, just regarding a second prototype and the question of a removable one piece wing. I agree that it is a fair amount of re-work and basically a completely new centre of fus and wing sections to be designed and constructed, however as has been stated by Chris Bott, the fuselage of this aircraft is large to say the least so one has to really consider whether this will be a model to construct if the wing centre is to remain fixed in situ.... The upside is that the model is more structurally sound in its present design with the removable outboard sections, as well as the easy repair of a wing tip, the downside is the fiddling with the two connections and locking the tips on. The upside of a one piece wing of course is the simple connection of wiring, ample space for fiddling with servo's (elevator and rudder), and far easier repairs if a wing is damaged in a major way, and of course the storage and the transport, the downside is very small, and would also allow for easier conversion to a fuelled version and even the addition of air retracts - there is of course ample room for this within the fus.... More modellers would, in my opinion, decide to go forth and join the Piper Clan with a removable wing. WWII twins would really benefit from Tons design, as they generally get thrown flown around with a lot more aggression, now I have to start rejigging the Canberra I started drawning...LOL Marty -
Piper Twin Apache PA23 -150 74"
Martin Roberts replied to Danny Fenton's topic in Own Design Project Blogs
Hi Ton and Danny, I am just thinking to self (and you as well), I do like Heritage color schemes, so how about this one - of course I would have to carefully consider accuracy when it comes to the flag And someone will obviously want to do this scheme - including the fourth wheel for Carrier training on the tarmac LOL Marty -
Piper Twin Apache PA23 -150 74"
Martin Roberts replied to Danny Fenton's topic in Own Design Project Blogs
Hi Danny, oops again, you are absolutely correct, I got myself muddled on the naming - yes the AZTEC was the later version or child in the family tree.... we all make mistakes sometimes ... maybe I should have read the instructions LOL...By the way in another family tree...on my wife's side they are all Piper's and one just has to get one's head around the names vs dates for that lot too Marty -
Piper Twin Apache PA23 -150 74"
Martin Roberts replied to Danny Fenton's topic in Own Design Project Blogs
Hey Danny, even if it is not 'published' by RCME I am sure that there are plenty of people here that would by the plan from you... there is one thing though, the aircraft you are working on is (I am totally sure) an AZTEC, the APACHE was the later version with all the bugs sorted and introduced gradually all the sharper edges such as the fin/rudder, redesigned the nacelles and the nose etc.... Your thoughts? Marty - dinner is a calling -
Piper Twin Apache PA23 -150 74"
Martin Roberts replied to Danny Fenton's topic in Own Design Project Blogs
Hi Danny, just sittin back havin a nice day off for my birthday, thought I would check out the build..... I must say that you and Ton are doing a remarkable job. This looks better than most kits. When you finish, I definitely want a copy of the plans, I would by a kit but it costs a lot to ship to OZ..... also the detail you are capturing in the build pics is fantastic. I wonder if Santa will use it to deliver his presents this year, you are of course still thinking of red and white scheme I hope Kind regards Marty -
Hi Tim, just taking the day of for my birthday - life's hard some times... I just found this build - looking good, at the moment I have to much to do and no time to build, but this would be a nice little project when I finish the back fence/the deck/the laundry/the wife's car/my car/my son's car/the other son's car, oh yes and the full time job at work LOL... keep up the good photo's Marty down under
-
Piper Twin Apache PA23 -150 74"
Martin Roberts replied to Danny Fenton's topic in Own Design Project Blogs
Hi Danny, great job, now I got the bug - I read you had some problems with the wing seat under belly area and found a nice flying photo - will try and upload it for you Marty - Down under - of course -
One thing that most people forget is that the COG is a theoretical point of aerodynamic balance for the design of the aircraft...some aircraft are designed to be dynamically unstable (stunt and fighters), some dynamically stable transport and civilian - Cessna's etc.), some (mostly the powered variety) are a little bit tail heavy flying with a high angle of attack (AOA) to create lift... great while you have a running engine, whilst most gliders are nosey with a low AOA to induce speed to create lift. This just means that the COG (bad terminology) should be just about the centre of lift (COL)- calculate all you want but if you don't know where the COL is then it's just trial and error until the aircraft flies the way the designer wants. As a typical ARTF goes the Park Zone Radian COG is far more forward than it could be, so the tail plane is angled down to generate nose up, this combined with speed increase causes the AOA to increase and generate the lift, generate more drag, followed by a theoretical stall - nose down - more speed - nose up - stall (porpoising) add a motor with down thrust to overcome the drag, reduce the stall. You can modify the radian move the COG back flatten the tail reduce the drag which increases the speed creating better lift etc... Vanessa allows you to adjust the harness until correct AOA is achieved, then if the tailplane is level (if the design is correct) the COG and the COL should be about the same place. Happy flying Marty
-
Hi Andrew, the COG as you know is usually located, dependant on the aircraft design air-foil, angle of attack (incidence) etc..., at about 30% of the wing chord. The tow hook provides a new centre of rotation (fulcrum), so if you move the tow hook behind the COG you lose all control with a resultant loss of aircraft - life- other OOOOPs. This is because the plane wants to go nose down but because the tow line is in the way the plane wants roll or yaw for the heavier than normal nose to get below the line, if you are lucky the plane starts to spin and the hook releases before you crash - a flat spin to ground is better than being dragged wing in to ground - you can imagine what happens next. The place I find best is about 1/2 way between the leading edge and COG so that the wing rotates naturally to a positive angle of attack causing the plane to climb without elevator. Too far forward - too much rotation and collapse the wings, not forward enough and you need to use up elevator and start introducing more drag which slows the acceleration and therefore the climb potential. If you make the tow hook adjustable, you can start with it further forward (say 1/3 from the wing tip to COG) and move it back incrementally until you get the right balance. At least when the hook is forward the plane will also want to track straight ahead and that would tend to eliminate roll etc... as long as the plane is balanced along the nose to tail axis - this can be done by placing a pin in the nose and another in the fin (near the top) before the rudder is attached, and settling the two pins on stands so the airframe is not touching anything, then balance the plane until the wings are level. Happy flying - Marty
-
Beginner have a mare!
Martin Roberts replied to David Jacobs's topic in Electric Flight for Beginners
Well said Simon, I completely forgot to mention an unpowered test flight Marty - All my planes know where the CoG is, and they head straight for it when I lose control -
Beginner have a mare!
Martin Roberts replied to David Jacobs's topic in Electric Flight for Beginners
Hi Dave, glad to see another newbie taking the plunge, but it's always better to have an experience pilot with you when starting, believe me I know.... One thing that all aircraft with propellors suffer from is the dreaded torque roll that so of our colleagues have mentioned, this happens when the propellor is still building up speed and as we all know for every action there is the equal and opposite reaction, in other words the motor (which really doesn't care about the air around it) turns (action) and causes the prop to turn, the prop doesn't want to because it has mass and a moment (length) etc... so the prop is causing the reaction which is then countered to some extent by the wings tailplane and fin and rudder, not to mention the mass of the aircraft. The smaller the aircraft, the smaller the mass and flying surfaces, however because the props are relatively small, the rotational speed of the prop has to be increased and therefor the actions are increased while the reactions are decreased...simple really the smaller and lighter the plane, the more susceptable it is to torque roll. But lets think about the other factors for a minute... the prop is rotating to force air backwards, so if you are sitting in the pilots seat and the prop is turning to your right, the blade is set at an angle (pitch) which is say 25 degrees from perpendicular to the crank this results in air being pushed at an angle to the position of the blade at any given time... therefore when the prop blade is at horizontal to your right side (starboard) the air is being pushed backwards and down at the same time which presents to the top of the wing first and under the wing last creating a lower pressure under the starboard wing. The exact opposite is happening on the port side higher pressure under and lower pressure over, with a result of more lift on the starboard wing and less lift on the port wing, then add the torque roll viola left bank to death.... The faster the prop is turning vs the lighter mass and short wing spells death and yes there are formulae to calculate it... The old timers use slow props speeds and longer wings to resolve the issue, but I would recommend a plane with a longer wing ... motor glider and a qualified pilot coach Marty - All my planes know where the CoG is, and they head straight for it when I lose control -
I for one would like to say that I look forward to the finished plans and information for the Leccie bits. As always Tony puts out a great plan and, as he says he spent time on simplifying the build. It would be great of course for an EDF A-6 or Folland Gnat, and I would love to have the DH98 and the Vulcan of course.... but if Tony does do another single prop warbird ..... please, please, please let it be an ME109 - not because it was German - because it is simply a beautifaully clean and simple design which of course all great planes are. Marty